高速加工在航空工业中的应用
高速加工的技术发展趋势是采用更快的切削速度、进给率和负荷更轻的切削,而传统加工通常采用负荷较重、切深较大的低速切削。
成功的高速加工需要重视刀具、主轴和机床动力学
工具技术和机床控制能力的进步使高速加工在航空零部件的制造中获得了越来越广泛的应用。尽管高速加工技术特别适合铝合金的加工,但在复合材料和硬金属材料的加工中也有其用武之地。
竞争压力正不断迫使制造商以更高效的方式加工零件。与此同时,航空结构件生产商也需要强度更高、质量更轻、公差要求更严的构件。采用高速加工技术可以使制造商缩短加工循环时间,同时还能加工出比以往更精巧、壁更薄的零件。
按照哈斯(Haas)公司加工经理Wayne Reilly的看法,许多人在使用高速加工这一术语时并不严谨。在Reilly看来,虽然一些人认为任何主轴转速超过10000rpm的加工就算高速加工,但另一些人对此却有更复杂一些的定义。他说,“实际上这取决于该术语的使用背景。工具制造商可能将其定义为转速,而机床制造商则可能将其定义为CNC数控系统中的某些前瞻处理程序块。高速加工的技术发展趋势是采用更快的切削速度、进给率和负荷更轻的切削,而传统加工通常采用负荷较重、切深较大的低速切削。”例如,哈斯公司生产的立式加工中心(VMC)为高速加工提供了高达30000rpm的额定主轴转速和30马力(22.4kW)的驱动系统额定功率。
辛辛那提(MAG Cincinnati)公司的铝件加工平台经理Randy Von Moll表示,“与其孤立地讨论主轴转速,我倒更喜欢高效加工这个术语。”他的定义除了主轴转速外,还包括机床的动态响应。他用了5个参数来定义高效加工:①主轴转速;②主轴功率;③高的进给率和刀路速率;④高的加、减速度;⑤高精度。后三个条件专门定义了机床的动态响应而不是主轴特性。Von Moll说,“为了更有效地切削合金材料(如铝合金),确实需要将高性能的主轴与机床的高动态响应结合起来。”
如果将航空零件分为“薄板件”和“厚板件”两大类,他认为可将高速加工分别定义为:对于厚度在50mm以内的薄板件,主轴转速为30000rpm,额定功率为80马力(60kW);对于厚度在50mm以上的厚板件,主轴转速为18000rpm,额定功率为135马力(100kW)。
Von Moll解释说,“在切削加工薄板件和厚板件时,机床的最高动态响应参数并无太大不同。对于两种工件,加速度/减速度都应在0.5g左右,应提供尽可能快的(非切削)往复运动,至少达到1500ipm(38m/min)。”
在加工复杂的凹腔类工件时,加速度/减速度对切削时间有很大影响,因为刀具在加工中必须多次改变方向。
机床的往复移动时间会影响切削时间,尤其是辅助时间(切削铝合金时辅助时间可占到全部加工循环时间的20%)。辅助时间包括切削一个新工件时刀具的定位时间或刀具移动到换刀机械手的时间。按照精益制造的观点,辅助时间是一种需要消除的浪费。几年前,辛辛那提公司推出了可实现快速往复移动与高加/减速度完美结合的HyperMach立式仿形铣床系列。这些机床的快速往复移动速度高达4000ipm(101m/min),其目的就是为了缩短辅助时间。HyperMach的X、Y、Z轴行程分别达到33m、3500mm和1250mm,并配置了附加的A、B或C轴,机床的主轴转速高达30000rpm。大部分HyperMach立式仿形铣床都是在一个共用的X轴龙门结构上安装两个相互独立的主轴。为了应对提高大型工件(尺寸可达2000mm×4000mm)加工效率的市场需求,辛辛那提公司将在IMTS 2008(2008年美国芝加哥国际制造技术展览会)上展出并演示HyperMach卧式系列。
“切削出小切屑并尽可能快速地加工”是牧野(Makino)公司设计工程师Alan Hollatz对高速加工的定义。他认为,高转速、小切深的加工方法可以减少传入工件或刀具中的切削热,工件和机床所受的切削力也较小。传统的低转速、大切深加工方法容易使现代设计中壁厚薄至0.030″(0.76mm)的工件产生变形。较小的切削力还意味着可以降低对工件夹持的要求。
