线切割基础知识(二)
大厚度切割应怎么办?
大厚度的切割是比较困难的,可不是丝架能升多高,就能切多厚。受放电加工蚀除条件的制约,后到一定程度,加工就很不稳定,直至有电流无放电的短路发生。伴随着拉孤烧伤很快会断丝,在很不稳定的加工中,切割面也会形成条条沟槽,表面质量严重破破坏。切缝里充塞着极粘稠的蚀除物,甚至是近乎于粉状的碳黑及蚀物微粒。大厚度通常是指200mm以上的钢,至于电导率更高,导热系数更高或耐高温的其它材料还到不了200mm,如紫铜,硬质合金、纯钨、纯钼等,70mm厚就已非常困难了。
大厚度切割的主要矛盾有:
没有足够水的进入和交换,间隙内不能清除蚀物,不能恢复绝缘,也就无法形成放电。
间隙内的充塞物以电阻的形式分流了脉冲源的能量,使丝与工件间失去了足够的击穿电压和单个脉冲能量。
钼丝自身的载流量所限,不可能有更大的脉冲能量传递到间隙中去。
切缝中间部位排出蚀除物的路程太长,衰减了的火花放电已形不成足够的爆炸力,排污力。
材料原因,大厚度存在杂质和内应力的可能性就大为增强了。切缝的局部异常和形变机率也就大了。失去了切割冲击力,却增大了被短路的可能性。解决大厚度切割的主要矛盾,可采取如下措施:
加大单个脉冲的能量(单个脉冲的电压、电流、脉宽,这三者的乘积就是单个脉冲的能量)。,加大脉冲间隔,目的是钼丝载流量的平均值不增大的前题下,形成火花放电的能力,火花的爆炸力被增强。选用介电系数更高,恢复绝缘能力更强,流动性和排污解力更强的冷却液。大幅度提高脉冲电压,使放电间隙加大,水进入和排出也就比较容易了。事先作好被切材料的予处理,如以反复锻造的办法均匀组织,清除杂质,以退火和实效处理的办法清除材料的内应力。以去除大的余理的办法使材料应力得到充分释放。提高丝速,更平稳的运丝,使携水和抗据短路的能力增强。人为偏制折线进给或自动进二退一的进给方式,使间隙被有效扩大。
锥度机床的最大锥度是怎样确定的?
锥度机床锥度切割靠增加了U、V且与X、Y轴能联动,构成了上下两个平面的协调运动。U、V和X、Y分别决定了上下平面两个端点,工件的上下两个平面上的轨迹点就在这两个端点的联线上,这就是锥度切割的基本原理。而U、V的行程就决定了上端点可以偏摆的幅度。UV最大摆幅b和上下导轮的中心距的比值就决定了t角的大小,t即是切割的最大斜度。运算控制系统的相似形公式可以很准确的把工件上下平面的尺寸折算到UV,XY两平面上去,运算控制系统丢失的精度极小。但必须注意到,只有丝垂直的时候,导轮V形槽才处于理想状态,只要一发生偏摆,即只要b>0,V形槽对丝的运动就产生了干扰作用,这个干扰作用通常在t角小于1.50时,误差是很小的,1.5~30时,误差已明显存在;30~60时,误差已直接构成了对加工精度和切割效果的威胁,尚能维持正常切割;当大于60时,不但精度已严重丢失,正常切割也很难维持,甚至造成钼丝脱槽。所以通常在直线机床上加装锥度装置形成的简易锥度机床,一般把最大切割锥度限制在±60。这个锥度值对一些出模斜度加工任务的完成已绰绰有余了。更大锥度的切割则要依赖于专用锥度机床,这种机床要从结构上解决导轮与UV偏摆随动的问题。不存在偏摆后导轮槽的干扰作用,切割的锥度从原理上讲是准确的。伴生的负面影响是,为解决偏摆随动问题而使整体刚性降低,运动迟滞和回差凸现,运动保真度精确度也大打折扣。日常应用,直线切割的通用性,稳定性和方便灵活性也受到影响,直、锥已很难兼顾。
锥度切割能准吗?
