超大型数控钻床在管板加工中的应用
1、管板加工技术
管板被广泛应用于石化、锅炉、制冷、汽轮机等行业,而管板加工是热交换器制造的重要工序,在换热器的生产中占有很重要的地位。管板加工的精度,特别是管孔间距和管径公差、垂直度、光洁度都极大地影响换热器的组装和使用性能。随着化工设备、电站的大型化,其热交换器直径也变得越来越大,直径为4m~5m的管板很常见,有的直径达到7m左右。大型管板的特点是管孔数量多、密、孔径小、深、精度和光洁度要求高,这就对管板的加工提出了很高的要求。
2、传统的管板加工方法
尽管各个厂家的加工工艺略有差别,但总的来说,不外乎,先划线(因划出的线成网格状,称网格线),打样冲点,用小钻头钻小孔,再正式钻孔,若孔壁光洁度要求高的,还要铰孔,最后倒角。分析一下这套工序,先说划线,若是标准管板(蜂窝状)还好说,若是图形复杂的,划线就很费事。再说钻孔,操作工人用摇臂钻钻孔,调整摇臂定位,再落下钻头,再抬起钻头重新调整摇臂定位,钻一个孔要做好几个动作,而操作工人的劳动强度较大,效率不高。总而言之,传统的管板加工方法,精度低、费时、费力,使得管板加工成为整个生产过程中的一个瓶颈,一谈起管板加工,人们就直皱眉头。
3、先进的管板加工方法
其实,制约管板加工的一个主要问题是设备问题。在传统的管板加工中,摇臂钻是其主要设备。由于其手动操作特性,操作方法比较固定,很难有潜力挖掘。尽管可以用钻模等办法来提高效率,但解决不了根本问题。只有从设备上想办法,才能从根本上解决问题。国外管孔加工已普遍使用多轴数控钻床,不再使用摇臂钻,数控平面钻床能够代替人工划线、钻孔,可以大大提高加工精度和效率。我国近几年也开始实现这类钻床的国产化,但大多数厂家的产品,床身较小(2m~3m),主轴(1个或两个)不多。不能加工大型管板。不能完全替代进口产品。因此对于要求加工精度高的大型管板(超过7m),只能到国外去加工。而进口数控机床,价格昂贵,安装周期长,不易维修,并不一定适合中国的国情。人们迫切需要国内机床厂家生产出超大型数控钻床,以满足管板加工厂家的需要。
4、国产超大型数控钻床在管板加工中的应用
山东法因数控机械有限公司是一家致力于数控机床研发、生产的厂家,自从2003年研制成功第一台超大型数控钻床PD4040A/4以来,技术日臻成熟,已经生产了几十台超大型数控钻床,分布于全国各地。有的用户,一次就从法因数控购进了两台超大型数控钻床。这种数控钻床,采用动力头龙门移动式结构,多主轴(2到12个主轴),用户可在订货时,自行选择工作台面的大小及主轴的多少。可加工工件的最大尺寸可达到7m×7m(根据需要,可生产加工更大管板的机床)。其主流产品是加工最大尺寸4m×4m的PD4040型及7m×4.5m的PD7045型,一般采用4个主轴,有四个数控滑台式钻削动力头,并能独立数控移动,动力头的最小间距为500mm左右,一次性最大实心钻孔直径为f50mm(可选),装夹工件厚度200mm左右(可选),零齿隙双面驱动,整机有十个数控轴(可选),具有CAD/CAM自动转换程序,既可用CAD文件转换成加工程序,又可用手工编程,可进行数控钻孔、扩孔、铰孔、倒角等工序的加工。从而省略了人工划线,不必再用手工钻孔,使得管板加工技术有了一个质的飞跃。大大提高了加工精度和生产效率。因其高效率,使得以前一个月才能完成的工作,现在几天就能完成。彻底消除了在整个生产过程中管板加工的瓶颈。
5、超大型数控钻床的具体使用方法
法因数控生产的超大型钻床采用PC (电脑)+ CNC(数控单元) + PLC(可编程控制器)的控制模式。在PC中输入管板的CAD图形,然后转化成DXF文件,然后运行法因数控自主开发的上位机软件,打开这个DXF文件,输入工件的基准点坐标,便可自动生成零件程序和零件程序信息。零件程序由机器生成,避免了人工编制零件程序容易出错的情况。然后,通过PC和CNC之间的通讯软件WINDNC把零件程序传入CNC,然后从CNC中调出零件程序进行加工。通过PC和PLC之间的通讯,监控机器的运行状况。
6、总结
在管板加工中正确地选用超大型数控钻床,是提高加工精度、生产效率的必由之路。及早投入使用超大型数控钻床,对于提高产品质量、增加产品科技含量、提高企业的竞争力、培养数控应用人才具有积极的意义。
声明:本网站所收集的部分公开资料来源于互联网,转载的目的在于传递更多信息及用于网络分享,并不代表本站赞同其观点和对其真实性负责,也不构成任何其他建议。本站部分作品是由网友自主投稿和发布、编辑整理上传,对此类作品本站仅提供交流平台,不为其版权负责。如果您发现网站上所用视频、图片、文字如涉及作品版权问题,请第一时间告知,我们将根据您提供的证明材料确认版权并按国家标准支付稿酬或立即删除内容,以保证您的权益!联系电话:010-58612588 或 Email:editor@mmsonline.com.cn。
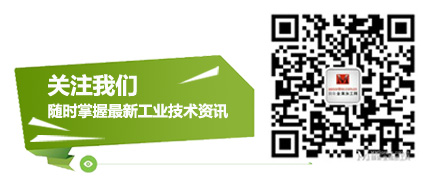
- 暂无反馈