Hollatz建议,在精加工铝合金时,应尽可能采用高速切削,“如果主轴额定转速为30000rpm,我们将尝试全速运行。同时,我们还会限制所用刀具的直径。考虑到刀具不平衡引起的离心力,机床转速越高时,刀具直径应越小。”作为一个实例,牧野生产的一种大型机床(主轴转速33000rpm,电机功率107马力[80kW])不推荐使用任何直径大于50mm的刀具。对于大多数切削加工而言,直径为25mm或更小的刀具切削效率最高。
与大多数机床供应商一样,Hollatz推荐在主轴转速较高时采用空心短锥柄(HSK刀柄),而不要采用CAT型刀柄。他指出,CAT刀柄在高速加工时可能会引起Z方向的精度问题。在以高转速进行加工时,曾经出现过CAT刀柄卡住主轴的极端情况。HSK刀柄的设计特点是采用锥面和端面双重接触,因此可以控制Z方向的精度。“当主轴转速在20000rpm以下时,可以采用CAT刀柄,但当转速高达30000rpm时,除了采用HSK刀柄以外别无选择。”
高速加工的另一个关键因素是CNC控制器及其在高速条件下精确控制机床运动的能力。具有“前瞻”功能的控制器可以根据刀具将要到达的位置控制刀具当前的速度和加/减速度,该功能与高速驱动主轴同样重要。
据Hollatz介绍,牧野机床控制器的标准“前瞻”功能有超过60-80个G码模块。其中的Super GI.4控制器程序包是为高速加工而专门设计的,有超过180-250个模块。对于相同的刀具路径,Super GI.4的运动速度比它所替代的SGI.3控制器提高了15%-30%。
据哈斯公司加工经理Reilly介绍,哈斯机床为高速加工控制提供了可选方案。哈斯的高速加工控制模块允许采用更高的进给率和更复杂的刀轨,而不会使机床出现停机等故障。哈斯机床采用称为“插补前加速度”的运动算法,并与多达80个模块的全“前瞻”功能相结合,其高速加工控制模块可提供高达500ipm(13m/min)的等高线进给运动,而无需冒编程的刀轨失真的风险。“这样做的最大好处就是执行程序时具有‘前瞻’性,而且当运动方向发生任何变化时都能保持尽可能快的运动速度。”Reilly解释说,“如果运动方向变化不大,运动速度也几乎不需要改变。速度的变化是与方向的变化成比例的。”
在航空工业中,随着新型飞机为减轻重量而采用更多复合材料,对复合材料的加工需求正变得日益迫切。波音787客机采用合成材料制造机身和机翼就是这一趋势的典型实例。铝合金的高速加工不久将成为标准工艺,将高速加工应用于其它常用航空材料似乎也具有意义,对于复合材料当然也不例外。“当采用近净成型工艺制造复合材料零件时,为了达到配合、连接和凹陷部位的精度要求,就需要进行机加工。”辛辛那提公司复合材料加工平台经理Jeff Crick解释说,“例如,利用层积加工可在机翼表面制造一个进入孔,但只能达到大约±0.5mm的精度(层积加工只能达到这种精度)。为了在要求的部位达到更高精度,就需要进行二次加工(如机加工),就像对铝合金、钛合金或钢材进行精加工一样。”
据Crick介绍,与加工铝合金相比,高速加工复合材料所需的功率和扭矩较小,机床本身无需像切削钛合金的机床那样厚重结实,但仍然需要有足够的刚性以克服振动和共振。大多数机床主轴的转速范围都在10-13000rpm(尽管它们可以更高速度运转)。例如,美国一家大型航空零部件制造商在一台转速为24000rpm的机床上,采用0.012-0.016″(0.3-0.4mm)的切深实现了对复合材料的高速加工。
现在,大部分复合材料都采用当初为金属切削而设计的加工单元来加工。Crick认为,最终的目标是制造出重量更轻、为加工复合材料而专门设计的专用机床。设计这种机床时必须注意一种趋势,即航空复合材料零部件的尺寸越来越大。Crick说,“复合材料零部件的尺寸可能非常大,如长达100′(30m)机翼外覆件,甚至包括整个机身部件,如新型波音787的机舱剖面直径超过20′(6m),长度超过30′(9m)。在这种大型结构中,对一节机身与另一节机身之间接合面的加工公差要求很严。其他零部件可能既长又带有筋板,如翼梁、纵梁、支柱和地板横梁等。
