轿车车身拼装焊接新方法探讨
轿车车身总成是轿车的重要部件,其拼装焊接的水平与质量是影响轿车质量的重要因素。本文针对车身需焊接的四大主要部件,以国际先进的焊接生产线为例,介绍了更高效的拼装加工方式与焊接方法;此外,通过对国内外汽车制造企业对於焊接尺寸和强度的检查对比,指出了更严格的焊接质量控制方法。轿车车身总成是轿车承载人员和保护人员安全的重要部件,一般都是在恶劣的环境下进行工作,既要受到废水、废气的侵蚀,又要承受巨大的静载负荷和冲击载荷。
目前,国内外汽车企业对轿车车身总成拼装基本采用激光焊接、多头自动焊机、焊接机器人、线上测量和混合式拼装自动线等新技术、新工艺,在保证产品质量和制造工艺简单的同时,轿车车身拼装焊接生产线本身投资成本低,生产周期也短。
轿车车身总成拼装焊接新工艺
轿车车身需要拼装焊接的部分现主要分为四门两盖总成焊接,左、右侧围总成焊接,车身底板发动机舱总成焊接,车身总成拼装焊接四大块。
1. 四门两盖总成焊接工序
四门两盖总成非常独立又特殊,它既是安全件又是运动件,还是轿车装饰件。国外汽车企业为提高生产效率,使其外表美观、产品安全,在门盖区域部分采用clinch连接方法,通过气液增力缸式冲压设备和连接模具,经过冲压加工,依据板件本身材料的冷挤压变形,将不同材质不同厚度的两层板件连接起来。
传统的点焊连接容易破坏板件表面的镀层,还会使板件产生热变形,连接质量无法进行无损伤的检测。而新工艺对板件表面无要求,连接表面原有的镀层、漆层不受损伤,连接过程的自动化程度高,并且能进行无损伤连接强度检测。由於在连接点处材料无撕裂损伤、无应力集中,因此clinch可消除因基准传递不一致而产生的尺寸误差;在夹具正式使用前就充分解决夹具定位结构件的变形误差,来减少对产品尺寸精度的影响,达到零件与零件装配协调性,和外观质量及整车装配速度等问题,实现极高的动态连接强度。
2. 左、右侧围总成焊接工序
由於轿车左、右侧围总成设计结构复杂,国外汽车企业原来是用移动式点焊枪进行手工焊接。但为提高生产效率,国外汽车企业对移动式点焊枪作了设计改进,以减少焊接总次数,达到能够自动焊接;同时对左、右侧围总成焊接线进行改造,安装转盘式输送机和可交替动作的左、右侧围焊接夹具,实现一面自动装夹,一面自动焊接,一面使零部件按规定生产节拍用机械传送带搬运。用於拼装的所有自动焊机都装有电子眼,可防止自动焊机的意外操作。
内外总拼是通过同一工位进行两次操作来完成的。首先在内总拼工位搭建车身骨架,然後再将外侧围覆盖於骨架之上完成外总拼。这就好比给车子穿上一层外衣,设计新车型时,只需更改外侧围及其他外覆盖件即可。
这种加工方式不但可提高生产效率,而且可有效降低由於两次定位焊接和工件转移所造成的尺寸误差。在焊接工艺方面由於车身同一工位两次总拼一次焊接,将减少或避免多层板焊点的出现,提高了焊点的稳定性,也有利於减小焊枪气缸体积,从而提高机器人柔性。这种设计方式将大幅度提高车辆在设计制造新车型方面的柔性生产能力,降低新车型的投入成本,并可大幅度缩短新车型的制造周期。
3. 车身底板发动机舱总成焊接工序
车身底板发动机舱总成是轿车车身总成的关键部件,国外汽车企业车身底板发动机舱总成焊接运送系统是采用传送线式,工作间用吊钩沿架空道输送、提升及下降。
它的焊接拼装是在有五个工位的移动式拼装台上完成的,其间互有轨道连接,要焊接的零部件在移动输送带上自动定位和夹紧,再通过动力驱动输送带送到工位。第一和第三工位主要是将各零部件通过液压夹具来定位、夹紧,第二和第四工位通过多台自动焊接机器人用激光焊接分别完成底板和发动机舱的焊接;第五工位通过多台自动焊接机器人将完成焊接的底板和发动机舱合拢後激光焊接,再将该总成通过动力驱动输送带送到车身总成拼装焊接生产线。
