变频器在精密深孔机械加工中的应用
在难加工材料上加工精密深孔,历来都是机械加工中的难点之一。长期以来,较为普遍的方式为采用钻原扩原铰的工艺。
以后虽有枪钻、BTA钻、喷吸钻等深孔加工工具和方法,在加工效率和加工质量上有所进步,但是如断屑、排屑、刀具磨损过快等问题仍然存在,依旧不能满足高精度、高质量、高效率、低消耗的现代化工业生产要求。采用振动切削深孔加工技术与交流变频调速技术相结合,对现有机床进行适当的改造,将对深孔加工的效率和精度有一个明显的提高,并且加工质量也更为稳定。
1、变频器调速原理
变频器是多种技术和理论综合发展的产物,一般包括主电路、控制、检测和保护等部分。主电路部分包括整流、滤波稳压、逆变等三部分,还留有直流平波电抗器、制动电阻、制动单元等接口。控制部分一般包含数字信号处理器和(或)高速微控制器,它们共同完成控制算法的实现、控制的动态调节、PWM控制信号的输出。监测部分包括对电压、电流、温度等变量的检测,并判断是否超过设定值以便进行系统保护。一般所说的变频器是指适用于工业通用电机和一般变频电机,并由一般电网供电(单相220V/50Hz、三相380V/50Hz)作调速控制的通用变频器。此类变频器由于工业领域的广泛使用已成为变频器的主流。
将交流变成直流,经过平滑滤波,再经过逆变电路,把直流变成不同频率的交流。使电动机获得无级调速所需要的电压、电流、频率。这种变频器叫交-直-交变频器,交-直-交变频器比较好的是采用双极性正弦波脉宽调制方法进行控制。这种脉动转矩小,扩展了调速范围,提高了调速性能,因此,在数控机床的交流驱动中得到了广泛应用。
2、振动切削深孔加工的基本原理
振动切削深孔加工也就是通常说的振动钻削,它是把振动切削技术应用于钻孔加工,在传统深孔加工的基础上,给刀具附加一定频率和振幅的有规律振动,刀具一边进给、一边振动的同时完成钻削作业,将使切削厚度产生周期变化,达到控制切削形状和大小的目的,从而有效地解决了深孔加工中的断排屑难题,是改善深孔加工质量,提高加工效率的一种先进的工艺方法。该方法针对加工材料和不同钻孔规格,只要对主轴转速n、进给量s、振动振幅a和频率f进行适当的选择和匹配,既可有效地控制切屑的形状和大小,满足断续切削的要求。理论断屑公式如式(1)所列,即
根据这一理论,对机床进行振动深孔钻镗床的改造,把先进的振动切削深孔加工技术与交流变频调速技术有效地结合起来,形成一种专用的精密深孔加工系统,解决孔径小于60mm、孔深达到4000mm、长径比L/D大于70的非回转类零件深孔加工中存在的问题。
3、振动切削深孔加工对机床改造的要求
一般深孔加工由于加工材料、孔深、孔径大小不同,也就有不同的刀具和不同的切削速度的要求。所以,为了满足生产企业日益广泛的加工需求,就必须增大主轴电机的调速范围,同时为了满足振动切削的要求,振动电机的调速范围也必须成倍扩大。
就我国目前所使用的机床来看,主要采用变级多速三相异步电动机和在机床床头箱内用电磁离合器来变换齿轮达到变速的目的,无法实施精度较高的恒线性控制,还不能适应那些要求主轴转速高低跨度大,高,中,低速兼有的零件加工需要。而对于一些采用直流调速拖动的数控机床,虽然可以实现无级调速,但必须经常维护换流电刷,使用成本较高,且电机最高转速受限制。因此,我们把变频调速技术应用到数控机床上,通过变频器对电机进行直接变速传动,可实现无级平滑调速,减小了大电机启动时对电网的冲击;提高了功率因数,节能效果显著;提高了加工效率和精度。
要采用振动深孔钻削,就需要对深孔钻镗床或者对普通机床进行适当的改造才能得以实现。若对普通车床进行改造,就需要在原车床的基础上增加振动装置、授油器、供油系统、电气控制系统等四大部件。若对深孔钻镗机床进行改造时,则只需增加振动装置和控制系统,其它部位稍作改动即可。其中,电气控制系统是实现振动深孔钻削的核心部件。
4、控制系统的原理
根据振动切削理论断屑公式,在进给量s和振动振幅a为定值时,要使式(1)成立,必须使振动频率f和主轴转速n保持特定的比例,频转比的控制是整个控制系统的核心,它的性能直接决定着断屑效果和加工过程的平稳性。为了满足振动切削深孔加工的高精度要求,确保加工过程中频转比保持相对稳定,必须采用以主轴电机的转速作为给定量,使振动轴的转速作为反馈量的电动机闭环调速控制系统。一般情况下,调速系统都采用转速、电流双闭环系统,但是通用变频器本身有限流保护,所以采用速度单闭环控制,不但结构简单,而且可取得良好的综合性能指标。
本系统采用如图1所示的控制方案,通过测速传感器检测主轴转速n和振动转速f,与事先设定好的速度比率(即频转比参数)k=f/n进行比较,通过PI调节,再将比较的差值转换成PWM电压信号发送给变频器,通过变频器对振动电机转速进行控制,使其跟随主轴电机在不同的切削负荷下转速的变化,从而使f/n维持设定比例k,保证数控车床的加工精度和稳定性。
