数控机床编程七--Master CAM自动编程二
(7)粗车方向/角度。用于设置粗切方向和粗车角度。Master CAM提供4种加工方向: 1)外径:选中此项则在工件外直径方向上切削。车刀运动的方向指向靠近主轴的方向。 2)内径:选中此项则在工件内直径方向上切削。车刀运动的方向指向远离主轴的方向。 3)前端面:选中face项则在工件的前端面方向上切削。 4)后瑞面:选中Back项则在工件的后端面方向上切削。设置粗车角度时可以直接在输入框中输入粗车角度。粗车角度可以是介于0至360之间的任一数值,—般情况下,外径或内径车削都是采用0度粗切角,端面车削则采用90度粗切角。
(8)设置刀具补偿
在车削加工中,Master CAM使用两种方式设置刀具偏移,即计算机补偿和控制器偏移。刀具半径补偿和控制系统刀具补偿对应于实际加工中的效果是一样的,但是经过后处理程序得到的最终数控加工程序是不同的:控制系统刀具补偿中刀具中心轨迹和编程轨迹是重合的;而刀具半径补偿中刀具中心轨迹与编程轨迹不重合,编程轨迹与零件轮廓线重合。
(9)设置进刀/退刀刀具路径
车削加工可以在每条切削刀具路径中添加进/退刀刀具路径。单击进/退刀向量按钮,弹出如图7-16所示的对话框设置进退刀刀具路径, 进刀刀具路径的设置方法与退刀刀具路径的设置方法相同。Master CAM 8.0有两种设置进刀刀具路径的方法:调整串连外形和添加进刀矢量。在调整串连外形的选项中可以串联的起点可以延伸或收缩。(10)切削参数。 如图7-17所示。用于设置粗车加工中是否进行底切加工,若允许底切,则设置底切参数。
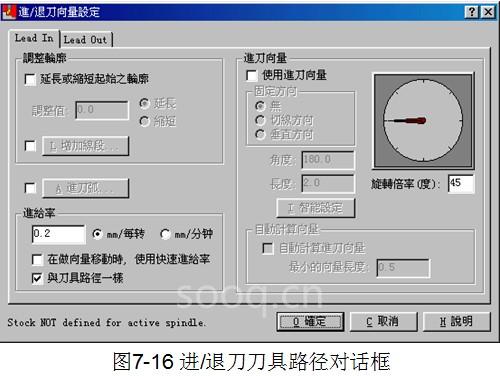
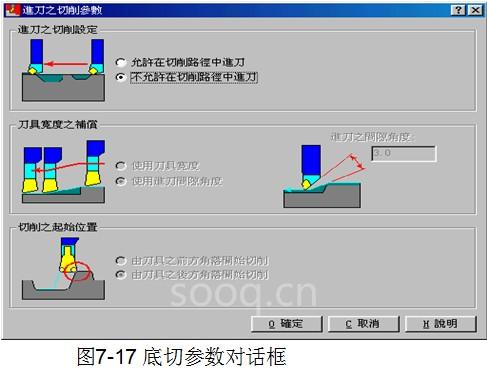
3.精加工。
精车刀具路径用于对工件表面进行精车削。以便提高工件表面的精度。如果对工件的要求较高,而粗加工后的工件表面不能满足要求,此时就必须进行精车加工。一般说来,需要精车加工的工件在进行精车加工之前已经进行了粗车加工。在Master CAM中精车加工必须生成精车加工刀具路径。相应加工参数设置如图7-18对话框所示。对话框中的精车加工刀具路径设置也包括刀具参数和精车加工刀具参数两项设置。精车加工参数在精车参数对话框选项卡中进行设置。
精车加工与粗车加工中的参数基本相同,只是在精车加工选项卡中增加了用来设置精车加工的次数,精车加工的次数应设置为粗车加工的预留量除以精车加工进刀量输入框中输入的精车加工进刀量。其它参数的设置参考粗车加工参数设置,在此不再复述。 4.端面车削加工。
端面车削加工用于生成车削工件端面的刀具路径。所有车削的区域由两点定义的矩形来确定。见图7-19所示。
