航空部件的3D打印制造推进速度正在加快
3D打印或增材制造技术自使用以来备受关注,并逐步应用于航空部件。目前,金属部件打印技术的步伐正在加快,霍尼韦尔公司已经开始采用3D打印技术制造APU金属部件,并且还在积极探索新部件的应用,其他未涉足零部件打印制造的航空企业也希望尽早进入该市场。
飞机内饰聚合物零件采用3D打印或增材制造已有几十年的历史。但由金属制造的飞机零件通常被认为对飞机安全至关重要,而且金属本身性能独特,想利用3D打印技术或增材制造技术制造金属零件并非易事,因此推进金属零件的3D打印需要较长的时间。
但是,目前金属打印技术的发展步伐正在加快,如发动机OEM已经开始尝试将其扩展到各种对性能和重量都有严格要求的发动机部件和结构的制造中。同时,OEM也在多样化利用3D技术。金属粉末以及丝材都在使用,且正在开发用于金属材料打印的不同技术。
3D打印技术的两个明显优势是可以减少浪费和适合于小批量快速生产。减少浪费意味着可以降低部件生产成本,而小批量生产可以加快部件进入市场的速度,减少对大量库存的需求。但是,3D打印的真正潜力在于能够重新设计整个系统和部件,以实现精准构型和功能需求,而不是简单地通过设计零件或零件集合来简化传统制造方法。而且这种潜力在开发新型发动机和飞机时,体现得更加淋漓尽致。因此,从这一角度来看,未来还会有越来越多零件采用增材制造生产。目前部分OEM已开始涉足这一领域,部分原因是它们有小批量生产的实际需求,另一方面它们也在为未来航空航天增材制造业积累经验。
霍尼韦尔公司已经开始采用3D打印技术制造辅助动力装置(APU)金属部件。而且,应用增材制造技术制造的零件正在逐渐增多。霍尼韦尔采用3D打印金属零件的一个原因可能是传统制造不能及时生产。另一个原因是如果传统供应商退出或不再与公司合作,霍尼韦尔可能会自行打印零件;如果供应商不能满足质量标准,霍尼韦尔也可能会选择自己打印零部件。
霍尼韦尔认为,使用3D打印技术制造发动机和辅助动力装置零件的基本区别在于尺寸和功率不同。此外,两者都是涡轮机,并且具有相同的组成部分,包括压气机、燃烧室、高压和低压涡轮机及排气系统。因此,打印APU部件也是霍尼韦尔的重中之重。
霍尼韦尔打印的第一个零件是APU的防溅板,于2015年12月18日交付客户。防溅板是一个非常简单的部件,霍尼韦尔选择采用3D打印技术制造,是因为霍尼韦尔明白通过其自己的质量控制体系能够满足打印、工程认证要求,并被FAA和客户接受。
目前,霍尼韦尔正在打印APU的导管和油管。选择这些部件主要有四个原因:OEM与供应商合作困难、打印可能会缩短交货时间、打印可能会提高产品质量,以及打印可能会降低零件制造成本。在打印这些零件的过程中,霍尼韦尔正在使用两种3D技术。大部分部件打印使用的是激光粉末床熔化成型技术,也称为直接金属激光烧结(DMLS)。较小部分部件打印使用的是电子束熔融(EBM),也被称为电子束粉末床熔合。同时,OEM也在研究粘合剂喷射和直接能量沉积(DED)。
同时,霍尼韦尔正在评估APU的所有非旋转部件,将他们作为增材制造的备选对象,包括压气机和涡轮机匣、支架、安装件、管类、叶片和扩散器。除了辅助动力装置之外,霍尼韦尔还在研究发动机部件的增材制造。并且,一些非APU部件已经获得了应用认证。此外,一些机械部件项目将于今年获得认证生产。
相反,一家规模较小且成立不久的公司Norsk Titanium选择了一种完全不同的增材制造方法。该公司拥有140名员工,正在通过DED方法加工钛丝,每月为10架波音787生产长达12英寸的钛金属配件。
该公司表示,如GE发动机的燃料喷嘴等尺寸小的复杂零件最好采用粉末床熔化技术进行打印。大型的钛结构件使用丝材熔融沉积(wire-fed technology)效果更好。该公司在一项称为快速等离子沉积的专利工艺中使用氩气炬,零件初始重约1磅。Norsk机器打印的速度要以每小时千克计,而不是盎司,这是粉末床熔化技术的特点。
丝材熔融沉积技术只能生产出近净成形零件,之后必须加工掉多余的金属,但该方法相比其他加工方法仍然非常快速和经济。与切割钛金属相比,其优势在于大幅降低了昂贵钛金属的BTF比率(指制造一个零部件所需的材料量与最终零部件中所含材料量的比率)。通常,切割钛结构部件的BTF为15:1。Norsk Titanium丝材熔融沉积技术的BTF仅约为3:1,即制造2kg的零件可以节省24kg的钛。
