汽车制造装备可靠性关键技术研究
高速、高效、高精度、高可靠性,是现代数控机床发展的主要趋势,也是数控机床进入汽车制造装备的基本要求。要提高加工效率,首先必须提高切削和进给速度,同时还要缩短加工时间。要确保加工质量,必须提高机床部件运动轨迹的精度,而可靠性则是上述目标的基本保证。
数控机床在汽车制造装备中占有重要的地位。国产数控机床近几年虽然取得了可喜的进步,但与国外同类产品相比还存在不少差距。从总体来说,国产数控机床在产品的品种上、性能上、可靠性上还不能满足作为汽车装备的需要,特别是高档数控机床。因而,造成近几年数控机床进口逐年激增,而国产数控机床的市场占有率不高,而且在逐年下降。
在精度方面,以加工中心加工典型件的尺寸精度和形位精度为例,对比国内外的水平,国内大致为0.008~0.010mm,而国际先进水平为0.002~0.003mm,按上述统计规律分析差距约为15年左右。
在可靠性方面,以平均无故障工作时间为例,国际先进的机床平均无故障工作时间(MTBF)一般都在5000小时以上,而国产机床仅在600小时左右。国产机床故障率较高是用户反映最强烈的问题之一。按目前汽车制造装备的需求,MTBF至少应在3000小时以上。可见国产数控机床的可靠性必须要尽快上一个台阶,否则必将被汽车制造装备业所淘汰。对数控机床新产品进行可靠性设计,对现有产品进行可靠性增长,提高数控机床可靠性,才能使国产数控机床在汽车制造装备领域占有一席之地。
产品的可靠性是指在规定的时间内规定的条件下完成规定功能的能力。数控机床系统属于机、电、液一体化的复杂系统,其可靠性问题涉及的范畴很广。包括系统可靠性问题、电子元器件可靠性问题、结构可靠性问题、机构可靠性问题。开展数控机床可靠性工作,可以借鉴航空航天等领域可靠性的方法和经验,但同时数控机床可靠性也有很强的特殊性,必须开展可靠性研究工作,攻克其中的关键技术。本课题将针对数控机床可靠性关键技术进行研究。
高速、高精度的机、电、液一体化复杂系统可靠性分析设计及试验技术,是可靠性学科的前沿课题。研究数控机床系统可靠性分析设计方法、可靠性试验及可靠性增长技术,为开展数控机床系统可靠性分析设计及试验奠定理论方法基础,有非常现实的需求。
随着数控机床向高速、高效、高精度的方向发展,机床结构与机构的动态性能问题尤其突出,是制约机床高速高精度发展的瓶颈,因此研究机床结构与机构的动态可靠性不仅有很强的学术意义,而且也具有重要的应用价值。建立机床动态可靠性设计方法是目前机床设计的当务之急。机床结构与机构的动态可靠性包括动态强度(寿命)可靠性和动态精度可靠性。结构与机构动态强度可靠性是机床可靠性的重要方面,直接影响整个数控机床系统的可靠性。而结构与机构的动态精度可靠性设计是保证机床精度的根本途径。
声明:本网站所收集的部分公开资料来源于互联网,转载的目的在于传递更多信息及用于网络分享,并不代表本站赞同其观点和对其真实性负责,也不构成任何其他建议。本站部分作品是由网友自主投稿和发布、编辑整理上传,对此类作品本站仅提供交流平台,不为其版权负责。如果您发现网站上所用视频、图片、文字如涉及作品版权问题,请第一时间告知,我们将根据您提供的证明材料确认版权并按国家标准支付稿酬或立即删除内容,以保证您的权益!联系电话:010-58612588 或 Email:editor@mmsonline.com.cn。
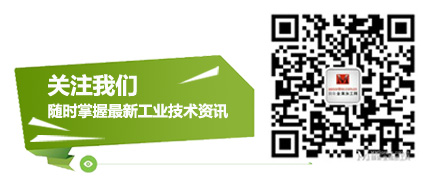
- 暂无反馈