合理选择刀具的重要因素
切断工序考虑因素根据最近的一份国际调查结果显示,用户重视生产效率、加工稳定性、无故障切削、刀具寿命可预测性以及零件质量一致性,并将其列为切断工序主要的优先考虑因素。
切断工序面临的挑战切断工序看上去或许相当直截了当,并且也确实如此,但是为了在保证现代车削的高生产效率时安全地执行这些工序,就需要克服所带来的切削挑战。这之中面临的主要问题仍是:毛刺和飞边形成、切屑形成和排屑、振动趋势以及不一致且过早的刀具磨损。
值得庆幸的是,如果选择合适的刀具并正确地加以应用,那么在今天这一切都不是问题。
刀具选择的第一步首先,需要确立最适合于工序的刀柄类型和刀具系统。在这里,尤其是工件直径起到了至关重要的作用,因为刀柄与所需的切削深度直接相关。切断时大多数切削深度处于6~28mm的中等加工范围之内。深切断的切削深度为28~55mm,而浅切断则为0.25~6mm。还有其它极端的情况。选择刀柄时,通用性和稳定性之间可能出现必要的折中。相关的批量大小和操作变化将影响到选择方向。由于刀具悬伸可设置成适合不同的直径,因此就可将带可调整刀板的刀具用于各种各样的工件直径。
另一方面,带整体式增强刀板的刀柄只适合一定范围的直径,但能提供最大的强度。两种不同的切断刀具类型之间是通用的切断刀具,具有适合单刃或双刃刀片的螺钉式或弹性夹紧。在这里,选择最大的刀柄尺寸,例如刀柄和刀板高度,增加了刀具的稳定性,从而适应不同切深的变化。 螺钉夹紧意味着最高的刀片及刀柄稳定性,而弹性夹紧则可利用窄刀具增加通用性和可达性,这样就只需切削少量材料,并且机床功率也较低。最佳的刀片选择步骤切削刃至关重要。它将在切削中引导刀具,并控制切屑,同时决定飞边和毛刺的形成以及或多或少的提高材料的切削效率。
刀具稳定性的根本所在是相对较薄的刀片与刀柄之间的接口质量。为了保持稳定性,就需要良好的轨道和V形刀片座结构,并最好与相对较长的刀片配合使用,这种结构对切断刀具性能来说至关重要。刀片宽度因切断刀具的切削深度能力而异,小切削深度(工件直径)可使用薄刀片,而大切削深度则需使用更宽的刀片以保证强度。刀柄上的刀片座型号与刀片宽度相对应,每种系统都有其特定的刀片宽度范围,例如CoroCut单、双刃系统具有八种不同的刀片宽度,范围从1.5~8mm不等;而CoroCut 3则适合于浅切断,具有3种刀片宽度,范围介于1~2mm之间。
当为工序选择刀片槽形和牌号时,应当确立切削刃锋利性、强度和宽度最合适的组合,以确保尽可能高的每转进给量,从而获得最大的生产效率。锋利的刃槽形易于切削,所需机床功率小,并且最小化了振动趋势。坚固的槽形负前角更大,切削刃也得到增强,因此能承受住要求更苛刻的切削和粗加工,并且可以实现更高的进给率。加工条件和操作变化指明了选择方向,并且通常存在折中,尤其在需要一定程度的通用能力时,半精加工槽形就是其良好选择。
通过选择当今的不同刀片,就能获得各种最佳化的可能性——Wiper(修光刃)刀片用于提高表面质量和进给;而增强的刀片圆角则可获得更高的进给能力和安全性,并通过更软的切削作用和毛刺最小化实现良好的切削控制。对于刀片牌号选择,切削刃强度应该是最初要优先考虑的因素,因为强度可确保切断工序的安全性。这意味着应优先考虑韧性,而不是更锋利和更硬的槽形和牌号。
