数控机床信息智能采集技术的现状与趋势
20 世纪 80 年代以来,众多国家都把先进制造技术的研究和开发作为国家的关键技术进行优先发展,涌现出一批有代表性和影响力的制造模式及相关技术体系,有力地推动了制造业的发展。作为一个工业大国,我国的制造业正面临来自发达国家加速重振制造业与发展中国家以更低生产成本承接国际产业转移的“双向挤压”。在这种严峻形势下,我国唯有加快研发智能制造技术,提高工业化水平,以此来应对传统优势减弱的挑战。传统的制造业技术正逐步向自动化、信息化技术发展,通过高新技术改造制造业是现代制造业发展的必然趋势,是企业生存和发展的必要途径,所以智能制造被越来越多的国家所提出或实施.现代企业制造车间中绝大部分都是数控机床,但由于现有的数控机床种类繁多,并且不具备把内部信息自动输出的功能,极容易形成“信息孤岛”。因此,对数控机床进行数据智能采集是建设数字化车间的一个关键环节。通过对数控机床信息采集系统的研发,将会促使企业的办公、管理和生产趋于自动化、网络化和智能化,从而达到加强企业管理、减少工作失误、提高工作效率的目的,对数控机床利用率的提高、企业的发展均有重要意义。研究制造设备数据采集在机床监管的自动化,信息化和我国制造业发展十分重要。
1 、数控机床信息采集系统研究现状
目前,国内外主要是针对 SIEMENS 系统和FANUC 系统进行数控机床数据采集研究。因为相对于其它系统而言,这两种系统在实际生产中应用最为广泛。
国外一般大型数控厂商的数控系统都开发有相应的数据采集系统与之相配套。国内由于数控系统还不是很成熟,目前的研究还主要集中在对国外数控系统的数据采集上,常用的系统整体结构如图 1 所示.
由于机床的种类非常多,机床的数据采集方法不可能做到完全一致,要实现统一的数据采集,就必须根据机床的不同类型设计出不同的采集方法。目前,数控机床的主要数据采集方式有如下三种。其中,一种是基于标准通信接口的数据采集方式,这种方式中,数控机床的标准通信接口主要是 OPC 接口、RS-232 串口、DNC 接口等接口。当前,大部分数控机床都带有标准的通信接口,计算机可以直接通过这些接口与数控机床进行信息交换,从而实现对数控机床的数据采集。第二种是基于 PLC ( Programmable LogicControl)控制的数据采集方式,这种方式中,对于车间中一些老式的机床,本身不含有与外部通讯的接口,只能通过机床的电器电路以及机床内部的 PLC 进行机床信号的采集。这些信号可以通过外接 PLC、数据采集卡等硬件来完成。上述基于数控机床电器电路及PLC 的采集方法,在实际应用中并不具有通用性。在现代企业车间,要实现完整的数据采集系统必须将这些方法综合起来,灵活地运用,这样才能真正意义上实现企业制造车间的数字化。第三种是基于硬件的数据采集方式,这种方式中,数据是通过采用数字量及模拟量的进行采集,能够对机床的 I/O 信号进行检测以此实现对机床状态的监控。
2 、数控机床信息采集主要方式的对比分析
现在国内外市场上出现了一些对数控机床进行数据采集和监控的系统。现对这些系统的采集方法进行比较常见的数据采集软件普遍都是数据采集软件或系统二次开发软件来进行数据的采集。
2.1 采用标准通信接口进行数据采集方式
(1)基于数控机床的 OPC(OLE for Process Con-trol)接口数据采集文中英文简称格式要一致。
西门子系列的高档系统和 FANUC 系统都可以通过采用 OPC 的方式进行数据采集。巴西圣保罗大学基于机床 OPC 接口,实现对机床的状态信息采集远程访问。德国约翰内斯·海德汉博士公司研制的 Heidenhain 系统中大部分采用以太网对 OPC 接口进行数据采集。中国科学院大学的王帅采用多线程与 OPC 技术作为信息采集的手段,在建立 OPC 客户程序与数控设备的 DCOM 通讯连接的基础上对服务器进行数据采集。在采集中只需对 OPC 接口及采集软件做相应的配置即可,而无需额外添加硬件设备,并且这种方式能采集到机床几乎所有的状态信息。浙江大学付林云研发的基于 OPC 的数控机床数据采集系统,通过机床以太网口采集机床信息。南京工程学院李亚鹏通过利用 C# 编写 OPC 客户端程序,易控组态软件作为 OPC 服务器,实现了客户端程序对易控 OPC 服务器的访问并且获取了服务器中的数据,从而实现了数据的实时采集。这种采集方式的优点是采集到数据比较多,缺点是对机床配置要求比较高,老式机床会受到限制。
(2)基于数控机床的 DNC 接口数据采集
这种采集方法主要是通过对机床系统或者电气电路的特定部位设置采集点,测试出控制电路的电压信号,通过对照检测电压信号的变化,实现机床状态数据采集的功能。对于自带 DNC 通讯接口的高档数控,通过在 DNC 接口外接数据采集卡并运行相应的软件,实现对数控机床的数据采集功能。通过这种类型的 DNC 外接口,还可以实现对机床加工信息的实时采集和远程控制,并可以实时机床主轴转速、进给速度、刀具使用寿命等信息进行采集。日本 mori-seiki 公司研制的 MORI -NET Global Edition 信息采集软件能够实现对数控机床的监控及远程控制等,并把各种加工信息及采集的辅助信息能够分享或者上传至网上。南京航空航天大学武国峰通过外接数据采集卡的方式利用 DNC 实现了对数控机床的运行状态、完工零件等信息的采集。
