【技术浅析】华中数控铣床对刀方法探讨
数控铣床在加工之前必须进行对刀,否则数控系统无法识别编程人员设定的工件坐标系,也就无法进行正常加工。对于同一个零件的加工,不同的编程人员设定的工件坐标系原点可能不同,因此对刀时的步骤和设定方法也不同。本文以华中数控 HNC-210B 为例,说明数控铣床对刀的不同方法和步骤。
1、对刀的不同指令
对刀任务为设定如图 1 所示的工件上表面中心点作为工件坐标系原点(编程原点)。
1.1 使用坐标系设定指令 G92 对刀
1.1.1 格式
格式为:G92 X_Y_Z_。其中,X、Y、Z 为刀具刀位点相对于工件坐标系原点的坐标。
图 1 工件坐标系原点图
1.1.2 操作方法
使用手轮方式使刀具与工件左侧接触(看到有少量切屑即可,也可以使用寻边器),记下此时的机床实际 X 坐标;再使刀具与工件右侧接触,同样记下此时的机床实际 X 坐标;算出两个 X 坐标的平均值,即为工件上表面中心点的X 坐标。同理,使刀具接触工件的前侧和后侧,可以算出工件上表面中心点的 Y 坐标。再使刀具与工件上表面接触(也可以采用 Z 轴对刀器),记下此时的机床实际 Z 坐标,即为工件上表面中心点的 Z 坐标,最后移动刀具使其机床实际坐标到达前面算出的 X、Y、Z 坐标,也就是刀具位于了工件坐标系原点,因此刀具的刀位点相当于工件坐标系原点的坐标是(0,0,0),则程序中的指令为:G92 X0 Y0 Z0。
但是加工之前,刀具与工件之间不能接触,要有一定距离,比如刀具在工件坐标系原点正上方 100mm,则刀具移动的 Z 坐标要在原来的基础上加上 100mm,故刀具的刀位点相当于工件坐标系原点的坐标是(0,0,100),则程序中的指令为:G92 X0 Y0 Z100。要注意的是,在加工之前刀具不能再移动,否则建立的工件坐标系会被破坏,无法进行正常加工,这对于操作人员将十分不方便,并且还需要操作人员自己算出平均值,比较麻烦,因此一般情况下不会采用 G92 指令设定工件坐标系。操作步骤示意如图 2 所示。
1.2 使用工件坐标系选择指令 G54 ~ G59 对刀
1.2.1 格式
格式为:G54/G55/G56/G57/G58/G59。
1.2.2 操作方法
按操作面板上“设置”→“坐标系”对应功能键,进入如图 3 所示的坐标系界面,通过光标键及翻页键在G54 ~ G59 中选择,以选择 G54 为例。使用手轮方式使刀具与工件左侧接触,将光标移动到 G54 的 X 位置,如图 3所示,按下界面最后一行的“记录Ⅰ”,再使刀具与工件右侧接触,按下界面最后一行的“记录Ⅱ”,再按下界面最后一行的“分中”,则确定了 G54 的 X 坐标,将光标移动到 G54 的 Y 位置,同理可以确定 G54 的 Y 坐标。最后使刀具与工件上表面接触,按下界面最后一行的“当前位置”,注意在确定 Z 坐标前要将光标移动到 G54 的 Z 位置。程序中的指令中加入 G54,数控系统会自动调用 G54 存入的 X、Y、Z 值。由于 G54 ~ G59 对刀操作简单,不需要操作人员计算平均值,并且加工之前刀具可以任意移动,因此通常情况下都采用 G54 ~ G59 方式对刀。
图 2 刀具操作步骤示意图
图 3 坐标系界面
2、同一工件不同工件坐标系的对刀
上述对刀任务选择的是工件上表面中心作为工件坐标系原点,而不同的编程人员选择的工件坐标系原点可能不同,还可以选择上表面的 4 个角点作为工件坐标系原点。
2.1 以工件上表面的左上角作为工件坐标系原点
如图 4,使刀具接触工件的左侧和前侧,由于刀具中心与工件坐标系原点相差一个刀具半径值,因此需要偏置。由图可知,工件坐标系原点处于左侧刀具的右边(+X 方向),故 G54 的 X 坐标应该加上刀具半径值,工件坐标系原点处于前侧刀具的后边(-Y 方向),故 G54 的 Y 坐标应该减去刀具半径值。加上或减去刀具半径值可以通过图 3 中最后一行的“正向偏置”“负向偏置”来进行。如要加上半径值,按“正向偏置”,输入半径值后回车即可;如要减去半径值,按“负向偏置”,输入半径值后回车即可。
2.2 以工件上表面的右上角作为工件坐标系原点
同理,如图 5,G54 的 X 坐标应减去刀具半径值,G54的 Y 坐标应减去刀具半径值。
