【干货】数控切削加工尺寸不稳定怎么办?
数控切削加工尺寸不稳定的问题可以说让人很头疼了,小编为您总结了十种常见情况和对应的解决方法。
话不多说,直接上干货!
1、工件尺寸准确,表面光洁度差
故障原因:
1)刀具刀尖受损,不锋利。
2)机床产生共振,放置不平稳。
3)机械有爬行现象。
4)加工工艺不好。
解决方案(与上对照):
1)刀具磨损或受损后不锋利,则重新磨刀或选择更好的刀具重新对刀。
2)机床产生共振或放置不平稳,调整水平,打下基础,固定平稳。
3)机械产生爬行的原因为拖板导轨磨损厉害,丝杆滚珠磨损或松动。机床应注意保养,上下班之后应清扫铁丝,并及时加润滑油,以减少摩擦。
4)选择适合工件加工的冷却液;在能达到其它工序加工要求的情况下,尽量选用较高的主轴转速。
2、工件产生锥度大小头现象
故障原因:
1)机床放置的水平没调整好,一高一低,产生放置不平稳。
2)车削长轴时,工件材料比较硬,刀具吃刀比较深,造成让刀现象。
3)尾座顶针与主轴不同心。
解决方案
1)使用水平仪调整机床的水平度,打下扎实的地基,把机床固定好提高其韧性。
2)选择合理的工艺和适当的切削进给量避免刀具受力让刀。
3)调整尾座。
3、驱动器相位灯正常,但工件尺寸不一
故障原因
1)机床拖板长期高速运行,导致丝杆和轴承磨损。
2)刀架的重复定位精度在长期使用中产生偏差。
3)拖板每次都能准确回到加工起点,但加工工件尺寸仍然变化。此种现象一般由主轴引起,主轴的高速转动使轴承磨损严重,导致加工尺寸变化。
解决方案(与上对照)
1)用百分表靠在刀架底部,同时通过系统编辑一个固定循环程序,检查拖板的重复定位精度,调整丝杆间隙,更换轴承。
2)用百分表检查刀架的重复定位精度,调整机械或更换刀架。
3)用百分表检测加工工件后是否能准确回到程序起点;若可以,则检修主轴,更换轴承。
4、工件尺寸变化,或轴向变化
故障原因
1)快速定位的速度太快,驱动和电机反应不过来而产生。
2)在长期摩擦磨损后机械的拖板丝杆和轴承过紧卡死。
3)刀架换刀后太松锁不紧。
4)编辑的程序错误,头、尾没有呼应或没取消刀补就结束。
5)系统的电子齿轮比或步距角设置错误。
解决方案(与上对照)
1)快速定位速度太快,则适当调整G0 的速度、切削加减速度和时间使驱动器和电机在额定的运行频率下正常动作。
2)在出现机床磨损后产生拖板、丝杆和轴承过紧卡死,则必须重新调整修复。
3)刀架换刀后太松则检查刀架反转时间是否满足,检查刀架内部的涡轮涡杆是否磨损,间隙是否太大,安装是否过松等。
4)如果是程序原因造成的,则必须修改程序,按照工件图纸要求改进,选择合理的加工工艺,按照说明书的指令要求编写正确的程序。
5)若发现尺寸偏差太大则检查系统参数是否设置合理,特别是电子齿轮比和步距角等参数是否被破坏,出现此现象可通过打百份表来测量。
5、加工圆弧效果不理想,尺寸不到位
故障原因
1)振动频率的重叠导致共振。
2)加工工艺。
3)参数设置不合理,进给速度过大,使圆弧加工失步。
4)丝杆间隙大引起的松动或丝杆过紧引起的失步。
5)同步带磨损。
解决方案
1)找出产生共振的部件,改变其频率,避免共振。
2)考虑工件材料的加工工艺,合理编制程序。
3)对于步进电机,加工速率 F 不可设置过大。
4)机床是否安装牢固,放置平稳,拖板是否磨损后过紧,间隙增大或刀架松动等。
5)更换同步带。
6、批量生产中,偶尔出现工件超差
1)批量生产中偶尔出现一件尺寸有变化,然后不用修改任何参数再加工,却恢复正常情况。
2)在批量生产中偶尔出现一件尺寸不准,然后再继续加工尺寸仍不合格,而重新对刀后又准确。
解决方案
1)必须认真检查工装夹具,且考虑到操作者的操作方法,及装夹的可靠性;由于装夹引起的尺寸变化,必须改善工装使工人尽量避免人为疏忽作出误判现象。
2)数控系统可能受到外界电源的波动或受到干扰后自动产生干扰脉冲,传给驱动致使驱动接受多余的脉冲驱动电机多走或少走现象;了解掌握其规律,尽量采用一些抗干扰的措施,如:强电场干扰的强电电缆与弱电信号的信号线隔离,加入抗干扰的吸收电容和采用屏蔽线隔离。另外,检查地线是否连接牢固,接地触点最近,采取一切抗干扰措施避免系统受干扰。
7、工件的每道工序都有递增或递减的现象
故障原因
1)程序编写错误。
2)系统参数设置不合理。
3)配置设置不当。
4)机械传动部件有规律周期性的变化故障。
解决方案
1)检查程序使用的指令是否按说明书规定的要求轨迹执行,可以通过打百份表来判断,把百分表定位在程序的起点让程序结束后拖板是否回到起点位置,再重复执行几遍观察其结果,掌握其规律。
