涂层枪钻在液压阀板零件深孔加工中的应用
枪钻涂层后,枪钻的支撑圆弧面对孔壁的挤压效果增强,又因为刀具许用转速的提高,使铁屑长度变短,排屑更加流畅,软材料的深孔加工获得了满意的加工质量,我们通过案例来验证一下。
液压阀板,是工程自卸车上的重要液压零部件。该零件上有相互垂直的两个ϕ16mm过油孔,这两个过油孔的深孔加工是该零件最关键的工序。
液压阀板的材料为45钢,钻孔前热处理硬度为HB180。
深孔钻床做为半精加工,按工艺要求,必须将孔径尺寸的一致性控制在ϕ15.94±0.015mm,孔粗糙度小于Ra1.6,为随后的精加工桁磨做工艺准备。
最初加工状态如下:
机床采用数控深孔钻床ZK2120×4/300,一次装夹四件工件。刀具采用国产硬质合金枪钻。
加工参数:钻头转速:1500r/min,进给量:0.03mm/r,油泵压力为4MPa。
加工一组工件后,检测四个工件:发现孔径尺寸分别为:ϕ15.95、ϕ15.96、ϕ15.93、ϕ15.96,有两个工件的孔径尺寸超差。更为严重的是,内孔的粗糙度较差,并且有不规则的沟槽。后经分析,沟槽为铁屑在孔壁的划痕。经后道工序桁磨实验,沟槽较深,无法桁磨消除。又加工几组工件,情况类似。后又改变刀具角度,增大油泵压力,加工状况均无明显改善,不能满足加工要求。
随后,为了排除刀具因素,更换了枪钻厂家,采用进口山特维克硬质合金枪钻,其他加工参数同上。加工结果孔径尺寸和粗糙度与国产枪钻相比均有不同程度的提高。但批量生产仍有30%左右的工件孔径尺寸超差,另外,孔壁依然会间断出现划痕,造成约35%的工件因划痕太深无法桁磨。
我们将工件钻孔前的热处理硬度提高至HB220左右,同样采用上述加工参数,深孔加工孔径尺寸可以控制在ϕ15.94±0.013mm,粗糙度Ra1.6,孔壁划痕大量减少。完全可以满足后道桁磨工序要求。经分析,造成孔径尺寸及粗糙度超差,最主要的原因是工件材料硬度太低。深孔加工时,工件对刀具的支撑不够,造成孔径尺寸不稳定;并且,因为工件材料硬度低,铁屑很容易在孔壁划出划痕。
但是,提高工件材料热处理硬度,会增加一笔不小的热处理费用。并且,因工件硬度提高,刀具磨损加大,也造成加工成本的上升。所以,提高材料硬度并不是最优解决方案。
针对材料偏软的情况,我们将枪钻的硬质合金钻头做涂层处理。涂层材料为TiN,涂层厚度2um。涂层枪钻与普通枪钻相比成本增加有限。
加工参数:钻头转速:1680r/min,进给量:0.035mm/r,油泵压力为4MPa。加工一组工件后,经检测,四个工件:孔径尺寸分别为ϕ15.945、ϕ15.95、ϕ15.94、ϕ15.945,内孔粗糙度Ra0.8~Ra1.6。内孔的铁屑划痕几乎消失,加工效果非常理想。又连续加工几组,加工状态非常稳定。
经大批量加工试验,涂层刀具寿命较未涂层的普通刀具延长50%左右,降低了加工成本。更重要的是,加工质量大大提高,完全可以满足加工要求。
声明:本网站所收集的部分公开资料来源于互联网,转载的目的在于传递更多信息及用于网络分享,并不代表本站赞同其观点和对其真实性负责,也不构成任何其他建议。本站部分作品是由网友自主投稿和发布、编辑整理上传,对此类作品本站仅提供交流平台,不为其版权负责。如果您发现网站上所用视频、图片、文字如涉及作品版权问题,请第一时间告知,我们将根据您提供的证明材料确认版权并按国家标准支付稿酬或立即删除内容,以保证您的权益!联系电话:010-58612588 或 Email:editor@mmsonline.com.cn。
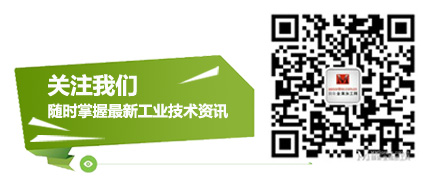
- 暂无反馈