技术讲堂 | 浅谈加工中常见刀具失效及应对方式(内含一对一答疑惊喜)
加工中基本刀具失效概述
这是一个关于在切削工具上最常见的单一刀具失效的概述。这些包括:
1. 后刀面和月牙洼磨损2. 积屑瘤3. 微崩4. 热机械失效5. 塑性变形6. 沟槽磨损7. 切屑锤击8. 刃口破损
对于这些刀具失效磨损,我们提供了一些可能的对策,以避免或至少最小化它们对加工过程的影响。
后刀面磨损分析
在切削中,后刀面磨损是最理想的刀具磨损状态。因为它是最容易判断和预测的刀具失效类型。后刀面磨损一般很均匀,它随着加工材料磨损切削刃而逐渐显现出来,类似于刀刃变钝。
后刀面磨损什么时候发生?
在加工过程中,后刀面磨损的发生有以下特点:
在较低的切削速度下,后刀面磨损主要是由磨料磨损和侵蚀磨损引起的。工件材料中的硬质微小夹杂物,会刮擦刀具表面。随后,刀具涂层的碎片可能会脱落,进一步刮伤刀具刃口。钴等其他元素最终会从刀具基体中磨损掉,这会降低硬质合金颗粒的粘附力,导致它们也容易脱落。
而在较高的切削速度下,扩散磨损成为后刀面磨损的主要原因,因为高速切削会在刀具边缘产生切削热,为扩散现象提供了有利条件。
后刀面磨损通常表现为沿着刀具切削边缘的均匀磨损。有时,工件材料可能会在切削边缘上形成涂抹,这可能会夸大磨损疤痕的视觉尺寸。
在切削耐磨材料,比如球墨铸铁、硅铝合金、高温合金、热处理后的沉淀硬化 (PH) 不锈钢、铍铜合金及钨硬质合金,以及在切削非金属材料,例如玻璃纤维、环氧树脂、强化塑料和陶瓷时,常会出现快速磨损。
后刀面磨损在加工各种工件材料时普遍存在,如果切削刃口不是由于其他类型的磨损而先失效,那么通常会因为后刀面磨损而达到使用寿命。
后刀面磨损应对方式
为了最小化后刀面磨损,可以采取以下一些纠正措施:
1. 降低切削速度:在某些情况下,降低切削速度可以减少刀具磨损,但这不符合生产需要,因为这会对加工周期带来不利影响;
2. 选择更耐磨的涂层硬质合金刀片;
3. 正确应用冷却液:恰当使用冷却液可以降低切削温度,减少刀具磨损,并延长刀具寿命。
月牙洼磨损分析
月牙洼磨损是由扩散和分解(高速切削时)以及磨料磨损(低速切削时)共同作用的结果。工件切屑产生的热量会使刀具基体中的钨钴碳化物颗粒分解,并且碳会通过扩散作用进入切屑中。这导致在刀片的前刀面上形成“凹坑”。随着凹坑的不断扩大,最终可能会导致刀片副刃的崩裂或者加速副刃磨损。
月牙洼磨损在前刀面上表现为凹坑或点状磨损的形状。在加工磨蚀性较强的工件材料时,如铸铁或表面硬度较高的工件(例如锻造工件),月牙洼磨损尤为明显。
月牙洼磨损应对方式
为了最小化月牙洼磨损,可以采取以下措施:
1. 使用含有厚层氧化铝的涂层:这些涂层可以提供额外的保护,减少刀具与工件材料之间的直接接触,从而减少由于高温和化学反应引起的磨损;
2. 恰当使用冷却液可以降低切削温度;
3. 降低切削速度和进给量:在低速和低进给量的条件下切削可以减少刀具上的热量和压力,从而降低月牙洼磨损的速度,但这不符合生产需要,因为这会对加工周期带来不利影响。
积屑瘤分析
积屑瘤(BUE)是由于工件材料在高压和足够高的温度下与切削刃发生粘附而形成的。这种粘附通常发生在切削区存在化学亲和力、高压力和足够温度的情况下。
积屑瘤的形成会导致工件材料在刀具前刀面和切削刃附近堆积,形成硬化堆积物。最终,积屑瘤会断裂并带走一部分切削刃,导致刀具发生崩裂和快速副刃磨损。
积屑瘤什么时候发生?
