立式双轴车削中心助力高效、高柔性加工
随着机床产品呈现出多轴化、复合化的发展趋势,并具有高效、多能和高精度的特点,东风汽车有限公司设备制造厂开发出对置双主轴立式车削中心,该机床可适应常用金属材料零件两端完全粗、精加工的高柔性、高精度加工,可实现全自动生产,并能很方便地连入自动生产线中,或者与同类机床串联形成新的具有高度柔性的加工自动线。
汽车、摩托车生产中存在大量轴、盘毂类回转体零件加工,往往数量大、品种多、要求高、工艺内容复杂,对车削设备提出了高效率、高柔性、高精度和多功能的要求,促进了车削设备的快速发展。许多刀辅具、电力驱动及控制、传动及测量等方面的新技术在其中得到应用,相关技术的发展也使得机床结构变得多种多样。
国外先进机床行业在数控车削中心的设计制造上技术成熟,其机床产品呈现多轴化、复合化的发展趋势,具有高效、多能和高精度的特点,代表了此类机床的发展方向。顺应这一发展趋势,我厂开发了对置双主轴立式车削中心,填补了国内此类设备空白。
机床总体布局和性能特点
引入全新立车设计理念,结合主轴倒置立车与传统立车结构形式,采用克服传统车床缺陷的机床结构布局方案,机床设计目标期望满足下列要求:
1. 高度自动化从而实现高效率,易于自动化连线。
2. 易于排屑,可靠定位,从而有利于加工自动化和加工质量的保障。
3. 适应常见金属零件两端完全粗、精加工的高柔性、高精度车削。
4. 先进技术的应用(大扭矩电主轴开发应用、高速度高精度进给系统开发应用以及动力刀架应用等)和先进的技术指标,适应国内机床应用维护水平的进步。
机床由床身、十字滑台、移动倒置机床主轴I、电动刀架I、固定正置主轴II、伺服动力刀架II、下料机械手、电气、液压、自动集中润滑、气路和自动冷却排屑系统等部件构成,根据具体零件加工条件,另配备相应刀辅具、夹具和上下料自动滚道,编制相应数控加工程序,即构成完整的自动化制造系统。
机床工作循环为:工件通过上料机动滚道到达上料位置→主轴I下行(Z1轴),上料油缸顶起工件实现端面定位,夹具I由回转油缸驱动夹紧→主轴I抓起工件沿 Z1、X1轴运行到刀架I加工区间→工件按程序加工→主轴I沿Z1、X1轴运行到主轴II,将工件放置主轴II,夹具II夹紧,主轴I 返回进入下一循环→刀架II沿X2、Z2轴运行到主轴II→工件按程序加工→夹具II松开,刀架II安装台上的下料机械手抓起工件沿X2、Z2轴运行到下料滚道并放下工件→下料机动滚道将工件送出机床。
由此显见,主轴I(夹具I)和刀架II的二坐标运动除完成切削进给功能外,还兼有自动上下料运动的功能,配备自动滚道后,全自动化生产变得简便易行,数控的主轴和进给轴运动保证了加工的灵活性。加工盆形工件时盆形向下,刀架I加工盆内特征,刀架II加工盆外特征,排屑顺畅,定位可靠,利于加工。对置双主轴+上下双刀架配置简单,实现工件两端完全加工,比较两台单轴立车组线,机床部件和占地面积更少,工件输送更简单、可靠,这些构成了机床结构最大的优点。
比较国外类似机床,本机床结构吸取了其优点,且主要技术性能指标已处相同水平,各进给坐标轴快进速度达40m/min,加速度达0.4g,定位精度和重复定位精度分别达0.008mm和0.005mm。
机床可加工工件最大直径φ350mm,最大高度250mm,两刀架均为8刀位,足以满足较复杂工件加工,配置伺服动力刀架,更可以对工件进行铣镗、钻孔、攻丝等加工,也可配置自动检测系统以具备刀具补偿和自动对刀功能,丰富、灵活的配置极大地满足了功能集成化、多工序工艺复合化的要求。
主要技术要点
1. 大扭矩车削电主轴的开发
立车主轴I需要快速移动,因此采用伺服电主轴驱动方式,比较传统机械主轴,其结构简单、体积小、重量轻、噪音小和传动惯量小,快速响应好,能实现极高的速度、加速度。
一般立车主轴上装较大夹具及工件,要求电机转速相对较低、扭矩相对较大,这一点与加工中心用电主轴显著不同,为此专门开发了本机床使用的电主轴,其转速额定1000r/min,最大2800r/min,扭矩额定260Nm,最大340Nm。
