数控机床之加工工艺路线设计浅析
数控机床加工的工艺路线设计必须全面考虑,注意工序的正确划分、顺序的合理安排和数控加工工序与普通工序的衔接。
1. 工序的划分
数控机床与普通机床加工相比较,加工工序更加集中,根据数控机床的加工特点,加工工序的划分有以下几种方式:
1)根据装夹定位划分工序
这种方法一般适应于加工内容不多的工件,主要是将加工部位分为几个部分,每道工序加工其中一部分。如加工外形时,以内腔夹紧;加工内腔时,以外形夹紧。
2)按所用刀具划分工序
为了减少换刀次数和空程时间,可以采用刀具集中的原则划分工序,在一次装夹中用一把刀完成可以加工的全部加工部位,然后再换第二把刀,加工其他部位。在专用数控机床或加工中心上大多采用这种方法。
3)以粗、精加工划分工序
对易产生加工变形的零件,考虑到工件的加工精度,变形等因素,可按粗、精加工分开的原则来划分工序,即先粗后精。
在工序的划分中,要根据工件的结构要求、工件的安装方式、工件的加工工艺性、数控机床的性能以及工厂生产组织与管理等因素灵活掌握,力求合理。
2. 加工顺序的安排
加工顺序的安排应根据工件的结构和毛坯状况,选择工件定位和安装方式,重点保证工件的刚度不被破坏,尽量减少变形,因此加工顺序的安排应遵循以下原则:
1)上道工序的加工不能影响下道工序的定位与夹紧
2)先加工工件的内腔后加工工件的外轮廓
3)尽量减少重复定位与换刀次数
4)在一次安装加工多道工序中,先安排对工件刚性破坏较小的工序。
3. 数控加工工序与普通工序的衔接
由于数控加工工序穿插在工件加工的整个工艺过程之中,各道工序需要相互建立状态要求,如加工余量的预留,定位面与孔的精度和形位公差要求,矫形工序的技术要求,毛坯的热处理等要求,各道工序必须前后兼顾综合考虑。
4. 数控机床加工工序和加工路线的设计
数控机床加工工序设计的主要任务:确定工序的具体加工内容、切削用量、工艺装备、定位安装方式及刀具运动轨迹,为编制程序作好准备。其中加工路线的设定是很重要的环节,加工路线是刀具在切削加工过程中刀位点相对于工件的运动轨迹,它不仅包括加工工序的内容 ,也反映加工顺序的安排,因而加工路线是编写加工程序的重要依据。
1)确定加工路线的原则
① 加工路线应保证被加工工件的精度和表面粗糙度。
② 设计加工路线要减少空行程时间,提高加工效率。
③ 简化数值计算和减少程序段,降低编程工作量。
④ 据工件的形状、刚度、加工余量、机床系统的刚度等情况,确定循环加工次数。
⑤ 合理设计刀具的切入与切出的方向。采用单向趋近定位方法,避免传动系统反向间隙而产生的定位误差。
⑥ 合理选用铣削加工中的顺铣或逆铣方式,一般来说,数控机床采用滚珠丝杠,运动间隙很小,因此顺铣优点多于逆铣。
2)数控机床加工路线
① 数控车床加工路线
② 数控铣床加工路线
立铣刀侧刃铣削平面零件外轮廓时避免沿零件外轮廓的法向切入和切出,应沿着外轮廓曲线的切向延长线切入或切出,这样可避免刀具在切入或切出时产生的刀刃切痕,保证零件曲面的平滑过渡。
③孔加工定位路线
合理安排孔加工定位路线能提高孔的位置精度,在XY平面内加工A、B、C、D四孔,安排孔加工路线时一定要注意各孔定位方向的一致性,即采用单向趋近定位方法,完成C孔加工后往左多移动一段距离,然后返回加工D孔,这样的定位方法避免因传动系统反向间隙而产生的定位误差,提高了D孔与其它孔之间的位置精度。
5. 工件的安装与夹具的选择
1)工件的安装
① 力求符合设计基准、工艺基准、安装基准和工件坐标系的基准统一原则。
② 减少装夹次数,尽可能做到在一次装夹后能加工全部待加工表面。
③ 尽可能采用专用夹具,减少占机装夹与调整的时间。
2)夹具的选择
根据数控机床的加工特点,协调夹具坐标系、机床坐标系与工件坐标系的三者关系,此外还要考虑以下几点:
① 小批量加工零件,尽量采用组合夹具,可调式夹具以及其它通用夹具。
② 成批生产考虑采用专用夹具,力求装卸方便。
③ 夹具的定位及夹紧机构元件不能影响刀具的走刀运动。
④ 装卸零件要方便可靠,成批生产可采用气动夹具、液压夹具和多工位夹具。
声明:本网站所收集的部分公开资料来源于互联网,转载的目的在于传递更多信息及用于网络分享,并不代表本站赞同其观点和对其真实性负责,也不构成任何其他建议。本站部分作品是由网友自主投稿和发布、编辑整理上传,对此类作品本站仅提供交流平台,不为其版权负责。如果您发现网站上所用视频、图片、文字如涉及作品版权问题,请第一时间告知,我们将根据您提供的证明材料确认版权并按国家标准支付稿酬或立即删除内容,以保证您的权益!联系电话:010-58612588 或 Email:editor@mmsonline.com.cn。
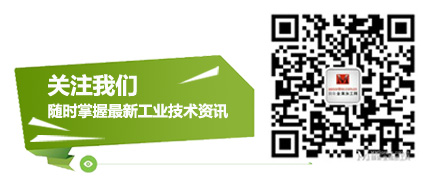
- 暂无反馈