国内数控机床刀具标准
一.国内应用的数控机床工具柄部及配用拉钉标准
1.国家标准GB10944-89《自动换刀机床用7:24圆锥工具柄部40、45和50号圆锥柄》
这个国家标准规定的柄部,在型式与尺寸上与国际标准ISO7388/1完全相同。详见图7.3-1和7.3-1。与ISO7388/1相比,增加了一些必要的技术要求,标注了表面粗糙度及形位公差,以保证刀柄的制造质量,满足自动加工中刀具的重复换刀精度要求。它主要应用于镗铣类加工中心机床的各种刀柄。
2.国家标准所规定的拉钉,《自动换刀机床用7:24圆锥工具柄部40、45和50号圆锥柄用拉钉》
这个国家标准所规定的拉钉,在型式与尺寸上与ISO7388/Ⅱ相同。可与前述标准GB10944-89中所规定的柄部配合使用。
3.日本标准JIS B6339-1986《加工中心机床用工具柄部及拉钉》
这个标准只适用于日本进口的加工中心机床及过去几年我国的部分机床厂与日本合作设计和生产的加工中心机床。它是在日本机床工业协会标准MAS403-1982的基础上制订出来的,在日本得到广泛的应用。我国1985年以后设计的加工中心机床已改用新的国家标准GB10994和GB10945。
4.国家标准GB3837-83《机床工具7:24圆锥联结》
这种锥柄主要用于手动换刀数控机床及重型镗铣床等。
二.整体式工具系统标准JB/GQ5010-1983《TSG工具系统 型式与尺寸》
TSG工具系统中的刀柄,其代号(按1990年国家标准报批稿)由四部分(JT-45-Q32-120)组成,各部分的含义如下:
JT-表示工具柄型代码。
45-对圆锥柄表示锥度规格。
Q32-表示工具的规格。
120-表示刀柄的工作长度。
它所表示的工具为:自动换刀机床用7:24圆锥工具柄(GB10944),锥柄为45号,前部为弹簧夹,最大夹持直径32mm,刀柄工作长度(锥柄大端直径φ57.15mm处到弹簧夹头前端面的距离)为120mm。
表1 工具柄部型式代号
代 号 工 具 柄 部 型 式
JT 自动换刀机床用7:24圆锥工具柄 GB 10944-89
BT 自动换刀机床用7:24圆锥BT型工具柄 JIS B6339
ST 手动换刀机床用7:24圆锥工具柄 GB 3837.3-83
MT 带扁尾莫氏圆锥工具柄 GB 1443-85
MW 无扁尾莫氏圆锥工具柄 GB 1443-85
ZB 直柄工具柄 GB 6131-85
表2 工具的用途代号及规格参数
用途代号 用途 规格参数表示的内容
J 装直柄接杆工具 装接杆也直径—刀柄工作长度
Q 弹簧夹头 最大夹持直径—刀柄工作长度
XP 装削平型直柄工具 装刀孔直径—刀柄工作长度
Z 装莫氏短锥钻夹头 莫氏短锥号—刀柄工作长度
ZJ 装莫氏锥度钻夹头 贾氏锥柄号—刀柄工作长度
M 装带扁尾莫氏圆锥柄工具 莫氏锥柄号—刀柄工作长度
MW 装无扁尾莫氏圆锥柄工具 莫氏锥柄号—刀柄工作长度
MD 装短莫氏圆锥柄工具 莫氏锥柄号—刀柄工作长度
JF 装浮动绞刀 绞刀块宽度—刀柄工作长度
G 攻丝夹头 最大攻丝规格—刀柄工作长度
TQW 倾斜型微调镗刀 最小镗孔直径—刀柄工作长
TS 双刃镗刀 最小镗刀直径—刀柄工作长度
TZC 直角型粗镗刀 最小镗孔直径—刀柄工作长度
TQC 倾斜型粗镗刀 最小镗孔直径—刀柄工作长度
TF 复合镗刀 小孔直径/大孔直径—孔工作长度
TK 可调镗刀头 装刀孔直径—刀柄工作长度
XS 装三面刃铣刀 刀具内孔直径—刀柄工作长度
XL 装套式立铣刀 刀具内孔直径—刀柄工作长度
XMA 装A类面铣刀 刀具内孔直径—刀柄工作长度
XMB 装B类面铣刀 刀具内孔直径—刀柄工作长度
XMC 装C类面铣刀 刀具内孔直径—刀柄工作长度
KJ 装扩孔钻和铰刀 1:30圆锥大端直径—刀柄工作长度
数控刀具国家标准
一.可转位刀具刀片型号编制标准
1.可转位车刀型号表示规则
GB/T5343.1,它等效采用ISO5680-1989。它适用于可转位外圆车刀、端面车刀、防形车刀及拼装复合刀具的模块刀头的型号编制。其型号也是由按规定顺序排列的一组字母和数字代号所组成。
2.可转位带孔铣刀型号表示规则
