颗粒增强复合材料加工表面粗糙度及刀具设计
一、引言
复合材料是由两种或多种不同材料组成的非均质体,其基体与加入体的物理性能和力学性能往往相差很大。如复合材料的基体一般都是普通材料,但其增强体通常都是高强度或高硬度的材料。在复合材料中,加入其它物相的目的通常是为了增强或增韧。例如,含碳纤维的磨料,其耐磨性能是普通中碳钢的1000倍,由于加入了比硬质合金还要硬的碳化硅颗粒,碳化硅颗粒增强金属基复合材料的耐磨性能得到了极大的提高。
由于碳化硅颗粒增强铝基复合材料(SiCp/Al),具有优良的物理、机械性能,即重量轻、比强度和比刚度高、热膨胀系数小、尺寸稳定性好,且具有良好的导热性能和耐磨、抗腐蚀特性。这类材料各向同性,克服了纤维增强型材料常存在的各种缺陷,而且制备工艺简单,成本低,因而成为复合材料研究领域中的一个热点。目前,在美、日、英、德等工业发达国家,其SiCp/Al在航空、航天和汽车制造等工业部门得到了广泛的应用。我国在这方面的研究开发也做了不少工作。如华南理工大学研制的铝、铜基耐磨复合材料,性能良好,目前已用于军工和汽车等行业。
在SiCp/Al复合材料中,由于以SiC陶瓷颗粒作为增强相而使其硬度、强度和耐磨性大幅度地提高,然而却使加工时刀具磨损严重,难以保证零件加工精度和表面质量,这在很大程度上阻碍了这种材料的推广应用。国内外的研究表明,切削SiCp/Al复合材料所得到的表面往往不是由刀刃直接切出,而是常有凹坑、非切削曲面、鳞刺和积屑瘤存在。相对硬质合金来说,采用聚晶金刚石和聚晶立方氮化硼等超硬刀具加工可取得较好的加工效果,但其成本高,而且刀具对加工表面熨压作用弱,加工过程中脱落的颗粒会损坏加工表面,大的硬质颗粒将显著影响复合材料的切削性能和加工表面质量。
为了解决切削颗粒增强金属基复合材料时加工表面粗糙、质量差,刀具磨损快的问题,对影响加工表面粗糙度的因素和切削表面成形机理及刀具磨损现象进行了分析和多次试验后,设计出具有光整熨压作用的硬质合金切削刀具。
二、颗粒增强金属基复合材料的加工表面形貌及成形机理
1.加工表面形貌特点
用YG3刀具刨削SiC颗粒增强铸铝材料。对SiCp/Al的切削表面观察可知,在已加工表面上存在各种加工导致的缺陷。如:颗粒破碎和脱落而留下的不规则凹坑,碎颗粒被刀刃和后刀面推挤而使表面产生的犁沟,切削时被压下后又弹起的颗粒,切削时因刀具挤压、摩擦工件导致基体材料受热软化涂抹或熔融的加工表面,切削刃前受挤压区颗粒与颗粒之间裂纹贯穿而产生的不规则自由表面以及因磨损的切削刃复制出的不平整表面等。试验结果表明,增强颗粒的份量、形状,尤其是颗粒度大小对复合材料的已加工表面形貌影响很大,加工粗大颗粒增强的复合材料时,其加工表面粗糙。
2.加工表面成形机理
研究结果表明,在切削颗粒增强复合材料的过程中,切削力与变形之间的关系比切削传统材料复杂得多,基体与增强体之间的协同效应对复合材料受力后的行为影响很大。复合材料中的增强体是基体塑性变形的障碍,这使得复合材料的切削变形机理不同于普通金属材料。切削时,材料在切削力作用下,由于材料的不均匀性,在强度薄弱处和有缺陷处形成微观裂纹核,然后裂纹极快地向前方扩展,使材料在切削刃前方开裂,形成分离面(原始切削表面)。切削刃分流点以上的材料,经剪切区形成切屑流出,分流点以下的材料经切削刃钝圆的推挤、熨压形成已加工表面。显然,颗粒增强复合材料的切削表面并非全部由切削刃直接切出,在很大程度上与原始潜在裂纹的形状和刀具熨压增强颗粒的情况有关。而原始裂纹的情况具有很大的随机性,往往与材料的组织结构有关。在纵向车削外圆表面时,情况与上述稍有不同,已加工表面是由切削刃钝圆、刀尖过渡圆弧部分以及刀具副切削刃的切削和熨压作用共同形成的。
三、影响SiCp/Al加工表面粗糙度的因素