(3)基于数控机床的 RS-232 串口数据采集
这种采集方法主要是通过 RS-232 串口在数控机床的控制程序里加入特定的宏程序指令,通过对返回的状态信息,如机床刀具坐标、加工状态、主轴转速、进给速度等信息的实时采集。日系数控系统,如 MAZAK ,三菱 M70 系列等采用系统厂商的数据采集软件进行数据采集,均能采集比较多的数据。大多支持串口编写宏程序,因而可使用宏程序进行数据的采集。北京华洋宏软件公司研制的 DNC-NET软件。该采集方式的优点是适用于老式的机床;缺点是机床输出的数据类型有限,想要对操作状态,监控等信息输出较为困难,尤其是当机床处在非加工状态时,就不能采集到机床状态信号。其次,机床输出数据有延时,不能够实时显示机床的运作状态。并且,采集需要要在加工程序中加入采集指令,程序编制复杂、较为麻烦。因此,宏程序数据采集一般只运用于老式机床数据采集。
2.2 采用 PLC 控制方式对机床的数据采集方式
这种采集方式主要是通过机床的电器电路以及机床内部的 PLC 进行机床信号的采集。如美国Predator Software 软件技术公司研发的盖勒普系统MDC(Manufacturing Data Collection & StatusManage-ment)。该系统能够实现对现场数据进行实时采集,并在分析管理之后,将信息存储在 Access ,SQL 和Oracle 等数据库中,能通过数控设备 PLC 进行数据采集,Siemens、Fanuc、Heidenhain 等多种型号控制系统均可被采集。
由于数控机床多用 PLC 控制,在计算机网络快捷、高效的时代下,PC-PLC 网络成为数控机床数据采集与监控的一个研究方向。中国计量学院的王国强利用 Siemens PLC 设计监管机床运行,实现对机床信息采集。但是由于数控机床的封闭性,为保证机床的正常工作需要熟悉每一台机床的 PLC. 实际应用中将很难直接从 PLC 读取机床的各种信息,这种采集方式的优点是对人机单元没有要求;缺点是需要对每一台机床的 PLC 都比较熟悉,以保证机床的正常工作。而且 Siemens 和 FANUC 数控机床自带的信息采集及检测软件价格相对昂贵。
2.3 基于数控机床的硬件数据采集方式
这种数据采集方式是通过采用数字量及模拟量的数据进行采集,能够对机床的 I/O 信号进行检测以此实现对机床状态的监控。南京航空航天大学的徐永乐数控机床信息采集系统以 ARM9 为硬件平台,通过开发 I/O 接口电路,实现机床侧信号到 ARM 端信号的转换。这种采集方式的优点是不受系统的限制,使用范围广;缺点是采集的数据少,当变动程序时,现场线路也将会随之改动,较为麻烦。
通过对上述三种采集方法的介绍可以得知,每种方法都有各自的优点,但也有其局限性。在选择方案的时候必须充分考虑机床的型号与所配有的通信接口以及所需要采集的信号种类。
如表 1 所示是对上述几种信息采集方法的比较.
3 、数控机床信息采集方式的发展趋势
在工业 4.0 发展和 《中国制造 2025》 的大前景下,国外很多企业对网络化车间管理和机床信息采集进行了研究开发,如德国 Siemens 公司研制的MCIS (Motion Control Information System )运动控制信息系统采集软件,丹麦 CIMCO 公司研制的 MDC-Max 6 信息采集软件,美国上升科技公司研制的extreme DNC 信息采集软件。相较于国外的机床信息管理系统,国内在这方面还处于起步阶段,我国市场上较为成熟的机床采集系统还较少,与国外产品相比仍有许多不足之处。比较有代表性的有北京机床研究所研发的 DNC 系统,北京兰光创新科技的CIMCO-DNC 系统等,九思易的自动化监控与信息管理平台等。
德国工业 4.0 等发展策略推动着智能制造,机械制造技术等核心产业的发展变革,影响着制造业的发展趋势,同时也影响着机床信息采集的发展趋势,主要发展趋势为:
(1)提高数控设备利用率,减少了数控设备可加工时间的相对浪费;
(2)通过智能化加工控制,对加工过程中外部变量进行采样监控,以此来实现加工参数的自动修正与补偿。
4、 结束语
我国是一个工业大国,机床信息采集的发展对我国工业的发展有着重要的意义。加快推进机床信息采集技术的研发是今后发展的必然趋势。与国外相比,我国现阶段成熟的信息采集系统还较少,研制出适合国情的数控信息采集系统,能实现资源共享和对数控设备的重组,并能提高数控机床使用效率,这是今后发展的重要趋势。
声明:本网站所收集的部分公开资料来源于互联网,转载的目的在于传递更多信息及用于网络分享,并不代表本站赞同其观点和对其真实性负责,也不构成任何其他建议。本站部分作品是由网友自主投稿和发布、编辑整理上传,对此类作品本站仅提供交流平台,不为其版权负责。如果您发现网站上所用视频、图片、文字如涉及作品版权问题,请第一时间告知,我们将根据您提供的证明材料确认版权并按国家标准支付稿酬或立即删除内容,以保证您的权益!联系电话:010-58612588 或 Email:editor@mmsonline.com.cn。
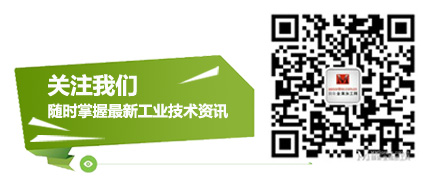
- 暂无反馈