形位误差检测技术研究
随着飞机制造业数字化工程的展开,数字化制造已成为我们航空企业生产发展的方向,这就要求数控检测技术与之相适应,实现对产品的数字化检测,以满足科研生产的快速发展及质量要求。国外先进的航空企业如波音、空客等大型航空制造公司,已将数字化检测技术用于数控测量中。在对形位公差的测量方面,仅借助于测量机的检测功能进行测量,对其测量原理理解不深,测量完全依赖于测量机软件功能,没有充分发挥其数控检测能力的作用。而测量软件对形位误差进行评定,其测量结果只能提供一个定量的误差值,不能定向地说明偏离方向。如测量对称度,其测量结果只能定量地反应出对称度偏差的数值,不能定向地反映出对称度偏差的方向;利用测量软件功能对轮廓度的检测,其结果只能反映出整个面的轮廓度误差,不能准确反映出具体部位超差的数值。所以直接利用测量机功能进行检测,既不便于产品返修,又不便于产品质量分析。因此,有必要对其数字化检测技术进行研究, 实现形位公差的数字化检测。
结合三坐标测量的特点,研究数字化检测形位公差,建立相应的零件坐标系,通过点的坐标值就可以直观地反映实物整个形体质量及偏离方向。这样既便于对不合格产品的返修,又便于工艺部门更准确地对产品质量进行分析,促进工艺方法的改进。数字化检测水平的高低直接影响着产品的质量及交付进度。因此研究产品数字化检测技术,提高工作效率和产品质量,具有重大的现实意义。
面轮廓度检测技术研究
如图1所示,面轮廓度公差带是包络一系列直径为公差值0.200mm的球的两包络面之间的区域,诸球的球心应位于具有理论正确几何形状的面上。当被测要素的理想轮廓相对基准没有位置要求时,属于形状公差;当被测要素的理想轮廓对基准有位置要求时,属于位置公差[1]。
数字化检测面轮廓度误差:在产品CAD模型被测面上提取理论测量点,将得到的型面上点位的理论数据及法矢方向,编辑成一个理论数据文本文件, 再应用数控测量矢量点程序对零件轮廓进行测量,得到实际点位, 通过实际点位与理论点位进行比较, 判断被测点位沿矢量方向的总误差是否满足公差要求[2]。其轮廓度误差评定是沿着被测面每点的法向将X、Y、Z 3个方向综合评定,采用公式:fi=I×(Xi-xi)+J×(Yi-yi)+K×(Zi-zi)(1)式中,I、J、K分别是X、Y、Z 3个方向的矢量分量,Xi、Yi、Zi为各点实际坐标值,xi、yi、zi为各点理论坐标值。
当面轮廓度为形状误差时,可根据测量点的坐标值,与曲面进行最佳拟合,达到所有测量点的最佳状态,进行最终的点位评定。
当面轮廓度为位置误差时,可根据测量点的坐标值,在所给定的位置方向上(所标注的基准上)不能进行平移和旋转,其他方向上可进行任意的平移和旋转,直到所有的点位达到最佳状态,进行最终的点位评定。轮廓度公差分析如图2所示。
如对下面工件进行检测:
根据曲面特征点的布局要求,在产品模型上提取被测部位的理论点位数据。利用矢量点的自动检测功能对这些点进行实际测量,用公式(1)计算出点的总误差,还可以通过观察每个实际测量点的坐标值, 分析出被测轮廓相对于理想轮廓的偏离状态。
线轮廓度的检测技术研究
目前,在做复杂的线轮廓度评价时,常采用牛顿迭代法等优化算法计算被测点到理论轮廓线的最近距离心,计算过程复杂,有些情况甚至无法求解。另外当整个轮廓曲线由多个表达式构成时,还需要先判断被测点所对应的轮廓表达式;对于已给出一系列型值点的轮廓常采用三次样条等函数来拟合理论轮廓,得到拟合的理论轮廓表达式后再依据前面的方法,计算出被测点的轮廓度误差,其中拟合过程必然会有精度损失[3]。
