在精密机器应用中降低成本和提高质量的解决办法
【编者按】本文介绍目前市场上常见的几种过滤方法并评估了它们对加工工艺的影响。
冷冻剂和润滑油的高效性能对世界各地的工程师和机床操作员来说都是一个巨大的挑战。保持液体清洁无金属杂质对研磨、钻孔、珩磨、抛光、EDM和其它精加工等工艺至关重要。
效率低下的过滤严重影响生产线的成品质量,对制造效率和废物管理等也有影响。
屏障过滤(滤筒、滤袋和滤片)
也许最常见的过滤方式就是利用某种形式的屏障,在液体流经屏障或循环时去除液体中的颗粒。屏障有很多种形式,不过通常都是滤筒、滤袋或滤片的形式。它们都采用了一定长度的介质(主要是流延、编织或纺织聚丙烯、聚酯或纤维素材料),可以打褶并做成滤筒的样子(从而增加表面积),展开或绕在轴芯上(用于深度过滤器),做成滤袋(便于使用或装下更多的灰尘)或者干脆在框架上撑起一卷平展的滤片材料。基本原理就是这些屏障上都有很多小孔,比如40微米大小的孔,在液体流过时其中大于这个尺寸的污染物就会被滤出。
屏障过滤会导致压力下降,这对使用介质的过滤既有好处也有坏处。以滤筒为例(当然滤袋和滤片的工作原理也是大同小异),如果尺寸正确的话,滤筒系统在开始用时的压差非常小(压差是指过滤器上游或之前和过滤器下游或之后的压力之间的差)。随着污染物从系统中被滤出,这些污染物开始堵塞部分滤筒介质,导致压差升高。这种情况将会持续,直到压差高到上游压力无法克服,这时滤筒就会被彻底堵塞。实际使用中,下游压力会降到一个无法使用的水平,或是出现断流的情况,而在发生这种情况之前,通常会设定一个最大压差,当达到最大压差时,滤筒基本已经堵塞,要么加以清洁,但更多的是取出丢弃并更换新的滤筒。
屏障过滤的主要好处有:
易于控制 — 压差的好处是它能清楚地为操作员或机器制造商指示过滤器的使用寿命,以及何时应该取出和更换滤筒,还可以使用一个简单的系统来读取下游压力降,以触发自动加工中心绕开过滤器(或在双工系统中切换至另一个并联的过滤器)或关闭机器。
资本成本 — 介质过滤的另一个好处是它的价格相对较低(尽管性价比不一定高!)。过滤器供应商通常会降低过滤器外壳的成本,因为一台新安装的机器会在之后很多年里因为一次性介质的销售而带来丰厚的收入。在污染水平较低的应用中,屏障过滤器能体现出很高的价值。
但屏障过滤法也存在缺陷,主要包括:
更换和处置成本 — 滤筒或滤纸被污染颗粒堵塞后需要加以更换,久而久之过滤器替换件的购置费用会很高,而且取出和更换旧过滤器还会产生停工时间。在某些工艺中,过滤器可能几天就要更换一次。
此外,处置成本也是一个越来越受到关注的问题。对于受到油污染的过滤器,处置成本相当高。随着ISO 14001的推出和对企业社会责任的重视,很多公司都制订了革新的环保政策,持续致力于减少工艺废物。
效率有限 — 这种压力损失的另一个缺点是,它限制了可行条件下可以达到的过滤水平。因此,在兼顾所需的过滤水平和保持流速且经济可行的过滤水平之间,介质过滤始终是一种折中途径。一般为了避免影响流速,过滤能力可以设为40微米。但这就意味着小于这个尺寸的颗粒仍然存在于流动的液体中,从而导致磨损,降低零件表面加工质量,缩短机油/冷冻剂使用寿命。这对于汽车零部件、轴承和医疗用品等精度要求极高的产品而言,是个尤为重要的问题。
