高性能数控机床与虚拟数控加工
航空、航天、汽车、模具、能源装备等制造行业的产品性能要求以及批量生产等方面对其零部件的加工要求越来越高。由于数控切削机床可以实现对复杂零件高精度、高质量、高柔性的加工,在现代产品零件的机械加工中,采用数控加工的比例不断增加。在普通数控机床基础上,过去的数控机床主要沿精密/超精密数控机床和高速加工机床两条轨迹发展。为了满足在数控加工过程中工件材料、零件几何形状、精度和表面质量等方面的新要求,并提高数控机床产品本身的竞争力,从20世纪90年代中期开始,综合了高精度和高速化两个方面的高性能数控机床受到高度重视,进入21世纪以来,高性能切削加工(HighPerformance Cutting)及其主要支撑技术——虚拟数控加工(VirtualCNC Machining)技术成为数控切削加工领域学者和工程师们关注的新热点。国际生产工程学会(CIRP)分别于2004年、2006年召开了第一、二届高性能切削国际会议,就高性能切削加工技术及装备涉及的机床动力学建模、控制、CAM、切削理论、铣削/钻削/磨削、微切削等方向进行了研讨,国内举行的先进制造技术方面的重要会议也已将高性能数控机床及加工工艺技术列为主题之一,可以说,高性能数控机床研发及其支持技术研究应用已成为数控机床发展的一个新趋势。
本文结合国内外文献资料和作者及其团队的部分研究工作,重点介绍和讨论高性能数控加工装备与技术的要求、高性能数控机床关键技术的研究与应用、虚拟数控加工技术以及面向零件工艺特征的虚拟数控加工力学仿真方法研究等内容。
高性能零件加工对数控切削加工装备与技术的要求
现代装备及产品中的高性能零件的特点体现在以下几个方面。
(1)材料特点。
金属材料零件是数控加工的主要对象,各种钢、铝合金等占有很大比例,钛合金、高温合金也有一定比例,金属材料毛坯可以由铸造、锻造、预拉伸、轧制等多种工艺制成,此外,非金属材料零件(主要是复合材料和光学硬脆性材料)的数控加工量也呈现增加的趋势。
(2)结构特点。
零件结构种类多样,如汽车及发动机的箱体、缸体/缸盖、盘、轴等零件,飞机壁板、梁、框、肋、缘条、长桁和接头及骨架等结构零件,航空发动机的叶片/叶盘/叶轮、机匣、盘环件等。此外,由于高性能、轻量化和高可靠性的设计要求,采用整体结构和复杂型面结构的零件比例大大增加,因此零件几何尺寸大、型面复杂、工艺特征多、壁厚小。
(3)工艺特点。
由于材料选用和结构设计上的特点,高性能零件数控切削加工过程中呈现出加工精度要求高、切削加工过程材料去除量大、加工变形控制难度大等特点,对加工质量、变形控制和加工效率提出了很高的要求。另外,现代制造业的发展还要保证零件加工过程满足日益严格的环境友好方面的要求。
高性能产品零件的材料、结构和工艺的特点,对加工质量、效率、成本以及环保等方面提出了更高的要求,高性能切削就是满足上述要求而提出的一个新的理念。所谓高性能切削加工是指在数控切削加工过程中,全面考虑机床、刀具、工件、编程、加工工艺和参数等因素及其相互作用,采用几何仿真、力学仿真的方法,通过对“机床-零件-刀具”工艺系统特性、数控程编、切削参数、走刀路径等的分析,对切削加工过程进行综合优化,实现优质、高效、低成本及绿色的数控加工。
在高性能数控切削加工中,高性能数控机床、高性能切削刀具、高性能数控编程与仿真系统(虚拟数控加工技术)、切削参数和工艺优化技术及工具等是其关键的支撑技术。限于篇幅,本文讨论的重点放在高性能数控机床与虚拟数控加工技术。
高性能数控机床研究与应用
1 高性能数控机床的主要特点
为满足高性能数控切削加工的要求,高性能数控机床应具备如下主要特点:
(1)多轴联动。
一般为四轴或五轴的多轴联动,或在五轴联动控制基础上还可以实现更多轴的控制以及实现复合加工联动控制。引入A/B、A/C坐标的多轴联动可方便地解决复杂结构和型面的加工问题,如叶片、复杂型腔、泵体、多面体等的加工;在多轴联动基础上实现的复合数控加工可以大大缩短工件定位装夹等辅助工作时间,提高机床加工效率。
