蔡司讲堂 | 看不见的X射线 看得见的工件隐私
1895年,伦琴率先发现X射线并于1901年被授予首次诺贝尔物理学奖 。作为20世纪最伟大的发现之一,不仅为开创医疗影像技术铺平了道路,更为此后CT技术的发展奠定了基础。
前不久,Frost & Sullivan咨询公司将“2015年全球在线CT系统市场产品领袖奖”授予来自德国的卡尔蔡司。以光学技术领先全球的蔡司一直专注于创新,其在在线计算机断层扫描(CT)上的卓越表现就是一个很好的例子。通过蔡司的CT系统,客户能在数秒之内对一个部件进行整体扫描,并轻松获取部件的全部三维数据。
CT系统在工业上的启用,令所见即所知的愿望成真。全新视角观察部件,确保可对其产品及生产工艺进行优化。在工业应用中,传统CT技术主要用于进行无损检测(NDT),确定工件内部是否存在缺陷。我们通常将具备可识别内部缺陷的工件视为次品,无关乎其缺陷程度。出于这个原因,即使CT系统存在一些实质性的测量误差,或者是在测量时存在显著的“偏离”,我们都是完全可以接受的。精确和可重复的测量需要特定的系统设计。举例来说,即使是一个能够产生真实图像的便携式扫描器,但如果需要更准确的数据,同样需要结合一个合适的坐标测量机(CMM)。
如果空隙在工件外侧,通过目视就可以很容易的进行识别并评估。而内部空隙的处理则较为困难,用于识别这些空隙的技术主要包括二维射线检测或三维计算机断层扫描(3D CT)技术。
固体工件的隐私如何知晓
现在,只需短短90秒,就能对复杂如汽车发动机缸盖这样的工件进行彻底检测,对活塞零件的检测只需要30秒,而对那些塑料的医疗用品更是只需要几秒钟。但是,在不同的3D系统中,其提供的检测精确度、易用性,以及考虑到重新校准和掌握需求时的实际信息传输量存在很大的变化。
高精度测量
理想化的检验流程可以是:
1. 100%检测铸件,并且速度要足够快,以保持生产流程的推进。
2. 检测流程是可重复、可重现且足够精确的,这样能够排除所有不合标准的工件,避免错误排除那些带有不影响性能孔洞的工件。
3. 实现上述目标的同时,无需频繁进行校准或后期处理。
4. 提供扫描结果的三维显示,实现有意义的分析。
5. 能够对工件进行分析,对其好坏进行分类。
无损检测系统不走“高精度”路线的原因
最初设计针对无损检测的测量系统的初衷是用在某些涉及紧密公差测量的领域,这些测量系统能够弥补原先系统的不足。
首先,大多数系统都允许对X射线源、试样及X射线探测器的位置进行宽幅调整,以适应不同尺寸的试样。但这种灵活性也导致高昂的成本。
第一,自由度的增加会产生显著的错误来源,同时降低系统的精度,而这往往都是不必要的。在许多情况下,这种“灵活性”真正的好处是让制造商重新调整现有系统,同时在制造这类系统时发挥规模优势。事实是,这些声称“无所不能”的测量系统往往会让你在测量精确度上付出代价。
另一个潜在的错误来源是测试期间转动工件的旋转平台。这是一个在测试期间必须移动的组件,但其运动的稳定性和可预测性取决于平台转动的轴承技术。高精度旋转轴的成本较高,但在测量期间能提供更准确的定位。由单个组件、可调节组件和低级转轴引起的运动量可能很小,但这些量累计之后则会导致对工件和缺陷测量的显著误差。因此测量中并不需要发生很严重的错误就可能导致将一个质量良好的工件送到废料堆中,尤其是当系统“出于安全起见”而夸大了测量误差。
温度变化也可能会影响精度。即使只是几度的变化也可能显著影响结果,因为CT系统的组件受温度影响发生了扩张或收缩的现象。如果检测目标只是通过无损检测简单的发现工件内部的缺陷,以确认没有量化问题,那么由于温度变化而产生的误差则不会影响结果。但是孔洞一般都非常小,要对其进行测量必须要考虑温度的影响。
虽然系统可以定期进行重新校准以排除温度变化的影响,但是重新校准就必须停止系统运行并降低产量。而那些致力于最小化或消除温度变化影响的系统成本较高,但这些系统在运行中可以带来更高的成本效益,同时能够产生可靠且可重复的测量结果。
(蔡司)
声明:本网站所收集的部分公开资料来源于互联网,转载的目的在于传递更多信息及用于网络分享,并不代表本站赞同其观点和对其真实性负责,也不构成任何其他建议。本站部分作品是由网友自主投稿和发布、编辑整理上传,对此类作品本站仅提供交流平台,不为其版权负责。如果您发现网站上所用视频、图片、文字如涉及作品版权问题,请第一时间告知,我们将根据您提供的证明材料确认版权并按国家标准支付稿酬或立即删除内容,以保证您的权益!联系电话:010-58612588 或 Email:editor@mmsonline.com.cn。
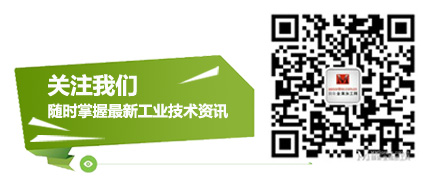
- 暂无反馈