当然工业中还有多种其它类型的屏障过滤系统(粉末、错流等),但是都不如滤筒、滤袋和滤片常见,而且也具有上述几项缺点。粉末或烛形系统还有其它缺点,比如粉末处理以及与此相关的健康和安全问题,错流系统(有希望使用数年后再更换滤筒介质)是一种减少对耗材依赖性的好方法,而且有很多可重复使用过滤的好处,但是成本非常高,而且对能源的依赖性更高。
沉降槽
有些工艺没有特别的过滤介质,而是依靠污染颗粒的自然沉降。液体在循环期间被抽入到一个存储槽中,在那里较大的颗粒会在重力作用下沉降出来。随后,在某些情况下,这些颗粒会由刮板输送机清除,或在某些情况下直到这些颗粒积累至一定临界点,再通过人工手动清洁。
沉降的主要好处有:
不用一直花钱购买过滤介质 — 没有要更换的一次性过滤器,所以持续运行成本要低于其它方法。
缺点如下:
污染物去除效率低 — 沉降并非真正的过滤,没有屏障或分离颗粒的方法。它依靠的是颗粒自身的重量,而且取决于液体在沉降槽中停留的时间。如果液体快速流过,沉降效果则微乎其微。因此沉降只对滤除较大或较重的颗粒有效。较轻的颗粒仍留在液体中继续流通。这对成品或机器来说存在损坏风险。
清洁停工时间 — 在没有任何自动去除污染沉淀物方法的工艺中,清洁存储槽是一项成本相当高的工作。因为它需要较长的停工时间,并且要彻底更换液体。
气旋分离
气旋、离心或旋液分离系统在世界各地都有广泛应用。这些系统的尺寸、价格和复杂程度各有不同,但是通用原理都是利用液体和污染物的密度不同来加速自然沉降。
被污染的液体被吸入一个垂直安装的圆锥形分离器,液体沿容器壁高速流动。污染颗粒在离心力的作用下被甩出,并受到回压的作用落下。污染物从液体中分离出来,通过下溢口排出,而清洁的液体通过溢出口流入清洁的液槽。
气旋分离的好处有:
不使用过滤介质 — 没有更换和维护屏障过滤器的问题。因此不会产生耗材成本和需要处置的废弃过滤器。
没有运动部件 — 气旋过滤通常没有任何运动部件,因此出现故障的可能性更小。
气旋系统的缺点有:
过滤有限 — 气旋系统通常只能滤出较大的污染颗粒。受到工艺的限制,它们对于低密度或5微米以下的小颗粒过滤效果并不好。由于无法滤除小颗粒,所以单独使用这种方法会给高精度加工带来问题。
高维护成本 — 很多气旋系统都需要定期清洁,除去积累的污染物,防止下溢口堵塞。
高投资成本 — 在大型机床应用中,气旋系统的资本投资要高于其它过滤方法。
磁过滤
磁过滤的基本原理是在液流路径中所有液流都必须经过的位置放置高强度永磁棒,通过充分的接触从液体中去除含铁污染物。磁棒要定期取出清洁,然后再放回原位。
从简单悬挂在机器油箱中的市售磁体,到无需任何操作员干预、24小时全天候运转的高强度设计自动清洁系统,市场上的磁过滤和分离设备多种多样。
很多研磨和铣削制造工厂已经采用鼓磁,通常都是搭配介质卷系统使用,有些还会把磁棒挂在滤袋中,但是这些系统的效率通常都会受到所用磁体的磁力、施加的接触时间(液体在能吸附含铁颗粒的区域流过的时间)或实际接触磁体的液量等因素的限制。
为了实现最有效的亚微米级过滤,设计的过滤系统必须能够确保所有污染液能在磁体环境中暴露足够长的时间,而且磁体的磁力强度足以吸出液体中的污染物。这种系统还必须易于清洁(如果是手动系统)或能够可靠地进行自动清洁。