(1) 进刀量。在进刀量输入框输入刀具开始进刀时距工件表面的距离。 (2) 粗加工进刀量。在其输入框中输入粗加工进刀量以生成端面车削粗车刀具路径。 (3) 精加工进刀量。 在其输入框中输入精加工进刀量以生成端面车削精车刀具路径。 (4) 精加工次数。用于设置端面车削精车加工的次数。 (5) 过切量。用于定义生成刀具路径时实际车削区域超出由矩形定义的加工区域的距离。在过切量输入框输入过切量。 (6) 退刀量。该输入框用于输入退刀量,若选中快速退刀对话框,就会快速退刀。
(7) 毛坯预留量。用于输入加工后的预留量。 (8) 切削方向由内向外。该选项用于设置加工方向。选中该复选框时,就会从离旋转轴较近的位置开始向外加工.否则就会从外向内加工。
5.切槽加工
切槽加工用于生成切槽车削加工的刀具路径,对槽形工件的槽进行加工。Master CAM则可以在垂直方向车削切槽,也可在端面方向车削切槽。用户可以按图7-20所示,进行切槽加工区域设置,设置后按”确定”按钮。

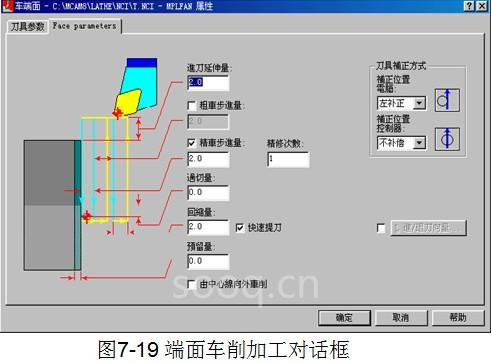
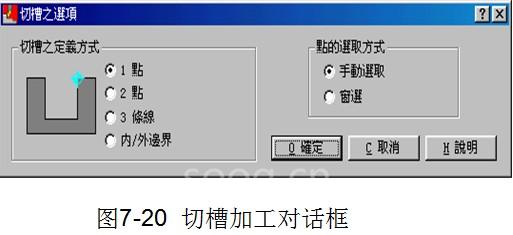
(1)切槽选项对话框有四种定义切槽加工区域方式。
1)一点方式。该选项通过在绘图区选取一点来设置加工区域。这时选取点是定义切槽的右外角点的位置,而实际加工区域的大小仍需在切槽的外形定义中来设置。用户可以通过手动选取或窗选方式进行点的选择。
2)两点方式。该选项通过在绘图区选取两点来设置加工区域。这时选取点可以定义切槽的宽度和高度,而实际加工区域的形状仍需在切槽的外形定义中来设置。
3)三条线方式。
该选项通过在绘图区选取三条直线来设置加工区域。选取的三条直线必须是一个矩形的三条边。这时可以定义切槽的宽度和高度,而实际加工区域的形状仍需在切槽的外形定义中来设置。
4)内/外边界。选择该选项,通过在绘图区选取两个串连来设置加工区域。这时切槽的外形由选取的串连来定义。
(2)设置切槽形状。使用上面提到的4种设置加工区域的方法中的一种设置加工区域后,系统弹出如图7-21所示的切槽切削对话框。在此对话框中刀具路径设置包括刀具参数、切槽形状参数、切槽粗车参数和切槽精车参数等4项设置。选择切槽的形状参数选项卡以设置切槽的形状。下面将对设置切槽形状参数选项卡中各参数进行说明。
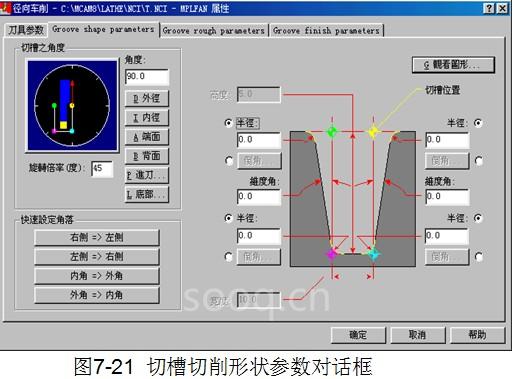
1)切槽角度栏。此栏用于设置切槽的方向。Master CAM通过设置切槽的角度来定义切槽的方向,用户可以直接在角度输入框中输入角度,也可用鼠标拖动圆盘中的切槽来设置角度,这时设置的角度以结果输入框中的输入值为增量。
