数控机床编程七-Master CAM综合应用实例四
7.3.2 曲面编程实例
图7-102所示为某新款手表外壳的手板,材料为进口的不锈钢。下面说明其加工工艺和使用MasterCAM编程的加工参数。
1.零件造型用MasterCAM 8.0完成此零件的曲面模型,如图7-103所示。
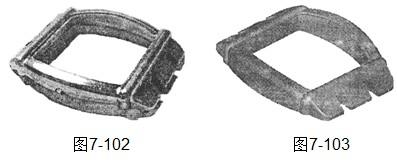
2.零件加工顺序
(1)曲面粗加工:使用φ6mm的高速钢球头刀加工。
(2)曲面精加工:使用φ3mm的硬质合金球头刀加工。(3)轮廓精加工:用φ2mm的硬质合金平头刀加工。(4)刻线:使用自已磨的划线刀。
3.程序编制
(1)曲面粗加工:
1)工艺分析 使用直径为Φ6mm的高速钢球头刀进行加工,设置机床主轴转速为2000r/min,切削进给为350mm/min。因为加工余量不大,故可选用曲面平行式精加工方式,这样提刀少,效率高。选择曲面平行式精加工方式,选取精加工曲面,在主功能菜单依次点击“主菜单→刀具路径→曲面加工→曲面精加工→平行铣削”选项。系统提示选取加工曲面,在曲面子菜单上点击“所有的”,接着点击“曲面”,选择所有的曲面作为加工对象,返回到曲面子菜单,点单“执行”,完成曲面选择。
2)选取加工刀具,设置加工类型及参数
①选刀:打开曲面平行精加工方式对话框的“刀具参数”选项,在刀具栏空白处单击鼠标右键,在弹出菜单中选“从刀具库中选取刀具”,系统弹出刀具选择对话框,选一把直径为φ6mm的球头刀,刀号为1。设定主轴转速为2000,切削进给为350,插入进给为150,冷却液为“喷油”,其余默认值。
②单击“平行铣削精加工参数”选项,设置曲面加工参数,安全平面高度为50,绝对方式;设置刀具 回退高度为50,绝对方式;慢速下刀起始距离为2,相对方式;刀长补正到刀尖;加工预留量为0.3;选取底平面为安全检查面,并留余量为0.1,其余默认值。
③单击“平行铣削精加工参数”选项,设置平行铣加工参数:加工公差为0.1;切削行间距0.3;加工方式为来回铣削,切削角度为90度。
④生成刀具路径。进行完所有参数的设置后,单击“确定”按钮,系统提示选择边界,点击“执行”完成边界的设定,系统即按设置的参数计算出刀具路径,如图7-104所示,在主功能区依次点击“主功能菜单→刀具路径 →操作管理”,进入操作管理菜单,选中要产生加工程序的操作, 点击执行后处理进入后处理 程式菜单。默认后处理程序 为FANUC系统,即MPFAN.PST, 点击确定,经后处理程序生成NC 程序,即可用于加工。
2、曲面精加工
(1)工艺分析使用直径为φ3mm的硬质合金球头刀进行加工,设置机床主轴转速为3800r/min,切削进给为500mm/min。
(2)选择曲面平行式精加工方式,选取精加工曲面,操作与粗加工相同。
(3)选取加工刀具,设置加工类型及参数。
1)选刀的操作与粗加工相同,选一把直径为φ3mm的球头刀,设定主轴转速为3800,切削进给为500,插入进给为300,程序号为2,其余参数与粗加工相同。
2)单击“曲面参数”选项,设置曲面加工参数。加工预留量为0.05,为后序打磨留余量,同样选取底平面为安全检查面,并留余量为0.5 ,其余参数与粗加工相同。
3)单击“曲面平行精加工参数”选项,设置平行铣加工参数。设置加工公差为0.01,切削行间距0.1,加工方式为来回铣,切削角度为90度。其余与粗加工相同。
4)生成刀具路径。操作与粗加工相同,产生刀具路径。
3.外形轮廓精加工