为了达到所需的磁场强度,从而达到理想的过滤效果,首选的磁体材料是钕铁硼(俗称“稀土”)。由于这是一种在液体中会快速腐蚀的不稳定材料,所以一般都经过镀镍处理,而且为了便于清洁并避免与正在过滤的液体接触,这种材料密封在不锈钢管中。稀土的磁场强度可以达到12000高斯(在不锈钢外壳之外测得 — 直接在镀镍磁体上测量没有意义,因为磁体并不是这样直接使用的)。这种强度比音箱、闩锁、开关等常见陶瓷磁体的磁场强6到7倍。
为了正确选择系统的规格和尺寸,无论是哪种系统,都必须了解流速和压力、预期污染等级和污染类型。磁过滤可以用于各种可能存在铁质颗粒的液体。目前最常见的此类应用主要针对铸铁或钢铁,不过也能用于磁吸力更小以及更难吸附的材料,例如不锈钢和碳化物。
工业中最常见的300号不锈钢普遍没有磁性,但在硬化后会具有顺磁性,然后便可以从液体中滤除。磨损或切削(研磨、铣削等)工艺都会引起硬化,因此液体中的零散颗粒就有可能带有顺磁性,在足够强的磁力下可以被滤出。这些磁吸力较小的材料需要以较低流速进行过滤,以便有足够的接触时间有效去除污染。
现代的高强度磁性系统具有独特的优点:
效率高 — 高强度磁过滤器可以滤除小到亚微米级的极小颗粒。可以提高系统中的机油/冷冻剂质量,为零件质量、表面加工带来积极影响,最终达到减少不良产品的目的。这在高精度工艺中尤其具有优势。更清洁的液体还能显著延长机床的使用寿命,从而缩短因机床/机轮温度过高或毁坏引起的停工时间和清洁机器所需的定期停工时间。采用磁过滤的投资回报通常也非常迅速。
全天候运转 — 现代的磁过滤系统可以配备全自动清洁系统,确保最大程度缩短维护停工时间。
经济 — 磁过滤采用永磁芯或永磁棒,无需更换或处置,同时节省滤芯替换成本和旧污染滤芯的处置成本。由于磁过滤的效率得到提升,机油/冷冻剂的清洁效率也随之提高,机油更换频率降低,因而还节省了机油更换成本和“旧”污染机油的处置成本。
环保 — 由于磁过滤器不需要使用任何消耗性介质,因此不会产生与介质过滤有关的废物。此外,机油更清洁,而且无需冷冻剂,不必再像从前一样频繁更换。如今,从成本及企业形象的角度考虑,大多数现代企业都非常重视环境保护。
磁过滤的主要缺点在于它无法滤除非磁性颗粒。不过这些颗粒在金属加工应用中构成的污染比例非常小。磁过滤还可以搭配其它类型的过滤使用,从而确保彻底滤除各种污染。
总结
随着大部分制造工艺面临的降低成本和提高产量的压力日益增大,制造工艺中采用恰当的过滤系统会给工作效率带来显著的影响。因此权衡每一种过滤的优缺点、投资成本及其对工艺的改善程度都变得非常重要。
声明:本网站所收集的部分公开资料来源于互联网,转载的目的在于传递更多信息及用于网络分享,并不代表本站赞同其观点和对其真实性负责,也不构成任何其他建议。本站部分作品是由网友自主投稿和发布、编辑整理上传,对此类作品本站仅提供交流平台,不为其版权负责。如果您发现网站上所用视频、图片、文字如涉及作品版权问题,请第一时间告知,我们将根据您提供的证明材料确认版权并按国家标准支付稿酬或立即删除内容,以保证您的权益!联系电话:010-58612588 或 Email:editor@mmsonline.com.cn。
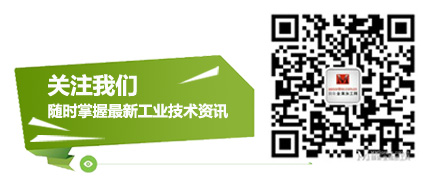
- 暂无反馈