数学模型可以有效地计算出刀具寿命
在金属切削加工中,刀具会使工件材料变形,并以切屑形式将其剪切下来。 变形过程需要大量的力,刀具会承受多种机械、热、化学和摩擦负荷。一段时间过后,这些负荷最终会导致刀具由于磨损过于严重而必须更换。通过恰当地预测刀具寿命,制造商可以根据刀具磨损情况精确地规划金属加工工艺,并因此控制成本,以及避免由于意外的刀具行为或不可接受的工件质量而造成意外停机。
于是,一个多世纪以来,科学家和工程师们建立和测试了数学模型并考虑到刀具所受到的力,以估算预期的刀具寿命。很多这样的模型都重点关注特定刀具在某些材料和加工中的性能,并通过简单的公式和重复性测试获得有效的刀具磨损情况预测。但可以应用于多种工件材料和刀具的广义模型更适合工业应用。这些模型考虑到了多种刀具磨损因素,因此它们的数学复杂性也随着所考虑因素的数量而相应增大 - 因素越多,计算越复杂。
尽管通过手写数学公式和手工计算即可对简单的刀具寿命等式进行求解,但仍然需要在生产环境中花费适量的时间,利用当今的计算机分析来对复杂模型的等式进行求解。数字计算非常可靠,但制造商应当对结果保持批判态度,尤其是在加工高级工件材料和使用极端加工参数时。整体而言,刀具寿命模型的发展过程将学术理论和实际应用紧密结合在了一起。
Archard 模型
对磨损过程进行的建模不仅仅局限在金属切削应用领域。在 20 世纪 50 年代,英国工程师 John F. Archard 开发出了一个经验模型,用于根据表面粗糙度的变化来计算滑动表面的磨蚀性磨损速度。他的等式是:
其中的 Q 代表磨损速度,K 代表恒定磨损系数,W 代表总计正常负载,L 代表表面的滑动距离,H 代表两个表面中更柔软表面的硬度。此模型主要认为,由于磨蚀性磨损而损失的材料数量与摩擦力成正比。
但Archard 模型并未说明刀具磨损现象,而是预测了随时间变化的磨损渐变速度。此模型涉及到两个表面互相干扰的速度、机械负载、表面强度、材料属性和磨损系数的影响。
但应当指出,Archard 模型不是专门为金属加工领域常见的高速应用而开发的,它也并未涉及到温度对磨损过程的影响。在金属切削所产生的 900˚C 高温条件下,表面强度和磨损系数都会发生变化。这样,Archard 模型本身就无法充分说明金属切削领域的刀具寿命。
Taylor 模型
在 20 世纪初期,美国工程师 F.W. Taylor 开发出了一个刀具寿命模型,此模型包含了与金属切削相关的因素。Taylor 发现,增大切削深度只对刀具寿命产生极小的影响,增大进给量所产生的影响稍大一些,而提高切削速度对刀具寿命产生的影响最大。下图显示了提高速度(蓝色的 vC)、增大进给量(灰色的 f)和增大切削深度(黑色的 ap)之后所产生的刀具磨损。
这促使 Taylor 开发出了一个重点关注各种切削速度所产生影响的模型。Taylor 基本模型的等式是 vc* Tm = CT,其中的 vC 代表切削速度,T 代表刀具寿命,m 和 CT 是常量,CT 代表影响一分钟刀具寿命的切削速度。
Taylor 还发现,刀具通常在开始运行时加速磨损,并在第二阶段趋于稳定但慢慢增大,最终进入快速磨损的第三阶段(也就是最终阶段),直到刀具寿命结束。他设计的模型展示了第二阶段与第三阶段之间的时间长度。
因此,Taylor 模型不适用于较低的切削速度,当切削速度较低时,工件材料会粘附和积聚在切削刃上并影响切削质量和损坏刀具。此外,在此模型范围外的高切削速度足以产生化学磨损。低速和高速磨损模式具有一个共同的特点,那就是不可预测性 - 粘附机制和化学机制会或快或慢地产生磨损。Taylor 模型立足于刀具寿命的第二阶段,也就是稳定而且可预测的磨蚀性磨损。
最初的 Taylor 模型关注切削速度的影响,在切削深度和进给量保持不变的情况下有效。确定了切削深度和进给量之后,可以控制速度以改变刀具寿命。
更多的实验催生出了一个扩展的 Taylor 刀具寿命模型等式,该等式包含了更多的变量,因此也变得更加复杂:
其中的 T= 以分钟为单位的刀具寿命,vc 代表切削速度,h 代表切屑厚度,b 代表切屑宽度。该等式还包含了一个表示刀具前角的变量以及一些适用于各种工件材料的常量。抛开其他因素不谈,此模型在一次更改一种切削条件时最准确。同时更改多种条件可能会产生不一致的结果。