在典型的底板电阻点焊应用中,机器人携带焊枪从零件不同的位置进行焊接。为了达到底板中部拱形区域的焊点,焊枪的喉深和喉宽必须有足够空间避开零件的乾涉,完成该区域的焊接。因此传统的底板区域焊枪会显得十分巨大、沉重,且机器人移动的时候非常笨重,很不方便。
采用可编程的底板电阻点焊接方式,相同时间内可以增加可焊焊点数量30%,还能显着减少车间现场的占地面积,并降低焊枪的维护成本,减少焊接设备数量,缩短系统建立和调试的周期。同时底板电阻点焊接是利用两台机器人将焊枪的上下电极臂分开,其中1台机器人为主机,另外1台为从机。机器人控制可保证电极的对中性。底板电阻点焊接方法成本低且柔性好。两套底板电阻点焊接设备可以满足车身通道上位置较复杂焊点焊接。
4. 车身总成拼装焊接工序
国外汽车企业轿车车身总成焊接运送系统也采用传送线式,工作间用吊钩沿架空道输送、提升及下降,各分装组之间的定位误差允许值也约为1毫米。车身总成拼装是采用自动线,可自动定位、自动夹紧、自动装卸。
车身总成拼装是在移动式车身总成拼装台上进行的,这台设备共有8个工位元,移动输送带由於采用大马力机械输送装置,能在8秒钟内完成自动定位,从而使车身总成拼装台能在规定的工位中正确定位和夹紧。当这些总成都定位和夹紧完毕,就开始对车身总成车身的关键部位按规定焊接要求进行焊缝焊接。
为保证车身总成有足够的刚度,和车身结构尺寸有足够的精度,车身的1600个焊缝有90%以上由70余台自动焊接机器人焊接,其中有40余台是五轴自动焊接机器人,每台自动焊接机器人每小时可焊2000条焊缝,其焊接方式是激光焊接,激光光束将车顶的边缘与侧围板材焊接在一起,单侧形成长达1600mm的连续焊缝,因而能保证焊缝质量。
而且,激光焊接在满足生产工艺的同时,又能提高焊接强度,且焊缝平整光滑,极其美观。每次焊接前,机器人需要通过测量来得知焊缝的起始和结束点;在焊接过程中,机器人还需即时跟踪车顶边缘的位置,以保证焊缝的位置正好在车顶的边缘和侧围的搭接处。
激光焊接代表车身制造先进工艺,而激光边缘焊更是激光焊中最先进的技术之一。拼装线上装配速度为每小时100台,比其他汽车装配线平均速度高50%。完成车身结构尺寸规定定位焊缝的焊接後,这些随行夹具将自动移去,车身总成离开移动式车身总成拼装线进入专用输送系统。
在专用输送系统两边有多台自动焊机来完成车身总成其余焊缝的焊接,每台自动焊机都按规定的程序正确地重复一系列规定动作指令,其焊接方式也是激光焊接,完成全部焊接指令後,车身总成自动进行车门等部件装配,然後进入油漆车间。
轿车车身总成拼装焊接的质量控制
轿车车身主要部分拼装焊接的质量控制方法,有以下几种。
1. 焊接强度检查
关於焊点的焊接强度,一般采用焊接非破坏性检查、焊接破坏性检查和超声波检查等方法,并由破坏性试验室来控制这些评定并分析这些评定数据。
① 焊接非破坏性检查
按照凿检图要求的频次、方法、判定准则对焊点质量的评定,该检查一般由操作工人完成。
每天对这些总成焊接件,按照规定频次先清理焊点数目和外观质量是否符合规定, 然後将专用凿子插入规定检查的焊点3-10mm处,到焊点内端平後,就上下扳动凿子,检查焊点是否松动,接着拔出凿子,用0.5-1镑锤子还原零件,如果焊点松动,就对缺陷的焊点填写说明缺陷部位及种类的缺陷记录。
②焊接破坏性检查
按照焊接破坏性作业指导书的规定项目、频次和要求,对这些总成焊点质量进行判定,一般是由经过专门培训的检验员完成。
检查方法就是利用液压张力钳或气动凿子将这些产品所有焊点全部撕开,对母材上留下的撕洞和焊核进行检查,对撕洞检查是否烧穿、是否存在不可接受的焊接裂纹等缺陷;对焊核是用游标卡尺检查其尺寸,如符合标准要求,则此焊点为合格,否则为不合格,则对缺陷焊点填写说明缺陷部位及种类的缺陷记录。
