用瑞士型卧式车床实现汽车零部件小批量加工
用一台配备B轴铣削主轴和大容量刀库的瑞士型车床,Magnus公司更有效地完成了工艺复杂的小批量业务委托,也就是那种之前很多加工厂甚至不会投标争取的业务。
Magnus公司的生产车间位于纽约州的Phelps,其生产区呈现一种整洁有序、环境控制良好的面貌。那里的加工设备也处于顶尖水平并维护良好,具备0.00001in(1in=25.4mm,下同)的编程分辨率、玻璃分划尺、主轴冷却器和高压冷却液系统。这家加工厂甚至还在其原型制造部配备了一对5轴机床。通过这种配置,如果某个原型产品制造项目进入了投产阶段,工厂就能及时制订有效的加工工艺,包括编程、刀具配置和工件夹装。
所有这些能力再配以技术纯熟的老练员工,使得这家工厂能够承接复杂的加工,这些业务经常要求十分精密的加工精度,并且是来自航空、医疗、光学和光子行业的客户。但令人同样印象深刻的是Magnus公司对采用新型加工技术和设备无止境的渴望。
Magnus公司所购入的瑞士型卧式车床并不是入门级车床,这台车床拥有可观的1.5in棒料加工能力和12ft(1ft=304.8mm,下同)棒料进给能力,并配备了一个B轴铣削主轴,还有可容纳60把刀具的自动刀库(ATC)、1000psi的高压冷却液输送系统,以及刀具监测和自适应控制系统。
Magnus业务发展部部长Don Miller解释说,做出这笔投资的目的是让工厂能够更有效地车削和铣削加工小批量复杂长型部件,否则这种小批量业务会由于需要多次夹装而不值得开展。在这方面具有特别宝贵价值的就是B轴铣削主轴和大容量刀库。
在使用B轴铣削主轴时,这台瑞士型车床实质上作为一台5轴车铣床,并额外配备滑动式主轴箱。滑动式主轴箱让这台车床能够有效车削小直径长工件,而B轴铣削主轴能以各个不同的角度接近车床主轴或副主轴上的工件。这样就有可能一次性完成加工,避免二次加工。此外,这台车床可容纳76把刀具的刀具库(B轴主轴ATC内可容纳60把,转台内可容纳16把),可以一次性装载多项加工所需的刀具,带来了减少夹装次数、缩短停机时间和提高整体生产率的效益。
Miller先生表示,这台瑞士型车床非常良好地补足了该工厂其他多功能加工设备的短板。事实上,Magnus公司添购这台设备代表了一种日益增长的趋势,非螺杆机床类加工厂正认识到瑞士型车床所具备的优势,这种车床能够整体加工长尺寸、形状复杂的工件以及接近棱柱状的工件,而这种工件要求进行大量的铣削和钻孔作业。
积极采纳先进技术
Magnus公司创建于1982年,目前是Floturn公司的子公司,拥有相当全面的加工能力,包括5轴机床、双主轴/双转台车床、卧式加工中心、立式加工中心以及集成化托盘系统,还拥有电火花线割加工设备。Magnus公司既能加工绝大多数常见材料,也能加工各种特异材料,如耐高温合金、钛、不锈钢、锰、铍铜和铝铍材料,典型加工批次量不超过300件。
在2009年,客户更为频繁地要求这家公司加工小批量的相对较长的小直径部件,这些部件要求进行车削和铣削或钻孔加工。作为Magnus公司新设备采购协调负责人的Miller先生讲到,公司承接了其中一些委托,采用铣床执行必需的二次加工。但是,由于这些委托需要执行耗时较长的多次夹装,所以与其他委托业务相比,吸引力不大。这种状况促使公司寻求更适合的设备来加工这些部件,而瑞士型车床似乎是理想之选。
在谨慎考虑了一定数量的各种瑞士型机床品牌和机型后,Magnus公司决定选用Tsugami TMU1车床。这款车床通过REM Sales公司在美国销售,提供了Magnus公司所需各项特色的最完美组合。与其他所有瑞士型车床类似,TMU1配备了滑动主轴箱。打磨后的棒料放置在导向套筒内,穿过主轴箱进行进给,而不是由刀具执行进给运动。这意味着,无论工件有多长,外圆车削刀具都在靠近导向套筒(即支撑点)处切削坯料。在刀具运动的同时,车床进给工件,从主轴处送出并经过刀具,部件实质上分段完成加工。
这样就使得瑞士型数控加工中心能够特别有效地应用于长细型车削部件的加工,而如果这种部件在传统车床上由顶尖进行支撑的话就会出现弯曲变形。
