高速加工成功的关键
高速加工成功的关键浓缩为三个要素:(1) 机床, (2) 刀具和(3) 编程。这三者的正确组合使得模具制造厂在生产率、质量和价格方面比他们的竞争对手更具优势。错误的组合浪费你辛苦挣来的钞票。
显然,选择正确的机床对于优化高速、小余量加工是至关重要的。因此,找到专门为高速加工设计的机床是重要的。不要被把标准机床用高速选件进行改造的产品诱惑。否则,你将得不倒完成你的最困难加工任务所必需的刚性、精度和速度。
1 机床
我们寻找的具有刚性结构的机床能吸收振动、提供刚度和抵抗挠曲,即使在很高的加速度时。优先考虑完全通过有限元分析、提供最佳刀具寿命和表面粗糙度的具有大量加强筋和铸铁结构的机床。此外,要密切关注机床的导轨、导轨系统、滚珠丝杠和平衡配重。
虽然机床本身应当很重,但其移动部件应该尽可能地重量轻而不牺牲刚性。重量轻且刚性好的导轨可获得最快的加速度并缩短整个切削时间。
至于导轨系统,你的应用决定了是否使用具有滚珠丝杠或直线导轨的机床。直线导轨非常适用于具有低扭矩主轴的小到中型规格的机床。而具有高扭矩主轴的中型到大型HSM机床要求滚珠丝杠。虽然与高转速主轴机床一起使用的每种系统都能以非常快的速度进行轻快的切削,滚珠丝杠在减振方面的确有优势。
那么你应该如何进行选择? 答案也许是两者均可。部分机床制造商在X轴使用直线导轨并在Y、Z轴使用滚珠丝杠。直线导轨承受工作台重量的载荷。这使得轴向惯性最小化,甚至在工作台载荷变化很大时。有了滚珠丝杠系统,需要移动工作台和克服爬行的扭矩值变得波动很大且难以调节。
任何机床最重要的结构要素之一是滚珠丝杠,但它通常被忽视了。你需要大直径、强壮的滚珠丝杠来防止挠曲和振动。脆弱的、重量轻的滚珠丝杠简直不能使任务完成。确保你得到的机床装有预拉伸的滚珠丝杠(在载荷下拉紧)以去除热变形、消除次级蠕变并提高轴向刚性。如果机床结构不能支持预拉伸的滚珠丝杠,那么滚珠丝杠必须通过循环的流体进行冷却,而这又产生维护的问题。
一台不具有预拉伸滚珠丝杠的机床必须要有精度的标定,但也许仍然是轴向刚性不足。装有很长的滚珠丝杠的长行程机床应该具有固定螺钉/回转螺母装置以防止螺钉的突然移动,而伺服电机应该直接与滚珠丝杠连在一起以形成刚性的连接。伺服电机不直接连接(例如,使用皮带轮和皮带)会造成运动特性和刚性的丧失,最终会牺牲精度和表面粗糙度。
正因为在HSM中很高的加速度,采用配重进行平衡是行不通的。因此,你将需要机床使用一个大型的无需平衡的伺服电机或一个液压的平衡系统(参阅以下侧栏中的机床设计:双立柱结构的优势和匹配控制、电机和驱动)。
主轴是任何一种机床的核心。虽然有大量的主轴类型可提供,包括齿轮箱和直接驱动的主轴,但是最适合于HSM应用的是产生最高转速的集成主轴或电主轴。一条很好的经验法则是寻找主轴转速从15,000到40,000r/min的机床。
集成主轴把电机和株洲结合在一起,实质上主轴心轴是转子,而主轴的轴套是定子。当你要求很高的转速和很好的表面粗糙度时,它们是非常理想的。
虽然集成主轴由于其维修成本高而变得很昂贵,但它们能提供极佳的热稳定性,变形小、优异的加速/减速和足够的切削扭矩。所有这些对于HSM应用都是至关重要的。
2 HSK 刀具
刀具是成功应用HSM的第二个关键。投资HSK刀柄,因为在刚性和转速方面HSK刀柄优于CAT/BT和MCAT/BBT系统。不要试图购买较便宜的刀具。归根到底,你仅减少采购成本。而你将从未收获HSM机床的所有好处。