针对目前线轮廓度评价方法的繁琐性和局限性,本文提出了一种基于离散点的轮廓度评价算法,该算法主要计算点到点的最小距离,避免了较为困难的点到不规则曲线最小距离的计算。
线轮廓度误差是指实际被测轮廓线对理论轮廓线的变动量。按轮廓度误差的定义,最基本的评定原则需要满足最小包容区域原则。最小包容区域是指由2条平行曲线包容实际轮廓线时,具有最小宽度的包容区域。在线轮廓度误差的评定中,任何方法都要以该原则为基本原则,但由于直接采用该原则较为困难,常采用最小二乘等近似算法。线轮廓度的评价依据有无基准可分为有基准要求的线轮廓度和无基准要求的线轮廓度。本文以有基准要求的线轮廓度为例,论述基于离散点的轮廓度算法,对于无基准要求的线轮廓度同样适用。
当线轮廓度要求只在任意方向上评定时,其实际测量的要求同面轮廓度是基本相同的,但当线轮廓度要求在任意方向上和规定长度内评定时,其实际测量要求同面轮廓度检测有一定的差异。检测评定时,必须对任意曲线的长度进行控制,在规定的长度内评定线轮廓度,这样的要求,比不规定长度评定相对公差要求松些。本文主要讨论在任意方向上、规定长度内评定线轮廓度的方法。
根据所得到的离散点的理论坐标值和理论法矢量,结合三坐标测量机的自动测点功能,将所有的理论离散点进行自动检测,得到这些理论离散点的实际测量值。
利用离散点进行线轮廓度的评定,即将理论轮廓的离散点P与被测轮廓的离散点Q进行对比计算。首先,对于每一个Q,均在P中搜索一个与其距离最近的点。其次,计算出每个Q对应的最小距离d。最后,计算出数列中的最大值dmax,即被测轮廓的线轮廓度误差。
如图3中零件,在曲面上标注线轮廓度,下框格中,线轮廓度要求被测曲面上沿任一方向和任一200mm长度上,线轮廓度公差为0.200mm,目前CMM测量软件只是在某一平面内评定线轮廓度,无法评定沿任意方向的线轮廓度误差。
CMM检测线轮廓度是通过测量线上每一点的坐标值,并经过数据处理获得误差值,作出合格与否的结论。要评定沿曲面任意方向的线轮廓度误差是否符合精度要求,必须编制专用的数据处理程序。
假设某一曲线有A、B、C 3个测量点,计算A、B、C三点的误差,若误差大于公差则不合格,若小于则合格。然而,一般事先测量点数无法确定,因此,可采用另一种等效方法,即采用两点比较的方法代替三点或更多点比较的方式,例如(A、B 、C) 三点的误差值肯定是(A、B)、( A、C) 、(B、C)3组误差值中的一个,若其中有一个不合格,则不合格,若全部合格则合格。
通过任意两点有无数个平面,而每个平面与曲面都有1条交线,因此无法确定两点之间所在曲线的距离,只能用两点的直线距离代替曲线距离,这样不仅能够对线轮廓度更好地控制,而且使算法具有可行性。线轮廓度数据评价程序主界面如图4所示。
图4 线轮廓度数据评价程序主界面
复合位置度检测技术研究
复合位置度公差提供了特征尺寸组定位和特征尺寸在组内相互关系( 约束旋转和平移) 上应用位置度公差的方式。要求是通过使用复合特征控制框来注明的。
对于此类位置度,位置符号只填入1次即对所有水平框格都适用。其中特征控制框中的每个完整水平框格都可以分别检查。
复合位置度中包括组定位公差带框和特征相关公差带框。
组定位公差带框的公差带框约束相关于规定基准的旋转和平移。对特征尺寸组作为一组定位规定了较大的位置度公差。适用的基准特征应按给定的优先顺序参考,并起到将理论正确尺寸与基准参考框相联系的作用。
特征相关公差带框是由特征相关控制。它们控制了各特征尺寸在组内( 特征与特征的关系) 的较小的位置度公差。基本尺寸可用于组定位公差带框,而不适用于特征相关公差带框。