最初的 Taylor 模型也无法充分说明切削刀具与工件之间的几何关系。可以让切削刃从直角方向(垂直于进给方向)或斜向(以相对于进给方向的前角)切削工件。此外,当切削刃的拐角不参与切削时,切削刃将被视为“自由”切削,当刀具的拐角参与工件的切削时,切削刃被视为“非自由”切削。现代金属切削应用中很少涉及自由直角切削或自由斜向切削,因此它们很少被提及。Taylor 的扩展等式增加了一个切削刃前角变量,但不允许刀具的拐角参与切削。
尽管是后见之明,但从当今金属切削技术水平和复杂程度的角度来看,Taylor 模型无疑存在着一些缺陷。即便如此,在其悠久的历史中,Taylor 模型依然为刀具寿命预测打下了坚实的基础,在某些条件下仍然能够提供有效的刀具寿命数据。
切屑厚度的角色
随着工程师们对刀具寿命模型不断进行开发和研究,一个事实变得明显起来,那就是所产生的切屑厚度与刀具寿命密切相关。切屑厚度是在垂直于切削刃的方向和垂直于切削方向的平面中测量出的切削深度和进给量之间的一个函数。如果切削刃的角度是 90˚(在美国是 0˚ 主偏角),则切削深度和切屑宽度相同,进给量和切屑厚度也相同。
刀具拐角参与工件切削的程度增加了另一个用于确定切屑厚度的变量。瑞典工程师 Ragnar Woxén 于 20 世纪 60 年代开发出了一种用于说明刀具刀尖圆弧吃刀程度的方法。他提出了一个用于计算车削加工中的等效切屑厚度的公式,该公式可计算出刀具刀尖的理论切屑厚度。这一成果非常透彻地分析了刀尖圆弧,并能够利用矩形来说明切屑面积。借助这一描述,模型可以反映刀具圆形刀尖圆弧的吃刀程度。
Colding 模型
瑞典教授 Bertil Colding 于 20 世纪 50 年代开发的一个刀具寿命模型,此模型说明了刀具寿命、切削速度与等效切屑厚度之间的关系,并考虑到切削工艺中的其他因素。这些因素包括刀具材料和形状、温度以及工件可加工性。使用此模型和它复杂的等式可以准确地计算多种切削条件同时变化时所产生的后果。
Colding 发现,更改等效切屑厚度(进给量)会改变切削速度与刀具寿命之间的关系。如果增大等效切屑厚度,则必须降低切削速度以保持同样长的刀具寿命。切屑厚度越大,更改切削速度后所产生的影响也越大。
另一方面,如果减小等效切屑厚度,刀具寿命将会延长,提高刀具速度后所产生的影响也会下降。进给量、切削深度、主偏角和刀尖圆弧的很多组合都可以取得相同的等效切屑厚度值。如果在恒定的切削速度下保持恒定的等效切屑厚度,则无论切削深度、进给量和主偏角如何变化,刀具寿命都将保持不变。
左图显示了在 Taylor 模型的稳定磨蚀性磨损条件下进行加工时,等效切屑厚度(由 he 表示)的变化与刀具寿命 (T) 和切削速度 (vc) 之间的关系。右图中也显示了这一直线关系。但由于 Colding 模型考虑到了其他磨损因素,因此也用另外一条曲线显示了此模型的预测结果。
当加工可产生稳定磨蚀性磨损的常规材料(例如钢材)时,该曲线得出的估算值没有太大价值。但在加工超级合金和钛合金等容易应变硬化的材料时,此模型在 Taylor 范围之外的预测能力就变得非常重要。这是因为当等效切屑厚度较小时,刀具会切削应变硬化的材料,因此会导致切削温度上升并需要降低切削速度以降低温度和保持刀具寿命。
但该曲线表明,在局部的切削范围内,更大切屑厚度与更高切削速度的组合或者更高生产率的切削条件可以延长刀具寿命。20 世纪 60 年代和 70 年代诞生了同时增大两种切削参数和提高金属切除率这一概念,这一突破性理念与当时的经验和直觉恰好相反。
通过开发包含金属切削工艺多种因素的模型(例如 Colding 模型)以及 Taylor 和 Archard 模型的概念,将理论和实际紧密结合在了一起。
实际应用日益复杂的刀具寿命模型时,需要对它们采用的多种因素执行计算机分析。在短时间内,可以手动计算出专门用于特定刀具、工件材料和切削条件的简单模型的结果。在某些情况下(例如手工计算时),基本 Taylor 模型可以在相对较短的时间内得出结果。