积屑瘤通常在以下情况下发生:
- 当加工的材料具有较强的粘附性,如非铁金属材料、超级合金和不锈钢时。
- 在切削速度和进给量较慢的操作中。
积屑瘤表现为在刀具切削刃顶部或副刃上看起来像闪亮的材料部分。它们会导致刀具前刀面上出现小坑或凹坑,并最终导致切削刃的崩裂。
积屑瘤的改善
1. 增加切削速度和/或进给率:这有助于减少材料在刀具前刀面上的粘附时间,从而减少积屑瘤的形成。
2. 选择具有更尖锐槽型和更光滑前刀面的刀片:这有助于减少材料粘附的可能性,并提高切削效率。
3. 正确应用冷却液,并增加冷却液的浓度:冷却液可以降低切削区的温度,减少材料的粘附,从而防止积屑瘤的形成。
微崩分析
崩刃是由切削材料中的机械不稳定或裂纹引起的。切削刃的崩刃通常是由于工件、机床或刀具本身的振动造成的。工件材料表面硬质夹杂物和中断切削会导致局部应力集中,从而引起裂纹和崩刃。
崩刃表现为切削刃上小块材料的断裂,常见于非刚性情况下。含有硬质颗粒的工件材料(例如沉淀硬化工件材料)也会导致切削刃崩刃。
微崩的改善
为了最小化崩刃磨损,可以采取以下纠正措施:
1. 正确的机床设置:确保机床稳定,减少振动。
2. 减少弯曲变形:减少机床和刀具系统的弯曲,以提高刚性。
3. 使用更坚韧材质和更强壮的槽型:选择具有更好抗冲击性能的刀具。
4. 减少进给量(特别是在进刀与出刀的地方)并增加切削速度。(也参见防止积屑瘤的纠正措施。)
热机械失效分析
热裂纹是由以下因素共同作用引起的:
热载荷(切削区域的高温)
热变化或梯度(切削边缘温度的变化)
应力裂纹大致垂直于切削边缘发展,最终导致硬质合金部分脱落,边缘崩裂。热裂纹主要在铣削和断续切削的旋转加工中观察到。间歇性冷却液的流动可能导致热裂纹。
热机械失效的改善
- 正确应用冷却液:冷却液可以帮助降低切削区域的温度,减少热裂纹的形成。
- 选择更坚韧的材质:使用具有更好热稳定性的刀具材质。
- 降低切削速度和进给量:这有助于减少切削区域产生的热量。
- 使用降低热量产生的槽型。
- 考虑不同的加工方法(切削时间与非切削时间的比例):调整加工策略,以减少刀具在高温下的持续时间。
塑性变形失效分析
热过载是导致塑性变形的主要原因。过度的热量会使碳化物粘结剂(钴)软化。然后,由于机械过载,切削边缘的压力使其在尖端处变形或下垂,最终可能导致崩裂或导致快速后刀面磨损。
塑性变形看起来像一个变形的切削边缘。需要仔细观察,因为塑性变形在切削边缘上可能与后刀面磨损非常相似。
塑性变形失效的改善
在切削温度高(高速度和高进给量)和工件材料本身强度高(硬质钢或经过应变硬化的表面和超级合金)的情况下,可以预期会出现塑性变形。
- 正确应用冷却液
- 降低切削速度和进给量
- 使用具有更大圆角半径的刀片
- 选择更硬、更耐磨的材质
通过采取这些措施,可以有效地减少塑性变形,提高刀具的耐用度和加工效率。
沟槽磨损失效分析
当工件的表面比其底层材料更硬或更磨蚀时,就会发生沟槽磨损。这可能是由于之前的切削过程中表面硬化(如不锈钢和超级合金等应变硬化材料)所致,或者起源于锻造或铸造表面上的表面鳞片。所有这些情况都会导致在切削刃与硬层接触的地方刀具磨损速度加快。这种局部集中的应力也可能导致沟槽磨损。
在与工件材料接触的切削边缘上,会产生压应力,而在切削边缘不接触的地方则不会。这会在直接接触的两个点(切削深度线)上对切削边缘产生高应力。任何形式的冲击,如工件材料中的硬质微夹杂物或轻微的中断,也可能导致沟槽磨损。