2) 切槽形状定义。Master CAM通过设置切槽的底部宽度、高度、侧壁倾角和内外圆角半径等参数来定义切槽的形状。如在内外角位置采用倒角方式,这时需先选择对应的倒角选择按钮,之后单击该倒角按钮,系统弹出如图7-22所示的切槽倒角对话框,用户可以通过该对话框来设置倒角参数。
3)快速设置切槽形状栏。Master CAM通过该栏快速设置定义切槽形状的各参数。单击右侧=>左侧按钮,系统将会把切槽右边的参数设置为左边的参数;单击(左侧=>右侧)按钮,系统将会把切槽左边的参数设置为右边的参数。单击(内角=>外角)按钮,系统将会把切槽内角的参数设置为外角的参数;单击(外角=>内角)按钮,系统将会把切槽外角的参数设置为内角的参数。
(3)设置切槽粗车参数。 在图7-23对话框中选择了粗车切槽复选框后,可在其中进行切槽粗车参数设置。下面对各参数进行说明。
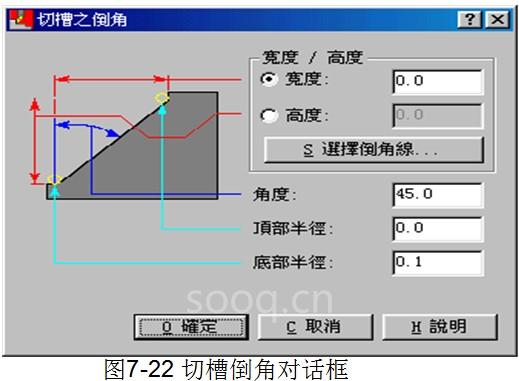

1)切削方向。该参数用于设置切槽粗车加工的进刀方向,系统提供了三种进刀方向。正向:刀具路径从切槽的左侧开始并沿+Z方向移动;负向:刀具路径从切槽的右侧开始并沿-Z方向移动;中间开始双向:刀具路径从切槽的中间开始并以双向切削方式进行加工。
2)粗加工步距。该参数用于设置切槽粗车加工的进刀量,提供了3种设置方式:步进次数,由设置的切削次数来确定每次切削的进刀量;进刀量,直接设置每次切削的进刀量;刀具宽度百分比:把每次切削的进刀量设置为刀具宽度的百分比。
3)退刀距离百分比。设置每次退刀时与侧壁的距离,用粗车进刀量的百分比来定义。
4)暂停时间。用于设置在每次粗车加工时在切槽底部刀具停留的时间。无:刀具在切槽底部不停留;秒:刀具在切槽底部停留的时间为输入框中的时间,单位为秒;转:刀具在切槽底部停留在输入框中的圈数。 5)切槽的壁边。有两种可以选择:步进和平滑。步进:系统就会按设置的下刀量进行加工,这时就会在侧壁生成台阶;平滑:选择此项后,按参数按钮,设置移除切槽的斜壁切削。 6)切槽步进。选择切槽步进对话框,弹出图7-24所示对话框,设置步进参数。
7)分层切深。选择分层切深对话框,弹出图7-25所示对话框。一般在进行深槽加工或加工较硬的材料时需要进行切槽的深度设置,主要是设置加工深度、刀具移动方式和回刀设置。
(4)设置切槽精车参数。如图7-26所示。有关参数设置下列说明。
1)多次走刀。同时加工多个切槽而且进行多次精车切削时的加工顺序就由此栏设置。
2)第一次的走刀方向。该栏用于选择第一次加工的方向,可以选择CCW(逆时针方向)或CW(顺时针)。
3)进刀。单击进刀向量按钮,系统弹出如图7-27所示的进刀向量对话框,用于设置每次精车加工的进刀刀具路径。
(8)设置刀具补偿
