车床机械加工失误合集,悬念百出!
数控机床应用于制造业的各领域,但在数控加工过程中,由于对刀错误、程序错误、操作失误、装夹不牢、工装设计不合理、机床不稳定等,会造成撞刀事故的发生,轻则导致工件报废,重则使机床发生损坏,人身安全事故。不小心要命!切记!!
数控机床加工撞机事故的视频集
防错,日文称POKA-YOKE,英文又称Error Proof 或 Fool Proof(防呆)。
从字面上看,防错,就是防止错误的发生。“错误”为什么会发生?“错误”造成与预期的偏离,最终可能产生缺陷,很大一部分原因是人们由于疏忽、无意识等造成的。
对于制造业来说,最担心的就是产品缺陷的产生,而“人机料法环”都有可能导致缺陷。
人为的错误不仅存在,无法完全避免,另外,人为错误还会影响机、料、法、环、测等因素(毕竟事情都是人做的,没法完全独立),比如加错料了。
人为错误的原因有哪些?
错误发生的十大原因分别是:遗忘、理解错误、识别错误、新手错误、意愿错误、疏忽错误、迟钝错误、缺乏标准导致的错误、意外错误、故意的错误。
a. 遗忘:当注意力不集中在某处时,会遗忘某些事情。
b. 理解错误:人们常根据以前的经验来理解新遇到的事物。
c. 识别错误:看得太快、看不清楚或者没仔细看会发生错误。
d. 新手错误:缺乏经验产生的错误,比如老员工一般比新员工少犯错误。
e. 意愿错误:特定时候决定不采纳某些规则发生的错误。
f. 疏忽错误:心不在焉发生的错误,比如无意识的穿过街道,没有留意到红灯是亮着的。
g. 迟钝错误:判断或者行动迟缓发生的错误。
h.缺乏标准导致的错误:没有规矩,不成方圆。
i. 意外错误:没有考虑到的情况发生了,导致的错误,比如某个检验设备突然故障了。
j. 故意错误:人为地故意制造错误,这个性质就恶劣啦。
由于操作不当或编程错误等原因,易使刀具或刀架撞到工件或机床上,轻者会撞坏刀具和被加工的零件,重者会损坏机床部件,使机床的加工精度丧失,甚至造成人身事故。因此,从保持精度的角度看,在数控机床使用中绝不允许刀具和机床或工件相撞。
撞机原因(欢迎补充)
程序编写错误
工艺安排错误,工序承接关系考虑不周详,参数设定错误。
例:A.坐标设定为底为零,而实际中却以顶为0;
B.安全高度过低,导致刀具不能完全抬出工件;
C.二次开粗余量比前一把刀少;
D.程序写完之后应对程序之路径进行分析检查;
程序单备注错误
例:A.单边碰数写成四边分中;
B.台钳夹持距离或工件凸出距离标注错误;
C.刀具伸出长度备注不详或错误时导致撞刀;
D.程序单应尽量详细;
E.程序单设变时应采用以新换旧之原则:将旧的程序单消毁。
刀具测量错误
例: A.对刀数据输入未考虑对刀杆;
B.刀具装刀过短;
C.刀具测量要使用科学的方法,尽可能用较精确的仪器;
D.装刀长度要比实际深度长出2-5mm。
程序传输错误
程序号呼叫错误或程序有修改,但仍然用旧的程序进行加工;
现场加工者必须在加工前检查程序的详细数据;
例如程序编写的时间和日期,并用熊族模拟。
选刀错误
毛坯超出预期,毛坯过大与程序设定之毛坯不相符
工件材料本身有缺陷或硬度过高
装夹因素,垫块干涉而程序中未考虑
机床故障,突然断电,雷击导致撞刀等
如何避免数控机床出现安全问题呢?
