Delcam OMV 在模具行业的应用
Delcam作为一家全球专业制造技术的软件公司,集近30年的先进技术经验推出了可控制加工制造过程中产品质量的解决方案,这便是OMV——"在机检测技术"。通过这套解决方案可以为模具企业节省大量生产成本、减少机器空闲时间、提高成品率,大大的提升了现有加工工序的生产力,全面提升了模具企业在加工制造过程中的质量控制能力。
从模具行业制造特点来看,具有以下几个方面:
1. 产量小,生产周期长;
2. 产品品质要求很高;
3. 成本高,返工较多;
4. 工件多为三维曲面加工;
5. 计算机直接产生加工程序;
6. 产品测量要求高。
而在模具加工过程中我们所关注的便是如何提高生产效率,这方面包含如何减少机床的停机时间;如何采用高速的加工技术;如何及时发现加工过程中存在的一些问题;如何优化刀路,减少加工时间,缩短交货周期等等。
目前模具加工中普遍存在的一些问题:
1. 手动设定工件坐标精度不高;
2. 手动设定工件坐标效率不高;
3. 无法在工件加工后及时测量工件,造成返工;
4. 返工过程中在机床与三坐标测量机之间往返搬运,并需要重新定位基准,造成机床生产率低下;
5. 易出现手动坐标系数据输入错误。
针对于这些问题,Delcam OMV——"在机检测技术"给出了全面细致的完美解决方案。
首先,对于Delcam OMV环境实施的搭建来说极为简单易行,通过模具企业现有的数控加工设备加装机床专用测头(Delcam对于市面机床测头全面支持),就使一台数控加工设备具备了三坐标检测能力,测头就像一把刀一样,平时放在刀库中,在加工前调出,便可自动测量工件相应位置、几何元素、自由曲面、尺寸公差及形位公差,并设定坐标原点,甚至工件即使放歪了,测头测量后,也可利用数控系统坐标系旋转功能自动找正,不需人为干涉。
我们再来看一下Delcam OMV的工作原理及实施流程,先将工件的工艺CAD数模导入到OMV软件中,然后在任意一台(支持企业DNC)装有OMV软件中的电脑中便可进行简便快捷并极具人性化的编程过程,编好测量测序后,通过软件内置的控制系统后处理文件将测量测序转化为机床控制系统识别的相应ISO代码,比如Siemens的G代码,Heidenhain的Q代码等等,然后通过232串口、U盘或DNC网络的方式传送给加工机床,机床便可自动换下刀头,调出测头进行测量,到此过程与我们通常的加工编程过程类似,不同之处在于测量完成后在机床控制器相应位置会产生一个文本文件,此文件只记录了所有测量单点的坐标值,需将此文件回传给OMV软件,通过一键式读取,便可生成完整的图文并茂的三坐标检测报告。
通过OMV的工作原理及实施流程我们可以看出,OMV与加工编程一样是以加工代码的形式进行工作,这样既省去了对机床本身进行任何硬件改造的过程,又可以将检测程序嵌入到任意关键工艺加工程序中,使得加工过程完成后自动进行测量,极大地提升了机床的加工工序的生产力,减少机床空闲时间,提高成品率。
对于OMV软件本身来说,多重的运行安全防护也是对于企业生产安全的最大保障,除了软件本身自带的机床仿真模型,我们还可以为企业定制开发相应的机床模型,这样便可在软件中模拟测量,OMV独具的全方位的碰撞干涉检验系统(已获专利保护)也极大地保障了机床实际运行时的安全。
OMV软件支持绝大多数的主流控制系统,比如Siemens、Heidenhain、Fanuc、Fidia、Haas、Okuma等等,此外对于国内自主研发的控制系统也同样支持,比如华中数控、广州数控等,对于极个别的数控系统Delcam也能通过其专业的技术开发团队予以支持。
随着五轴加工中心的应用越来越普及,五轴机床的优势显而易见:缩短加工时间,提高生产效率,减少设备投资。例如,斜面的加工更为快捷、方便。在三轴机器使用等高方式加工需要4个小时,但在五轴机床上仅需要30分钟即可完成,并且还可以得到更好的表面质量。 所以为了避免耗时的修模工作,使用Delcam OMV技术便使工件在机床上实现直接测量,并根据测量结果快速做出反应,指导加工改进,借此避免了更多的精度损失与时间浪费。 特别在合模方面,应用Delcam OMV在机检测技术将会大大缩短合模周期,过去工件的合模测试需要至少一周的时间,而应用Delcam OMV技术只需一天即可完成。
Delcam OMV目前在国内应用非常广泛,例如武汉重冶集团,长安汽车模具公司,珠海格力大金精密模具等等,在这些企业的关键部门均取得了重要的应用价值。二十世纪是生产力的世纪,二十一世纪是质量的世纪。Delcam公司关注用户核心工艺技术和知识积累,全面提供更多的先进加工技术,帮助客户进一步提高加工效率、降低生产成本,达到更好的加工结果,通过OMV过程质量控制,PowerINSPECT产品终检,可以大幅度减少模具调整时间,降低人员工作量以及技能要求,使用户产品品质得到飞越。Delcam公司愿意为提升中国科技及制造业能力,实现制造强国,贡献自己的力量!
声明:本网站所收集的部分公开资料来源于互联网,转载的目的在于传递更多信息及用于网络分享,并不代表本站赞同其观点和对其真实性负责,也不构成任何其他建议。本站部分作品是由网友自主投稿和发布、编辑整理上传,对此类作品本站仅提供交流平台,不为其版权负责。如果您发现网站上所用视频、图片、文字如涉及作品版权问题,请第一时间告知,我们将根据您提供的证明材料确认版权并按国家标准支付稿酬或立即删除内容,以保证您的权益!联系电话:010-58612588 或 Email:editor@mmsonline.com.cn。
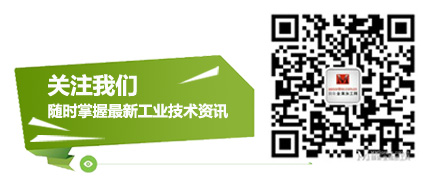
- 暂无反馈