ATCS PLC在机床控制中的应用
φ3500立式机床是一种自动化程度要求较高的机电设备,一般应用于冶金行业,车制各种大型工件;它通常采用继电器逻辑控制方式,设备的电控系统故障率高,检修周期长。随着技术的进步,这类控制系统已显示出越来越多的弊端。近年来PLC机在工业自动控制领域应用愈来愈广,它在控制性能、组机周期和硬件成本等方面所表现出的综合优势,是其它工控产品难以比拟的。如果用PLC控制技术对这些系统实施改造,则具有普遍的技术及经济意义。
2 方案选择
原设备为手动操作,根据使用部门的建议,在改造方案上维持改造前设备人一机界面的原始性,这样可以有效减少设备使用人员的误操作,不至于使设备的事故率在技术改造后有所增加。
系统的工作台变速单元依靠液压电磁阀来实现,并由机械传动部件不断地改变传输比,达到改变工作台转速目的。其变速操作相当繁琐,必须先让主机停车,选好速度后,微动使齿轮重新啃合再挂挡,最后重新启动。根据现场负载计算与理论分析,保留主拖动方式,用一台FRN15G95-4JE电压型通用变频器,对工作台电机进行速度换向控制。FRN15G954JE电压型通用变频器具有转矩矢量控制、转差补偿、电AVR自整定、负载转矩自适应等一系列先进功能,在无速度传感器的开环运行条件下,采用磁通矢量控制和电机参数自动测试等功能后,其调速性能达到甚至高于传统晶闸管供电的双闭环直流调速系统。原系统还有左右两个刀架,可纵向横向移动,通过电磁离合器与左右驱动电机连接。左右驱动电机有Y/△变换,因此有两级工作进给速度:I级0.29- 45.6m/min,II级0.58-91.2m/min。改造时,仍维持原方式。
3 PLC机型选择
3.1 输入输出点数
PLC控制系统的输入信号包括操作台控制输入、工作台和刀架各速度信号、分布在机床上各部分行程开关及变频器投入信号。共有64个输入点。
PLC的控制负载主要分成三类:一是10台交流电机正反转主接触器;二是用于左右刀架调速的离合器线圈(电磁离合器直接由PLC驱动);三是显示、报警负载(包括显示灯、声光报警器等);四是工作台调速输出(到变频器)。共56个输出点。
3.2 PLC选型
确定输入输出点后,还要进行PLC选型,本系统除了与变频器连接需模拟量外,全部为开关量,再考虑到性能价格比及输入输出点数,选用德维森公司ATCS系列PPC31型机, PPC31为模块化结构,系统配置灵活,编程功能强,性能价格比高。
4 系统设计
4.1 变频器设计
系统所有动作都有PLC控制。当PLC输出继电器out1=ON时,工作台正转;输出继电器out2=ON时,工作台反转。工作台共有16级速度。操作时,首先将二进制值存储在PLC数据区,当正反转时,操作台输入速度值,而PLC输出一路二进制值,经D/A转换到变频器的12号输入端,满足工作台调速要求。当out1 and out3=O N时,工作台点动正转;当out2 and out 3=ON时,工作台点动反转。点动速度用变频器提供的多段速指令选择。当电机过载缺相时,热继电器FR动作,使变频器THR端子OFF,可在瞬间封锁 U.V.W输出,同时闭合故障继电器30A-30C触点,经PLC输入继电器产生系统故障报警。
在快速制动过程中,一但电机反馈“泵升”电压使变频器母线电压达到800V时,制动单动BU功率模块立即导通,接入电阻R迅速释放电机储能,实现安全快速的制动。
4.2 软件设计
PLC通过编程器输入程序,达到控制目的。由于PLC工作过程是循环,程序执行速度快,在刀架进给双速电机时,需要通过Y/△变换实现变速,因此为了避免Y/△变换中电源短路,除了用互锁外,还必须设置切换延时,定为1S。同样,在横梁下降(反转)时,还需要回升(正转),因此也需要设置切换延时,以防电源短路。
声明:本网站所收集的部分公开资料来源于互联网,转载的目的在于传递更多信息及用于网络分享,并不代表本站赞同其观点和对其真实性负责,也不构成任何其他建议。本站部分作品是由网友自主投稿和发布、编辑整理上传,对此类作品本站仅提供交流平台,不为其版权负责。如果您发现网站上所用视频、图片、文字如涉及作品版权问题,请第一时间告知,我们将根据您提供的证明材料确认版权并按国家标准支付稿酬或立即删除内容,以保证您的权益!联系电话:010-58612588 或 Email:editor@mmsonline.com.cn。
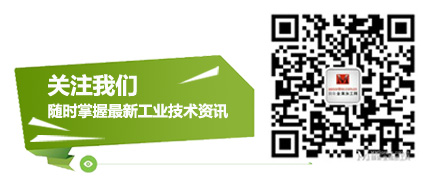
- 暂无反馈