摇臂钻--车架纵梁孔加工
车架是载重汽车的重要零部件,素有载重车的“脊梁”之称。载重车品种的变化关键是车架品种的变化,因此,优质高效地实现车架纵梁孔的加工显得特别重要。
载重车架大多是边梁式结构,由纵梁与横梁等零部件装配连接而成。一般纵梁由主梁和加强板(或称加强梁、副梁)组成,纵梁的形状为槽型。加强板镶套在主梁内,与主梁用铆钉(或者点焊、塞焊)连接。车架单根纵梁上平均有大小和用途不同的各类孔达到350多个,孔径从φ7~50mm不等,各种孔的质量要求也略有差别。
目前,东风公司车架厂纵梁孔加工的主要方式有:模具落料冲孔、平面数控冲孔机冲孔、三面数控冲孔机冲孔和通过模板利用摇臂钻床钻孔等。不同的孔在加工方式、加工精度以及加工效率等方面存在着较大的差别。
各种孔加工工艺
纵梁模具冲孔成形的工艺为:剪切(或直接使用单倍尺片料)→落料冲孔→成形(槽型)。主要是利用3000~5000t压力机,对单倍尺平板料进行冲孔加工,一般加工时,冲孔模和成形模分开,冲孔时表面涂N32#机油,可以减少发热,提高表面质量,延长模具的使用寿命。平面数控冲孔是一种先加工孔后成形槽型纵梁的工艺方式,其工艺为:剪切(或直接使用单倍尺片料)→平面冲冲孔→成形(槽型);或者是:剪切(或直接使用单倍尺片料)→模具落料冲定位孔→平面冲冲孔→成形(槽型),两种方式分别适用于以边定位和以孔定位的平面数控冲孔机。三面数控冲孔工艺适合于已经成形后的槽型纵梁的孔加工。大梁冲孔前如果能够对纵梁表面进行处理,如酸洗和抛丸等,可以有效提高纵梁孔的加工质量,延长冲头的使用寿命。
纵梁钻孔有三种情况:一是平板料叠钻孔,这也是一种先加工孔再成形的纵梁生产工艺方式,就是先利用压力机或者平面冲加工出一组定位孔,将平板料(一般不超过5片)叠放在一起,最上面放钻模板。钻模板可以是机加工的钻模板,也可以平面冲加工出来的“样板梁”,一般“样板梁”只使用一次。二是以主梁为模板,套钻加强板上的孔。三是以成品的左(右)纵梁为模板,通过定位、夹紧的方式,将左(右)纵梁上的孔复制到右(左)纵梁上。
各种工艺精度比较
1. 孔加工方式不同,则加工出的孔表面粗糙度不同
平面数控冲和三面数控冲也是利用上下模具冲孔原理,其加工出的孔的表面粗糙度与大梁模具冲孔的表面粗糙度基本相当,能达到IT14,可以通过调整上下模的间隙及刃口状态,使孔表面粗糙度达到较理想的状态,故一般不需要清理毛刺等工序环节就可以直接进入下一道工序。有些车架专业生产厂,将抛丸(或酸洗等表面处理)工序布置在冲孔工序之后,虽然减少了冲头的使用寿命,但是对于冲孔后消除纵梁表面应力,提高孔加工的表面粗糙度是非常有利的。而钻孔则不同,钻孔时会产生大量铁屑,因此钻孔后孔的表面粗糙度较差,孔周的毛刺必须清理。提高钻孔后的表面粗糙度方式主要有:一是可以根据不同的大梁材料,对刀具的顶角进行改进,利于断屑;二是钻孔时使用切削液对刀具进行冷却,当然,切削液不易回收,容易造成环境污染;三是刀具每钻10~20个孔就进行刃磨。我厂引进了自动钻头刃磨机,大大提高了刃磨效率,减少了辅助作业时间。
2. 各种方式加工孔的尺寸公差和形位公差也不相同
前面已经提到,平面数控冲和三面数控冲也是利用上下模具冲孔原理,和模具冲孔一样,由于材料的回弹等因素,会导致孔径偏小、孔内毛刺大及孔位置度偏差等质量问题。钻孔也存在这种现象,表1是几种孔加工方式的精度对比。
3. 各种孔加工工艺的效率
纵梁孔加工的工艺不同,则加工的效率不同,成本也不同。在具体的工艺选择上,则根据不同的企业的生产规模、不同产品的具体产量进行优化组合。从表1可以看出,数控冲孔柔性化程度高,在新产品研发、试制等方面具有明显的优势。
质量与效率的提升
1.质量与数量是一对矛盾,东风公司车架厂在处理纵梁孔加工时,对不同的孔(孔组)区别对待。例如:对于纵梁腹面和翼面有装配关系的孔组,如板簧支架用孔,采取平面冲(三面冲)先加工定位工艺孔,再用T型模板补钻的方法来保证。对于后桥装配用孔,先在车架左右纵梁下翼面的后桥中心制作一个φ11mm的定位工艺孔,在车架总成装配完毕后,利用φ11mm的定位工艺孔控制模板在车架长度方向的移动,利用丝杠对中钻模板可以保证模板与车架两者的对称中心重合,孔位精度可达到±0.5mm,保证了后桥装配的可互换性(见图1)。对于发动机支架、转向机支架及车身支架等关键孔进行重点质量把关。对于管线、管夹等用孔,则一次性冲出,提高生产效率。