1、编程员在编程时设定的工件坐标系原点应在工件毛坯以外,至少应在工件表面上。
在正常情况下,工件坐标系原点可以射在任何地方,只要此原点与机床坐标系原点有一定的关系即可。但在实际操作时,万一出现指令为零或接近零时,刀具就会直接指零或接近零的位置。在铣削加工时,刀具将奔向工作台或夹具基面;在车削加工时,将奔向卡盘基面。这样,刀具将穿透工件直指基准面。此时,若为快速移动,则必发生事故。 FANUC系统一般设定:当省略小数点时,为最小输入单位,通常为Hm。当疏漏了小数点时,则输入的值将缩小成千分之一,此时,输入的值就会接近于零。或者,由于其他原因,使刀具本应离开工件但实际并未离开工件而进入工件之内。出现这种情况是,工件坐标系零点应设在工件以外或在工作台(或夹具)基面上,其结果将是不一样的。
2、编程员和操作者在书写程序时,对小数点要倍加小心。
FANUC系统在省略小数点时为最小设定单位,而大多数国产系统及欧美的一些系统,在省略小数点时,则为mm,即计算器输入方式。若你习惯了计算器输入方式,则在FANUC系统上就会出现问题。不少编程员和操作者,可能两种系统都要使用,为防止因小数点而出现问题。 为了使小数点醒目,在编程时往往把孤立的小数点写为“0”的形式。当然,系统在执行时,数值的小数点以后的零被忽略。
3、操作者在调整工件坐标系时,应把基准点设在多有刀具物理(几何)长度以外,至少应在最长刀具的刀位点上。
对于工件安装图上的工件坐标系,操作者在机床上是通过设置机床坐标系偏移来获得的。亦即,操作者在机床上设定一个基准点,并找到这一基准点与编程员设定的工件坐标系零点之间的尺寸,并把这一尺寸设为工件坐标系偏移。
在车床上,可把基准点设在刀架旋转中心、基准刀具刀尖上或别的位置。如果不附加另外的运动,则编程员指令的零,即为刀架(机床)的基准点移动到编程的玲位置。此时,若基准点设在刀架旋转中心,则刀架必与工件相撞。为保证不相撞,则机床上的基准点不但应设在刀架之外,还应设在所有刀具之外。这样即使刀架上装有刀具时,基准点也不会与工件相撞。
▲
在铣床上,X、Y轴的基准点在主轴轴心线上。但是,Z轴的基准点,可以设在主轴端或在主轴端之外的某点上。若在主轴端,当指令为零时,主轴端将到达坐标系指定的零位置。此时,主轴端的端面键将与工件相撞:若主轴上再装有刀具,则必与工件相撞。为保证不相撞,则Z轴上的基准点应设在所有刀具长度之外。即使不附加别的运动,基准点也不会撞工件。
4、操作者在调整刀具长度偏置时,应保证其偏置值为负值。
编程员在指令刀具长度补偿时,车削用T代码指令,而铣削用G43指令,即把刀具长度偏置值加到指令值上。在机床坐标轴的方向上,规定刀具远离工件的运动方向为正,刀具移近工件的方向为负。操作者把刀偏值调整为负值,是指令刀具移向工件。程序中指令刀具向工件趋近时,除了指令值之外,还要附加刀具的偏置值,这个附加的值是移向工件的。此时,万一此值被疏漏,刀具就不会到达目标点。
为使刀具偏置值为负值,则在规定机床上的基准点时,必须设在所有刀具长度之外,至少应在基准刀具的刀位(尖)点上。
1、 查看光滑系统,压力表状况,清洁光滑系统过滤网,替换光滑油,疏通油路。
2、 查看气路系统,清洁空气过滤网,消除压力气体的走漏。
3、 查看液路系统,清洁过滤器、清洁油箱,替换或过滤油液。能够的情况下,替换密封件。
4、 紧固各传动部件,替换不良标准件。
5、 油脂光滑部位,按需求,加注光滑脂。
6、 清洁、清洁各传动面。
7、 查看刀库、机械手状况,剖析机械手磨损状况,向客户提出替换主张。
8、 批改批改外部元件的损坏件。
9、 查看防护罩状况。精确的将信息反馈给客户
声明:本网站所收集的部分公开资料来源于互联网,转载的目的在于传递更多信息及用于网络分享,并不代表本站赞同其观点和对其真实性负责,也不构成任何其他建议。本站部分作品是由网友自主投稿和发布、编辑整理上传,对此类作品本站仅提供交流平台,不为其版权负责。如果您发现网站上所用视频、图片、文字如涉及作品版权问题,请第一时间告知,我们将根据您提供的证明材料确认版权并按国家标准支付稿酬或立即删除内容,以保证您的权益!联系电话:010-58612588 或 Email:editor@mmsonline.com.cn。
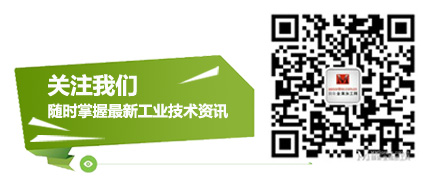
- 暂无反馈