沟槽磨损失效的改善
一些纠正措施包括:
- 在使用多次切削时,减少进给率并改变切削深度
- 如果加工高温合金,增加切削速度(这将导致更多的后刀面磨损)
- 选择更坚韧的刀片材质
- 对于高进给量,使用断屑的槽型,以防止积屑瘤的形成,特别是在不锈钢和耐热合金中
切屑锤击分析
切屑锤击是一种现象,由切削刃上未切削部分的切屑回卷并撞击所致。结果是未切削的切削刃(或切削刃的一部分)发生断裂。这种风险在涉及高进给量和大切深组合的操作中更大。
切屑锤击失效的改善
为纠正切屑锤击现象,可以采取以下措施:
- 改变进给率和切削深度
- 选择不同的切削刃角度
- 使用不同的断屑槽型
- 选择更坚韧的刀片材质
刃口破损分析
任何关于基本刀具失效模式的概述也必须包括切削刃口断裂,切削刃的灾难性断裂不是一种刀具失效模式,而是一种由于使用工具不当而引起的不受欢迎且危险的现象。当切削刃断裂时,这意味着选择的切削条件使得作用在切削刃上的机械载荷如此之大,以至于刀具无法承受。
刃口破损改善
从较低的切削条件值(主要是切削深度和进给量)开始,或者选择一个更强的切削刃(更坚韧材质或更强壮的槽型)。
还可能是前面提到的某一失效模式扩大并严重削弱了切削刃,以至于它再也无法承受作用在它上的载荷。在这些情况下,尽早更换新的切削刃可以防止断裂。
刀具失效的判断
失效描述主要集中在刀具失效的视觉方面。除此之外,当刀具磨损时,还可以观察到其他现象,这些现象表明刀具正在磨损,可能需要更换。
刃口的突然断裂。这是非常不愉快的方式,表明刀具需要更换。由于影响刀具边缘恶化的因素众多,不可能全部考虑在内,有时可能会导致刀具边缘在某些情况下断裂。
如果刃口破损以系统性的方式发生,则需要停止操作并进行全面评估。系统性的刀具断裂表明,作用在刀具边缘上的载荷与刀具的承载能力之间存在不平衡。应该降低切削力或选择更强的刃口。
触摸测试是评估刀具刃口状态的最简单测试之一。积屑瘤或刀具边缘的微小崩裂可能肉眼看不见,但用手指可以感觉到。积屑瘤和崩裂应在操作过程中尽量减少。
加工过程中的噪音水平变化可以表明刀具正在磨损。尖锐的高频噪音表明切削条件不佳。
在加工过程中形状、形状或颜色变化的切屑是刀具边缘形状变化的另一个迹象。
当加工表面的粗糙度降低时,也可能表明是刀片转位或者更换刀片的时候了。
功率消耗的增加或振动倾向的增强。
快来判断一下
这是什么类型的失效吧~
如果太难不会也没有关系!
欢迎发图片给小编
小编帮您
把难题丢给山高的技术大哥
视频解答您的刀片失效类型
(仅限前3名幸运观众)
(山高刀具)
声明:本网站所收集的部分公开资料来源于互联网,转载的目的在于传递更多信息及用于网络分享,并不代表本站赞同其观点和对其真实性负责,也不构成任何其他建议。本站部分作品是由网友自主投稿和发布、编辑整理上传,对此类作品本站仅提供交流平台,不为其版权负责。如果您发现网站上所用视频、图片、文字如涉及作品版权问题,请第一时间告知,我们将根据您提供的证明材料确认版权并按国家标准支付稿酬或立即删除内容,以保证您的权益!联系电话:010-58612588 或 Email:editor@mmsonline.com.cn。
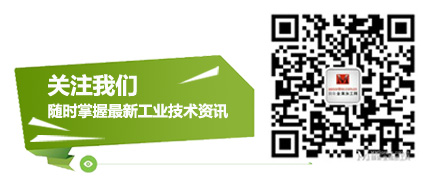
- 暂无反馈