机器人执行扫描 宝马无需拆解就可分析车辆
据外媒报道,宝马集团在原型车研发、生产和分析过程中引入了计算机断层摄影技术(CT),为汽车行业首例。得益于此项技术,即使在车辆的早期研发阶段,宝马都可对从宝马MINI到劳斯莱斯等全系车型进行质量管理。扫描工作由4个机器人执行,机器人在原型车的外部四处走动,从而产生数千个横断层面影像,用于详细检查车辆的创新技术、新材料和粘接技术。目前,车辆基本都是需要拆解才能进行分析,但是CT可在车辆完好无损的情况下,检查车辆。新型X射线系统安装于宝马集团位于德国慕尼黑(Munich)研究与创新中心(FIZ)的试点工厂,位于宝马研发部与生产部的十字路口。
生产集成和试点工厂负责人Udo Hanle表示:“使用先进的计算机断层摄影技术是我们向前发展的重要一步,因为该技术将帮助我们进一步提高产品质量。我们现在无需先拆解原型车就可详细分析他们,新系统让我们以传统静态计算机断层扫描技术无法实现的方式检查车辆。最终,将使我们更快地将新技术集成到一系列的车辆中。”
分析内部结构
材料与工艺分析主管Michael Koch补充说:“多年来,我们一直在用CT和X射线扫描和检查车辆,但该最新系统将质量保证提高至全新水平。我们现在分析车辆可达微米级别。”
由于各种原因,如检测焊接和螺钉连接以及在涂漆前后需要验证车身状况(极端温度会影响粘合剂粘合),就需要达到如此程度的细节检查。然后,可根据扫描结果对批量生产的车型进行针对性的修改。
扫描工作由4个机器人协同进行。一旦车辆在扫描系统中就位,机器人就会在其四周移动。机器人结对工作,他们向车辆发送X射线,然后再传给合作对象。然后,他们所搜集的数据通过专门研发的计算机程序计算出多层、三维影像,构成详细分析车辆内部工作原理的基础,提供了小至100微米的物体信息(大约是人类头发的宽度)。
目前,工程师们正在研究人工智能用于评估检查结果可达到何种程度。通过处理大量数据,人工智能软件可以学习到不同的模式,连接各个数据项,并逐步自动评估检查结果。
两年研发工作
宝马集团工程师和佛劳恩霍夫X射线技术研发中心(EZRT)花了两年的时间研发该系统,是汽车行业的首例。宝马集团项目经理Philipp Janello解释说:“与X射线专家和试点工厂的工程师们合作,借助在车身上进行全面的测试评估,我们可以改善测试系统软件。”最终,研发出了一个满足宝马集团要求的定制系统。
声明:本网站所收集的部分公开资料来源于互联网,转载的目的在于传递更多信息及用于网络分享,并不代表本站赞同其观点和对其真实性负责,也不构成任何其他建议。本站部分作品是由网友自主投稿和发布、编辑整理上传,对此类作品本站仅提供交流平台,不为其版权负责。如果您发现网站上所用视频、图片、文字如涉及作品版权问题,请第一时间告知,我们将根据您提供的证明材料确认版权并按国家标准支付稿酬或立即删除内容,以保证您的权益!联系电话:010-58612588 或 Email:editor@mmsonline.com.cn。
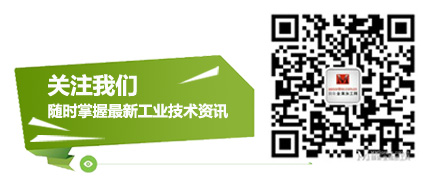
- 暂无反馈