叶轮在航空航天等领域的广泛应用
整体叶轮作为动力机械的关键部件,广泛应用于航空航天等领域。叶轮叶片的型面非常复杂,对发动机性能影响大,设计研制周期长,制造工作量大,其加工技术一直被视为制造业中的重要课题。传统加工工艺采取分体加工方案,即叶片与轮毂分别采用不同的毛坯,分别加工成形后将叶片焊接在轮毂上。该方案不仅费时费力,而且难以保证叶轮的各项性能指标。
随着高速铣削技术、多轴尤其是五轴数控机床及CAM技术的不断发展,应用五轴联动数控机床进行叶轮加工,既可以保证刀具的球头部分对工件进行准确的切削,又可以利用其转动轴工作以避免刀具的刀体或刀杆部分与工件其他部分发生干涉或过切,充分满足了叶轮零件生产的要求。
对于CAD/CAM处理后产生的叶轮加工程序,在叶轮正式加工之前,都必须经过刀具轨迹的干涉检验和程序试切。其目的就是为了检验和验证NC程序的正确性,因而产生了虚拟现实技术的仿真技术,它能够全面逼真地反映现实加工环境和加工的过程,如工件的装夹定位、机床调整、切削参数选取、加工结果和设计结果的比较等;同时,对加工过程中出现的碰撞、干涉等进行提前预警。因此合理地评价了现场工、夹、刀具等的实用性,并能对产品、工装等的可加工性和工艺规程的合理性进行评估,这也是工艺、编程人员所需要的。
叶轮加工工艺分析
叶轮结构可分为轮毂曲面以及叶片曲面2部分,叶片包含包覆曲面、压力曲面和吸力曲面,如图1所示。叶轮轮毂曲面由叶片中性面根部曲线和叶片中性面顶部曲线绕Z轴转而成;经过旋转轴Z的设计基准面为子午面;中性面是处于叶片压力面和吸力面中间位置的曲面。
整体叶轮的结构特点可以看出,加工整体叶轮时刀具轨迹规划的约束条件较多,相邻叶片空间较小,加工时极易产生碰撞干涉,自动生成无干涉刀位轨迹较困难。
整体叶轮的加工难度如下所述:
(1)叶轮加工流道变窄,叶片相对较长,刚度较低,属于薄壁类零件,在加工过程中极易变形。
(2)流道最窄处叶片深度超过刀具直径的9倍以上,相邻叶片空间极窄,在清角加工时刀具直径较小,刀具容易折断,切削深度的控制也是加工的关键技术。
(3)叶轮曲面为自由曲面(包含小叶片、窄流道),叶片扭曲比较严重,加工时极易产生干涉。
根据工艺分析结果及采用的五坐标精加工设备,本课题所选案例——叶轮的加工路线为:毛坯→车加工外子午曲面→五坐标精加工。对于叶片及圆角,采用五坐标设备一次加工完成,既保证了刀具轨迹切削的连续性,又保证了叶片、圆角的精度以及叶片和圆角之间的衔接,其中五坐标精加工工序细分为:荒加工流道→叶片荒加工→叶片半精加工→流道半精加工→叶片精加工→流道精加工。
声明:本网站所收集的部分公开资料来源于互联网,转载的目的在于传递更多信息及用于网络分享,并不代表本站赞同其观点和对其真实性负责,也不构成任何其他建议。本站部分作品是由网友自主投稿和发布、编辑整理上传,对此类作品本站仅提供交流平台,不为其版权负责。如果您发现网站上所用视频、图片、文字如涉及作品版权问题,请第一时间告知,我们将根据您提供的证明材料确认版权并按国家标准支付稿酬或立即删除内容,以保证您的权益!联系电话:010-58612588 或 Email:editor@mmsonline.com.cn。
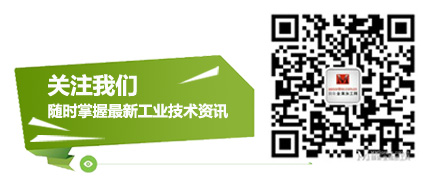
- 暂无反馈