其次基于操作因素和加工条件获得合乎要求的表面质量和进给率,并继续改进牌号使其更为耐磨,从而获得更高的进给和更长的刀具寿命。通过应用最新且广泛的PVD涂层牌号使工艺变得更为简单。这种牌号能够提供具有高进给能力的通用解决方案,并且对大多数工件材料都进行了优化。(GC1125)加工时对切削刃磨损的检验和基本分析指出了为获得最佳性能而进行的切削参数调整或可能的替换牌号。基本指标是切削刃变形,这意味着切削刃太韧了;而切削刃崩碎则意味着切削刃太硬,记得采用推荐的切削参数。
最小化飞边和毛刺毛刺形成是切断工序中的一个控制问题,也是一项刀片选择因素。切削刃的前角(主偏角)很大程度上决定毛刺的形成——0°主偏角一般会产生最笔直的切削路径和最佳的表面质量,但是会在切口末端留下毛刺。在切断的部分落下并且切削刃通过工件中心后,斜角刃就能最小化或完全切掉毛刺。由于很容易控制刀具偏离预期的直刀具路径,因此具有较大前角的切削刃会对切口的直线度产生负面影响。出于这个原因,尽管从锋利方面应考虑低进给槽形可选用的10°和15°的前角,但适中的斜角刃(5°)通常为最佳选择。在限制飞边形成方面,切削刃的锋利性起到了很重要的作用。
磨削的正前角切削刃可以最小化飞边,而带有大圆角刀尖的坚固槽形则容易形成飞边,尤其是采用较大的进给率时。在这方面,当采用同一刀具或精加工刀具切断之后的额外走刀可能是获得最佳生产效率的一种解决方案。
切断工序的其他影响因素优化装夹不仅可影响工序结果,而且也对可优化的程度产生影响。基本原则是最小化刀具悬伸以获得刚性,并确保切削刃尽可能靠近中心线。对于良好的切断方法来说,合适且充足的冷却液供应及其方向常常也至关重要。带集成式冷却液供应的刀块就是一种解决方案;此外冷却液从下面供应可以延长刀具寿命和改善切屑控制。切断棒料时,所切削的工件直径会不断变小,到达中心时接近于零。切削速度因此会显著降低,从而增大积屑瘤在切削刃上形成的趋势,进而对刀具寿命产生负面影响。提高主轴转速并在穿过之前将进给率降低几毫米能够弥补这种不利影响。
最基本的优化因素对于竞争激烈的切断应用来说,最佳化进给率几乎总是主要优先考虑的其中一个因素。进给在很大程度上决定生产效率的高低,也即执行工序所需时间的长短。(成功地实现每转0.15mm的进给,而不是0.10mm,并且刀具寿命更长和可预测,两者之间存在着巨大的差别。)进给也意味着可以在切削、停留或啄进期间通过改变进给来控制切屑形成。在降低切削速度时也可提高进给率以最小化振动趋势。进给率也应针对正确的刀具压力进行设置以确保直刀具路径,并在切断终了前有所降低以免强行切断,同时在间断切削时确保其安全性。最后得出结论,进给、刀片和刀柄的组合是切断时至关重要的最佳化因素。
声明:本网站所收集的部分公开资料来源于互联网,转载的目的在于传递更多信息及用于网络分享,并不代表本站赞同其观点和对其真实性负责,也不构成任何其他建议。本站部分作品是由网友自主投稿和发布、编辑整理上传,对此类作品本站仅提供交流平台,不为其版权负责。如果您发现网站上所用视频、图片、文字如涉及作品版权问题,请第一时间告知,我们将根据您提供的证明材料确认版权并按国家标准支付稿酬或立即删除内容,以保证您的权益!联系电话:010-58612588 或 Email:editor@mmsonline.com.cn。
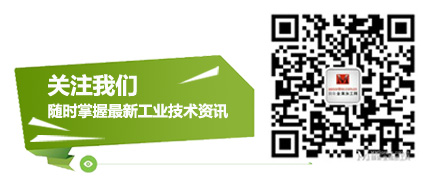
- 暂无反馈