在车削加工中,Master CAM使用两种方式设置刀具偏移,即计算机补偿和控制器偏移。刀具半径补偿和控制系统刀具补偿对应于实际加工中的效果是一样的,但是经过后处理程序得到的最终数控加工程序是不同的:控制系统刀具补偿中刀具中心轨迹和编程轨迹是重合的;而刀具半径补偿中刀具中心轨迹与编程轨迹不重合,编程轨迹与零件轮廓线重合。
(9)设置进刀/退刀刀具路径
车削加工可以在每条切削刀具路径中添加进/退刀刀具路径。单击进/退刀向量按钮,弹出如图7-16所示的对话框设置进退刀刀具路径, 进刀刀具路径的设置方法与退刀刀具路径的设置方法相同。Master CAM 8.0有两种设置进刀刀具路径的方法:调整串连外形和添加进刀矢量。在调整串连外形的选项中可以串联的起点可以延伸或收缩。(10)切削参数。 如图7-17所示。用于设置粗车加工中是否进行底切加工,若允许底切,则设置底切参数。
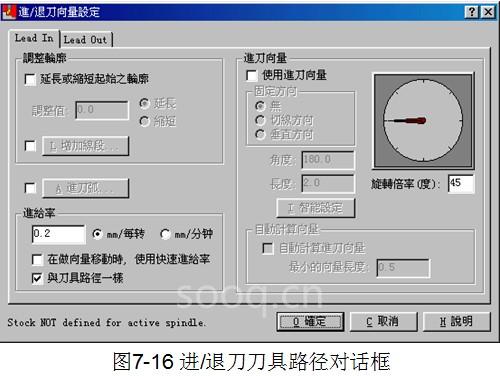
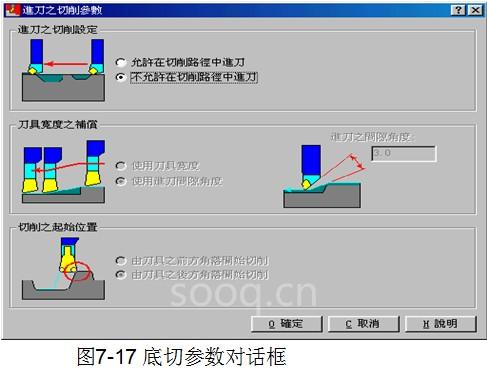
3.精加工。
精车刀具路径用于对工件表面进行精车削。以便提高工件表面的精度。如果对工件的要求较高,而粗加工后的工件表面不能满足要求,此时就必须进行精车加工。一般说来,需要精车加工的工件在进行精车加工之前已经进行了粗车加工。在Master CAM中精车加工必须生成精车加工刀具路径。相应加工参数设置如图7-18对话框所示。对话框中的精车加工刀具路径设置也包括刀具参数和精车加工刀具参数两项设置。精车加工参数在精车参数对话框选项卡中进行设置。
精车加工与粗车加工中的参数基本相同,只是在精车加工选项卡中增加了用来设置精车加工的次数,精车加工的次数应设置为粗车加工的预留量除以精车加工进刀量输入框中输入的精车加工进刀量。其它参数的设置参考粗车加工参数设置,在此不再复述。 4.端面车削加工。
端面车削加工用于生成车削工件端面的刀具路径。所有车削的区域由两点定义的矩形来确定。见图7-19所示。
(1) 进刀量。在进刀量输入框输入刀具开始进刀时距工件表面的距离。 (2) 粗加工进刀量。在其输入框中输入粗加工进刀量以生成端面车削粗车刀具路径。 (3) 精加工进刀量。 在其输入框中输入精加工进刀量以生成端面车削精车刀具路径。 (4) 精加工次数。用于设置端面车削精车加工的次数。 (5) 过切量。用于定义生成刀具路径时实际车削区域超出由矩形定义的加工区域的距离。在过切量输入框输入过切量。 (6) 退刀量。该输入框用于输入退刀量,若选中快速退刀对话框,就会快速退刀。
(7) 毛坯预留量。用于输入加工后的预留量。 (8) 切削方向由内向外。该选项用于设置加工方向。选中该复选框时,就会从离旋转轴较近的位置开始向外加工.否则就会从外向内加工。