CAT/BT系统存在什么问题? 在高转速下,它们不能很好地夹持。那是因为它们仅依靠与主轴的锥面接触获得刚性。随着主轴转速的提高,离心力能张开它们的拉钉夹持系统。
在高转速下,主轴头部由于离心力的作用而轻微膨胀,因为拉杆的拉力恒定,引起传统的刀柄进一步朝向主轴内部移动。这种刀具的后拉改变了Z轴的尺寸精度而且会导致刀具粘附在主轴上。
但为何不用MCAT/BBT系统呢? 因为机床主轴端面和刀柄法兰面之间的双重接触,以及与主轴锥面的接触,使它们的刚性得到提高。这种接触减少了机床在高转速时的振动和机床主轴与刀柄锥面之间的微振磨损。可是,MCAT/BBT刀柄具有与CAT/BT系统相同的拉钉夹持配置,而且会碰到离心力引起的相同的问题。
与传统的刀柄不同,HSK刀柄是中空的,而且它们的夹紧机构是从内部开始工作的,使刀柄不受离心力的影响。还有,因为HSK是短锥柄,主轴轴承的位置更接近主轴头部,刚性得到提高。
与供应商合作为你的HSM机床和应用进行选择最佳的HSK系统,这是一个很好的主意。HSK-A系统对于转速不超过24,000r/min的高扭矩切削是理想的。另一方面,HSK-E刀柄不具有A型系统的驱动槽,因而改善了在高速下的平衡。这种类型非常适用于主轴高转速下的低扭矩精加工。
经验法则是对于转速不超过15,000r/min的重切削使用大型的HSK-100A,中型规格HSK-63A的适用于转速不超过24,000r/min的半精到精加工,而小型的HSK-50E刀柄适用于高速精加工。
3 编程
既然你已经有了最佳的HSM机床并已使用HSK刀柄。但你仍然得不到你想要的结果。是否你忽视了编程?
把用于传统加工的编程软件和方法照样应用到HSM加工是一个常见的错误。但是使用针对HSM进行优化的软件,你将得到优异的零件质量和更好的综合效果。你还将在无人看管的加工(使用多种刀具不中断地自始至终加工零件)中获得一致的结果。此外,如果你的编程软件精确地识别上道加工的余量,你将能从粗加工直接进入半精加工无需过渡切削。
今日高级的CAM系统具备成功应用HSM所必须的几个特性。最重要的是拥有的软件能把实际数据压缩到表面数据。很多系统在生成加工程序时在表面上放置一个三角形的网格。不幸的是,放置在表面上的所有这些微小的三角形不是真正的表面数据。而在根本上,这种类型的软件在加工时将损害表面粗糙度和精度。 要寻找的CAM的其它关键特性包括摆线式粗加工路径、等高线加工和余量自动识别及再加工。
寻找正确的软件包和合作伙伴
正确的机床是成功实施高速加工的基础。因此,要找到能减振的结构具有刚性极好的机床、针对HSM进行优化的先进运动系统和能处理你的最困难加工任务的高转速主轴。然后在那个强壮的基础上构造正确的刀柄和编程。
最后的一个推荐 - 请求你的机床供应商帮助优化你的工艺。他们能帮你设计一个能体现杰出的供应商帮助优化工艺的解决方案。他们能为你的HSM应用你设计一个优秀且效果一致的解决方案。记住,正确地组合机床、刀柄和编程将引发成功的高速加工并保正你的工厂具有竞争优势。
机床设计: 双立柱结构的优势
基本的机床设计对HSM加工有着巨大的影响。拿C形框架机床和双立柱系统的不同作举例。
C形框架设计常见于小型/中型规格的机床,额定的工作台负载小于1,500 lbs,它有一个床身、一个立柱和一个沿立柱上下滑动的动力头。这种配置将X轴置于Y轴之上,它使得两个轴上的载荷是可变的。当工作台负载改变时,使机床难以调节和控制这种可变的载荷,两个轴都受到影响。