2.3 以工件上表面的右下角作为工件坐标系原点
同理,如图 6,G54 的 X 坐标应减去刀具半径值,G54的 Y 坐标应加上刀具半径值。
2.4 以工件上表面的左下角作为工件坐标系原点
同理,如图 7,G54 的 X 坐标应加上刀具半径值,G54的 Y 坐标应加上刀具半径值。
图 4 刀具中心与工件坐标系原点偏置 1
图 5 刀具中心与工件坐标系原点偏置 2
图 6 刀具中心与工件坐标系原点偏置 3
图 7 刀具中心与工件坐标系原点偏置 4
3、多把刀具的 Z 向对刀
数控铣床加工中,经常会使用多把不同的刀具加工同一个零件,理论上每一把刀具都需要对刀。对于加工同一个零件,每一把刀装夹到主轴上时,刀具的轴心线都是同轴的,因此只需要对标准刀进行 X 向和 Y 向对刀,其他刀具不需要对 X 向和 Y 向,使用和标准刀相同的对刀值即可。每一把刀装夹到主轴上的长度不同,因此每一把刀的 Z 向必须对刀。如果把每一把刀所对的 Z 值都记下来,然后在使用每一把刀之前将 G54 的 Z 值进行修改,则非常麻烦,并且耽误时间,效率低。为了提高效率,可以采用刀具长度补偿的方法进行 Z 向对刀。
3.1 每一把刀都进行长度补偿的 Z 向对刀(绝对坐标)
将 G54 的 Z 值输入零,按“刀补”中的“刀补表”键,进入如图 8 所示的界面,然后将每一把刀所对的 Z 值输入到长度补偿里。
图 8 补刀表界面
3.2 设置标准刀进行长度补偿的 Z 向对刀(相对坐标)
将 G54 的 Z 值输入一号刀(标准刀)对应的 Z 值,按“刀补”中的“刀补表”键,进入如图 8 所示的界面,一号刀的长度补偿值输入零,其他刀的长度补偿值输入其与一号刀的长度差值。长度差值确定方法:一号刀与工件上表面接触,按“设置”中的“相对清零”键,进入如图 9 所示的界面,按“Z 轴清零”,再换成其他刀具,同样使刀具与工件上表面接触,屏幕上显示的 Z 轴相对实际坐标即为长度差值。
4、刀具折断后的对刀
数控铣削加工中会出现刀具折断的情况,特别是精加工时采用直径很小的刀具时,如果切削参数设置不合理,很容易断刀。断刀后,对刀的表面已经被切掉,因此可以利用 Z 轴对刀器对新刀具进行 Z 向对刀(X 向和 Y 向不需要对刀),如图 10 所示。
4.1 绝对坐标方式
将 Z 轴对刀器平放在工件上或平口钳上,先用标准刀与 Z 轴对刀器上表面接触(Z 轴对刀器指针指到零),记下此时的 Z 坐 标( 如 -388.5mm);再换成新刀具,同样使其与 Z 轴对刀器上表面接触,记下此时的 Z 坐标(如 -408.5mm),则两者的差值为 -20mm。再计算标准刀与断刀的长度补偿差值,如为 -22.5mm,两个差值求差为 2.5mm,说明新刀比断刀长了 2.5mm,则新刀的长度补偿值应为断刀长度补偿值(如 -308.6mm)的基础上加上2.5mm。此方法比较繁琐,也容易出错,故一般不用。
图 9 清零界面
4.2 相对坐标方式
将 Z 轴对刀器平放在工件上或平口钳上,先用标准刀与 Z 轴对刀器上表面接触(Z 轴对刀器指针指到零),按“设置”中的“相对清零”键,按“Z 轴清零”,再换成新刀具,同样使其与 Z 轴对刀器上表面接触,屏幕上显示的 Z 轴相对实际坐标就是长度差值,将其输入到对应的长度补偿值里即可。这种方法不用计算,操作非常简单。
图 10 刀具折断后的对刀图
5、结语
对于不同的操作人员和不同的数控系统,数控铣床的对刀方法不尽相同。在实际操作过程中通过不断摸索,选择操作最简单、最不容易出错的方法对刀,可以起到事半功倍的效果。
(阳涛 数控机床市场)
声明:本网站所收集的部分公开资料来源于互联网,转载的目的在于传递更多信息及用于网络分享,并不代表本站赞同其观点和对其真实性负责,也不构成任何其他建议。本站部分作品是由网友自主投稿和发布、编辑整理上传,对此类作品本站仅提供交流平台,不为其版权负责。如果您发现网站上所用视频、图片、文字如涉及作品版权问题,请第一时间告知,我们将根据您提供的证明材料确认版权并按国家标准支付稿酬或立即删除内容,以保证您的权益!联系电话:010-58612588 或 Email:editor@mmsonline.com.cn。
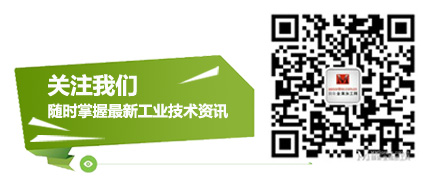
- 暂无反馈