高速干式切削技术的优越性
随着国内外市场对锻钢曲轴的需求越来越大,迫切需要各个生产线迅速提升产能满足客户需求,其中机加线及其数控设备是产能提升的重点。我公司在曲轴精车主轴工序采用了高速干式切削技术,实现了提升产能、节约成本的良好效益。
高速干式切削技术的优越性
在曲轴加工的各个工序中,精车主轴工序是衔接粗加工和精加工的纽带,它不仅可以精确控制曲轴侧台、R角及轴向和径向尺寸,还可以减少精磨主轴CBN砂轮磨耗,减少精磨的加工成本及精磨的单支节拍,是曲轴加工的关键工序之一,我们在此工序中采用了高速干式切削技术。
与中速湿式加工相比,高速干式切削的主要优点如下:单位时间内金属切除量显著提高,切削速度由102m/min提升到180m/min,缩短工时244s,刀片寿命降低7.6%,切削液成本节省10%~12%;加工精度高,保证工艺要求D±0.02mm,表面粗糙度好;通过调整切削力,克服了振动引起的抗力,有利于加工轴颈尺寸大、质量大的曲轴;激振频率高,切削平稳,基本上消除了高频和低频振刀,刀片崩刃机率下降了70%,表面残余应力小;节省了切削液使用及维护费用,同时避免了切削液对环境的污染和对人体的危害。
高速干式切削的技术要求
锻钢曲轴属于难加工材料,其具有强度高(650MPa<σb<900MPa)、硬度大(200机床、刀具都有非常高的要求,同时还要保证工艺尺寸,解决轴颈振刀、延长刀具寿命、降低加工成本等相关难题。
1.对机床的技术要求
数控机床是实现高速切削的首要条件和前提保障,曲轴加工不同于其他工件加工,有时转速可以达到每分钟几千转。通常加工曲轴的设备应具备导轨、顶尖和转塔刚性好、回转精度高以及可提供足够的转矩。这些因素是保证机床对曲轴这类特殊工件进行高速切削的基本要求,这也是采购机床时特别需要注意的要求。
2.对刀具性能的技术要求
高速切削时刀具的失效形式主要是磨损和破碎,刀具要分别按照磨钝标准和破碎寿命选择切削用量来确定刀具寿命。
涂层硬质合金刀具性能要求总结如下:
(1)选择合适的涂层技术
采用MT-CVD+HT-CVD复合涂层技术的刀具综合了多种涂层材料的优点,具有优良的热硬性、高温韧性和耐磨性,能有效解决高速干式切削合金钢刀具使用寿命低的难题。
(2)足够的硬度和韧性
高速切削时,刀具承受的切削力大,要求刀具材料的硬度至少为工件材料硬度的3倍以上,一般涂层刀片硬度大于HRA89.0,经表面强韧处理的复合涂层显微硬度达2 600HV。如果片面追求高硬度刀具材料,易引起刀片崩刃,刀具材料必须要有足够高的韧性。
(3)热化学稳定性好
干式切削的高温能加剧刀具材料与曲轴材料的化学亲和性和材料间组成元素的扩散、溶解,其中的Al2O3涂层在切削过程中形成的惰性保护膜能起到抗氧化和耐扩散磨损的作用,特别是α-Al2O3能在高温下能保持良好的化学稳定性和热稳定性,从而延长刀具寿命。
(4)低摩擦系数
表面TiN涂层能代替切削液的润滑作用,降低刀—屑、刀—工件摩擦产生的切削热,同时提高了刀具的耐用度。另外,断屑器的形状也是影响切削温度的因素之一。刀—屑接触时间长,切削温度升高快,切削刃易钝化。
3.对加工工艺的技术要求
曲轴作为一种特殊形状的细长轴(L/D≈9),顶尖压力过大会造成曲轴弯曲,高速切削过程中能产生很大的惯性离心力,振刀现象在所难免,因此,必须对切削参数、刀具角度、机床性能与曲轴材质进行合理搭配,才能解决数控车振刀问题,保证各个尺寸满足工艺要求。
(1) 工艺参数的合理安排
解决振刀问题是实现高速切削的前提。众所周知,数控车振刀与主轴转速、进给速度和背吃刀量密切相关。通过主切削力、进给力和背向力对振刀的影响进行比较,我们发现:切削过程中必须提供足够的切削力才能克服振动引起的抗力,保证刀具进行平稳切削。
具体的切削用量因曲轴材质、形状等因素有关差距很大,在此不做赘述。
振刀问题解决后,为充分发挥精车淬火前曲轴的加工效率,同时避免精车淬火后曲轴发生再生颤振,影响精磨主轴磨削效率,需对粗车主轴、精车淬火前主轴、精车(或半精磨)淬火后主轴的加工余量进行合理分配。余量的选择因产品材质、机床精度及轴的跳动而异。常按倒推法计算:
精车淬火后主轴颈加工余量为:精车后四主跳动量+刀纹深度×2+A(A=0.2~0.5 mm);
精车淬火前主轴颈加工余量为:淬火后四主跳动量+刀纹深度×2+A(A=0.2~0.5 mm)。
(2) 刀具参数的合理选择