(1)工艺分析 轮廓宽度和深度都是0.5mm,圆角半径为1.75mm,因为使用三轴联动加工中心制作,为保证形状精度,用直径为φ2mm的硬质合金立铣刀进行加工。设置机床主轴转速成为3500r/min,切削进给为300mm/min,考虑到刀具的切削负荷,所以深度分层切削,每层深度为0.03mm。选择轮廓铣削加工,选取加工工件3D曲线,该曲线为刀中线,并已投影到工件的底部曲面上。
1)在主功能菜单依次点击“主功能菜单→刀具路径→外形铣削”选项。
2)系统提示选取外形铣削加工的外形边界,将视图设置为侧视图。选取加工外形的3D曲线,注意箭头方向,为逆时针,它决定是顺铣还是逆铣,此时为顺铣,这样表面精度好。
(3)选取加工刀具,设置加工类型及参数
1)选刀:打开外形铣削对话框的选项卡,选直径为φ2mm的立铣刀,刀号为3,设置主轴转速为3500,切削进给为300,插入进给为300,冷却液为开,程序号为3,其余默认值。
2)单击“外形参数”按钮,系统显示3D外形铣削加工。设置高度参数:设置慢速下刀起始距离为0,毛坯高度为-1.3,不使用刀具半径补正,加工预留量为0,其余与粗加工相同。
4)激活深度切削“切削深度”,不安排精加工,每次切削深度为0.03,第次切削后不抬刀。
5)激活进退刀选项,设置直线和圆弧切向进退刀,以避免刀具的损坏和提高工件表面质量。
6)生成刀具路径。操作 与粗加工相同,产生刀具 路,如图105所示。
4.刻线
(1)工艺分析 在表带两侧曲面上共刻8条线,深度为0.1。使用自己磨的刻线刀,形状如图7-106所示。用直径6mm的高速钢棒,先磨出锥度,再磨去一半,最后倒出后角和避空,设置机床主轴转速成为5000r/min,切削进给为300mm/min,考虑到刀具小,为减少切削负荷,所以深度分层切削,每层深度为0.01mm。
(2)选择轮廓铣削方式,选取要刻的8条3D曲线,曲线为刀中线,并已投影到表壳曲面上。
1)在主功能菜单依次点击“主功能菜单→刀具路径→外形铣削”选项。
2)系统提示选取外形铣削加工的外形边界,将视图设置为顶视图,选取要加工的8条3D曲线。注意箭头方向:左边的四条线箭头从左向右,右边的四条线箭头从右向左,它们决定了加工方向,保证从底处向高处加工,防止因顶底而断刀。
(3)选取加工刀具,设置加工类型及参数
1)选刀:系统打开外形轮廓对话框的选项卡,选直径为φ1mm的球头刀,刀号为4。设置主轴转速5000,切削进给为300, 插入进给为300, 冷却液开, 程序 号为4,其余默认 值,实际用图106 所示 的刀具。
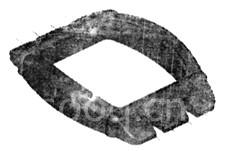
2)单击“外形铣削参数”按钮,系统显示3D外形铣削加工。
3)设置高度参数:安全平面高度为20,绝对方式;刀具回退高度为20,绝对方式;慢速下刀起始距离为0,增量方式;毛坯高度为-4.95,绝对方式;不使用刀具半径补正;加工预留量XY和Z都为0;其他参数都为0。
4)激活深度切削,不安排精加工,每次切削深度为0.01,每次切削后抬刀,其他参数按默认值。
5)激活进退刀选项,设置直线进刀,长度为200%,即2.0mm,以避免刀具的损坏,其他都为0。
(4)生成刀具路径 操作与粗加工相同,产生刀具路径,如图7-107所示。
图7-102所示为某新款手表外壳的手板,材料为进口的不锈钢。下面说明其加工工艺和使用MasterCAM编程的加工参数。
1.零件造型用MasterCAM 8.0完成此零件的曲面模型,如图7-103所示。
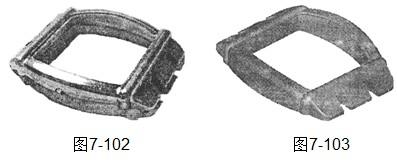