2.由于模具冲孔,辅助时间和冲压时间相对固定,无论纵梁长短,冲孔时间不变,故效率提升空间非常有限。对于钻孔和数控冲孔,则提升空间较大。例如我们把大梁片料的跌钻孔由单机作业改为多机作业(2~5台钻床),就是多台钻床同时钻孔,每台钻床负责纵梁上一段孔的加工。每次叠钻纵梁片料5片,模板由模具(或平面数控冲孔机)冲制完成。同时多机作业,减少了装夹、定位和换刀等辅助时间,既保证了精度,又大大提高了钻孔加工效率(见图2)。
3.平面数控冲孔机一般由上料、坯料定位、进料辊道、送料机械手、冲孔压力机、出料辊道及下料等部分组成。根据模具的布置,国内外平面数控冲孔机主要有4种形式。
(1)回转模库和回转下模式 其模具为环形排列,上模放在回转模库上,下模装在回转模架上。变换模位是通过上模库与下模架同步回转和机械手取模、放模和压力机(或主油缸)横向移动的合成运动来完成。由于模架回转惯量较大(半径较大),加之机械手往复移动,以及定位销定位等因素,其换模时间很长,影响生产率。
(2)回转冲模式 其模具为环形排列,上下模分别装在上下回转模架上,可同步回转。其变换模位是通过上下模架同步回转和压力机(或主油缸)横向移动的合成运动来完成。由于模架回转的惯量大(半径大),加之定位销定位等因素,其换模时间较长,影响生产率。
(3)直线排列上下模一体式模具为直线排列,各上下模分别装在固定的上下模架上,模架直线运动。变换模位是通过模架移动和压力机(或主油缸)横向移动的合成运动来完成。由于模架的行程较长,其换模时间略长,会影响一些生产率。
(4)直线排列上下冲模固定式 模具为直线排列,上下模分别固定在压力机的滑块和工作台上。变换模位是通过上模上方的气动垫块进出和压力机横向移动的合成运动来完成。由于气动垫块进出的时间极短,与压力机的横向移动时间重合,其换模时间最短,生产率最高。由此可见,辅助换模(冲头)时间不同,冲孔加工的效率也不同(见表2)。 回转模库和下模的布置方式仍然是目前国内的主流设备(见图3)。
4.提高三面数控冲孔机效率的有效途径,主要是充分利用整个纵梁的长度空间,根据不同孔径的数量分布情况,采用多台压力机同时冲孔。三面数控冲的腹面和翼面冲孔压力机均为开式压力机,均为直线排列上下模固定式结构。三面数控冲的多台压力机布置形式主要有4种。A型由1台腹面冲孔压力机和两台翼面冲孔压力机组成,B型由由两台分别冲腹面大小孔压力机和两台翼面冲孔压力机组成,C型由由1台腹面冲孔压力机(冲小孔和大孔)和一台纵向可移动的腹面冲小孔压力机和两台翼面冲孔压力机组成,D型由两台分别冲腹面大小孔压力机、1台可纵向移动的腹面冲小孔压力机和两台翼面冲孔压力机组成。由表3可知,C型和D型的效率高,将是大型规模化车架生产企业引进设备的主要方向。
孔的质量检测
1. 纵梁孔的表面粗糙度检测
采用目测及表面粗糙度仪比对检测,可以对孔加工的表面粗糙度进行较好的判定。对于模具冲孔和数控冲孔来说,一般孔的表面粗糙度属于免检项目,而对于钻孔则应该重点检测。
2. 孔的尺寸及形位公差检测
一般孔径按照自由尺寸公差IT14进行检测,为此我们专门制作了一套台阶式的测棒,用来检测φ9~21mm常用孔的孔径、圆柱度等,效果较好。
对于有装配关系的孔组位置度检测,通常有4种方法:一是钳工划线检查,比如平面冲孔或者三面冲孔的第一根纵梁,这种方法效率低、精度差;二是利用专门的检测样板对关键孔进行专检;三是利用数控设备自带的光电装置进行检测;四是利用三坐标机专检,特点是辅助时间长,但是精度高,常作为质量控制及争议仲裁的重要手段。
声明:本网站所收集的部分公开资料来源于互联网,转载的目的在于传递更多信息及用于网络分享,并不代表本站赞同其观点和对其真实性负责,也不构成任何其他建议。本站部分作品是由网友自主投稿和发布、编辑整理上传,对此类作品本站仅提供交流平台,不为其版权负责。如果您发现网站上所用视频、图片、文字如涉及作品版权问题,请第一时间告知,我们将根据您提供的证明材料确认版权并按国家标准支付稿酬或立即删除内容,以保证您的权益!联系电话:010-58612588 或 Email:editor@mmsonline.com.cn。
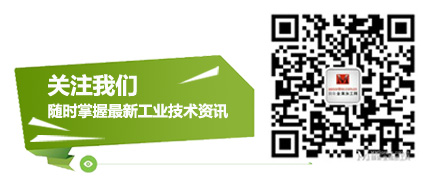
- 暂无反馈