高速切削过程中选择恰当的刀具几何参数,可以使更多的切削热被切屑带走。一般需注意以下几点:①结合干式切削技术要求,高速切削选用比常规刀具略大的正前角可以获得锋利、强韧的切削刃,以减少前刀面与切屑的摩擦。一般选γ0=12°~15°,鉴于弥补大前角对切削刃的强度的削弱,刀片需要刃口强化,主要强化形式是钝圆刃和后刀面刃磨负倒棱,倒棱宽度约0.1~0.3mm。因材质不同,倒棱宽度与曲轴硬度成反比。锻钢曲轴一般不对前刃进行倒棱。②后角的选择主要考虑减少工件与后刀面的摩擦。③较大的负刃倾角可增强刀头的强度,提高切削刃的抗冲击能力,一般选择λs=5°~8°。④根据曲轴材质和切削用量选择合适的断屑器,刀—屑接触长度能直接影响切削的摩擦状况,适当增加摩擦力可有效抑制振动。
(3) 圆角加工工艺
由于粗车主轴机床加工精度低,为保证轴向尺寸,侧台和R角的加工余量比轴颈的余量略大。当车刀快速进给到R角区域时,侧台余量每增加0.01mm,背吃刀量就相应增加1.2倍,切削力增大3倍,导致切削刃破损,尤其是加工材质较硬及淬火后的曲轴材料时。因此,最直接的解决办法是尽可能地减少粗车主轴侧台的加工余量或者在精车主轴颈前对侧台首切。在单支加工节拍允许的情况下,可适当降低切削速度和进给量,这样可以保持高速进给时切削的平稳性,刀片崩碎的机率可降低45% 。从刀具的材质上考虑,可以选择韧性好的刀具材料,崩刃现象可得到明显改观,刀片寿命可提高30%。
(4)振刀控制
曲轴的振刀形式主要有两种,一种是由高频振动引起的鳞状振纹,另一种是由低频振动引起的螺纹状振纹。高频振刀出现的位置具有随机性,对精车主轴工序影响不大,而低频振刀常出现在二、三、四主轴颈的一侧或者两侧,严重的低频振刀可能会产生废品,因此必须加以解决。数控车振刀不是简单的因为某一个环节出现问题而造成,它是由多个因素共同作用形成的,每个主要问题如不能得到有效解决都会引起振刀,因此需要对振动原因进行整体分析,将问题逐一解决。
以下几方面需特别注意:
①不平衡量超差。主轴高速旋转过程中,不平衡量产生的交变应力能导致离心力振动波纹紊乱,引起严重的低频振刀。表2为加工过程中出现严重振刀的曲轴不平衡量测定值。如果出现此情况应及时调整中心孔专机,保证动平衡量不超差。
②调整刀尖高度。加工较软的曲轴材质时,刀尖应略低于中心线,当曲轴材质较硬时刀尖应略高于中心线,具体降低或提高刀尖高度还要根据后角负倒棱的宽度及后刀面的磨损情况来定。
避免顶尖应力集中。当机床进入高速切削状态,重力、切削力、离心力及不平衡量产生的交变应力会集中到顶尖上,其合力的反作用力能使曲轴弯曲变形、跳动超差。一般会在靠近顶尖的轴颈上产生严重振刀。针对此现象,可通过减小顶尖的伸长量、调整顶尖压力值及增强顶尖的抗振强度来解决上述问题。
③增加抗振阻尼。切削过程中,振动的产生能量通过导轨、刀台传递给刀尖,一旦有振动趋势,机床的其他振动能量会迅速传递给振动系统,转化成有害的振动能量,引起严重的低频振刀,通过实验高性能减震垫块能有效的吸收振动能量,同时,还能得到很好的表面粗糙度。
④刀柄的选择。由于平衡铁的存在,需要将刀杆伸出刀台50~80mm。对于重切削难加工工序,选择刚性好的刀柄能提供足够的稳定性、平衡切削流并延长刀具寿命,这意味着外圆车削时可采用高的切削参数。通过上压式(刚性夹紧)、杠杆式和楔块式三种夹紧方式的使用效果发现:由于切削热的影响,楔块式的圆柱销受热产生变形使刀片和刀垫不能很好的贴紧。同样,杠杆式的夹紧力矩不容易控制,过大或者过小也会导致刀片和刀垫不能很好地贴紧,这两种夹紧方式在高速进给时都易产生崩刃。上压式刀柄夹紧力大、夹紧可靠且定位面积大载荷分散抗冲击性强,因此上压式刀柄是重切削加工工序的首选。
声明:本网站所收集的部分公开资料来源于互联网,转载的目的在于传递更多信息及用于网络分享,并不代表本站赞同其观点和对其真实性负责,也不构成任何其他建议。本站部分作品是由网友自主投稿和发布、编辑整理上传,对此类作品本站仅提供交流平台,不为其版权负责。如果您发现网站上所用视频、图片、文字如涉及作品版权问题,请第一时间告知,我们将根据您提供的证明材料确认版权并按国家标准支付稿酬或立即删除内容,以保证您的权益!联系电话:010-58612588 或 Email:editor@mmsonline.com.cn。
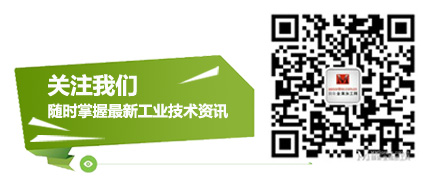
- 暂无反馈