2.零件加工顺序
(1)曲面粗加工:使用φ6mm的高速钢球头刀加工。
(2)曲面精加工:使用φ3mm的硬质合金球头刀加工。(3)轮廓精加工:用φ2mm的硬质合金平头刀加工。(4)刻线:使用自已磨的划线刀。
3.程序编制
(1)曲面粗加工:
1)工艺分析 使用直径为Φ6mm的高速钢球头刀进行加工,设置机床主轴转速为2000r/min,切削进给为350mm/min。因为加工余量不大,故可选用曲面平行式精加工方式,这样提刀少,效率高。选择曲面平行式精加工方式,选取精加工曲面,在主功能菜单依次点击“主菜单→刀具路径→曲面加工→曲面精加工→平行铣削”选项。系统提示选取加工曲面,在曲面子菜单上点击“所有的”,接着点击“曲面”,选择所有的曲面作为加工对象,返回到曲面子菜单,点单“执行”,完成曲面选择。
2)选取加工刀具,设置加工类型及参数
①选刀:打开曲面平行精加工方式对话框的“刀具参数”选项,在刀具栏空白处单击鼠标右键,在弹出菜单中选“从刀具库中选取刀具”,系统弹出刀具选择对话框,选一把直径为φ6mm的球头刀,刀号为1。设定主轴转速为2000,切削进给为350,插入进给为150,冷却液为“喷油”,其余默认值。
②单击“平行铣削精加工参数”选项,设置曲面加工参数,安全平面高度为50,绝对方式;设置刀具 回退高度为50,绝对方式;慢速下刀起始距离为2,相对方式;刀长补正到刀尖;加工预留量为0.3;选取底平面为安全检查面,并留余量为0.1,其余默认值。
③单击“平行铣削精加工参数”选项,设置平行铣加工参数:加工公差为0.1;切削行间距0.3;加工方式为来回铣削,切削角度为90度。
④生成刀具路径。进行完所有参数的设置后,单击“确定”按钮,系统提示选择边界,点击“执行”完成边界的设定,系统即按设置的参数计算出刀具路径,如图7-104所示,在主功能区依次点击“主功能菜单→刀具路径 →操作管理”,进入操作管理菜单,选中要产生加工程序的操作, 点击执行后处理进入后处理 程式菜单。默认后处理程序 为FANUC系统,即MPFAN.PST, 点击确定,经后处理程序生成NC 程序,即可用于加工。
2、曲面精加工
(1)工艺分析使用直径为φ3mm的硬质合金球头刀进行加工,设置机床主轴转速为3800r/min,切削进给为500mm/min。
(2)选择曲面平行式精加工方式,选取精加工曲面,操作与粗加工相同。
(3)选取加工刀具,设置加工类型及参数。
1)选刀的操作与粗加工相同,选一把直径为φ3mm的球头刀,设定主轴转速为3800,切削进给为500,插入进给为300,程序号为2,其余参数与粗加工相同。
2)单击“曲面参数”选项,设置曲面加工参数。加工预留量为0.05,为后序打磨留余量,同样选取底平面为安全检查面,并留余量为0.5 ,其余参数与粗加工相同。
3)单击“曲面平行精加工参数”选项,设置平行铣加工参数。设置加工公差为0.01,切削行间距0.1,加工方式为来回铣,切削角度为90度。其余与粗加工相同。
4)生成刀具路径。操作与粗加工相同,产生刀具路径。
3.外形轮廓精加工
(1)工艺分析 轮廓宽度和深度都是0.5mm,圆角半径为1.75mm,因为使用三轴联动加工中心制作,为保证形状精度,用直径为φ2mm的硬质合金立铣刀进行加工。设置机床主轴转速成为3500r/min,切削进给为300mm/min,考虑到刀具的切削负荷,所以深度分层切削,每层深度为0.03mm。选择轮廓铣削加工,选取加工工件3D曲线,该曲线为刀中线,并已投影到工件的底部曲面上。
1)在主功能菜单依次点击“主功能菜单→刀具路径→外形铣削”选项。
