新型加工工艺超硬车削技术的性能优势介绍
随着制造业的不断发展,世界机床制造厂家一直在寻求用新技术来降低加工零件和成品的生产成本,使得超硬切削成为当前各制造商关注的新型加工工艺。预期在不久的将来,超硬切削技术将会发展得更加成熟,并被人们所广泛地使用。
超硬车削被定义为对HRC45以上高硬材质工件单点切削的加工过程。通常工件材质硬度可达到HRC58~68的范围,切削刀具材质基本上选用CBN(立方氮化硼)。
超硬车削技术为那些不要求超高精密磨削的加工制造提供了一个新的选择。当然,对某些超高精密要求的工件、容易变形的工件和特殊要求的工件,磨削工艺还是比较适合的选择。
虽然目前超硬车削还不能完全取代超高精密磨削,但已能取代相当一部分的精密磨削,从而减轻了磨削制造过程中昂贵的生产成本。目前,超硬切削的工件表面粗糙度一般可达Ra0.2~Ra0.4,圆度可达0.0005mm,尺寸精度可控制在0.003mm以内。经过切削比较发现超硬车削加工工艺比一般磨削加工工艺的生产效率要高4~6倍。
在不使用切削液冷却的情况下切削一个HRC62的坚硬零件,会产生很多的热量。一般超硬切削时,切削点区域内的温度可高达926℃。事实上,局部高温热化可以帮助切削过程的完成,刀具切削点的高热预先对工件的切削层会产生退火和软化效应,使得工件比较容易切削。
这一切削过程中,绝大部分的热是由切屑剥离而产生的。为了求得精美的表面加工质量,在最后一道切削时,应尽可能减少切削深度,一般控制在0.25mm以内。
当前超硬车削已被广泛应用在汽车零部件制造中。上海汽车齿轮总厂已非常成功地将这一技术运用于大批量生产当中,他们在齿轮渗碳淬火后采用以车代磨,进行成品的最终精密加工,以达到零件设计的公差和表面粗糙度要求。被加工工件的表面粗糙度可达Ra0.2~Ra0.4,圆度可达0.0005mm,0.003mm的公差带Cpk值可达1.67。
声明:本网站所收集的部分公开资料来源于互联网,转载的目的在于传递更多信息及用于网络分享,并不代表本站赞同其观点和对其真实性负责,也不构成任何其他建议。本站部分作品是由网友自主投稿和发布、编辑整理上传,对此类作品本站仅提供交流平台,不为其版权负责。如果您发现网站上所用视频、图片、文字如涉及作品版权问题,请第一时间告知,我们将根据您提供的证明材料确认版权并按国家标准支付稿酬或立即删除内容,以保证您的权益!联系电话:010-58612588 或 Email:editor@mmsonline.com.cn。
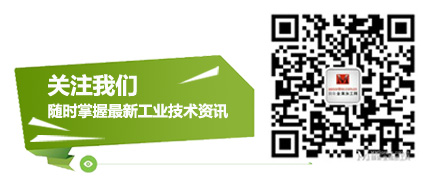
- 暂无反馈