(2)高速主轴。
最大主轴转速高于12000r/min,可高达42000r/min甚至更高,同时,主轴还应提供足够的功率和扭矩。高速主轴配合使用高性能刀具系统,可以实现高速切削加工,如飞机大型铝合金结构件的高速数控加工中,切削线速度一般达1000~4000m/min,最高切削线速度可达5000m/min以上,同时,高主轴转速使切削时的每齿进给量减小,从而减小了刀齿上的切削负荷。
(3)高动态响应的进给系统。直线进给轴速度可达30~60m/min或更高,新型数控机床的进给加速度可达到1~2g,小型的数控机床可达更高。高性能数控机床采用直线电机驱动的直线轴运动和力矩电机驱动的摆动轴运动,可大大简化机械传动结构,实现所谓“零传动”,并在轴运动控制器中对速度、加速度和加速度变化率的控制曲线(Profile)进行优化,从而抑制运动过程中的谐振,获得非常高的动态响应特性,实现复杂型面、型腔加工过程中频繁加减速条件下的高速进给。
(4)高精度。
直线轴定位精度在微米(μm)数量级,并可实现更高的位置精度。由于进给伺服中采用直线电机驱动、高精度高刚度运动部件构成的运动控制系统,并考虑进给系统中的机电耦合作用,采用全闭环反馈控制、PID+前馈控制甚至更复杂先进控制算法的数字伺服控制以及补偿控制,数控机床的坐标轴运动平稳性和运动精度进一步提高。
(5)高刚度。
主轴系统、进给系统和机床结构应具有良好的静态刚度和动态刚度以及热稳定性。足够高的静态刚度可以抵抗由于机床零部件重力和零件加工时的切削力引起的机床变形,保证刀具与工件在切削过程中的静态位移;优良的动态特性可防止和减小切削过程中由于动态切削过程产生的强迫振动和自激振动,以满足刀具与工件在切削过程中的动态位移要求;良好的热稳定性使得机床在加工过程中受到切削热、环境温度变化等作用时,热变形尽量小。最终,机床高静动态刚度和热稳定性将使零件切削加工获得好的表面质量和高的切削效率。
(6)智能化。
智能化是新一代数控机床的重要特征。智能化主要表现在两个方面,一方面是机床控制的智能化,如在机床轴运动控制上引入前馈控制、预测控制、鲁棒控制等先进控制策略,在加工过程控制上引入自适应控制、学习控制等。另一方面是将专家系统、自动检测及自动补偿功能等嵌入数控系统,例如在数控系统中配备自动编程与仿真、机床状态监测、故障诊断、刀具自动管理及补偿、机床热变形/振动监测与补偿等功能,使数控机床具有更多的“智能”,提高数控系统的控制性能,从而实现机床和加工过程的智能化、最优化控制。
虚拟数控机床与虚拟加工技术
1 虚拟数控机床
在国际生产工程学会2005年的会议上,Y.Altintas、C.Brecher、M.Weck、S.Witt等制造技术领域知名学者联合发表了论文《VirtualMachine Tool》,对虚拟机床技术、研究进展及挑战进行了全面的论述。
本节的主要内容来自他们的这篇重要论文以及作者的部分研究工作。虚拟机床VMT(VirtualMachine Tool)是实际机床产品的计算机仿真模型,也称为机床的虚拟样机,它可以用来像真实的机床一样进行演示、分析和测试。在设计过程,可反复改变机床虚拟模型,并仿真验证各种设计,直到机床性能满足要求。这种虚拟机床技术可以大大缩短机床产品开发周期,显着降低开发成本。采用虚拟样机技术开发现代数控机床的集成开发环境主要包括:
·机床零件的有限元计算;
·机床结构的有限元分析及优化;
·柔性多体耦合仿真;
·3D计算机辅助设计和运动学优化验;
·性能仿真匹配和测试。
VMT是数控机床分析仿真和设计优化的有力工具,当前VMT研究中需要解决的关键问题有:
·“刚性体+柔性体”耦合建模与分析方法;
·机械零件结合面动态特性分析与计算方法;
·“机械结构+伺服系统”耦合的机电系统动态特性建模与分析;
·“机械结构-伺服系统-切削过程”耦合建模与分析方法;
·基于3D实体模型的性能样机建模与分析方法。
2 虚拟数控加工