为了加工这些既长又薄且容易弯曲的零件(Crick形象化地将它们形容为“湿面条”),辛辛那提公司开发了一种专用挤压件铣床(图5)。该机床既可以加工铝合金也可以加工复合材料,加工尺寸范围13′×8′(4×2.4m),主轴转速24000rpm,采用直径不超过25mm的12种刀具进行加工,工件可长达40′(12m)。
“当几乎所有加工方式和工件材料都可通过高速加工获益时,自由切削材料(如铝合金或复合材料)受益最大,”哈斯公司加工经理Reilly说,“由于采用高转速、大进给、小切深的硬铣削技术,淬硬模具钢也可从高速加工中获益。钛合金作为航空工业越来越重要的工件材料,当然也是受益者之一。”
“如果说铝合金切削机床像F1赛车,钛合金切削机床就更像推土机,”MAG维修技术公司的生产力解决方案经理Dan Cooper说,“它们在主轴转速方面有很大不同,尽管高速加工原理——高转速、小切深对于钛合金有时也具有意义,尤其是薄壁零件最好采用高速加工原理加工。举例来说,一个用户的零件厚度为0.030″(0.76mm)、高度为3″(76mm),这种大高度薄壁件不能采用老式传统工艺进行粗加工,低转速、大切深、大扭矩切削将导致工件变形和刀具偏移,对于新型5553钛合金零件的加工尤其如此。”
Cooper指出,钛合金的低导热性、高弹性模量与高强度相结合,使其成为一种难切削材料,“虽然切削扭矩和动态刚性对于复合材料和铝合金加工也许并不太重要,但对于钛合金加工却非常重要。与铝合金加工相比,这会限制钛合金加工速度的提高。”
Cooper宁愿用表面速度和进给率而不是主轴转速来衡量高速加工。表面速度是主轴转速和刀具直径的函数;进给率是主轴转速和刀齿密度的函数。由于刀齿越密、表面速度(SFM)越高,就意味着进给率越高,因此刀具的设计至关重要。
Cooper介绍说,MAG的新型硬质合金刀具可以390fpm的表面速度进行加工。“用一把直径25.4mm、刀槽数最多的刀具,我们只能以1500rpm的转速和2.5m/min的速度加工,而这对于钛合金加工已是相当高的速度了。”
高速加工技术已在铝合金加工中证明了自己的优势,人们期望它在加工像钛合金一样更新、更硬的材料时也能做到这一点。
“如今,铝合金的高速加工正在成为标准工艺。”马扎克(Mazak)公司西区总部和航空技术中心的加工经理Rudy Canchola说。对他来说,目前最大的加工挑战是高温合金(如15-5不锈钢、5553或6Al4V钛合金),这些材料在航空工业的使用越来越多。最近,他计划在马扎克机床上采用各种刀具进行切削试验(包括在Mazak VCN-510C立式加工中心上进行钛合金加工试验)。Canchola说,“我们已经证明用整体硬质合金立铣刀加工钛合金的速度可达500-600fpm。我们认为这是非常不错的。”
他们还分别用山高(Seco)、英格索尔(Ingersoll)、肯纳(Kennameta)和山特维克(Sandvik)的刀具在Mazak Vortex 815-II五轴加工中心上进行了加工15-5不锈钢的切削试验。试验采用顺铣加工方式,表面切削速度达到400-600fpm。
Canchola说,“我们的大多数机床都具有实现这种高表面进给率的能力。如果用户需要切削这种材料,我们可以向他们提供在这些试验中获得的数据”。
加工高温合金时,机床控制器的“前瞻”功能不象加工铝合金时那么重要,因为此时的切削速度并不太高。最重要的控制功能是测量主轴和轴系所承受的载荷并据此进行调整。马扎克机床能够接收来自伺服电机的反馈电信号,并调整速度使其与切削条件相互匹配,如有必要还可以停机更换刀具。
声明:本网站所收集的部分公开资料来源于互联网,转载的目的在于传递更多信息及用于网络分享,并不代表本站赞同其观点和对其真实性负责,也不构成任何其他建议。本站部分作品是由网友自主投稿和发布、编辑整理上传,对此类作品本站仅提供交流平台,不为其版权负责。如果您发现网站上所用视频、图片、文字如涉及作品版权问题,请第一时间告知,我们将根据您提供的证明材料确认版权并按国家标准支付稿酬或立即删除内容,以保证您的权益!联系电话:010-58612588 或 Email:editor@mmsonline.com.cn。
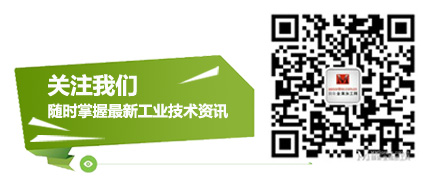
- 暂无反馈