当复合特征控制框的下框格未规定参考基准时,特征相关公差带框可在由组定位公差带框建立和控制的边界内自由旋转和平移;如果在下框格规定了基准,它们控制特征相关公差带框可在由组定位公差带框建立和控制的边界内相关于基准的旋转;当规定了基准特征参考时,位置度框最上面框格规定的一个或多个基准特征时,应按相同的优先顺序约束坐标系的旋转。
复合公差有2个或多个框格。每个框格都建立公差带并约束显示在框格内的任何参考基准。第一框格内的参考基准建立所有适用旋转和平移约束相关于所参考基准。第二和后续框格内的参考基准仅建立旋转约束相关于所参考基准。
当框格内的参考基准空缺表示没有通过这些框格建立旋转和平移约束。对带有复合位置度公差的组特征的应用,通过第一框格建立组定位公差带,单独的特征相关公差带通过各后续框格建立。
例如测量孔位置度上框格为相对于A、B、C基准位置度,公差要求为φ0.25;下框格为相对于A、B、C基准位置度,公差要求为φ 0.10;
对于上框格位置度检测时,按A、B、C基准建立坐标系后,按照其特征元素与基准之间的关系,直接对位置度进行评价,相对于A、B、C基准不允许进行旋转和平移。
对于下框格位置度检测时,按A、B、C基准建立坐标系后,按照其特征元素之间尺寸关系,对位置度进行评价,相对于A、B、C基准不允许进行旋转。
公差带: 如图5中公差值前面带有表示直径的符号φ,则该位置度公差带的形状为圆柱;在测量时主要是通过测量孔的两端极限点的位置度误差来控制孔的位置度,当孔的两极限点的位置度误差合格时,孔的位置度合格。在评定其误差时,设各圆心的理论坐标为oi(xi, yi zi),圆心的实际坐标为Oi(Xi, Yi Zi), 则各孔两端极限点的位置度误差表示为=2(Xi−xi)2+ (Yi−yi)2。
下面举例说明,复合位置度的检测方法。
检测过程如下:
步骤1:将被测零件恰当地定位在三坐标测量机的工作台上(CMM工作面),如图5所示。
步骤2:图5中的零件是采用复合位置度控制孔组位置,就是由2个位置度联合控制孔组的位置,上框格为孔组公差带要求,4个φ0.25mm 的公差带,其几何图框相对于基准A、B、C而确定;下框格为各孔之间的进一步要求,4个φ0.12mm的公差带,其几何图框仅相对于基准A定向,对于A、B、C 3个基准都没有定位要求,因此它可在一定的范围内任意移动。孔的实际轴线必须同时符合上下框格的位置度要求,即只能位于φ0.25mm和φ0.12mm2个圆柱形公差带的重叠部分内,如图6所示。
步骤3:以基准A建立Z轴方向,用基准B建立X轴方向,且定义基准A、B、C 3个面的交点X=0、Y=0、Z=0,此坐标系为1#坐标系。
步骤4:对圆柱的轮廓进行测量,分别用每个圆柱面上的实际点位拟合成圆柱,共拟合4个圆柱。
步骤5:构造圆柱两端面,将被测圆柱分别与两端头平面相交,得到8个极限点。
步骤6:在1#坐标系下,通过观察每个极限点的坐标值就可以分析出被测孔相对于基准的偏离状态,用每个极限点的实际位置与理论位置求距离,该距离的2倍就是每个被测孔相对于基准A、B、C的位置度误差。
求下框格位置度误差, 位置度误差下框格有基准的测量, 如图6所示。
步骤7:在1#坐标系下,以1孔和2孔构造线建立X'轴方向,定义1孔X=10、Y=20,此坐标系为2#坐标系。
步骤8:在2#坐标系下,通过观察每个极限点的坐标值就可以分析出被测孔之间的偏离状态,用每个极限点的实际位置与理论位置求距离,该距离的2 倍就是每个被测孔之间的位置度误差。
当下框格位置度超差时,在上框格位置度合格的前提下,可以任意平移或旋转2#坐标系,直至下框格位置度达到最佳状态为止。
当上框格位置度和下框格位置度检测都合格的情况下,该复合位置度合格,否则该复合位置度不合格。
其他位置度检测技术研究