2)系统提示选取外形铣削加工的外形边界,将视图设置为侧视图。选取加工外形的3D曲线,注意箭头方向,为逆时针,它决定是顺铣还是逆铣,此时为顺铣,这样表面精度好。
(3)选取加工刀具,设置加工类型及参数
1)选刀:打开外形铣削对话框的选项卡,选直径为φ2mm的立铣刀,刀号为3,设置主轴转速为3500,切削进给为300,插入进给为300,冷却液为开,程序号为3,其余默认值。
2)单击“外形参数”按钮,系统显示3D外形铣削加工。设置高度参数:设置慢速下刀起始距离为0,毛坯高度为-1.3,不使用刀具半径补正,加工预留量为0,其余与粗加工相同。
4)激活深度切削“切削深度”,不安排精加工,每次切削深度为0.03,第次切削后不抬刀。
5)激活进退刀选项,设置直线和圆弧切向进退刀,以避免刀具的损坏和提高工件表面质量。
6)生成刀具路径。操作 与粗加工相同,产生刀具 路,如图105所示。
4.刻线
(1)工艺分析 在表带两侧曲面上共刻8条线,深度为0.1。使用自己磨的刻线刀,形状如图7-106所示。用直径6mm的高速钢棒,先磨出锥度,再磨去一半,最后倒出后角和避空,设置机床主轴转速成为5000r/min,切削进给为300mm/min,考虑到刀具小,为减少切削负荷,所以深度分层切削,每层深度为0.01mm。
(2)选择轮廓铣削方式,选取要刻的8条3D曲线,曲线为刀中线,并已投影到表壳曲面上。
1)在主功能菜单依次点击“主功能菜单→刀具路径→外形铣削”选项。
2)系统提示选取外形铣削加工的外形边界,将视图设置为顶视图,选取要加工的8条3D曲线。注意箭头方向:左边的四条线箭头从左向右,右边的四条线箭头从右向左,它们决定了加工方向,保证从底处向高处加工,防止因顶底而断刀。
(3)选取加工刀具,设置加工类型及参数
1)选刀:系统打开外形轮廓对话框的选项卡,选直径为φ1mm的球头刀,刀号为4。设置主轴转速5000,切削进给为300, 插入进给为300, 冷却液开, 程序 号为4,其余默认 值,实际用图106 所示 的刀具。
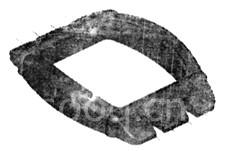
2)单击“外形铣削参数”按钮,系统显示3D外形铣削加工。
3)设置高度参数:安全平面高度为20,绝对方式;刀具回退高度为20,绝对方式;慢速下刀起始距离为0,增量方式;毛坯高度为-4.95,绝对方式;不使用刀具半径补正;加工预留量XY和Z都为0;其他参数都为0。
4)激活深度切削,不安排精加工,每次切削深度为0.01,每次切削后抬刀,其他参数按默认值。
5)激活进退刀选项,设置直线进刀,长度为200%,即2.0mm,以避免刀具的损坏,其他都为0。
(4)生成刀具路径 操作与粗加工相同,产生刀具路径,如图7-107所示。

声明:本网站所收集的部分公开资料来源于互联网,转载的目的在于传递更多信息及用于网络分享,并不代表本站赞同其观点和对其真实性负责,也不构成任何其他建议。本站部分作品是由网友自主投稿和发布、编辑整理上传,对此类作品本站仅提供交流平台,不为其版权负责。如果您发现网站上所用视频、图片、文字如涉及作品版权问题,请第一时间告知,我们将根据您提供的证明材料确认版权并按国家标准支付稿酬或立即删除内容,以保证您的权益!联系电话:010-58612588 或 Email:editor@mmsonline.com.cn。
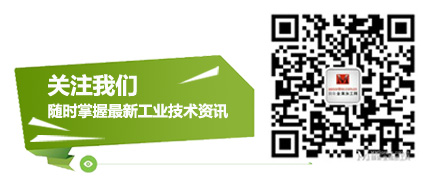
网友评论
匿名:
相关链接
最新反馈
- 暂无反馈
无须注册,轻松沟通