首先应该肯定,从原理上讲,锥度是可以切准的。因为当输入导轮半径,上下导轮中心距离,下导轮距下平面的距离,工件的高度和锥度角后,由程序中的那个相似形公式做数学模型,可以把工件上平面和下平面的尺寸很准确地换算成XY与UV的组合运动数值,以μ为当量的步距是可以满足极高的精度要求的。但实际切割时,仍有许多直接影响精度的误差存在,如导轮半径、导轮中心距、下导轮到下平面的距离这类的数字,是很难求得一个很准确的数值的,它们的误差值与μ级精度相比大概要差百倍千倍。造成程序运行中的假数真算。精度丢失的另一重要原因是切锥度时上下导轮竖直方向是不在同一位置的,此时给丝定位的已不是导轮V形槽的根部,V形槽的V形面已干涉了丝的初始位置,这是一个含有极其不定因素的变量,这是一个幅度从几个μ到几MM的变量,而这个量无法在任何运算中加以补偿。故而在大锥度的切割机上,采用了导轮与UV轴随动的结构,也有人称作连杆式结构,从而解决了导轮V形面干涉钼丝的问题。但因复杂的联动系统,不少于三处的活动关节,使导轮已承载在一个刚性较差,支点和力臂都较长的活动轴体的端头上。整体稳定性、刚性以及动作的滞后,都成了影响切割精度的重要因素。
尽管锥度切割还存在许多难以克服的问题,它仍是线切割的一个强大功能,是可以藐视任何机械加工的独具的优越性,它可以解决机械加工行业无人能够做到的特殊的难题。锥度功能的使用有一个熟练的过程,针对性的工艺试验和输入参数对加工结果的影响估测是锥度切割的重要经验。试验和经验可以帮助你切割出精度很高的锥度零件,第一件可能不够满意,但第二件或第三件完全有把握拿到一个合格的产品。因为改变输入参数中的任何一个,比如上下导轮的中心距或是锥度角,它可以直接控制上平面的尺寸或下平面的尺寸。以第一件做参照,第二件做修正,第三件成功的可能性是很大的。这样的参照,修正和成功经过几次,也可以到得心应手的程度。最终以我们现有的机床,锥度切割的控制能力,可以达到的精度通常在0.05左右,这对锥度零件的生产来说,适用性和满意度已经很高了。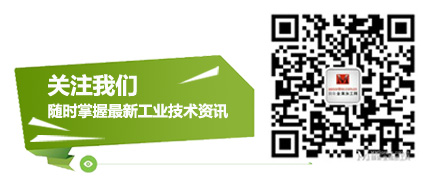
大厚度的切割是比较困难的,可不是丝架能升多高,就能切多厚。受放电加工蚀除条件的制约,后到一定程度,加工就很不稳定,直至有电流无放电的短路发生。伴随着拉孤烧伤很快会断丝,在很不稳定的加工中,切割面也会形成条条沟槽,表面质量严重破破坏。切缝里充塞着极粘稠的蚀除物,甚至是近乎于粉状的碳黑及蚀物微粒。大厚度通常是指200mm以上的钢,至于电导率更高,导热系数更高或耐高温的其它材料还到不了200mm,如紫铜,硬质合金、纯钨、纯钼等,70mm厚就已非常困难了。
大厚度切割的主要矛盾有:
没有足够水的进入和交换,间隙内不能清除蚀物,不能恢复绝缘,也就无法形成放电。
间隙内的充塞物以电阻的形式分流了脉冲源的能量,使丝与工件间失去了足够的击穿电压和单个脉冲能量。
钼丝自身的载流量所限,不可能有更大的脉冲能量传递到间隙中去。
切缝中间部位排出蚀除物的路程太长,衰减了的火花放电已形不成足够的爆炸力,排污力。
材料原因,大厚度存在杂质和内应力的可能性就大为增强了。切缝的局部异常和形变机率也就大了。失去了切割冲击力,却增大了被短路的可能性。解决大厚度切割的主要矛盾,可采取如下措施:
加大单个脉冲的能量(单个脉冲的电压、电流、脉宽,这三者的乘积就是单个脉冲的能量)。,加大脉冲间隔,目的是钼丝载流量的平均值不增大的前题下,形成火花放电的能力,火花的爆炸力被增强。选用介电系数更高,恢复绝缘能力更强,流动性和排污解力更强的冷却液。大幅度提高脉冲电压,使放电间隙加大,水进入和排出也就比较容易了。事先作好被切材料的予处理,如以反复锻造的办法均匀组织,清除杂质,以退火和实效处理的办法清除材料的内应力。以去除大的余理的办法使材料应力得到充分释放。提高丝速,更平稳的运丝,使携水和抗据短路的能力增强。人为偏制折线进给或自动进二退一的进给方式,使间隙被有效扩大。
锥度机床的最大锥度是怎样确定的?