但即使是扩展的 Taylor 模型也可能需要大量的手工计算时间,因此在生产环境中对 Colding 等式中的因素进行手工计算是不切实际的。为了充分利用这些高级模型的预测能力,制造商们应使用计算机的计算程序(请参阅关于山高的 Suggest 的附注)。这些程序可以在几秒钟甚至更短的时间内对复杂等式进行求解并提供有用的加工指导。不过,电子计算辅助工具依然要求机械师以审慎的态度进行思考,并将结果与自己在车间实际工作中获得的常识和经验进行比较。
结论
最后,刀具寿命建模并不是一种纯学术追求;它可以帮助制造商提高生产率和控制成本。制造业重点考虑的是需要花费多少时间和成本才能生产出特定数量的合格工件。了解在需要更换刀具之前刀具能够准确、高效地切削多长时间非常重要。工艺可靠性以及对刀具成本和停机时间进行的控制取决于是否能够准确地预测刀具寿命。模型还允许更改工艺以便最大限度提高速度、质量或可靠性。切削刀具寿命模型的进一步发展能够帮助制造商精密调整自己的工艺并实现自己的生产目标。
附注
计算机辅助计算
在生产环境中,所有的机床操作员都希望知道切削刀具在出现磨损或失效之前还能坚持多久。但与此同时,他们还必须在刀具使用寿命内充分地应用刀具。刀具寿命建模已经从简单地手工记录个别运算的结果发展为运用复杂的模型并以数学方式纳入尽可能多的切削工艺变量。
少数几个能够快速完成的手工计算方式基本上能够得出有价值的刀具寿命估算值。模型越复杂,所需的计算和时间就越多。最好的模型能够提供与现实紧密契合的刀具寿命预测。但如果在实施复杂模型时进行计算所花费的时间不少于加工本身所花费的时间,它的经济效益就值得商榷了。因此,可以使用计算机的计算程序,它们能够快速和绝对准确地处理高级切削刀具寿命模型所涉及到的因素。
其中一个示例是山高提供的 Suggest 在线资源。作为山高 My Pages 数字站点中的一个 Portlet,Suggest 是一款免费的应用程序,适用于 iOS® 或 Android® 平台的移动设备和具有网络浏览器的计算机。
Suggest 利用山高 80 多年来积累的金属加工经验为新的作业提供切削刀具建议或为重复性项目提供刀具选择方案。这款应用程序汇集了数千种切削刀具产品和应用程序的综合数据,可以根据用户的输入提供完整的刀具建议。
Suggest 不仅仅是一个在线目录,它还是一款先进的产品选择器,可以快速找到用于在要求公差范围内加工零件的刀具和一系列工序。Suggest 可以根据极少的数据提供建议。不过,用户输入的信息越多,所提供的建议就越贴切。每个数据输入字段中的默认值让具有各种金属加工技能水平的用户都能够得心应手。用户可以随时调整自己输入的数据,并过滤、排序和比较信息以便精密调整建议。所有刀具建议都可以保存下来并以电子方式共享或者打印,以便于分发。
全面的资源有助于制定工艺规划,而且便于为特定的作业找到高效且经济实惠的刀具和切削策略。应用成熟的技术能力和和工艺规划技能,可以大大缩短整体的工艺规划时间。
山高总部设在瑞典法格斯塔市,在超过 75 个国家/地区设有办事处,是为铣削、车削、孔加工和螺纹加工领域提供全面金属切削解决方案的全球最大供应商之一。另外,80 多年来,公司一直与各行各业的制造商密切合作,提供他们所需的刀具、工艺和服务,帮助他们获得最高的生产率和最大的利润率。如需了解详细信息,请联系当地的山高代表或访问 www.secotools.com。
(山高刀具集团技术培训经理 Patrick de Vos)
声明:本网站所收集的部分公开资料来源于互联网,转载的目的在于传递更多信息及用于网络分享,并不代表本站赞同其观点和对其真实性负责,也不构成任何其他建议。本站部分作品是由网友自主投稿和发布、编辑整理上传,对此类作品本站仅提供交流平台,不为其版权负责。如果您发现网站上所用视频、图片、文字如涉及作品版权问题,请第一时间告知,我们将根据您提供的证明材料确认版权并按国家标准支付稿酬或立即删除内容,以保证您的权益!联系电话:010-58612588 或 Email:editor@mmsonline.com.cn。
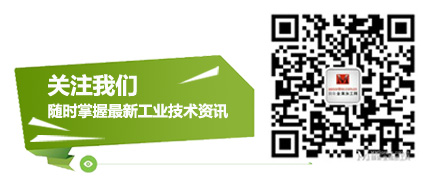
- 暂无反馈