提升大型工件的粗加工效率
随着切削技术的发展,对轨道车辆车轮、风力发电机轮毂、机械和工程设备机架及其它超大型零件进行粗铣和粗车加工时,不再需要依靠“蛮力”。一些先进的切削刀具不仅能提高加工效率,还可以延长刀刃使用寿命,减小机器和底座上承受的切削力,降低切削功率。
为提高生产效率,一家德国发电设备生产商正采用ISCAR公司方肩铣对GGG70球墨铸铁轮毂进行重型加工。每齿进给量fz:0.35-0.42mm/min,刀片每刃可持续加工40min,每刃可以完成对几个零件的加工。工作台进给量Vf:557-668mm/min,切削宽度ae:0.7xD,切削深度Ap:11-15mm。切屑控制问题的解决,也是提高生产效率的一个重要因素。有效排屑,既避免了重复切削,又延长了刀具寿命。有效提升了此类加工30%以上的生产效率。
另一家欧洲重型设备生产商在采用方肩铣对大型不锈钢棒料进行粗加工时也有同样受益。在切削参数为:每齿进给量fz:0.37mm,工作台进给量Vf:482mm/min,切削深度Ap:9-11mm的前提下,后刀面磨损比以前大幅减少。不仅加工效率提高,而且刀片每刃仍然持续加工近1小时。总体提升此类加工生产效率20%以上。强韧设计的卷屑槽保证在对长屑材料CrMnS13V进行加工时产生短小卷曲的碎屑。
奥地利一家生产商对一个100吨级的GS60铸钢发电机架进行面铣粗加工,工作台进给量Vf:800mm/min,切削深度 Ap:15mm,每齿进给量fz:0.5mm。即便加工效率为同类加工标准的2倍,切削刃的持续加工时间仍然达到25-40min,甚至可完成32m长度的切削任务。而以往,因为过度的后刀面磨损,需要在加工中途更换刀刃。
同样的改进也发生在对大型工件进行粗车加工中。在对渗碳马氏体钢轨道车辆车轮表面进行粗加工时,每转进给量fn:1.3mm/rev,切削深度Ap:6mm,平均每刀刃可加工6个零件,大大超越以往。
以上的成功,主要源自于ISCAR在小型零件加工和小型刀具中久经考验的六大技术改进。ISCAR已将它们进一步拓展至22mm规格的刀片。
小刀具,大零件,高收益
除提高产能外,改进后的六大刀具特性还给大型零件加工带来其它效益。一方面,小切深大进给对于不对称笨重零件加工时产生的切削力低,对夹具产生的应力变形小,从而对夹具的操作简易性,高刚性要求降低。另一方面,可以实现对重型零件的更全面加工,避免此类不便于移动的零件搬移至别的机床进行下一步的加工。最后,切削刃寿命更长的特点可以缩短停机时间,减少接刀痕以及在切削过程中由于切削刃失效引起的“撞击”。最重要的是,可以缩短交货期。
显然,在需要大量大型零件的风力发电行业中,类似加工显得尤为重要。
声明:本网站所收集的部分公开资料来源于互联网,转载的目的在于传递更多信息及用于网络分享,并不代表本站赞同其观点和对其真实性负责,也不构成任何其他建议。本站部分作品是由网友自主投稿和发布、编辑整理上传,对此类作品本站仅提供交流平台,不为其版权负责。如果您发现网站上所用视频、图片、文字如涉及作品版权问题,请第一时间告知,我们将根据您提供的证明材料确认版权并按国家标准支付稿酬或立即删除内容,以保证您的权益!联系电话:010-58612588 或 Email:editor@mmsonline.com.cn。
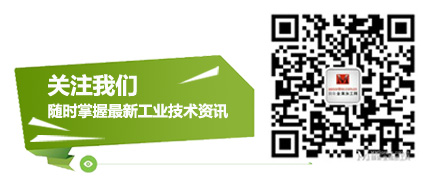
- 暂无反馈