锥度机床锥度切割靠增加了U、V且与X、Y轴能联动,构成了上下两个平面的协调运动。U、V和X、Y分别决定了上下平面两个端点,工件的上下两个平面上的轨迹点就在这两个端点的联线上,这就是锥度切割的基本原理。而U、V的行程就决定了上端点可以偏摆的幅度。UV最大摆幅b和上下导轮的中心距的比值就决定了t角的大小,t即是切割的最大斜度。运算控制系统的相似形公式可以很准确的把工件上下平面的尺寸折算到UV,XY两平面上去,运算控制系统丢失的精度极小。但必须注意到,只有丝垂直的时候,导轮V形槽才处于理想状态,只要一发生偏摆,即只要b>0,V形槽对丝的运动就产生了干扰作用,这个干扰作用通常在t角小于1.50时,误差是很小的,1.5~30时,误差已明显存在;30~60时,误差已直接构成了对加工精度和切割效果的威胁,尚能维持正常切割;当大于60时,不但精度已严重丢失,正常切割也很难维持,甚至造成钼丝脱槽。所以通常在直线机床上加装锥度装置形成的简易锥度机床,一般把最大切割锥度限制在±60。这个锥度值对一些出模斜度加工任务的完成已绰绰有余了。更大锥度的切割则要依赖于专用锥度机床,这种机床要从结构上解决导轮与UV偏摆随动的问题。不存在偏摆后导轮槽的干扰作用,切割的锥度从原理上讲是准确的。伴生的负面影响是,为解决偏摆随动问题而使整体刚性降低,运动迟滞和回差凸现,运动保真度精确度也大打折扣。日常应用,直线切割的通用性,稳定性和方便灵活性也受到影响,直、锥已很难兼顾。
锥度切割能准吗?
首先应该肯定,从原理上讲,锥度是可以切准的。因为当输入导轮半径,上下导轮中心距离,下导轮距下平面的距离,工件的高度和锥度角后,由程序中的那个相似形公式做数学模型,可以把工件上平面和下平面的尺寸很准确地换算成XY与UV的组合运动数值,以μ为当量的步距是可以满足极高的精度要求的。但实际切割时,仍有许多直接影响精度的误差存在,如导轮半径、导轮中心距、下导轮到下平面的距离这类的数字,是很难求得一个很准确的数值的,它们的误差值与μ级精度相比大概要差百倍千倍。造成程序运行中的假数真算。精度丢失的另一重要原因是切锥度时上下导轮竖直方向是不在同一位置的,此时给丝定位的已不是导轮V形槽的根部,V形槽的V形面已干涉了丝的初始位置,这是一个含有极其不定因素的变量,这是一个幅度从几个μ到几MM的变量,而这个量无法在任何运算中加以补偿。故而在大锥度的切割机上,采用了导轮与UV轴随动的结构,也有人称作连杆式结构,从而解决了导轮V形面干涉钼丝的问题。但因复杂的联动系统,不少于三处的活动关节,使导轮已承载在一个刚性较差,支点和力臂都较长的活动轴体的端头上。整体稳定性、刚性以及动作的滞后,都成了影响切割精度的重要因素。
尽管锥度切割还存在许多难以克服的问题,它仍是线切割的一个强大功能,是可以藐视任何机械加工的独具的优越性,它可以解决机械加工行业无人能够做到的特殊的难题。锥度功能的使用有一个熟练的过程,针对性的工艺试验和输入参数对加工结果的影响估测是锥度切割的重要经验。试验和经验可以帮助你切割出精度很高的锥度零件,第一件可能不够满意,但第二件或第三件完全有把握拿到一个合格的产品。因为改变输入参数中的任何一个,比如上下导轮的中心距或是锥度角,它可以直接控制上平面的尺寸或下平面的尺寸。以第一件做参照,第二件做修正,第三件成功的可能性是很大的。这样的参照,修正和成功经过几次,也可以到得心应手的程度。最终以我们现有的机床,锥度切割的控制能力,可以达到的精度通常在0.05左右,这对锥度零件的生产来说,适用性和满意度已经很高了。
声明:本网站所收集的部分公开资料来源于互联网,转载的目的在于传递更多信息及用于网络分享,并不代表本站赞同其观点和对其真实性负责,也不构成任何其他建议。本站部分作品是由网友自主投稿和发布、编辑整理上传,对此类作品本站仅提供交流平台,不为其版权负责。如果您发现网站上所用视频、图片、文字如涉及作品版权问题,请第一时间告知,我们将根据您提供的证明材料确认版权并按国家标准支付稿酬或立即删除内容,以保证您的权益!联系电话:010-58612588 或 Email:editor@mmsonline.com.cn。
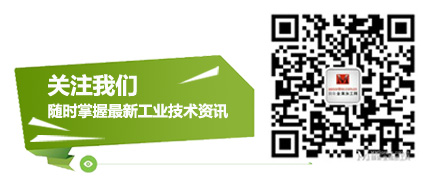
网友评论
匿名:
相关链接
最新反馈
- 暂无反馈
无须注册,轻松沟通