在一台C形框架的机床上,工作台也许通过滑板得到完全的支撑,但滑板从未被铸件床身完全支撑。这导致的固有的不稳定性是不能被HSM接受的。
相反,双立柱桥式结构对于中型规格和更大的HSM机床来说是理想的。在这种配置中,Y和Z轴具有固定的负载,而仅有工作台的负载在变化。由于轴向载荷和惯性从不改变(刀具和刀柄重量的不显著的差别除外),这使得机床在Y和Z向能被非常精确的调节。
这种双立柱桥式设计还特有一个很长的铸件床身,它能完全支撑工作台以适应机床极长的行程。这种配置消除了不平衡或倾斜和偏转。
数控机床在线检测技术
数控机床是现代高科技发展的产物,每当一批零件开始加工时,有大量的检测需要完成,包括夹具和零件的装卡、找正、零件编程原点的测定、首件零件的检测、工序间检测及加工完毕检测等。目前完成这些检测工作的主要手段有手工检测、离线检测和在线检测。在线检测也称实时检测,是在加工的过程中实时对刀具进行检测,并依据检测的结果做出相应的处理。在线检测是一种基于计算机自动控制的检测技术,其检测过程由数控程序来控制。闭环在线检测的优点是:能够保证数控机床精度,扩大数控机床功能,改善数控机床性能,提高数控机床效率。
数控机床的在线检测系统由软件和硬件组成。硬件部分通常由以下几部分组成:
机床本体:机床本体是实现加工、检测的基础,其工作部件是实现所需基本运动的部件,它的传动部件的精度直接影响着加工、检测的精度。
数控系统:目前数控机床一般都采用CNC数控系统,其主要特点是输入存储、数控加工、插补运算以及机床各种控制功能都通过程序来实现。计算机与其他装置之间可通过接口设备联接,当控制对象或功能改变时,只需改变软件和接口。CNC系统一般由中央处理存储器和输入输出接口组成,中央处理器又由存储器、运算器、控制器和总线组成。
伺服系统:伺服系统是数控机床的重要组成部分,用以实现数控机床的进给位置伺服控制和主轴转速(或位置)伺服控制。伺服系统的性能是决定机床加工精度、测量精度、表面质量和生产效率的主要因素
测量系统:测量系统有接触触发式测头、信号传输系统和数据采集系统组成,是数控机床在线检测系统的关键部分,直接影响着在线检测的精度。其中关键部件为测头,使用测头可在加工过程中进行尺寸测量,根据测量结果自动修改加工程序,改善加工精度,使得数控机床既是加工设备,又兼具测量机的某种功能。
计算机系统:在线检测系统利用计算机进行测量数据的采集和处理、检测数控程序的生成、检测过程的仿真及与数控机床通信等功能。在线检测系统考虑到运行目前流行的Windows和CAD/CAM/CAPP/CAM以及VC++等软件,以及减少测量结果的分析和计算时间,一般采用Pentium级别以上的计算机。
有了机床、刀具和编程的着正确组合,模具制造商将收获高速加工所有的好处。
声明:本网站所收集的部分公开资料来源于互联网,转载的目的在于传递更多信息及用于网络分享,并不代表本站赞同其观点和对其真实性负责,也不构成任何其他建议。本站部分作品是由网友自主投稿和发布、编辑整理上传,对此类作品本站仅提供交流平台,不为其版权负责。如果您发现网站上所用视频、图片、文字如涉及作品版权问题,请第一时间告知,我们将根据您提供的证明材料确认版权并按国家标准支付稿酬或立即删除内容,以保证您的权益!联系电话:010-58612588 或 Email:editor@mmsonline.com.cn。
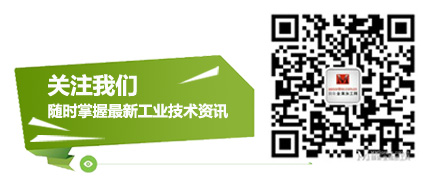
- 暂无反馈