常用的其他位置度有同轴度、对称度、平行度、垂直度、倾斜度等,利用三坐标测量机进行数字化检测的原理是将这些抽象的形位误差测量,转换为相应的点位控制评定,并根据其相应的位置度算法,计算得出相应的位置度评定结果。
如对对称度的测量:
对称度是表示零件上两中心对称要素保持在同平面内的状况。对称度公差是被测要素相对基准要素所允许的最大变动量。零件上对称结构要素很多,如键槽的两侧面,V型槽,连杆滑块的两侧面及回转体表面等[5]。
下面举例说明,在三坐标测量机上对称度的检测。
(1)公差带:被测平面的对称度公差带为相对于基准中心平面对称配置,且距离为公差值0.1mm的两平行平面之间的区域,如图7所示。
(2)检测:根据面的特征点的布局要求,在产品模型上提取被测面上的理论点位数据。检测过程如下:
步骤1:将被测零件恰当地定位在三坐标测量机的工作台上(CMM工作面),如图8所示。
步骤2:在基准A(基准中心平面)上建立Z轴方向,且定义A基准Z=0。
步骤3:对面的轮廓进行测量,得到实际点位。
步骤4:根据公差带的类型,这些点的Z向公差可以分配为:+0.05/-0.05。
步骤5:通过观察每个实际点位的Z向坐标值可以判断对称度是否合格,还可以分析出被测平面相对基准平面的偏离状态。
针对复合面轮廓度的方法和复合位置度基本相同,主要是将面轮廓度转换为矢量点的检测,针对基准的标注在测量坐标系建立中的应用与复合位置度相同。
结论
数字化的概念在加工制造业中被广泛的推广应用,简单地利用测量机软件功能进行产品检测,虽然可以定量得出测量结果,但其测量结果不便于以后的工艺分析。研究形位公差数字化检测, 提出了利用离散点检测评定形位误差的方法,直观地反映出实物整个形体的质量及偏离方向, 不仅便于不合格品的返修, 而且可以促进工艺方法的改进, 具有潜在的经济效益。
复杂的形位误差在国际设计理念中已广泛应用,我国最新的设计中也在应用一些复杂的形位误差,但针对有些复杂的形位误差的概念,还没有很清晰的解释,例如,复合面轮廓度,规定范围内评定的线轮廓度等,需要我们进行研究学习,深入了解其概念及评定方法,从而研究出其相应的检测方法。
参 考 文 献
[1] 张学昌.基于点云数据的复杂型面数字化检测关键技术研究及其系统开发[D].上海:上海交通大学,2006.
[2] Pfeiffer A.Dasta analysis in the grid.era,nuclear symposium conference record,2003IEEE,2003:22-25.
[3] 侯宇,张竞,崔晨阳.复杂线轮廓度误差坐标测量的数据处理方法.计量学报,2002(1):1-3.
[4] 张进,王仲,李超,等.离散点的线轮廓度评价算法.光学精密工程,2008(11):2281-2285.
[5] 徐先懂,宋述稳.形位误差的数据处理.中国测试技术,2004(4):1-3.(责编 夏宛)
声明:本网站所收集的部分公开资料来源于互联网,转载的目的在于传递更多信息及用于网络分享,并不代表本站赞同其观点和对其真实性负责,也不构成任何其他建议。本站部分作品是由网友自主投稿和发布、编辑整理上传,对此类作品本站仅提供交流平台,不为其版权负责。如果您发现网站上所用视频、图片、文字如涉及作品版权问题,请第一时间告知,我们将根据您提供的证明材料确认版权并按国家标准支付稿酬或立即删除内容,以保证您的权益!联系电话:010-58612588 或 Email:editor@mmsonline.com.cn。
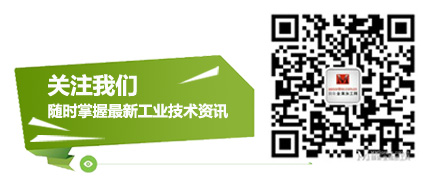
- 暂无反馈