手机模具电火花机床加工案例
手机外壳按键的加工有3个关键的技术要求:一是表面粗糙度要好,需要达到Ra0.2mm左右或者更高;二是电火花成形加工出来的表面的粗糙度一致性要非常好。目前各大手机厂商对外壳件的表面纹路都有非常苛刻的要求;三是对加工速度的要求。
我们采用了FO 350 SP电火花机床来加工这个工件。FO 350SP机床是电火花产品线中的中高档机床。该机型行程:XYZ轴:350mm×250mm×300mm;最大加工电流:64安培;最佳加工表面粗糙度Ra0.1mm;工件材料:S136(HRC52);外形尺寸95×40mm;型腔深度:8mm;采用一粗一精两个铜电极加工,粗加工电极的缩小量0.2mm,精加工电极的缩小量0.1mm。最后的结果,粗加工时间6小时40分,精加工时间15小时4分,总的时间21小时44分钟。由于该机床标配了抛光电源,最后加工后的粗糙度达到了Ra0.22mm。
该机型还同时配备了第四代放电监控专家系统,能实时监测放电的每一个火花回路,并实时加以优化,最大程度地提高加工效率和减少电极的损耗;PCE能量控制专家系统能根据电极加工面积的变化,实时地调整加工电流,达到所有加工型腔面的完整一致的表面质量;SPAC短路保护控制专家,这是阿奇夏米尔的专利专家系统,通过很短的特殊放电及时消除可能的短路加工,从而提高了加工效率。微细电源极大地减少了电极的损耗,达到减少电极数量,从而降低了加工的成本;全新的平动专家系统,通过新的平动计算方法,大大提高了精加工的加工效率。由于上面这些先进智能的专家系统,充分保证了加工后的工件不仅粗糙度达到要求,表面质量一致性非常好,而且达到客户满意的加工效率。
在数控系统方面,该机床面向客户应用的DPC动态过程控制的操作系统,由于集成了手机外壳的应用模块。操作者可以很方便选择,从而保证了初学者也能达到专家级的加工效果。总之,该机型可以说非常智能,同时又非常容易使用,是手机模具厂商最佳的选择机型。
由于现在手机更新换代的速度非常快,一般从设计到成品只有几个月的时间,而留给模具制造厂商的时间则更短,一般只有一个月甚至更短。所以,模具厂商对加工时间的要求越来越高,对机床厂家提出了更高的要求,不仅要好,还要快!
新的要求总会有新的工艺出现。在FO 350 SP成形机床里面加入了一种导电的粉末,一种新的放电工艺Gamma技术,出来的加工结果非常好。
还以上面的例子说明,同样采用一粗一精两个电极,加工完成同样的表面粗糙度,最后的加工时间是粗加工3小时22分钟,精加工5小时40分钟,总的时间9小时2分钟,比原先不用Gamma技术加工效率整整提高了62%左右,可以说是显着提高!
声明:本网站所收集的部分公开资料来源于互联网,转载的目的在于传递更多信息及用于网络分享,并不代表本站赞同其观点和对其真实性负责,也不构成任何其他建议。本站部分作品是由网友自主投稿和发布、编辑整理上传,对此类作品本站仅提供交流平台,不为其版权负责。如果您发现网站上所用视频、图片、文字如涉及作品版权问题,请第一时间告知,我们将根据您提供的证明材料确认版权并按国家标准支付稿酬或立即删除内容,以保证您的权益!联系电话:010-58612588 或 Email:editor@mmsonline.com.cn。
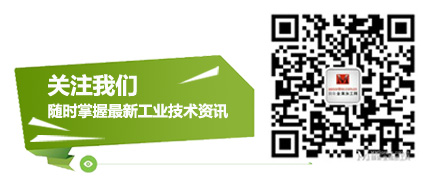
- 暂无反馈