全方位解读大型飞机设计及先进生产技术
【编者按】历经半个世纪的发展,我国飞机制造科研能力与世界先进水平依然还存在一定的差距,特别是飞机制造的关键技术有待突破,设计人才有断层,风险较大,资金短缺等严重等制约了行业的进一步发展和品质的提高。
飞机机体制造要经过工艺准备、工艺装备的制造、毛坯的制备、零件的加工、装配和检测诸过程。工艺准备工作即包括制造中的协调方法和协调路线的确定(见协调技术),工艺装备的设计等。飞机机体的主要材料是铝合金、钛合金、镁合金等,多以板材、型材和管材的形式由冶金工厂提供。飞机上还有大量锻件和铸件,如机身加强框,机翼翼梁和加强肋多用高强度铝合金和合金钢锻造毛坯,这些大型锻件要在300~700兆牛(3~7万吨力)的巨型水压机上锻压成形。
数字化三维设计
国内飞机制造企业经过长期的三维工艺设计与仿真、CAX/CAPP/MES系统集成等技术的研究,突破了基于模型的定义(MBD)、三维工艺设计可视化、三维装配过程仿真验证及优化、三维工作指令的创建、发放及浏览、多系统集成和业务流程优化等关键技术瓶颈,构建了体系完整的、能支撑装配、机加、钣金、冶金等各类工艺设计业务需求的三维化、系统化、集成化的企业级数字化工艺设计平台,实现了传统二维工艺设计制造体系向三维数字化工艺设计制造体系的成功转型。
飞机总体设计阶段,制造企业已开始进行工艺总方案设计,并通过采用基于成熟度的协同工艺审查的方法,依据设计成果,同步展开后续工艺策划工作,包括装配协调、零件制造技术、工艺分离面、部件装配图表等一系列工艺指导性文件的定义与编制。
在三维工艺模式下三维数据(模型等)替代了二维工程图纸和纸质工艺指令。三维工艺电子数据包(指令)成为生产现场工作的技术依据,通过工艺设计平台与生产管理系统的集成,将三维工艺指令等工艺数据信息发放到车间生产现场,并以三维的、动态的、交互式的定制界面展示、描述工艺过程,将生产工艺、人员、设备、工装及工具等资源信息有效集成,通过直观的界面显示产品的设计结构关系、工艺结构关系和几何模型,显示工艺仿真过程和工装使用定位方法,显示与仿真过程相应的操作说明等,使工人按指令进行操作,准确快速地查阅工艺过程中需要的信息,提高工作的准确性和效率。
三维工艺设计与仿真、基于轻量化模型的工艺过程可视化技术以及CAX/PDM/MES多系统集成技术的应用,有效地缩短产品研制周期,提高产品质量和生产效率,真正实现无二维图纸、无纸质工作指令的三维数字化集成制造,有效改善生产现场工作环境,使现场工人容易理解,减少了操作错误,提高了产品质量和生产效率。三维数字化工艺设计技术的深入应用必将推动我国飞机制造业的快速发展。
部件机械加工
飞机制造业中的工艺装备一般指机械加工夹具、装配型架、钣金模具、焊接夹具、测量检验夹具等。机械加工是获得飞机零件最终形状和精度的最主要方法,而机床夹具在保证飞机零件机械加工质量和工装加工效率方面起到重要作用。
飞机制造工艺装备的柔性化,一直是航空工业迫切希望解决的问题,因此得到了业界的广泛重视,并进行了大量的研究。柔性工装是基于产品数字量尺寸协调体系,采用可重组模块化结构的工装,自动化程度高。柔性工装系统目的是降低工装制造成本,缩短工装准备周期,同时大幅度提高生产率。
数控加工,尤其是数控铣削,是目前飞机结构件机械加工的主要方法。高速切削方法被普遍采用,如西飞大型复杂结构件均在西飞数控中心完成加工,结构件种类包括机翼大梁、壁板、梁间肋、框、大型支撑接头和对接接头等,这些结构件除具有槽腔多、壁厚薄、精度高等特点外,需要满足飞机变斜角理论曲面等飞机机翼结构件的通常特性以外,还具有零件轮廓尺寸大、槽腔深和基准平面轮廓度要求严等特性。