它是在ISO7406-1986的基础上制订的。它适用于可转位面铣刀、三面刃(槽)铣刀、套式立铣刀及圆柱形铣刀型号的编制。其型号由11个号位组成(面铣刀只有10个号位,没有第11个号位)。前1~4号位表明刀体的特征。波折号后边的号位表示刀片装夹方式和刀片特征。
3.可转位带柄铣刀型号表示规则
它是在国际标准ISO7848-1986的基础上制订的。它的型号也由11个号位组成。其中有5个号位表示刀体的特征,两个号位表示柄部的特征,另外4个号位则表示刀片的装夹方法及其切削刃长度的特征。
4.可转位刀片型号表示规则
GB2076-87,等效ISO1832-85,国内外硬质合金厂生产的切削用可转位刀片(包括车刀片和铣刀片)的型号都符合这个标准。它是由给定意义的字母和数字代号,按一定顺序排列的十个号位组成。其中第8和第9个号位分别表示切削刃截面形状和刀片切削方向,只有在需要的情况下才予标出。
二.可转位刀片标准
1.GB2079-87(代替GB2079-80)无孔的硬质合金可转位刀片:此标准等采用国际标准ISO0883-1995。标准中规定了TNUN、TNGN、TPUN、TPGN、SNUN、SNGN、SPUN、SPGN、TPUR、TPMR、SPUR、SPMR共12种类型刀片的系列尺寸。
2.GB2077-87(代替GB2077-80)硬质合金可转位刀片圆角半径:此标准等效采用国际标准ISO3286-1976。标准规定刀尖圆角半径rε的尺寸系列为0.2、0.4、0.8、1.6、2.0、2.4、3.2mm。
3.GB2078-78(代替GB2078-80)带圆孔的硬质合金可转位刀片:此标准等效采用国际标准ISO3364-1985。标准中规定了TNUM、TNMM、TNUG、TNMG、TNUA、TNMA、ENUM、FNMM、WNUM、SNUM、SNMM、SNUG、SNMG、SNUA、SNMA、CNUM、CNMM、CNUG、CNMG、CNUA、CNMA、DNUM、DNMM、DNUG、DNMG、DNUA、DNMA、VNUM、VNMM、VNUG、VNMG、VNUA、VNMA、RNUM、RNMM共36种类型的带圆孔硬质合金刀片尺寸系列。
4.GB2081-87(代替GB2081-80)硬质合金可转位铣刀片:此标准等效采用国际标准ISO3365-1985。此标准规定了SNAN、SNCN、SNKN、SPAN、SPCN、SPKN、SECN、TPAN、TPCN、TPKN、TECN、FPCN、LPEX共13种类型的可转位铣刀片系列尺寸。
5.GB2080-87(代替GB2080-80)沉孔硬质合金可转位刀片:此标准等效采用国际标准ISO6987/1-1993。标准中规定了TCMW、TCMT、WCMW、WCMT、SCMW、SCMT、CCMW、CCMT、DCMW、DCMT、RCMW、RCMT共12种类型的沉孔硬质合金可转位刀片系列尺寸。
三.可转位铣刀标准:
1.可转位立铣刀国家标准GB5340-85:它是参照国际标准ISO6262/1-1982和ISO6263/2-1982制订的。有削平型直柄立铣刀和莫氏锥柄立铣刀两部分。
2.可转位三面刃铣刀国家标准GB5341-85:它是参照国际标准ISO6986-1983制订的。
3.可转位面铣刀国家标准GB5342-85:它是参照国际标准ISO6462-1983制订的。
4.可转位螺旋立铣刀:标准规定了直径32~100mm直柄或锥柄的立铣刀。因其刃部较长,由沿螺旋线方向排列的多片硬质合金可转位刀片相互交错搭接而成,适用于粗铣。
数控刀具(分两大系统:车削系统和铣镗削系统)的特点与要求
数控刀具要求精度高、刚性好、装夹调整方便,切削性能强、耐用度高。合理选用既能提高加工效率又能提高产品质量。
刀具选择应考虑的主要因素
1、被加工工件的材料、性能:金属、非金属,其硬度、刚度、塑性、韧性及耐磨性等。
2、加工工艺类别;车削、钻削、铣削、镗削或粗加工、半精加工、精加工和超精加工等。
3、工件的几何形状、加工余量、零件的技术经济指标。
4、刀具能承受的切削用量。
5、辅助因数:操作间断时间、振动、电力波动或突然中断等。
车削系统(整体式工具系统)
1、组成:由刀片(刀具)、刀体、接柄(或柄体)、刀盘等
2、可转位刀片的代码及参数
3、可转位刀片的断屑槽槽型:断屑自如、排屑流畅
