电池深度探索,蔡司新能源汽车电池方案技术手册发布
随着新能源汽车的市场规模不断扩大,电池制造商如果希望在强手林立的市场中拔得头筹,就不能在质量上走捷径。电池的质量保证过程是复杂且多方面的,从材料研发、原材料加工、电芯生产到电池模组装配,品控伴随着生产的每一步。
该技术手册介绍了新能源汽车电池的六个主要质量检验关口,以及应对每个关口质量挑战时的解决方案。蔡司工业显微镜及CT系统的完备产品组合赋能了电池的研发及质量控制,满足其各环节中所需的所有成像及计量需求:
内容简介
电池深度探索
蔡司新能源汽车解决方案
总
质量检验关1:/ 材料研发
阴极、阳极和隔膜材料研发
客户面临的挑战
电芯材料的微观结构,如颗粒的大小、形状和化学成分以及杂质的存在,将决定电池的性能
需要各种分析解决方案来了解材料和电池性能之间的关系
聚合物材料,如粘合剂、导电剂和隔膜,需要不喷金、低电压、高分辨率和高对比度的电镜成像
质量检验关2:/ 结构研究
用于功能性研究的预组装测试
客户面临的挑战
在制备用于分析的样品时,已经充电和老化的锂离子电池必须避免暴露在空气
大面积横截面成像对于可视化电池的内部电极结构,以及材料的形状、孔隙和裂纹等细节非常重要
需要在不拆解电池的情况下无损3D高分辨率成像分析电池结构的原始状态
质量检验关3:/ 原材料加工
来料检测
客户面临的挑战
原材料颗粒,如阴极和阳极颗粒,其孔隙、裂缝和损坏,会降低电芯的性能和效率
为了分析电池故障的可能性并能够更好地控制生产工艺,可视化原材料的微观结构是必要的
检查阴极颗粒的化学元素比例和阳极粒子的纯度是生产高质量电芯的另一个重要步骤
质量检验关4:/ 电极生产
清洁度 – 防止颗粒污染
客户面临的挑战
金属异物可导致锂枝晶生长、短路或热失控,对锂离子电池构成重大安全问题
电池活性材料在运输和生产工艺中很容易被污染
为了防止任何质量问题,需要严格控制粒径大小超过 5 μm 的异物
质量检验关4:/ 电极生产
毛刺检查 – 监测电极毛刺
客户面临的挑战
铜和铝集流体上的金属毛刺的主要来源是由于刀片的切割
决定何时更换刀片涉及到质量和成本之间的权衡
质量检验关5:/ 电芯生产
客户面临的挑战
需要检查电芯的内部缺陷(金属异物、极片翻折和极耳焊接等),以避免后续浪费和安全隐患
必须准确、清晰、快速地识别电芯的内部问题
对于组装好的电芯,需要无损测量其极片的排列和位置的尺寸,特别是对齐度
质量检验关6:/ 模组装配
客户面临的挑战
无损CT检查是新能源汽车电池模组装配的必要步骤
任何与安全问题有关的模组内部缺陷都应在QC和QA过程中发现
CT扫描必须能够分析到几微米的小金属颗粒,以及几微米级的缺陷来确保装配质量和进行失效分析
点击下方按钮填写表单,即可获取蔡司新能源汽车电池方案技术手册。
(蔡司工业质量 )
声明:本网站所收集的部分公开资料来源于互联网,转载的目的在于传递更多信息及用于网络分享,并不代表本站赞同其观点和对其真实性负责,也不构成任何其他建议。本站部分作品是由网友自主投稿和发布、编辑整理上传,对此类作品本站仅提供交流平台,不为其版权负责。如果您发现网站上所用视频、图片、文字如涉及作品版权问题,请第一时间告知,我们将根据您提供的证明材料确认版权并按国家标准支付稿酬或立即删除内容,以保证您的权益!联系电话:010-58612588 或 Email:editor@mmsonline.com.cn。
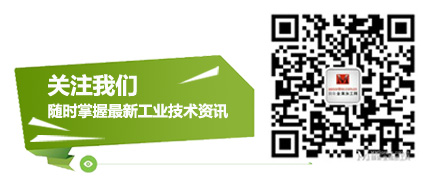
- 暂无反馈