为了保证加工质量,每种零件均研制了专用夹具,基座为比较笨重的铸件,且定位精度不高。车间工具库乃至车间地面上堆满了各类夹具。从生产一种零件转换为生产另一种零件时,夹具重新组合转换时间在2h左右,严重影响了生产效率。飞机上的大型整体结构件,如整体蒙皮和壁板,目前仍部分采用大型模胎来进行铣削和切边。
飞机结构件的数控加工,应有柔性夹具作为加工质量和加工效率的保证。成组夹具和拼装夹具是实现柔性夹具的重要手段。计算机辅助夹具拼装规划、夹具生产流程管理是柔性夹具系统中的重要功能模块,必须得到较好的解决。柔性夹具一般应具备气动或液压夹紧功能,并与数控机床在结构和控制上集成一体。
激光焊接技术
大飞机机体制造应用了大量的焊接结构和焊接产品,焊接方法的选择主要集中在传统焊接技术,新型焊接技术也有了应用,尤其搅拌摩擦焊技术首次应用到飞机产品的制造上。
大飞机制造过程中,其中焊接技术是连接技术中很重要的部分,是制造技术的重要组成部分,同时也是飞机机体及发动机容器、管路和一些精密器件制造中不可缺少的技术,在现代生产和制造领域中,越来越多的产品采用各种焊接方法把不同材料、形状、结构和功能的零部件连接成一个复杂的整体,大大简化了构件整体加工的工序。
在大飞机机体研制中,有针对性的进行了大量激光焊接基础技术研究。对于不锈钢薄壁大型复杂结构部件,外形为双曲面复杂结构、尺寸大、焊缝长,采用手工TIG焊接工艺焊接此零件,焊接变形很大,焊缝外表面凸凹不平,缩沟较深,达不到设计对产品外观质量要求,而且内表面焊缝突出部分与之装配件产生干涉,装配时装配困难。
目前,国外将激光焊接技术应用于飞机大蒙皮的拼接、蒙皮与长桁、翼盒、机翼与内隔板和加强筋的焊接等,用激光焊接技术取代传统的铆钉进行铝合金飞机机身的制造达到减轻飞机机身重量,提高强度的目的。这也将是国内激光焊接技术在飞机制造应用的发展趋势。
数字化测量技术
随着科学技术与飞机数字化制造业的飞速发展,与其相适应的飞机数字化测量技术,以其高精度、高效率、高自动化等优势在飞机制造领域应用越来越广。一些光学三维大尺寸形貌检测技术日益成熟,其相关的仪器设备,如激光跟踪仪、机器视觉测量系统、iGPS、激光雷达扫描测量系统等已应用在国内外飞机制造工业的许多领域。
对于一些尺寸大、精度要求高的飞机或特殊机型飞行器,我国传统的测量手段已无法满足其要求,数字化测量技术是首选。尤其是采用多数字化测量系统组合的方式,不仅可以克服测量范围大与测量精度低的矛盾,还可获得更准确的测量结果,而且能够满足多功能的要求,成为飞机数字化制造中的关键支撑技术之一,大大提高了系统的可扩展性及应用范围,在提高飞机制造、装配质量和效率方面发挥了重要作用。
最近几年,国外基于模型定义技术在波音787机型上的成功应用使得设计制造一体化技术得到大的发展。波音、空客及福特等公司已经普遍采用基于数字化测量设备的产品进行三维测量与质量控制,建立了较完整的数字化测量技术体系,开发了相应的计算机辅助三维检测规划与测量数据分析系统,制定了相应的三维检测技术规范,显着提高了检测效率与质量。
现代先进飞机装配技术已经完全不同于传统的飞机装配技术,即不再使用传统的复杂型架来定位和夹紧零部件进行装配工作。而是充分吸收和利用了现代高新科技,如计算机、软件、激光跟踪定位、自动化控制等技术,发展成飞机无型架定位数字化装配技术,它们在飞机装配线中主要用来测量和定位各种工艺装备,或直接用来定位飞机的被装配构件,是飞机数字化装配系统的重要组成部分。
飞机制造业不仅关系到国防航空航天事业的发展,也是关系到国民经济建设的重要产业。同时,由于数字化测量技术在飞机制造业的广泛应用,已使其成为一个国家科技与工业发展水平高低的重要标志。因此,数字化测量技术已是推动飞机制造业向前发展的必要趋势。
