CAM系统中粗加工刀具轨迹的优化设计
一、前言
复合加工、高速加工以及高精度加工是当前CAM系统重点研究的三个问题。其中复合化加工要做到合理地确定各个工步以及各个工步的功能参数。必须平衡各个工步在各加工阶段(粗加工、半精加工和精加工)的切削量,这样才能平衡刀具载荷,使载荷保持在刀具使用的合理范围之内,以提高刀具寿命和加工效率,这也是高速加工的基本要求之一。一般应采用系列刀具从大到小分次加工,以达到所需尺寸,而应避免用小刀具一次完成加工。粗加工时大多采用大直径刀具,与小刀具相比,它的刚性好、抗振及热变形小,而且能可靠地断屑或卷屑,以利于切屑的排除。优化设计粗加工时的刀具轨迹,可以给精加工留下较小的残余量,提高残余量加工的效率。
二、刀具轨迹的优化设计
在加工零件的侧面时,刀具中心轨迹必须相对于加工表面向外移一个刀具半径,才能避免误切。但如果侧面形状中有曲率半径小于刀具的圆弧,那么外移后,圆弧与直线常常没有交点,因此得不到刀具的加工轨迹。此时,为了保证粗加工的顺利进行,一般的方法是把小圆弧作为直线看待,下一步再换用更小的刀具来完成加工。
但是,为了让粗加工时能尽可能多地铣削,应该使刀具轨迹更贴近加工表面,为下次的小刀具加工留下更小的残余量,为此,我们提出了如下的刀具轨迹优化设计方法。
首先以刀具的半径R来进行移位补偿(offset),如零件待加工面有曲率半径小于刀具半径R的凹圆弧时,计算出的刀具轨迹不连续,移位补偿计算失败。这时,可进行如下处理:设分割数为N,首先以R/N为假想的刀具半径,来做移位补偿计算,如果还不成功,则可以把N加大,或如上所述,不进行优化,以近似直线进行粗加工。但是,若以直线代替凹圆弧,精加工时需铣削过大的残余量,影响加工结果。若以R/N为假想的刀具半径,移位补偿成功的话,相对于加工表面向外移R/N,得到T1,再用(1-1/N)R相对T1进行移位补偿,成功的话得到CL1,即是优化后的刀具中心轨迹。不成功的话,继续相对于加工表面向外移2R/N,得到T2,再用(1-2/N)R对T2进行移位补偿,直到成功。因为事先确认过R/N移位补偿是成功的,所以按上述方法试下去,一定可以成功。
三、加工计算实例
一个待加工的零件模型,其上侧面中包含有曲率半径为30mm和35mm的凹圆弧,粗加工时,选用半径为40mm的刀具,如果不进行轨迹优化设计,则凹圆弧没被加工,全部作为残余量由下一道工步用小刀具来加工,按我们的设计方法进行轨迹优化后,90%的小凹圆弧部分都被铣掉,仅留10%左右作为残余量加工。这样完全符合复合化加工中平衡各工步切削量的要求。
四、结束语
关于分割次数N的设定,要考虑到两个方面的影响。N过大,计算量增大,影响到CAM编程的速度,N太小,又会使刀具轨迹优化程度不高,残余量较大。根据我们的经验,N一般取为7较好。
随着CAM技术应用的深入,对CAM的细部进行研究,提高零件的加工精度和效率是众多企业非常关心的问题。上面介绍的刀具轨迹优化设计方法,已经成功应用于IE-CAM系统中,该软件已在日本中小企业中得到使用,并获得了好评。
声明:本网站所收集的部分公开资料来源于互联网,转载的目的在于传递更多信息及用于网络分享,并不代表本站赞同其观点和对其真实性负责,也不构成任何其他建议。本站部分作品是由网友自主投稿和发布、编辑整理上传,对此类作品本站仅提供交流平台,不为其版权负责。如果您发现网站上所用视频、图片、文字如涉及作品版权问题,请第一时间告知,我们将根据您提供的证明材料确认版权并按国家标准支付稿酬或立即删除内容,以保证您的权益!联系电话:010-58612588 或 Email:editor@mmsonline.com.cn。
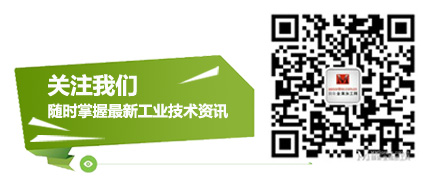
- 暂无反馈