就瑞士型卧式机床来说,9轴型的TMUI机床体积相当可观,能够容纳直径1.5in的棒料。其主轴和后轴提供了6000r/min、11/7.5kW的输出功率和完备的C轴加工能力。主轴的特色体现是原始设备制造(OEM)的“双重构造”设计方案,能够在靠近导向套筒处实现载荷更大的车削。这款机床配备了可容纳16把刀具的转台以备主轴使用。
当然,这款机床标志性的要素就是其B轴铣削主轴。其异于传统瑞士型机床设计方案之处在于,它采用了集群式刀具设计,刀具相对于部件的方向固定,无论其垂直于棒料的表面还是直径。其5.5ps(1PS=0.74kW,下同)、10000r/min的主轴提供了210°的B轴旋转范围(±105°),并安装在立柱上,还提供了线性的X、Y和Z轴运动能力。B轴旋转运动能够实现0.001°的步进,让B轴能够以各种不同的角度接近夹持在主轴或副主轴上的工件。因此,B轴可以执行各种作业,例如各种并非常见的表面夹角进行钻孔,并可执行3+2轴和全5轴仿形轮廓加工。这种能力可理想地应用于存在倾斜表面形状、仿形轮廓表面、表面形状偏离中心线和几何定位公差严谨的工件。副主轴还可以用于实施后退式加工,所以可对工件进行整体加工。这就是说,B轴主轴还可以在“静止”模式下发挥功能,与转台联手实现小齿轮车削加工。
B轴主轴配有KM40锥体并由一个60刀具位的ATC来提供支持(该机床的标准配置为30刀具位)。TMU1车床编程员兼操作员Will Breen说,增大刀具库容量对于最大程度减少夹装次数有着重要意义,因为可以一次性装载多次加工作业所需要的刀具。这样就不需要每一次加工作业都执行一次夹装,而可以只用一次夹装例行程序来支持多次作业,最大程度减少了机床的作业耗时。通过Parlec刀具预设置器可以轻松地在设置过程中输入刀具偏差量,从而无需精确校准刀具。尽管这款车床拥有大刀具容量,但Breen先生仍说自己还在尝试减少所用刀具的数量。他采用了将刀具位专门指定用于特定刀具/作业(粗加工、精加工、挖槽等)的方式实现了这点。
精益求精
Breen先生对Magnus公司所使用的传统车削中心及其定制Mazak双转台/双主轴车削中心有使用经验,但在被选中成为TMU1车床的编程员和操作员之前,他对瑞士型机床毫无经验。他说,由于滑动式主轴箱以分段方式完成整个工件的加工,所以早期遇到的挑战就是,要在编制部件加工程序之前制订好部件的编程策略。对于有些委托业务来说,Breen先生会使用PartMaker CAD/CAM软件。目前,他一直在积累在TMU1车床上运行过经过验证的程序库,尽管他可以选择在类似作业现有程序基础上进行修改,但他实质上通过剪贴程序代码编制了新程序。
通过对自己所负责的这台车床几年来的经验累积,Breen经常能够找到一些方法来改善重复作业的部件加工程序,并不断地在指挥多次作业同时运行方面取得良好成绩。他还认识到经常使用Caron Engineering公司生产的刀具监测自适应控制(TMAC)系统所带来的宝贵价值。这套TMAC系统采用多种传感器来测量主轴在切削期间输出的功率,以测定刀具是否已经磨损或断裂。安装在TMU1车床上的一台显示仪提供了实时数据查看功能并且为所有监测到的事件提供了时间标记。其自适应控制能力可自动调节每把刀具的进给速度,在刀具磨损的同时保持刀具在切削过程中的输出功率恒定不变。通过这种对不同切削条件的调节适应,系统让刀具可以在其最优功率水平下执行切削。
至目前为止,Breen先生已经在瑞士型车床的学习道路上取得长足的进步,并开始培训Magnus公司的其他员工来操作TMU1。这项培训工作很重要,因为Magnus公司已经认识到瑞士型车床所带来的良好效益,并正计划在适当时机添购这种车床。
(文章来源:互联网)
声明:本网站所收集的部分公开资料来源于互联网,转载的目的在于传递更多信息及用于网络分享,并不代表本站赞同其观点和对其真实性负责,也不构成任何其他建议。本站部分作品是由网友自主投稿和发布、编辑整理上传,对此类作品本站仅提供交流平台,不为其版权负责。如果您发现网站上所用视频、图片、文字如涉及作品版权问题,请第一时间告知,我们将根据您提供的证明材料确认版权并按国家标准支付稿酬或立即删除内容,以保证您的权益!联系电话:010-58612588 或 Email:editor@mmsonline.com.cn。
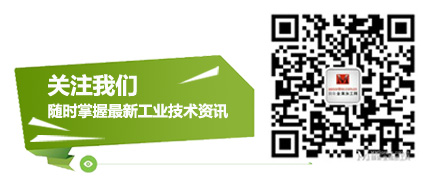
- 暂无反馈