② 超声波技术检查
国外汽车企业近期已广泛采用超声波技术来检查焊点质量,该类检查应由经过专门培训的检验员完成。这种方法就是技术人员先根据各种不同总成的板材配置,设计不同检测计划,检验人员只要根据不同总成,按照检测计划要求将超声波检测仪放置到该被检测总成,就能检查出被检测总成的焊点质量。必须注意的是,超声波检测仪开始操作时,先要核对检测程序是否正确,再要检查检测仪外接设备是否正常,才能实施操作。
2. 焊接尺寸检查
关於焊接尺寸,一般应用总成检测标准样架、柔性检具、激光测量仪和悬臂三座标测量仪来检测,并由三座标测试室来控制这些检测和分析这些检测数据。
① 标准样架
四门两盖总成的焊接尺寸是否符合规定,一般用标准样架来进行抽样检验,标准样架根据轿车四门两盖总成的外形尺寸和装配要求设计制造。而且,对这些总成标准样架的测量点要定期检定,每天还要用标准样件对测量点进行校正,有关人员对总成尺寸的检测结果、样架测量点的检定结果和样架测量点的校正结果,按规定进行记录和分析。
② 柔性检具
车身底板发动机舱总成和左、右侧围总成的外形复杂,制造和使用标准样架难度较大。国外汽车企业一般采用柔性检具来检测这些总成的焊接尺寸。柔性检具在使用前由专门电脑软件工程师编制操作程序,检验人员必须严格按操作程序实施,工程技术人员根据采集数据对程序进行修正後,完成最佳程序提供使用,定期分析采集数据。
③ 激光测量仪和悬臂三坐标测量仪
国内轿车生产企业多采用悬臂三座标测量仪,检测轿车车身总成焊接尺寸。由於轿车车身总成要测量的数据有3000个左右,测量周期较长,因此,其测量频次难以提高,对产品焊接尺寸变化就无法进行有效控制。
目前,国外轿车企业已广泛采用激光测量仪来对制造的白车身进行100%线上测量,通过安装在机器人上的激光测头和照相机对白车身上的面、孔和槽进行采样和测量。这比之前采用的三座标测量抽检白车身的质量水平又有较大提高, 同时具有测量时间短、100% 测量、即时偏差检测、即时报警等优势。
通过线上测量系统和三座标测量的优势互补,可以更好地掌握白车身的尺寸状态,提高了白车身的尺寸质量。线上测量系统在使用前也必须由专门电脑软件工程师编制操作程序,检验人员必须严格按操作程序实施,工程技术人员根据采集数据对程序进行修正後,完成最佳程序提供使用,并定期分析采集数据。
必须注意,每批轿车的各类总成检测采集到的数据应是在相同生产工艺状况下完成的,并保持每批轿车各类总成的生产批号。经检验合格的各类总成应按批号建立发放记录,以备追溯性检查使用。凡在检验中发现各类总成的缺陷产品,必须按生产批号做好检验记录和汇总分析,同时由相关部门制订纠正措施和进行质量改进。
可见,车身总成拼装工艺是一个不断更新、发展的技术领域,随着国内外汽车企业对轿车拼装工艺研究的不断深入,针对产品质量问题进行原因分析和制定相应的质量改进措施,轿车拼装技术水平必将不断提高。
声明:本网站所收集的部分公开资料来源于互联网,转载的目的在于传递更多信息及用于网络分享,并不代表本站赞同其观点和对其真实性负责,也不构成任何其他建议。本站部分作品是由网友自主投稿和发布、编辑整理上传,对此类作品本站仅提供交流平台,不为其版权负责。如果您发现网站上所用视频、图片、文字如涉及作品版权问题,请第一时间告知,我们将根据您提供的证明材料确认版权并按国家标准支付稿酬或立即删除内容,以保证您的权益!联系电话:010-58612588 或 Email:editor@mmsonline.com.cn。
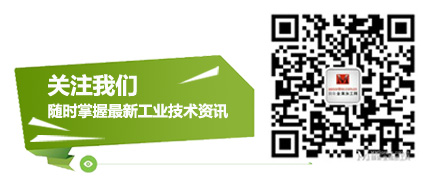
- 暂无反馈