焕发刀具潜能的金刚石涂层
通过化学气相沉积(CVD)工艺在钨硬质合金刀具上涂覆金刚石涂层,可以产生无与伦比的优势。
化学气相沉积金刚石保留了天然金刚石的属性。其超高硬度和弹性模量保障了非常高的尺寸稳定性及耐磨性。和天然金刚石一样,化学气相沉积金刚石的摩擦系数很低,因此切削力和功耗很低,摩擦发热很低,切割时可以防止积屑瘤的形成。
这些防腐涂层在用于切割腐蚀性聚合物诸如用于复合材料的酚醛树脂等时具有很长的使用寿命,同时,它们还可以防止切削液产生的腐蚀性损坏。
金刚石涂层刀具擅长于加工研磨性非金属材料、有色金属及研磨性有色金属等。但是,金刚石与含有铁、镍或钴等的金属合金产生化学非稳定性限制了这种涂层刀具在有色金属合金及超耐热合金切削中的使用。
晶体化学气相沉积金刚石
有很多涂层被称作金刚石,但是化学气相沉积金刚石是唯一采用100%真正金刚石晶体的涂层。
金刚石由纯碳原子组成,以一种特有的晶体方位排列,从而拥有独特的物理性能。在9,000~10,000维氏硬度上,晶体金刚石的硬度几乎为非晶体、类金刚石涂层(DLC)的两倍。
非晶体金刚石,或者称类金刚石涂层,是用物理气相沉积(PVD)工艺涂覆的碳薄膜。这些薄膜比化学气相沉积工艺涂覆的金刚石薄膜薄。
它们没有晶体结构,寿命一般为化学气相沉积金刚石涂层刀具的10-15%。
与刀具上涂覆金属烧结多晶金刚石(PCD)形成金刚石刀尖不同,化学气相沉积晶体金刚石涂层可以使整个刀具表面(包括带有复杂几何结构的刀具在内)受到超硬材料的保护。能够涂覆此类独特几何结构使化学气相沉积金刚石涂层刀具具备比多晶体金刚石刀具更显著的优势,制作后者的磨削成本非常高。
带有金属-氮化物的物理气相沉积涂层,诸如氮铝化钛(TiAlN),其微观硬度只有晶体金刚石的1/3。
化学气相沉积金刚石涂层钻头与刀尖多晶金刚石钻头相比所具备的优点在碳纤维钻削应用中得到了充分展现,并将单孔成本降低了70%以上。化学气相沉积的多层金刚石钻头在出现毛刺和分层现象之前可以在复合材料中加工300个通孔,而PCD刀尖钻头却只能加工150个通孔。
晶体金刚石是在热丝化学气相沉积过程中形成的,这种过程的时间为20-40小时。该过程中所采用的温度1,500°F (815.5℃)可以防止除整体硬质合金以外的东西被涂敷,精确的预处理过程需要采用6%等级的硬质合金来实现最佳粘附。
不经过预处理,金刚石与渗碳硬质合金之间几乎没有任何化学键。但是,金刚石可以嵌入粗糙地硬质合金表面,并通过硬质合金和金刚石的机械互锁作用而粘附到表面上。
含钴10%的刀具可以进行涂层处理,但是为实现良好粘附而需要额外处理使涂敷过程花费昂贵。在各大公司努力提高沉积率并开发新的预处理方式的同时,涂层技术本身也取得了重大进步。
多层金刚石
金刚石刀具涂层LLC公司的总裁Roger Bollier说:“起初,在刀具上只能形成单层多晶金刚石。”
Bollier说:“但是最近所取得的技术进步使得可以形成纳米级晶体金刚石。纳米级晶体结构可以产生非常光滑的表面并保持尖锐的刀刃,可以大大减少在加工碳纤维复合材料时的分层现象。”
他补充说:“将多晶和纳米级晶体金刚石结合成互锁层可以形成最好的金刚石涂层,而多层金刚石涂层已经成为所有有色金属材料涂层的一种选择。”
纳米级晶体金刚石的多层提高了涂层的断裂韧性。此外,亚微米晶体的微晶粒结构可以在切削刃上形成光滑的表面,用于加工出精细的表面光洁度,这样在加工粘性有色金属时,可以降低积屑瘤的形成。这些涂层还可以在干式或用最少润滑加工铝合金时延长刀具寿命。
所有涂层的一种共同故障是裂纹。那种高而独立的多晶金刚石结构趋向于沿直接进入基体的断裂线产生裂纹。一旦涂层出现这种问题,整个涂层就都会剥落。