在实际零件加工之前,在虚拟环境中考虑机床运动学、动力学、数控系统、空间精度、切削力、主轴转矩/功率、加工误差等,实现对加工过程的仿真和优化,从而可以正确、经济和高效地加工出首件合格零件。虚拟加工的本质可以认为是对数控加工过程进行几何仿真和力学仿真,并在两个仿真的基础上优化数控加工切削参数和过程。CAM仿真软件、虚拟机床和切削过程动力学是虚拟加工的重要支持工具。
·NC程序几何仿真——主要解决刀具干涉、碰撞检查、NC程编错误导致的尺寸路径误差等,也可从几何运动方面进行NC程序的部分优化;
·机床结构特性仿真——机床结构动力学、静力学和整体性能(整机进给和主轴驱动)仿真;
·加工动力学仿真——考虑机床动力学和切削过程扰动情况下的轨迹生成、插补、进给等仿真;
·加工过程优化——对各种不同切削条件下的切削力、转矩、功率、振动、生成表面等进行计算和仿真,经过迭代比较进行切削参数和加工工艺的优化。采用CAM仿真软件对NC程序进行走刀轨迹仿真校验、干涉校验等的几何仿真软件已商品化,并在国内制造企业大量应用。当前,虚拟数控加工研究的重点是对切削过程中“机床+工件+工艺(切削过程)系统中的力学仿真问题。
3 面向工艺特征的虚拟数控加工力学仿真研究
对数控加工切削过程进行力学仿真,是虚拟机床和虚拟数控加工的基础。作者领导的团队自主开发了“数控铣削加工动力学仿真系统(SimuCut)”和“数控加工动力学特性测试与分析系统(DynaCut)”,目前已应用于40多个航空、航天、船舶、电子、兵器等军工行业的数控加工车间,为铣削加工切削参数快速优化、提高机床切削加工效率提供了一条新思路和一套快捷方法及工具,在国防科技工业千台数控机床增效工程中,对单台机床的提速增效已取得了明显成效。为了进一步适应实际数控加工过程中零件结构、工艺特征的多样性,在解决铣削过程动力学仿真的基本问题后,我们进一步开展了面向加工工艺特征的虚拟数控加工力学仿真,主要目标是面向零件加工几何特征(如侧壁、深腔、拐角等)和不同走刀方(如直线、圆、螺旋线、摆线等),考虑数控机床动态特性和工件材料特性,在不同的切削参数条件下,进行数控加工过程切削力、主轴转矩/功率、加工振动、刀具变形/工件变形、表面形貌等计算和仿真,根据不同的优化目标,实现切削参数和加工过程优化,并可为虚拟数控机床和虚拟数控加工过程提供力学仿真方法和数据支持。图3给出了铣削加工常见的几何特征之一——直角拐角等切深侧铣加工时进行力学仿真时的输入界面,给定刀具几何参数、铣削方式、铣削用量、切削力系数、刀具模态等参数后,经仿真计算可以得到各向切削力、切屑厚度、主轴转矩/功率、稳定性曲线等。
结束语
高性能数控机床研发及其支持技术已成为数控机床发展的一个重要趋势,将对提高航空、航天、汽车、模具等高性能零件的数控加工质量、效率产生重要作用。虚拟机床技术为缩短新型数控机床产品研发周期、降低开发成本提供了一个新的途径。但VMT不只是一个虚拟功能样机,更不是一个简单的3D模型,采用现有的CAD、CAE软件还难以直接完成建模与分析,其中最关键是需解决机床结构及系统中各环节或零部件之间,及其与切削过程动态之间的耦合关系。虚拟数控加工技术将为虚拟机床建模分析、切削参数优化、切削过程优化等提供重要的基础方法和基本数据。
声明:本网站所收集的部分公开资料来源于互联网,转载的目的在于传递更多信息及用于网络分享,并不代表本站赞同其观点和对其真实性负责,也不构成任何其他建议。本站部分作品是由网友自主投稿和发布、编辑整理上传,对此类作品本站仅提供交流平台,不为其版权负责。如果您发现网站上所用视频、图片、文字如涉及作品版权问题,请第一时间告知,我们将根据您提供的证明材料确认版权并按国家标准支付稿酬或立即删除内容,以保证您的权益!联系电话:010-58612588 或 Email:editor@mmsonline.com.cn。
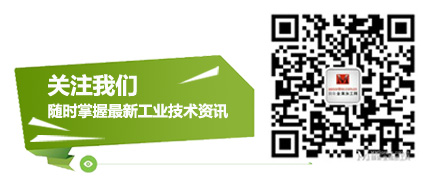
- 暂无反馈