4、可转位刀片的夹紧方式:楔块上压式、杠杆式、螺钉上压式要求:夹紧可靠、定位准确、排屑流畅、结构简单、操作方便
5、可转位刀片的选择
1)、刀片材料选择:高速钢、硬质合金、涂层硬质合金、陶瓷、立方碳化硼或金刚石
2)、刀片尺寸选择:有效切削韧长度、被吃刀量、主偏角等
3)、刀片形状选择:依据表面形状、切削方式、刀具寿命、转位次数等
4)、刀片的刀尖半径选择:
A、粗加工、工件直径大、要求刀刃强度高、机床刚度大时选大刀尖圆弧
B、精加工、切深小、细长轴加工、机床刚度小选小刀尖圆弧
刀具系统(模块式工具系统)
1、组成;刀片(刀具)、刀杆(或柄体)、主轴或刀片(刀具)、工作头、连接杆、主柄、主轴所组
2、数控铣削刀具的选择
1)、铣刀类型的选择:
A、加工较大平面选择面铣刀,
B、加工凸台、凹槽、小平面立铣刀,
C、加工毛坯面和粗加工孔选择镶硬质合金玉米铣刀,
D、曲面加工选择球头铣刀,
E、加工空间曲面模具型腔与凸模表面选择模具铣刀,
F、加工封闭键槽选键槽铣刀,等等
2)、铣刀参数的选择
A、面铣刀主要参数选择
a)、标准可转位面铣刀直径在Φ16-Φ630):粗铣时直径选小的,精铣时铣刀直径选大的,
b)、依据工件材料和刀具材料以及加工性质确定其几何参数:
铣削加工通常选前角小的铣刀,强度硬度高的材料选负前角,工件材料硬度不大选大后角、硬的选小后角,粗齿铣刀选小后角,细齿铣刀取大后角,铣刀的刃倾角通常在-5--15度,主偏角在45-90度
B、立铣刀主要参数选择
a)、刀具半径r应小于零件内轮廓最小曲率半径
b)、零件的加工高度H≤(1/4-1/6)r
c)、不通孔或深槽选取l=H+(5~10)mm
d)、加工外形及通槽时选取l=H+rε+(5~10)mm
e)、加工肋时刀具直径为D=(5~10)b
f)、粗加工内轮廓面时,铣刀最大直径D
D=d+2[δsin(φ/2)-δ1]/[1-sin(φ/2)]
3、加工中心刀具的选择
加工中心刀具通常由刃具和刀柄两部分组成,刃具有面加工用的各种铣刀和孔加工用的各种钻头、扩孔钻、镗刀、铰刀及丝锥等,刀柄要满足机床主轴自动松开和夹紧定位,并能准确地安装各种刃具和适应换刀机械手的夹持等要求。
1)、对加工中心刀具的基本要求
A、刀具应有较高的刚度
B、重复定位精度高
C、刀刃相对主轴的一个定位点的轴向和径向位置应能准确调整
2)、孔加工刀具的选择
A、钻孔刀具及其选择
B、扩孔刀具及其选择
C、镗孔刀具及其选择,应特别重视刀杆的刚度
3)、刀具尺寸的确定
主要是刀具的长度和直径的选择,如加工孔依据其深度和孔径选择
4、刀柄的选择
1)、依据被加工零件的工艺选择刀柄
2)、刀柄配备的数量:与被加工零件品种、规格、数量、难易程度、机床负荷有关
3)、正确选择刀柄柄部形式
4)、坚持选择加工效率高的刀柄
5)、综合考虑合理选用模块式和复合式刀柄
工具系统
1、工具系统发展趋势:向着柔性制造系统和模块化组合结构发展
2、车削类工具系统
3、镗铣类工具系统:分整体失和模块式工具系统
4、刀具管理系统:
1)、是柔性制造系统中一个很重要、技术难度很大的系统
2)、刀具管理系统的任务
3)、刀具管理系统的基本功能
原始资料、系统计划、硬件配置和软件系统等等。
总结:
1、数控刀具要求精度高、刚性好、装夹调整方便,切削性能强、耐用度高。合理选用既能提高加工效率又能提高产品质量。
2、刀具选择应考虑的主要因素。
3、工具系统向着柔性制造系统和模块化组合结构发展。
声明:本网站所收集的部分公开资料来源于互联网,转载的目的在于传递更多信息及用于网络分享,并不代表本站赞同其观点和对其真实性负责,也不构成任何其他建议。本站部分作品是由网友自主投稿和发布、编辑整理上传,对此类作品本站仅提供交流平台,不为其版权负责。如果您发现网站上所用视频、图片、文字如涉及作品版权问题,请第一时间告知,我们将根据您提供的证明材料确认版权并按国家标准支付稿酬或立即删除内容,以保证您的权益!联系电话:010-58612588 或 Email:editor@mmsonline.com.cn。
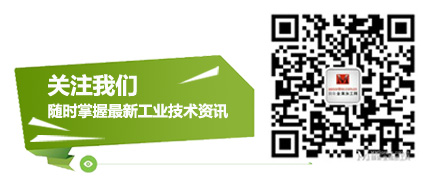
- 暂无反馈