电加工技术在航天零件加工中的应用
【编者按】电加工技术不仅实现了硬、脆、韧、粘等难加工材料的加工,而且实现了高效低成本的加工。目前, 我所的电加工技术主要应用在过滤器中液滤片、壳体、分流板,阀体中导向簧片、弹簧,微小孔以及异形孔零件的加工。电加工技术随着现代制造业的发展,加工精度和效率不断提高,航天产品中许多高精度、结构复杂的零件采用传统的金属切削加工效率低、合格率低,很难适应航天任务的需求,但是,如果通过改进加工工艺流程,采用电加工技术很多问题就迎刃而解了
在航天产品零件加工中有许多难加工材料,如钛合金、高温耐热材料、不锈钢和硬质合金等,这些材料用传统的金属切削机床加工,不仅效率低而且刀具费用昂贵,加工成本极高,有的材料甚至根本无法加工。还有许多零件形状复杂,如窄缝、窄槽、空间位置复杂刀具无法完成的加工部位,以及微小孔等采用传统的机械加工方法无能为力。以上这些成为航天零件加工中的“瓶颈”。
电加工技术不仅实现了硬、脆、韧、粘等难加工材料的加工,而且实现了高效低成本的加工。
目前, 我所的电加工技术主要应用在过滤器中液滤片、壳体、分流板,阀体中导向簧片、弹簧,微小孔以及异形孔零件的加工。电加工技术随着现代制造业的发展,加工精度和效率不断提高,航天产品中许多高精度、结构复杂的零件采用传统的金属切削加工效率低、合格率低,很难适应航天任务的需求,但是,如果通过改进加工工艺流程,采用电加工技术很多问题就迎刃而解了。下面就通过几个典型案例来探讨电加工技术在提高零件精度、表面质量以及加工效率等方面的优点。
1. 案例一:采用线切割技术解决细长孔加工难题
如图1所示的零件,材料为:
1Cr18Ni9Ti,外径10.5 mm,内孔直径,总长23.5 mm。根据设计要求,内孔直径
,尺寸公差必须满足图样要求。因此内孔直径
成为该零件加工的难点。
难点一:材料为难加工材料。
1Cr18Ni9Ti为奥氏体不锈钢,韧性大、热强度高、导热系数低、加工过程中硬化严重和散热困难等诸多因素,导致刀尖处切削温度高、极易产生积屑瘤,既加剧了刀具的磨损,又影响了零件表面粗糙度。
难点二:孔小、尺寸精度高。
内孔直径直接采用钻削方式根本无法达到图样尺寸精度要求,采用车削镗孔方式,由于孔的深径比大于5,镗刀直径必须小于4mm,强度低且刀尖磨损严重,同样无法确保尺寸精度和表面粗糙度。该孔一直采用车削加工,先用φ 3.8 mm的钻头钻孔,然后用铰刀铰孔,每次铰孔前均需要用新铰刀试铰,再手工磨制铰刀摸索切削参数。如此加工效率极低,每件加工耗时2 h左右,而且内孔加工容易出现锥度,合格率仅为30%左右,长期以来只能通过多投产来保数量。
为了确保零件加工满足图样设计要求,经过多次试验,将零件按照图样要求车外圆φ 10.5 mm和长度23.5 mm到尺寸,并确保尺寸一致性在0.02 mm内,内孔用φ2 mm钻头打通作为线切割的穿丝孔。然后,用夹具夹外圆找正,采用慢走丝线切割加工内孔。试验结果表明,采用慢走丝线切割的方法很好地保证了零件的加工尺寸精度以及尺寸的一致性。经过计量内孔直径为4.009 mm,内孔表面粗糙度值为0.825 mm,内孔直径一致性能控制在0.002 mm内。线切割时间为每件30 min,加工周期能缩短50%,合格率却能达到98%以上。因此,采用慢走丝加工既能保证内孔直径尺寸公差满足图样要求,提高零件加工合格率,又能提高零件加工效率。
2. 案例二:电火花成形解决零件走线槽毛刺问题