由于使用的是钛丝,Norsk Titanium不用承担金属粉末的昂贵费用,该做法减少或抵消了BTF收益。该公司承认,钛丝的成本高于钛块,但是不多。Norsk Titanium使用的是标准Ti64钛卷,而且按照其要求的捻度和清洁度规格生产的。
Norsk Titanium用了10年时间开发了第四代非真空打印机,它可以干净、安静、快速地打印零件,这对于零件取证非常重要。该打印机每秒测量600个参数,可以确保控制所有印刷部件中的熔池和结构均匀。该公司指出,其在挪威安置的3台打印机和在纽约安置的9台打印机可以保证同时生产同样的零件。该打印机历时10个月获得FAA认证,并成为了波音公司的供应商。
目前,Norsk Titanium的打印机可打印的最大尺寸为900毫米×600毫米×300毫米(35英寸×24英寸×12英寸)。该公司正决定将其下一代打印机瞄准更大的零件或更复杂的零件。当然,其目标供应对象是大量使用钛部件的新型波音787、空客A350和庞巴迪C系列飞机。
Norsk Titanium正在生产数百种不同形状和尺寸的测试零件,以向监管机构和OEM展示其3D打印方法适用于更多零件。一旦证明其打印过程的能力和稳定性,个别部件的认证就会变得更加容易,且认证时间会更短。该公司现在可以借助仿真软件完成一些认证任务。
可用于打印的最好的零件应具有明显的尺寸维度。事实上,Norsk Titanium也提前做了大量的工作,例如,Norsk Titanium已经与美国势必锐航空系统公司(Spirit AeroSystems)建立了合作关系(势必锐航空系统公司生产数以千计的钛合金零件)。势必锐航空系统公司期望这些零件中至少有30%可以利用Norsk Titanium快速沉积工艺进行生产。
尚未涉足零部件打印制造的大型航空企业正急于进入该市场。伊顿宇航集团(Eaton’s Aerospace Group)正积极投资于增材制造业,其中航空增材制造业务总监Mike York率领了一个业务部门专门负责具体的增材制造技术应用。伊顿宇航集团在密歇根州南菲尔德市拥有一个卓越中心,用于开发聚合物和金属增材制造。该中心正在试行开发,并将提供小批量零件生产。此外,该中心正在开发适用于自身高温聚合物材料的增材制造技术。未来伊顿宇航集团还计划将金属材料的3D打印技术推向市场。在印度西部的普纳,一个更大的伊顿团队正在研究增材工艺和产品的模拟。
伊顿宇航集团主要对DMLS、EB、DED和冷喷涂技术感兴趣。对于聚合物,专注于直接激光烧结和熔融沉积建模,同时还探索其他工艺。该公司希望提前布局这一市场,获得速度、成本、性能方面的各种制造优势。该公司已确定将排气管、阀门、过滤组件和其他产品作为金属增材制造的候选产品。对于聚合物,其研究包括用增材聚合物替换一些铝部件以节省成本并减轻重量。
决定增材制造零件适用性的关键因素之一是该零件的复杂性。在传统方法方法制造中,复杂性意味着会增加制造成本。但是使用增材制造,复杂性并不一定会增加成本。因此随着增材工艺的改进,零件通过降低复杂程度以缩减成本的需求将逐渐减少。除了能够节省成本,利用增材制造还可以实现更新的设计,也就是说在减轻重量或减小尺寸或改善流体流动或压力的同时还可以改善零件性能。
伊顿宇航集团计划在2019年底之前推出首款增材制造零件,但后续的增材制造产品还需等待一些时日。但伊顿公司认为,未来5~10年后其产品中很大一部分将由增材制造完成。
声明:本网站所收集的部分公开资料来源于互联网,转载的目的在于传递更多信息及用于网络分享,并不代表本站赞同其观点和对其真实性负责,也不构成任何其他建议。本站部分作品是由网友自主投稿和发布、编辑整理上传,对此类作品本站仅提供交流平台,不为其版权负责。如果您发现网站上所用视频、图片、文字如涉及作品版权问题,请第一时间告知,我们将根据您提供的证明材料确认版权并按国家标准支付稿酬或立即删除内容,以保证您的权益!联系电话:010-58612588 或 Email:editor@mmsonline.com.cn。
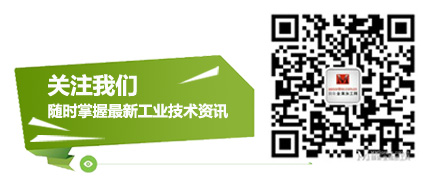
雷尼绍参展慕尼黑上海光博会2025
- 暂无反馈