5.切槽加工
切槽加工用于生成切槽车削加工的刀具路径,对槽形工件的槽进行加工。Master CAM则可以在垂直方向车削切槽,也可在端面方向车削切槽。用户可以按图7-20所示,进行切槽加工区域设置,设置后按”确定”按钮。

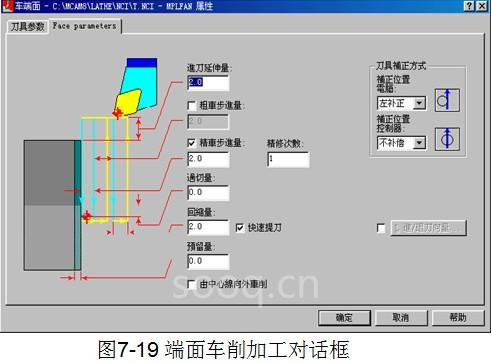
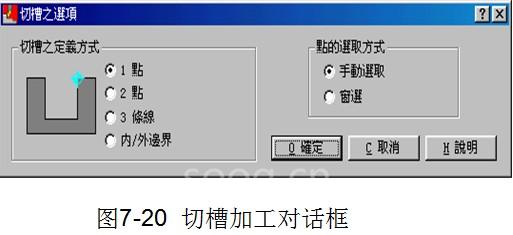
(1)切槽选项对话框有四种定义切槽加工区域方式。
1)一点方式。该选项通过在绘图区选取一点来设置加工区域。这时选取点是定义切槽的右外角点的位置,而实际加工区域的大小仍需在切槽的外形定义中来设置。用户可以通过手动选取或窗选方式进行点的选择。
2)两点方式。该选项通过在绘图区选取两点来设置加工区域。这时选取点可以定义切槽的宽度和高度,而实际加工区域的形状仍需在切槽的外形定义中来设置。
3)三条线方式。
该选项通过在绘图区选取三条直线来设置加工区域。选取的三条直线必须是一个矩形的三条边。这时可以定义切槽的宽度和高度,而实际加工区域的形状仍需在切槽的外形定义中来设置。
4)内/外边界。选择该选项,通过在绘图区选取两个串连来设置加工区域。这时切槽的外形由选取的串连来定义。
(2)设置切槽形状。使用上面提到的4种设置加工区域的方法中的一种设置加工区域后,系统弹出如图7-21所示的切槽切削对话框。在此对话框中刀具路径设置包括刀具参数、切槽形状参数、切槽粗车参数和切槽精车参数等4项设置。选择切槽的形状参数选项卡以设置切槽的形状。下面将对设置切槽形状参数选项卡中各参数进行说明。
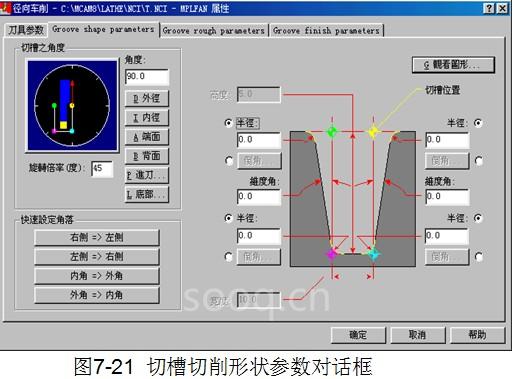
1)切槽角度栏。此栏用于设置切槽的方向。Master CAM通过设置切槽的角度来定义切槽的方向,用户可以直接在角度输入框中输入角度,也可用鼠标拖动圆盘中的切槽来设置角度,这时设置的角度以结果输入框中的输入值为增量。
2) 切槽形状定义。Master CAM通过设置切槽的底部宽度、高度、侧壁倾角和内外圆角半径等参数来定义切槽的形状。如在内外角位置采用倒角方式,这时需先选择对应的倒角选择按钮,之后单击该倒角按钮,系统弹出如图7-22所示的切槽倒角对话框,用户可以通过该对话框来设置倒角参数。
3)快速设置切槽形状栏。Master CAM通过该栏快速设置定义切槽形状的各参数。单击右侧=>左侧按钮,系统将会把切槽右边的参数设置为左边的参数;单击(左侧=>右侧)按钮,系统将会把切槽左边的参数设置为右边的参数。单击(内角=>外角)按钮,系统将会把切槽内角的参数设置为外角的参数;单击(外角=>内角)按钮,系统将会把切槽外角的参数设置为内角的参数。
