主动锥齿轮车削工艺的优化
主动锥齿轮是汽车上的重要零件之一,其技术要求很高,北京北齿有限公司通过对其加工工艺的分析,对不足之处加以优化,实现了低成本、高品质的生产。
驱动桥主动锥齿轮是发动机纵置车辆都必须配备的驱动桥的重要零件之一,属于轴类零件,由圆锥形的齿部和安装轴承的轴径和联接传动的花键轴及外螺纹组成,是将发动机的动力传递到驱动车轮的重要传动齿轮。
传统车削工艺的不足
传统的车削加工工艺采用以仿形车床为主的工艺,不仅工序多、流程长,而且质量控制和物流管理都不能满足精益制造的要求。
原有生产线存在以下缺点:
1、机床装备落后
原有加工工艺采用的是仿形车床,加工尺寸完全依靠操作者人工调整刀具的装夹位置来控制,刀具更换不易,质量波动较大,只能采用粗精车分开的工艺。
2、工件夹持方式造成工序多
原有车削加工工艺通常是先夹持工件一端、加工另一端,然后调换加工的方式,总共需要两道工序才能完成加工。
3、毛坯去除量大
工件的毛坯是模锻件,平均加工余量为2.5MM,必须分为多次走刀,不仅费时,材料浪费也很大。
车削加工工艺优化分析
针对原有车削工艺当中存在的影响效率和精度的问题,我们采取了一系列的改善措施。表2所示为经过优化后的车削工艺,可以看出单件工时大大缩短。
1、装备升级
对于仿形车床的不足,我们采用了1台铣钻机床和2台数控车床代替原有8台普通机床,换刀时间对加工尺寸的影响变小,并实现了在一次装夹条件下,完成全部车削加工和软磨加工任务,提高了加工尺寸精度。
2、采用端面驱动方式
为了进一步缩短工艺,优化采用端面驱动方式。端面驱动条件下,夹持和驱动条件要求较高,通过分析对比,端面驱动顶尖采用的是性价比较高的韩国GG产品,数控车床采用的是尾座顶紧力可设置的LGMAZAKQTN200U型数控车床,并且配置了刚性和精度保持性较高的套筒式回转顶尖,保证了夹持的可靠性。
3、减少毛坯去除量
我们在优化工件车削加工的同时,也对毛坯锻件进行了优化,将平均加工余量减少到1.6MM,在减少了车削加工的走刀次数的同时,降低了材料消耗。如采用楔横轧工艺制备毛坯,还可能进一步缩短加工节拍和减低材料消耗。
通过工艺优化,大幅度缩短了工艺节拍,缩短了工艺流程,减少了在制品存量,并且为相似的轴类零件的车削加工提供了有益的经验。
声明:本网站所收集的部分公开资料来源于互联网,转载的目的在于传递更多信息及用于网络分享,并不代表本站赞同其观点和对其真实性负责,也不构成任何其他建议。本站部分作品是由网友自主投稿和发布、编辑整理上传,对此类作品本站仅提供交流平台,不为其版权负责。如果您发现网站上所用视频、图片、文字如涉及作品版权问题,请第一时间告知,我们将根据您提供的证明材料确认版权并按国家标准支付稿酬或立即删除内容,以保证您的权益!联系电话:010-58612588 或 Email:editor@mmsonline.com.cn。
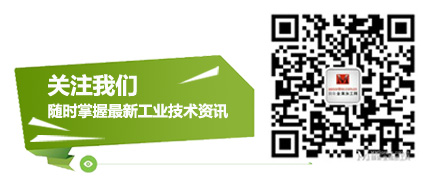
- 暂无反馈