数控机床单向定位功能的实用分析
数控机床的单一方向定位功能也称精密定位功能,一般简称单向定位。指数控坐标轴以预先设定的一个方向完成定位,定位方向与运动方向无关,在准备功能中用G60表示。
1 单向定位的执行过程
如果在从A点向B点定位的程序段中指令了G60,CNC先判别设定的定位方向与A点到B点的运动方向的关系。如果方向相反,则指令运动部件多走一段过冲量L,到达B’再反向向B点完成定位;方向相同时,也要在距离B点L处停一下,再向前完成定位。定位方向和过冲量大小由参数设定。
一般认为,当需要排除间隙进行精密定位,或加工精度接近机床定位精度的孔时,应采用单向定位G60功能。
2 单向定位功能的实际效果验证
我们在加工中心上使用该功能时,发现当设定的过冲量太小时,反向定位误差较大,而且全部表现为欠行程。增大过冲量设定值到某一值后,使用该功能的效果与使用快速定位G00没有区别。同向定位时,设定的过冲量大小不影响定位效果,与使用G00没有区别。
在一台V600型立式加工中心X轴做单向定位实验的数据。该轴为工作台左右移动,工作台面积800mm×400mm,采用两条铸铁贴塑导轨副,滚珠丝杠直径40mm,两端固定支承并预拉伸,采用半闭环控制方式。定位距离200mm,分别用指令G60反向、G60同向、G00反向、G00同向,在快速空载条件下完成定位。表中0.005mm左右的误差属变值随机性误差。可以看出,设定过冲量2mm反向定位时都产生了0.04~0.02mm的负定位误差。同向定位和设定过冲量大于3mm时,定位误差与使用G00没有区别。
3 实验结果分析
现代数控系统都具备间隙补偿功能,数控轴接受反向运动指令时,间隙补偿软件自动发生一定数量的补偿脉冲,使运动部件越过间隙和变形后,再向指定点移动。从这个意义上说,G60排除反向间隙的作用没有实际意义。因此,过冲量较大时,使用G60反向定位的效果与G00反向定位和G00同向定位的效果没有区别。
过冲量设定值较小时,G60反向定位出现欠行程(即少走)与进给系统的惰性变形有关。
目前市场最普及的中低档数控机床一般都采取半闭环控制方式,位置反馈信号取自伺服电机轴或滚珠丝杠轴。进给系统刚度不足或有变化、摩擦力变动、加减速时惯性力的大小、由于表面粗糙度和硬度不均匀引起的接触变形等因素的影响都没有被包含在位置控制环内。机床出厂时,在快速空载条件下向若干目标点定位。一般目标点距离都大于50mm,在这段行程内,运动部件足以加速到快速定位的速度。然后测出这个特定条件下各目标点正反向时的定位误差,由此确定间隙补偿和螺距误差补偿数值,存入CNC记忆装置,作为以后自动运行时的误差补偿信息。因此机床出厂后的精度情况还包含了特定条件下进给系统惰性变形的影响。称之为“惰性变形”,是因为运动部件停止速度为零后,变形依然存在,直到下次运动才打破这种平衡状态。与本文所述问题有关的惰性变形主要由摩擦力变化和加减速时惯性力变化引起。当过冲量设定值较小、采用G60反向定位时,如图实线所示,A点到B’点的距离较大,运动部件可以加速到快速定位速度。在接近B’点的减速过程中,进给系统受惯性力的影响产生拉伸,储存了较大的变形量。在B’点反向时,CNC软件补偿电路自动加入一个补偿值。从某种意义上说,这个值是从B’到B点间快速定位状态下的摩擦力和减速时的惯性力共同作用下形成的,是A点到B点和B’点到B点间两次拉伸的惰性变形量的差值。但是由于B’点到B点距离太小,部件移动速度很低,产生的摩擦力和减速惯性力与出厂前测定间隙补偿值的条件相去甚远。这时加入的反向间隙补偿值没有起到补偿作用,反而造成部件停止时越过B点,形成负定位误差。
4 结论
数控机床应慎用单向定位G60功能,一般使用G00即可。
使用单向定位功能时,应检查参数中过冲量设定值是否足够大。根据我们数次实验,过冲量合理值与快速定位速度有关,可取L≥V/5000(mm),其中V为快速定位速度(mm/min)。
因为缺乏定量分析和深入研究,文中所述单向定位反向时欠行程的原因和过冲量的最小值计算尚有推敲之处,欢迎读者提出宝贵意见。
声明:本网站所收集的部分公开资料来源于互联网,转载的目的在于传递更多信息及用于网络分享,并不代表本站赞同其观点和对其真实性负责,也不构成任何其他建议。本站部分作品是由网友自主投稿和发布、编辑整理上传,对此类作品本站仅提供交流平台,不为其版权负责。如果您发现网站上所用视频、图片、文字如涉及作品版权问题,请第一时间告知,我们将根据您提供的证明材料确认版权并按国家标准支付稿酬或立即删除内容,以保证您的权益!联系电话:010-58612588 或 Email:editor@mmsonline.com.cn。
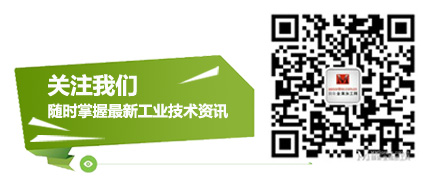
- 暂无反馈