5、控制系统的硬件结构
整个控制系统是由频转比控制器(80196KC单片机)、变频器和交流电机三个重要部分组成,如图2所示。在该系统中,频转比控制器通过检测主轴转速和振动转速,按设定的频率转速比,通过控制交流电机变频调速器的外部电压控制端来调节振动电机速度,从而保证维持设定的频转比值。
其中主电机带动一级同步齿形带传动,带动主轴(刀具)旋转,振动电机驱动连杆机构实现主轴(刀具)的轴向振动,当主电机运转时,主轴电机与振动电机均由变频器控制实现主轴转速和振动频率的无级调节,且振动电机与主轴电机之间运转为闭环控制,即通过控制器设定比率控制振动电机频率;振动振幅采用双偏心机构来实现,可根据所选进给量的大小来调节。
根据主轴电机最大转速1000r/s的要求,该控制系统频转比率应在0.00~5.00之间无级可调。在电机传动中,为了保持调速时电机的最大转矩不变,该系统必须保持频率和电压之比为常数。在出现异常情况下,系统必须具备应急故障处理功能和发出报警显示。
6、变频器的选型
变频器的选择,必须根据应用场合及负载特性的具体情况,并从容量、输出电压、输出频率、保护构造、V/F(电压/频率)模式、电网—逆变器的切换、瞬停再启动等诸方面进行综合考虑,进而选择满足要求的机种、机型。一般通用型V/F控制方式的变频器,主要考虑输出功率和电流,选择必须等于或大于被驱动异步电机的功率和电流的变频器。我们选择了西安春日电器有限公司的KVFC系列通用变频器,其中11kW的主轴电机选用KVFC-4110(11kW/400V),1.5kW的振动电机选用KVFC-417(1.7kW/400V)。
7、变频器功能的设置
变频器设计了充分的频率设定功能和频率控制接口。变频器的频率输出可以用数字键盘设定,如基本频率、启动频率、最大最小频率、跳跃频率及宽度、多段运行频率值以及加减速斜率等,利用键盘的上升下降键、起停健可以实时改变电机的速度。另一种办法是利用输入接口端子来控制电机的运转,如正转指令、反转指令、复位输入、加减速时间的转换、多段运行频率的选择、自由运行等控制端子。这时的运行频率值可以用电压输入0~5V或0~10V来设定,也可以用(4~20)mA的电流信号来设定。
由于我们采用单片机作为控制器,其工作电压为5V。因此,使用单片机输出0~5V连续变化的模拟信号,通过变频器VRC端子控制变频器实现主轴电机和振动电机的变频无级调速。变频器的主要功能参数设置如表1所示。
变频器参数的设定也是系统稳定运行的关键。若系统运行时电机转速太低,转矩过小,由于负载的作用,会使电机转差损耗大,发热厉害,严重时会导致电机烧毁,因此必须给电机设定下限频率或者设置自动转矩提升功能。加、减速时间整定也是参数整定的关键项,如果加、减速时间设定不合理,变频器会出现过电流或过电压而自动停机。因此,加速时必须限制频率的上升率以防止过电流,减速时必须限制频率的下降率以防止过电压。
8、控制系统的软件设计
软件功能是以系统的性能要求和硬件的设计为基础来设计的。针对振动切削深孔加工系统的功能要求,软件系统需要完成以下几个方面的任务:有主控程序、主轴电机测速模块、振动电机测速模块、振动电机控制模块、伺服电机控制模块、显示子模块、设定参数读取和PI控制算法以及故障保护模块等任务。振动电机控制模块负责实时输出PWM电机控制信号,根据给定的比率控制振动电机转速,使其保持f/n越k。
9、结语
本文结合振动钻孔技术和交流变频调速技术,对普通机床进行改造,利用单片机为数控机床的控制器,设计完成了振动切削深孔加工控制系统。在生产实践中得到了应用,证明这种复合加工技术能有效地解决深孔加工中的断屑、排屑这一主要问题,因而可简化刀具结构,降低对切削液系统的要求,可相对缩小排屑空间而提高钻杆强度和深孔钻削系统的刚性,保证加工的稳定性和质量。尤其对难加工材料的深孔钻削,效果更为明显,是在难加工材料上进行深孔加工的最有效工艺措施。
声明:本网站所收集的部分公开资料来源于互联网,转载的目的在于传递更多信息及用于网络分享,并不代表本站赞同其观点和对其真实性负责,也不构成任何其他建议。本站部分作品是由网友自主投稿和发布、编辑整理上传,对此类作品本站仅提供交流平台,不为其版权负责。如果您发现网站上所用视频、图片、文字如涉及作品版权问题,请第一时间告知,我们将根据您提供的证明材料确认版权并按国家标准支付稿酬或立即删除内容,以保证您的权益!联系电话:010-58612588 或 Email:editor@mmsonline.com.cn。
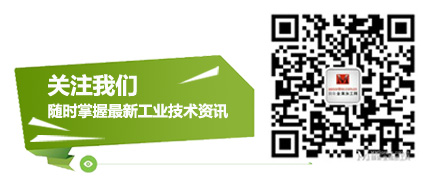
- 暂无反馈