但是,纳米级晶体金刚石却以与基体呈45度角的方式产生裂纹。交错的多晶和纳米金刚石晶体层不断改变在加工过程中形成的裂纹其方向,从而将金刚石涂层的寿命提高40%。
图示Sunnen Products Co.公司出品的单冲程珩磨辊是通过一种镀镍工艺在刀具基体上以机械方式粘附金刚石磨料而制作形成的。
金刚石涂层刀具寿命
金刚石涂层刀具的寿命与被切割材料、切割速度、进给速度以及零件几何结构等有关。
一般地,石墨金刚石涂层刀具比不带涂层的钨硬质合金刀具的寿命长10-20倍。因此,利用它们,可以进行无人看管加工,用一把刀具可以完全加工多个工件。大大减少磨损及刀具的重新校正。
在复合材料应用中,获得较长寿命并非罕见。对于高密度纤维玻璃、碳纤维及G10-FR4,有报道称,金刚石涂层刀具的寿命为不带涂层的钨硬质合金刀具寿命的70倍。
由于对刀具涂覆金刚石需要很长时间,因此为实现具有良好粘附力的金刚石涂层刀具所需进行的预处理过程成本高昂。
尽管金刚石涂层刀具成本为高质量硬质合金刀具的5倍左右,但是它们却大大降低了整体生产成本,因为它们具有广泛的操作范围和很长的使用寿命。例如,有一家汽车制造厂在加工高密度纤维玻璃时,通过用可以加工750个零件、价值150美元的金刚石涂层立铣刀代替可以加工15个零件价值15美元的立铣刀,生产率大大提高。这种做法为公司每年节省了60多万美元。
随着航空业制造商越来越多地使用复合材料,工程师们意识到,将金刚石涂层与适应特定应用场合的刀具几何结构进行适当组合可以提供最有效的加工解决方案。
复合材料,诸如高密度纤维玻璃、碳纤维及G10-FR4等很容易磨损。若对刀具不进行适当预处理,那么这些材料的磨损有可能降低金刚石薄膜在硬质合金上的粘附性。
在一个航空应用中,国防制造和加工中心(NCDMM)及金刚石刀具涂层LLC公司为加工西考斯基(Sikorsky)黑鹰直升机中的驱动轴(由一个内部钛衬体、一个IM7碳纤维管和一个外部钛端接头组成的)提供了一个“单刀”解决方案。这种金刚石涂层刀具可以加工出高质量孔,加工成本只有PCD刀具的几分之一。
在另一个应用中,NCDMM和金刚石刀具涂层公司开发了一种用于加工(洛克希德-马丁导弹和火力控制公司的)高精度瞄准系统的金刚石刀具。由于在研磨性应用中,刀具磨损非常严重,因此洛克希德此前很难实现很高的精度。在其他涂层发生剥落的应用场合,化学气相沉积金刚石涂层却大大提高刀具寿命和零件加工质量。
如何形成金刚石涂层
金刚石涂层是在真空室中采用氢气和甲烷形成的。通常,这些气体是以50:1的比例加到真空室中,以氢气为主。真空室内的高温元素会引起沉积过程的发生。例如, sp3 Inc.采用加热到大约2,200℃的细丝来将甲烷离解为碳和氢。然后,碳原子形成晶核,并生长成微细的金刚石晶体,随着时间的推移,这些微细晶体会形成连续的金刚石薄膜。金刚石缓慢生长,每小时大约0.5~1.0微米。
在刀片上培养40微米的薄膜几乎需要两天的时间,大部分圆刀需要一个晚上的时间进行涂敷。
声明:本网站所收集的部分公开资料来源于互联网,转载的目的在于传递更多信息及用于网络分享,并不代表本站赞同其观点和对其真实性负责,也不构成任何其他建议。本站部分作品是由网友自主投稿和发布、编辑整理上传,对此类作品本站仅提供交流平台,不为其版权负责。如果您发现网站上所用视频、图片、文字如涉及作品版权问题,请第一时间告知,我们将根据您提供的证明材料确认版权并按国家标准支付稿酬或立即删除内容,以保证您的权益!联系电话:010-58612588 或 Email:editor@mmsonline.com.cn。
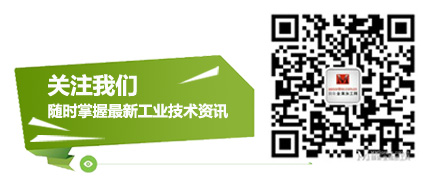
- 暂无反馈