主轴尾端装有齿轮式绝对编码器,用于主轴转速和周向位置控制反馈,实现主轴C轴功能,使得机床具备周向特征加工功能,如钻孔、攻丝和铣槽等。
车削工件环状端面时,往往采取恒线速、变转速切削,直到限制转速后再恒转速切削,有利于提高效率和表面加工质量。配置德国INDRAMAT公司MTC200-R数控系统和DIAX04系列全数字交流伺服系统,使其得以方便实现。
采用进口精密角接触球轴承组,轴承采用全寿命免维护高级脂润滑,采用气密封,0.1MPa压力气流经端盖与主轴表面间隙外泄,阻挡污物进入,空气过滤精度0.001mm且经过干燥,这种密封比接触式密封和迷宫密封效果更好。
内装主轴电机作为高功率密度的伺服电机,电流较大,定子绕组电流和转子感应涡流产生大量热量,进而影响到轴承温度,对其强制冷却是必需的。主轴箱体设计了通过转子、轴承外部的水冷通道,采用压力低于0.3MPa温度低于40℃的水强制冷却,水中加防锈剂。水冷系统的可靠工作极为重要,水冷系统具备温度、压力监控报警,防止主轴损坏。
机床自动化运行,采用进口回转油缸和液压动力卡盘。
主轴箱体采用铸造铝合金材料,重量比铸铁减轻 60%,减小惯量利于提高加速性能,同时利于主轴散热。考虑硬度较低,容易擦伤,其主轴孔不宜直接安装配合较紧的轴承,主轴孔内衬以钢套,确保可多次高精度重复装配。箱体壁内加工出气、液通道孔,管线全从主轴尾端接入,整齐美观。
主轴旋转部分经动平衡,等级G2.5,主轴高速区间运转平稳,无振动,利于使用寿命和加工质量。
2. 高速、高精度进给系统开发
进给系统包括X1、X2、Z1、Z2四轴伺服控制直线运动,完成两个工位的进给功能。
采用进口高刚性精密滚柱直线导轨,满足粗加工高负载和精加工高精度两方面要求;使用进口光栅尺作为滑台位置测量反馈元件,组建机床全闭环控制系统。
使用伺服电机和进口精密滚珠丝杠组成进给运动系统,对传动系统中电机负载、惯量匹配性能和系统刚性进行精心设计校核。各轴负载惯量与电机转动惯量之比控制在1.0~1.5之间,保证其运动响应迅速;采用丝杠两端固定并对丝杠预拉伸,提高系统刚度,保证实现微细进给。
3. 电控系统
配置INDRAMAT公司MTC200-R数控系统,该系统具有高性能、高柔性和高可靠性等特点,有丰富的NC编程指令集,可以满足各种通用、专用机加工机床的加工要求,该数控系统还集成了PLC控制器、PLC编程器,人机接口等功能;配置INDRAMAT公司的DIAX04系列全数字交流伺服系统,该系列伺服系统具有高精度、高速度和高可靠性等特点,并具有完善的故障诊断、状态提示功能;配备10.4in(1in=25.4mm)彩色液晶TFT显示器作为人机接口,实时显示机床的状态,包括各伺服轴的运动速度、当前位置、各机床检测开关的状态以及执行元件的状态等;该机床还有操作提示功能、故障诊断和显示功能,指导操作及维修人员进行使用、维修机床。
结语
新型立式车床具有结构紧凑、敞开性好和排屑流畅的特点,可适应常用金属材料零件两端完全粗、精加工的高柔性、高精度加工,可实现全自动生产,并能很方便地连入自动生产线中,或者与同类机床串联形成新的具有高度柔性的加工自动线。该机床于2005年成功研制后,各项性能指标达到预期目标,投入生产使用良好,并获得2006年中国数控机床展览会春燕奖二等奖、2007年中国汽车工业科技进步三等奖项。
声明:本网站所收集的部分公开资料来源于互联网,转载的目的在于传递更多信息及用于网络分享,并不代表本站赞同其观点和对其真实性负责,也不构成任何其他建议。本站部分作品是由网友自主投稿和发布、编辑整理上传,对此类作品本站仅提供交流平台,不为其版权负责。如果您发现网站上所用视频、图片、文字如涉及作品版权问题,请第一时间告知,我们将根据您提供的证明材料确认版权并按国家标准支付稿酬或立即删除内容,以保证您的权益!联系电话:010-58612588 或 Email:editor@mmsonline.com.cn。
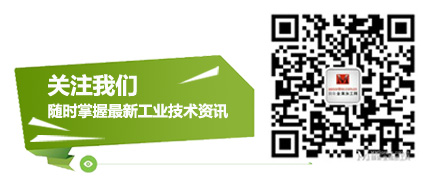
- 暂无反馈