2)检查系统参数是否设置合理或被人为改动。
3)有关的机床配置在连接计算耦合参数上的计算是否符合要求,脉冲当量是否准确。
4)检查机床传动部分有没有损坏,齿轮耦合是否均匀,检查是否存在周期性,规律性故障现象。若有则检查其关键部份并给予排除。
8、工件尺寸与实际尺寸只相差几丝
故障原因
1)机床在长期使用中磨擦、磨损,丝杆的间隙随着增大,机床的丝杆反向间隙过大使加工过程的尺寸漂浮不定,故工件的误差总在这间隙范围内变化。
2)加工工件使用的刀具选型不对,易损,刀具装夹不正或不紧等。
3)工艺方面根据工件材料选择合理的主轴转速、切削进给速度和切削量。
4)与机床放置的平衡度和稳固性有关。
5)数控系统产生失步或驱动选型时功率不够,扭矩小等原因产生。
6)刀架换刀后是否锁住锁紧。
7)主轴是否存在跳动串动和尾座同轴度差等现象。
8)在一些特殊加工场合,反向间隙无法补入,导致加工总是存在偏差。
解决方案(与上对照)
1)机床磨损丝杆间隙变大后通过调整丝杆螺母和修紧中拖板线条减小间隙,或通过打百份表得出间隙值(一般间隙在 0.15 mm 以内)可补进电脑,可通过电脑的间隙补偿功能来把间隙取代,使工件尺寸符合要求。
2)由于是刀具材质使加工工件尺寸产生变化,则按要求合理选择刀具,而由于刀具装夹不正等原因产生的则根据工件的工艺要求合理选择刀具角度和工装夹具。
3)当怀疑是加工方面的工艺问题,则根据材料的性质,合理地编制加工工艺选择适当的主轴转速,切削进给速度和切削量。
4)由于机床共振引起则把机床放置平稳,调整好水平,必要时打下地基,安装稳固。
5)数控系统产生的尺寸变化,首先判断程序是否按图纸尺寸要求编制,然后再根据所选的配置检查设置的参数是否合理(如 : G0快速定位速度和切削时的加减速时间常数等)。是否有人故意改动,其次是考虑所选配的驱动器功率大小是否合理,通过判断相位灯观察电脑发给驱动的脉冲是否有失步现象。
6)检查刀架换刀后反转时间够不够,是否使刀架有足够的时间来锁紧,检查刀架的定位和锁紧螺丝是否有松动。
7)检查主轴和尾座的同轴度是否存在跳动、串动等现象。
8)利用编程技巧消除间隙。
9、系统引起的尺寸变化不稳定
故障原因
1)系统参数设置不合理。
2)工作电压不稳定。
3)系统受外部干扰,导致系统失步。
4)已加电容,但系统与驱动器之间的阻抗不匹配,导致有用信号丢失。
5)系统与驱动器之间信号传输不正确。
6)系统损坏或内部故障。
解决方案(与上对照)
1)快速速度,加速时间是否过大,主轴转速,切削速度是否合理,是否因为操作者的参数修改导致系统性能改变。
2)加装稳压设备。
3)接地线并确定已可靠连接,在驱动器脉冲输出触点处加抗干扰吸收电容;一般的情况下变频器的干扰较大,请在带负载的请况下判断,因为越大的负载会让变频器负载电流越大,产生的干扰也越大。
4)选择适当的电容型号。
5)检查系统与驱动器之间的信号连接线是否带屏蔽,连接是否可靠,检查系统脉冲发生信号是否丢失或增加。
6)送厂维修或更换主板。
10、机械方面引起的加工尺寸不稳定
故障原因
1)步进电机阻尼片是否过紧或过松。
2)电机插头进水造成绝缘性能下降,电机损坏。
3)加工出的工件大小头,装夹不当。
4)工件出现椭圆。
5)丝杆反向间隙过大。
6)机械丝杆安装过紧。
解决方案(与上对照)
1)调整阻尼盘,使电机处于非共振状态。
2)更换电机插头,做好防护,或是更换电机。
3)检查进刀量是否过大或过快造成的过负荷,检查工件装夹不应伸出卡盘太长,避免让刀。
4)检查主轴的跳动,检修主轴,更换轴承。
5)通过打百分表检查丝杆的反向间隙,是否已从系统将间隙补入,补入后间隙是否过大。
6)检查丝杆是否存在爬行,是否存在响应慢的现象。
声明:本网站所收集的部分公开资料来源于互联网,转载的目的在于传递更多信息及用于网络分享,并不代表本站赞同其观点和对其真实性负责,也不构成任何其他建议。本站部分作品是由网友自主投稿和发布、编辑整理上传,对此类作品本站仅提供交流平台,不为其版权负责。如果您发现网站上所用视频、图片、文字如涉及作品版权问题,请第一时间告知,我们将根据您提供的证明材料确认版权并按国家标准支付稿酬或立即删除内容,以保证您的权益!联系电话:010-58612588 或 Email:editor@mmsonline.com.cn。
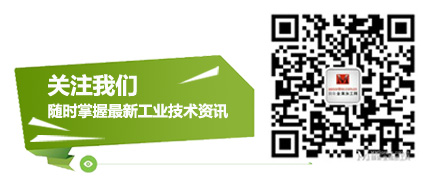
- 暂无反馈