(3)设置切槽粗车参数。 在图7-23对话框中选择了粗车切槽复选框后,可在其中进行切槽粗车参数设置。下面对各参数进行说明。
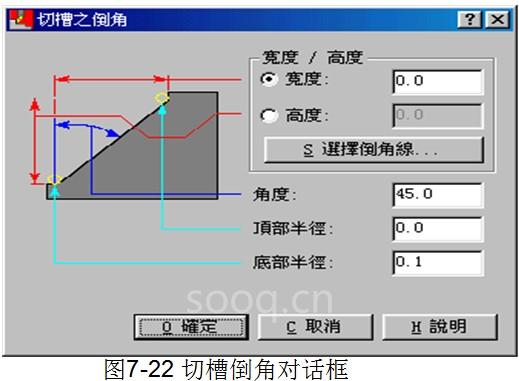

1)切削方向。该参数用于设置切槽粗车加工的进刀方向,系统提供了三种进刀方向。正向:刀具路径从切槽的左侧开始并沿+Z方向移动;负向:刀具路径从切槽的右侧开始并沿-Z方向移动;中间开始双向:刀具路径从切槽的中间开始并以双向切削方式进行加工。
2)粗加工步距。该参数用于设置切槽粗车加工的进刀量,提供了3种设置方式:步进次数,由设置的切削次数来确定每次切削的进刀量;进刀量,直接设置每次切削的进刀量;刀具宽度百分比:把每次切削的进刀量设置为刀具宽度的百分比。
3)退刀距离百分比。设置每次退刀时与侧壁的距离,用粗车进刀量的百分比来定义。
4)暂停时间。用于设置在每次粗车加工时在切槽底部刀具停留的时间。无:刀具在切槽底部不停留;秒:刀具在切槽底部停留的时间为输入框中的时间,单位为秒;转:刀具在切槽底部停留在输入框中的圈数。 5)切槽的壁边。有两种可以选择:步进和平滑。步进:系统就会按设置的下刀量进行加工,这时就会在侧壁生成台阶;平滑:选择此项后,按参数按钮,设置移除切槽的斜壁切削。 6)切槽步进。选择切槽步进对话框,弹出图7-24所示对话框,设置步进参数。
7)分层切深。选择分层切深对话框,弹出图7-25所示对话框。一般在进行深槽加工或加工较硬的材料时需要进行切槽的深度设置,主要是设置加工深度、刀具移动方式和回刀设置。
(4)设置切槽精车参数。如图7-26所示。有关参数设置下列说明。
1)多次走刀。同时加工多个切槽而且进行多次精车切削时的加工顺序就由此栏设置。
2)第一次的走刀方向。该栏用于选择第一次加工的方向,可以选择CCW(逆时针方向)或CW(顺时针)。
3)进刀。单击进刀向量按钮,系统弹出如图7-27所示的进刀向量对话框,用于设置每次精车加工的进刀刀具路径。
声明:本网站所收集的部分公开资料来源于互联网,转载的目的在于传递更多信息及用于网络分享,并不代表本站赞同其观点和对其真实性负责,也不构成任何其他建议。本站部分作品是由网友自主投稿和发布、编辑整理上传,对此类作品本站仅提供交流平台,不为其版权负责。如果您发现网站上所用视频、图片、文字如涉及作品版权问题,请第一时间告知,我们将根据您提供的证明材料确认版权并按国家标准支付稿酬或立即删除内容,以保证您的权益!联系电话:010-58612588 或 Email:editor@mmsonline.com.cn。
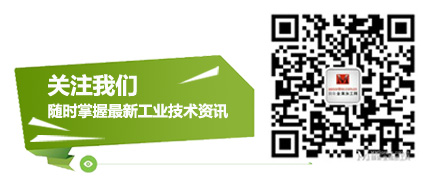
网友评论
匿名:
相关链接
最新反馈
- 暂无反馈
无须注册,轻松沟通