1.试验条件
为了提高颗粒增强金属基复合材料的加工表面质量和设计出合理的切削刀具,首先对切削条件和复合材料组织结构对颗粒增强金属基复合材料加工表面粗糙度的影响进行研究,并进行了如下切削试验。
选用三种不同颗粒度和体积分数的SiC颗粒增强铝基复合材料进行试验。其颗粒度参数分别为:1号材料:14μm,10%;2号材料:40μm,20%;3号材料:63μm,20%。基体材料为铸铝合金ZL109。试件经160MPa成型挤压冷却制备成中空圆柱体,并经T6热处理。
采用聚晶金刚石刀具(PCD)进行切削。刀具几何参数为:前角γ0=0°,后角α0=11°,主偏角κr=75°,副偏角κr′=15°,刀尖圆弧半径rε=0.20mm。考虑到3号材料中有较大的SiC颗粒,切削时有较大的冲击,所以刀具采用0°前角。
试验选用的切削参数范围是:切削速度vc=80~250m/min,进给量f分别为015mm/r、0.20mm/r、0.24mm/r、0.28mm/r、0.30mm/r,切削深度(背吃刀量)ap为0.2mm、0.4mm、0.6mm、0.8mm、1.0mm。
2.试验结果与分析
从试验所得的曲线来看,随着切削速度vc的增加,已加工表面粗糙度稍有下降。这是由于随着切削速度的增加,切削变形减少,裂纹和鳞刺等也减少,同时温度的上升使切削时被压下的增强相颗粒的弹性恢复减少所致。由于切削变形增加的缘故,因此,随着切削深度ap的增加,材料的已加工表面粗糙度的变化也不明显,只是略有上升。
由试验结果可知,随着进给量f的增大,加工表面的粗糙度会急剧增大。在vc=80~200m/min的不同切削速度下改变进给量进行切削,其试验结果具有相同的规律性。Ra值在3.15~11.0μm范围内变化。
比较试验结果还发现,在改变切削速度和切削深度时,所获得的表面粗糙度值均低于改变进给量切削时的表面粗糙度,这是因为前者采用了较小的进给量(f=0.10mm/r)。由于进给量小于刀尖圆弧半径rε,在切削过程中,切削表面被重复挤压,因而表面粗糙度得到改善。而当进给量f等于或大于刀尖圆弧半径rε时,切削表面由刀具一次性切出,不再有熨压修整作用,因此,已加工表面具有颗粒增强复合材料的切削表面特征。
从试验结果还可以看到材料组织结构对加工表面粗糙度的影响。由于材料1的增强颗粒尺寸(14μm)比材料2(40μm)要小,故切削得到的加工表面粗糙度值也小。这是由于在颗粒增强复合材料中,基体与增强体之间的协同效应对其切削行为有很大的影响,材料中的增强体是基体塑性变形的障碍,因而切削变形增加,加工表面粗糙度增大。这一结论与很多学者的研究结果是一致的。但试验结果发现,颗粒尺寸较大的材料3的切削表面粗糙度几乎都小于其它两种材料,这与常规的结论相反。据分析,这是由于含有粗大增强颗粒的复合材料结构上的不均匀性导致加工中局部基体产生严重的塑性变形,再加上切削粗大的硬颗粒引起刀具急剧磨损和破损,因此切削温度很高,基体受热软化并被磨损了的后刀面挤压而使加工表面较为平整。
四、改善颗粒增强金属基复合材料切削性能的刀具设计
1.切削颗粒增强金属基复合材料时刀具的磨损
在SiCp/Al材料中,由于碳化硅颗粒的硬度高达HV2700~3200,而常规YG类硬质合金刀具的硬度仅为HV1800左右,所以在加工过程中,碳化硅颗粒与前、后刀面发生剧烈的摩擦,从而加速刀具磨损。试验结果发现,在车削外圆工件时,刀具的主、副后刀面的磨粒磨损是刀具的主要失效形式,这在材料的颗粒度较小时尤为明显。当SiC颗粒度较大时,刀具在切削过程中,由于材料的局部不均匀和非连续性,造成对刀具的冲击,所以在主切削刃处往往发生崩刃。随着切削时间增加,崩刃处呈钝圆并有沟纹,从而造成加工表面质量恶化。
2.切削刀具的设计