数字化装配
将各零部件或组件按照设计技术要求进行组合、连接,形成高一级的装配件直至整机的过程,是整个飞机制造过程中最为关键的一环。飞机装配技术经历了从人工装配、半机械/半自动化装配到机械/自动化装配的发展历程,而目前得到各经济、军事发达国家高度重视的数字化装配技术,正成为现代飞机制造的科技制高点。
飞机数字化装配技术体系涉及了装配工艺规划、数字化柔性定位、装配制孔连接、自动控制、先进测量与检测以及系统集成控制等众多先进技术和装备,是机械、电子、控制、计算机等多学科交叉融合的高新技术集成。
随着计算机信息和网络技术的飞速发展,以美国波音、洛克希德·马丁公司和欧洲空客公司为代表的大型飞机公司均开始并采用飞机数字化装配技术。波音777、A380、JSF等新型军、民机的生产研制过程,充分体现了国外发达国家飞机制造过程中数字化装配技术的现状和发展趋势。
国内的飞机装配,虽然在局部上也采用了较为先进的技术,如采用CAD技术进行了包括建立型架标准件库和优化型架及参数设计,对工装、工具和产品的装配过程进行了三维仿真等,开始采用激光测量+数控驱动的定位方式,部分机型还采用了自动钻铆技术等,但总体上与发达国家相比还存在较大差距。
数字化装配技术代表了当今飞机制造的发展方向,涉及多学科如新材料、通信、机械、计算机、控制、电子等领域的综合研究与应用,其研究必须与工艺技术、实验技术、检测技术和现代管理等技术的研究相结合,以实现生产模式和方法的转变。
冷喷涂技术
热喷涂是国内外航空发动机公司使用最广泛的一种涂层制备技术,主要被用于耐磨、抗氧化、抗腐蚀、可磨耗封严、热障、防粘接、抗微振磨损、阻燃以及零件尺寸修复涂层的生产。物理气相沉积技术则用于发动机热端涡轮工作叶片和导向叶片部件的优质高温防护涂层制备。在国内,空心阴极电弧离子镀技术被用于MCrAlY和AlSiY抗氧化涂层的制造,电子束物理气相沉积技术用于热障涂层的生产。
发动机制造企业需搭建校企合作和聚智平台,结合涂层生产和外场问题,加强与科研院所沟通,以发挥其在涂层应力研究方面的优势,尽快开展X光衍射、逐层剥离、钻孔和曲率法等涂层残余应力测试技术工程应用研究,制定涂层残余应力测试行业标准,更好地保证我国在产和新型发动机涂层科研生产的顺利进行。
在制备涂层的材料熔融、沉积过程中,由于粉末颗粒本身的淬火应力、其对已沉积涂层的冲击应力以及涂层与基体材料在热-机械性能方面差异造成的失配应变和热梯度效应,某些情况下还有后续加工和服役环境的作用,都会使涂层内不可避免地出现或大或小的残余应力。
近年来发展起来并日趋成熟的冷喷涂(ColdSpraying)技术,可以实现低温状态下的涂层沉积,与热喷涂技术相比,冷喷涂过程对粉末粒子的结构几乎无热影响,金属材料沉积过程中的氧化可以忽略。冷喷涂是一种金属喷涂工艺,但是它不同于传统热喷涂(超速火焰喷涂,等离子喷涂,爆炸喷涂等传统热喷涂),它不需要将喷涂的金属粒子融化,所以喷涂基体表面产生的温度不会超过150摄氏度。
声明:本网站所收集的部分公开资料来源于互联网,转载的目的在于传递更多信息及用于网络分享,并不代表本站赞同其观点和对其真实性负责,也不构成任何其他建议。本站部分作品是由网友自主投稿和发布、编辑整理上传,对此类作品本站仅提供交流平台,不为其版权负责。如果您发现网站上所用视频、图片、文字如涉及作品版权问题,请第一时间告知,我们将根据您提供的证明材料确认版权并按国家标准支付稿酬或立即删除内容,以保证您的权益!联系电话:010-58612588 或 Email:editor@mmsonline.com.cn。
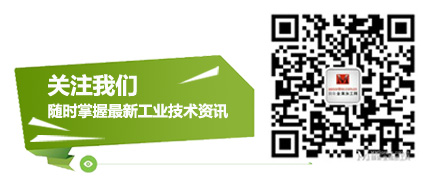
- 暂无反馈