提高齿轮加工精度的有效策略分析
近年来,随着机械精密化、智能化的推进,人们对机械制造的精良程度和使用性能有了更高层次的要求。因此,零件加工业也要进行相应的调整和转变。齿轮加工作为机械制造中的重要环节,其加工精度是诸多业内人士共同关注的焦点,也是专业人士一直探索与研究的重要方向。因此,在这种大环境下,对齿轮加工加工精度展开了探讨是非常有必要和有意义的。
1 、齿轮加工精度的主要影响因素分析
在齿轮实际加工过程中,可以对其加工精度造成影响的主要因素有以下 6 种:①齿轮铸造时齿坯的误差,其对齿轮加工精度的影响是根本性的;②制造过程中加工道具的制造误差;③刃磨误差;④刀具安装时产生的误差;⑤齿轮在加工过程中产生的安装误差;⑥加工机床自身存在的误差。以上任何一种误差超过规定值都会对齿轮加工精度造成影响,且多种误差叠加的影响会导致精度进一步下降。而根据 GB/T 10095 中的相关规定,齿轮标准误差通常可以细分为 5 个方面,即周节累积误差、基节误差、齿形误差、齿圈径向误差以及齿向误差。因此,为了确保齿轮加工精度,我们在其加工过程中,应对上述 5 个方面的标准误差实施全面、严格、规范的检验。
2 、提高齿轮加工精度的有效策略
2.1 提高齿坯件的加工质量
在齿轮加工过程中,齿坯件的加工质量对其精度有着根本性的影响,因为其实齿轮后续加工的基础直接关系着齿轮加工的安装和定位精度。比如,在齿轮滚齿过程中,如果齿坯安装缝隙比较大,则易导致齿坯加工偏心问题的发生。这不仅会导致齿圈出现圈径跳动偏差过大的情况,还会直接影响齿轮后续加工,严重时会造成齿轮加工失败。
此外,齿圈齿坯的断面跳动精度还会对剃齿加工工序造成不良影响,这是因为剃齿时的定位面是齿轮端面,通常在齿轮齿坯最大圆跳动位置进行锥齿而最终加工成型的。因此,在齿轮加工过程中,要严格控制齿坯的加工质量,具体要求为:在加工孔类齿轮的过程中,齿轮孔精度应当控制在 H6 级别,且在齿坯外圆不大于 80 直径的端面跳动量必须控制在 0.017,大于 80 的则应控制在 0.022 1 之内;在加工轴类齿轮齿坯时,外圆尺寸精度定位时应按照 H5 级别进行,外圆跳动应当控制在 0.015 之内。
2.2 提高机床自身的精度
齿轮加工离不开机床,所以,机床的工作性能和精度也会直接影响齿轮的加工精度。据相关统计显示,大部分齿轮加工精度下降的原因是机床自身存在问题。因此,想要提升齿轮加工精度,还需要从提高机床精度和工作性能做起。具体措施有以下 2 个:①加工前应仔细检查机床零配件等各方面的细节,科学、仔细地调节切削用量、材料安装等,尤其要注重刀具的选择、几何参数的设置和机器润滑冷却等。②在齿轮加工前,应提升刀具的刚度,并及时养护设备;在加工过程中一旦发生问题,应通知维修人员,争取在第一时间解决问题,防止影响到齿轮加工的精度。
2.3 减小齿轮与工装装夹的误差
在提高机床自身精度的同时,我们还应减小齿轮与工装装夹之间的误差,这也是提升齿轮加工精度的一项重要举措。此外,改良加工工艺、提高夹具中心轴和胎具中心的精确度,也能达到提升齿轮加工精度的目的。
2.4 完善齿轮加工工艺
除了齿坯件、机床及夹具等基础设施外,加工工艺也是影响齿轮加工精度的重要因素。想要提高加工精确度,应不断完善加工工艺。具体措施有以下 4 个:
①保证工作台与夹具中心轴轴心能完全重合。通常情况下,我们在会在夹具底层安装止口,虽然该止口与工作台之间的缝隙较小,但还是会产生误差,所以,安装时我们应尽量避免存在缝隙。
②安装刀具前应充分检查,确保刀具端面与内孔等部位清洁,并将刀刃轻轻推入刀柄中,严禁使用重物锤击刀柄。
③提升滚齿的精度。滚齿是我们在加工齿轮时常用的处理方式,要想提升滚齿精度,必须使用精良的滚刀在精密的滚齿机上操作。此外,还应确保机床回转中心与齿轮中心完美重合,以有效减小径向误差;提升工作台蜗轮副回转的精度;将刀架与机床等垂直放至既定区域,并科学调整其与各零件轴线的偏移,控制好打磨量,严禁产生较多的余量。
④提升齿轮自身的热处理能力。一般在进行热处理的过程中,齿轮精确度、硬度和使用年限等都会受到一定程度的影响,且在热处理之后还要进行磨齿处理,这一工序也会对齿轮精度造成影响,因此,严控齿轮加工中的各个环节和细节才是确保齿轮精度的最有力措施。
3、 结束语
综上所述,在齿轮加工过程中,能对其精确度造成影响的因素众多,既包括加工环境因素,又包括其自身因素。因此,想要做好这项工作,应增强工作人员的质量意识,从齿轮加工的机床、夹具、刀具、各生产工序等着手,严把各道质量管卡,并有效提升整个生产加工团队的技术水平,确保齿轮加工的科学性、规范性,从而保证齿轮精确度的提升。
声明:本网站所收集的部分公开资料来源于互联网,转载的目的在于传递更多信息及用于网络分享,并不代表本站赞同其观点和对其真实性负责,也不构成任何其他建议。本站部分作品是由网友自主投稿和发布、编辑整理上传,对此类作品本站仅提供交流平台,不为其版权负责。如果您发现网站上所用视频、图片、文字如涉及作品版权问题,请第一时间告知,我们将根据您提供的证明材料确认版权并按国家标准支付稿酬或立即删除内容,以保证您的权益!联系电话:010-58612588 或 Email:editor@mmsonline.com.cn。
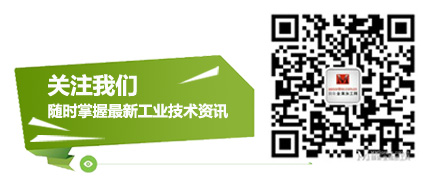
- 暂无反馈