颗粒增强金属基复合材料的切削加工难点在于刀具磨损很快,普通硬质合金刀具切削30s,刀具磨损VB已大于0.4mm,而且加工表面随机性大,质量差。这主要是这种材料由于具有不连续的、硬度相差很远的多相结构,材料的切削性能表现出塑、脆两性(总体硬度低、但切屑呈单元或崩碎状),磨钝的刀具往往靠硬挤较软的基体而形成粗糙的表面。从上述对SiCp/Al加工表面成形机理和表面粗糙度切削试验结果分析可知,颗粒增强复合材料中增强相SiC颗粒的尺寸、形态、体积分数和切削用量中的进给量是影响切削表面粗糙度的主要因素。所以在刀具设计中,必须针对材料切削时弹、塑性变形的特点,有效地减轻刀具—工件间的挤压滑擦。通过合理设计刀具,改变材料受力情况,诱导材料内剪切带网络和裂纹的扩展沿理想切削线方向进行,在刃前区材料中形成潜在分离面,再由切削刃对其进行压熨修平,从而达到主动控制切削加工过程,获得良好的切削加工表面质量及延长刀具寿命的目的。
经反复试验,设计的切削刀具的几何参数为:刀具前角为5°~10°,具有较大的刀具后角和大的修光圆弧半径;前刀面具有大的负倒棱前角。倒棱的宽度和前角与材料增强相颗粒大小有关,后接圆弧过渡的熨压带,以利于使凸出的硬质点向加工表面下压,减小其对切削刃和熨压带的划擦磨损。较大的前角使切屑能以一定的压力沿前刀面顺利流出,由于切屑中SiC颗粒对前刀面的磨擦作用,在一定程度上可实现刀具的“自磨锐”。
根据这一思路,设计了具有熨压光整作用的硬质合金外圆车刀。刀具材料为YG8,刀具几何参数为:前角γ0=6°,主后角α0=10°,主偏角κr=90°,副偏角κr′=15°,刀尖圆弧半径rε=0.20mm。此外,在副切削刃与刀尖连接处,刃磨出大圆弧过渡,并在副切削刃上磨出负倒棱。
3.熨压光整刀具的试验结果
试验结果表明,刀具采用90°主偏角可有效减少切削时刀具对工件的径向分力,减轻由此产生的材料中硬颗粒的回弹。再通过刀具修光棱面的熨压、光整作用,使已加工表面的粗糙度明显下降。此外,刀具的熨压作用可使已加工表面发生延展和拉伸,产生基体材料塑性流动,从而可弥合表面微观裂纹,减少应力集中现象。
从试验可知,为了取得最佳的切削表面效果,刀具的引导光整棱面,其高度应小于轮廓微观不平度的平均高度,以减少母体材料的受压弹性变形;其宽度应大于进给量f,以实现连续的熨压。对于不同颗粒尺寸和体积分数的SiCp/Al材料,引导光整面的尺寸会稍有变化,可通过试验进行优化。
为了验证新型刀具的效果,对1、2号材料进行了切削试验。测试结果显示,对材料1车削15分钟后,刀具未产生明显的磨损带,继续车削材料2约40分钟后,刀具光整棱面的宽度仅增加了0.1mm。在整个切削试验中,已加工表面的粗糙度值基本稳定,Ra最大值不超过0.8μm。经切削光整加工后,试验材料的加工表面粗糙度测试结果为:材料1的已加工表面的粗糙度Ra的平均值为1.08μm;材料2的粗糙度Ra的平均值为0.52μm,均小于由PCD刀具切削的加工表面粗糙度试验结果。熨压刀具与常规刀具相比,由于具有熨压光整作用,已加工表面的粗糙度明显下降。
声明:本网站所收集的部分公开资料来源于互联网,转载的目的在于传递更多信息及用于网络分享,并不代表本站赞同其观点和对其真实性负责,也不构成任何其他建议。本站部分作品是由网友自主投稿和发布、编辑整理上传,对此类作品本站仅提供交流平台,不为其版权负责。如果您发现网站上所用视频、图片、文字如涉及作品版权问题,请第一时间告知,我们将根据您提供的证明材料确认版权并按国家标准支付稿酬或立即删除内容,以保证您的权益!联系电话:010-58612588 或 Email:editor@mmsonline.com.cn。
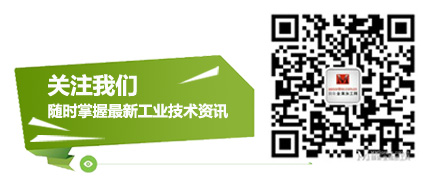
- 暂无反馈