如图2所示零件是由两种不同材料焊接而成,其中中间两段有1.5 mm×3 mm和1.5 mm×3.5 mm的走线槽,φ 1.5 mm通孔走线孔,走线孔和走线槽的加工只能在分段单件粗加工之后进行,由于零件精车过程中毛刺翻到走线槽和孔内,长期以来走线槽和孔毛刺的去除都是由钳工手工用什锦锉刀倒角完成,由于中间两段之间的距离只有5 mm(见图2),施展锉刀空间狭小,导致在修锉去毛刺过程中把零件划伤(见图3、图4)。
以看出手工修锉走线槽和孔存在以下几方面的缺点:①修锉过程中零件表面质量不易控制,很容易造成零件表面划伤。②手工修锉去毛刺效率低下。③手工修锉走线槽倒角一致性不能保证。④手工去毛刺后容易引起二次毛刺。
针对零件的结构特点以及加工特点,提出采用电火花成形的加工方法去除零件1.5 mm×3 mm和1.5 mm×3.5 mm走线槽以及φ 1.5 mm走线孔边沿的毛刺。根据图5设计加工如图6所示成形电极。
通过工艺试验表明:针对零件1.5 mm×3 mm和1.5 mm×3.5 mm的走线槽以及φ 1.5 mm走线孔边沿的毛刺,采用电火花成形的加工方法进行加工去除具有如下几方面的优点:①零件去毛刺过程可控,且不会造成零件表面划伤。②大大减轻了劳动强度。③操作过程可控、省时高效,加工效率能提高50%以上。④能保证倒角加工的一致性,适合零件的批量化生产。采用电火花成形加工效果良好,其加工后效果如图7、图8所示。
如图9所示零件是太阳敏感器中承载光学头部的高精度重要零件, 2个梯形型通孔中间有一个50 mm×41 mm的矩形窗口。通过数铣其他所有形面均能达到设计图样要求,唯独中间50 mm×41 mm的矩形窗口只用T型刀能加工成如图10所示的形状。
按照工艺流程要求单独有一道工序在普通铣床上用特制的T型刀加工矩形窗口上下“残留”的尖角。如果采用普铣的加工方法,直接用T型刀仍无法加工,必须将特制的T型刀的刀柄先从梯形腔内穿过底部的接插件窗口(见图11),再将刀柄装到机床的主轴上。在加工的时候还必须确保T型刀的侧刃不能碰到侧面,加工1件就需要换装刀具至少2次。因此,加工效率不仅低,而且还很难保证图样尺寸要求。
为了满足设计图样要求,决定采用电火花成形技术加工矩形窗口, 设计如图1 2 所示尺寸为:(暂不可见),材料为紫铜的电火花成形电极。
通过试验表明,改用电火花成形加工方法完全可行且具有如下几方面优点:①找正方便、加工效率高。只需找正首件,基本不用重复找正,适于小批量生产。②加工成本低。采用的紫铜电极成本比合金刀具成本相比廉价,电极损耗小可重复使用。③尺寸一致性有保证,能提高零件合格率。减少零件加工对操作者技能水平的依赖,找正工件,只要参数设置合理,正确操作就能确保零件合格。
4. 结语
通过上述典型案例分析表明,随着电加工技术的快速发展,许多采用传统金属切削加工很难解决的问题,采用现代电加工技术能“迎刃而解”。实践说明电加工不但能提高零件的加工合格率、表面质量,而且还能提高加工效率,降低成本。因此,要不断创新、开拓思路,利用电加工技术优势结合先进的金属切削技术来制定高效、优质的加工方案,提高零件的加工精度和合格率,才能确保航天产品的高可靠性。
声明:本网站所收集的部分公开资料来源于互联网,转载的目的在于传递更多信息及用于网络分享,并不代表本站赞同其观点和对其真实性负责,也不构成任何其他建议。本站部分作品是由网友自主投稿和发布、编辑整理上传,对此类作品本站仅提供交流平台,不为其版权负责。如果您发现网站上所用视频、图片、文字如涉及作品版权问题,请第一时间告知,我们将根据您提供的证明材料确认版权并按国家标准支付稿酬或立即删除内容,以保证您的权益!联系电话:010-58612588 或 Email:editor@mmsonline.com.cn。
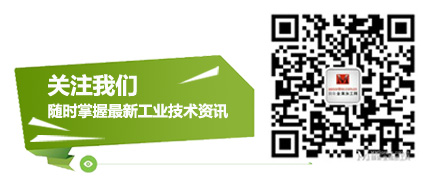
- 暂无反馈