电火花数控线切割之机械结构优良特性简析
数控线切割机床是一种高精度、高效率的自动化加工设备。尽管数控线切割机床价格偏贵,一次性投资大,但仍然为机械制造厂家所普遍采用并取得很好的经济效益,其原因在于数控线切割机床能自动化地,高精度、高质量、高效率地解决中、小批量的加工问题。数控技术、伺服驱动技术的发展及在机床上的应用,为数控机床的自动化、高精度、高效率提供了可能性,但要将可能性变成现实,则必须要求数控机床的机械结构具有优良的特性才能保证。这些特性包括结构的静刚度、抗振性、热稳定性、低速运动的平稳性及运动时的摩擦特性、几何精度、传动精度等。
一、提高机床结构的静刚度
机床结构的静刚度是指在切削力和其他力的作用下,机床抵抗变形的能力。
机床在加工过程中,受多种外力的作用,包括运动部件和工件的自重、切削力、驱动力、加减速时的惯性力、摩擦阻力等。机床的各部件在这些力的作用下将产生变形,如 各基础 件的弯曲和扭转变形,支承构件的局部变形,固定 连接面和运动啮合面的接触变形等。这些变形都会直接或间接地引起刀具与工件之间产生相对位移,破坏刀具和工件原来所占有的正确位置,从而影响机床的加工精度和切削过程的特性,所以,提高机床的静刚度是机床结构设计的普遍要求。数控机床为获得高效率而具有的大功率和高速度,使它所承受的各种外力负载更加恶劣,而且加工过程的自动化也使得加工误差无法由人工干预来修正和补偿,所以,数控机床的变形对加工精度的影响会更为严重。为了保证数控机床在自动化、高效率的切削条件下获得稳定的高精度,其机械结构应具有更高的静刚度,有标准规定数控机床的刚度系数应比类似的普通机床高 50 %。
1 .合理设计基础件的截面形状和尺寸,采用合理的筋板结构
机床在外力的作用下, 各基础件将 承受弯曲和扭转载荷,其弯曲和扭转变形的大小则取决于基础件的截面抗弯 和抗扭惯性矩 ,抗弯、 抗扭惯性矩大,变形则小,刚度就高。
2 .采用合理的结构布局,改善机床的受力状态,提高机床的静刚度
在切削力、自重等外力相同的情况下,如果能改善机床的受力状态,减小变形,则能达到提高刚度的目的。以机床主轴为例,在其他条件不变的情况下,缩短主轴前端的悬伸长度,可以减小主轴承受的弯矩,从而减小主轴前端的挠度,提高主轴的刚度。
采用合理的机床结构布局,可以显著地改善机床的受力状况,提高机床的刚度。
3 .补偿有关零、部件的静力变形
在外力的作用下,机床的变形是不可避免的,如果能采取措施使变形对加工精度的影响减小,其结果相当于提高了机床的刚度。依照这一思路,产生了许多补偿有关零、部件的静力变形的方法,这种方法普遍用于补偿因自重而引起的静力变形。
4 .提高机床各部件的接触刚度
在机床各部件的固定连接面和运动副的结合面之间,总会存在宏观和微观不平,两个面之间真正接触的只是一些高点,实际接触面积小于两接触表面的面积 ( 名义接触面积 ) ,因此,在承载时,作用于这些接触点的压强要比平均压强大得多,从而产生接触变形。 由于机床总有为数较多的静、动连接面,如果不注意提高接触刚度,各连接面的接触变形就会大大降低机床的整体刚度,对加工精度产生非常不利的影响。
5 .采用钢板焊接结构
长期以来,机床基础件主要采用铸铁件。近年来,以钢板焊接结构代替铸铁件的趋势不断扩大,从开始在单件和小批量的重型和超重型机床上的应用,逐步发展到有一定批量的中型机床。
二、提高线切割机床结构的抗振性
机床的振动会在被加工工件表面留下振纹,影响工件的表面质量,严重时则使加工过程难以进行下去。机床加工时可能产生两种形式的振动:强迫振动和自激振动。机床的抗振性指的是抵抗这两种振动的能力。
强迫振动是在各种动态力 ( 如高速回转零件的不平衡力、往复运动件的换向冲击力、周期变化的切削力等 ) 作用下被迫产生的振动。如果动态力的频率与机床某部件的固有频率重合,则将发生共振。机床结构抵抗强迫振动的能力可以用动刚度大小来表示。
自激振动是在投有外加动态力的情况下,由切削过程自身所激发的振动。自激振动的频率接近或略高于机床主振型的低阶固有频率,振幅较大,对加工过程产生极为不利的影响。当机床的刚度、刀具切削角度、工件与刀具材料、切削速度和进给量都一定时,影响自激振动的主要因素就是切削宽度 b ,因此,可以把不产生自激振动的最大切削宽度,称为临界切削宽度 ,作为判断机床切削稳定性 ( 抵抗自激振动的能力 ) 的指标。
高速切削是产生动态力的直接因素,强力切削也意味着切削宽度大。数控机床在追求高速度、高切削效率的同时,也埋下了容易产生受迫振动和自激振动的根源。切削过程的自动化又使得振动难以由人工来控制和消除,数控机床只有靠自身机床结构的高抗振性来减小和克服振动对加工精度、加工过程的影响。
提高机床的抗振性,可以从提高静刚度、固有频率和增加阻尼几个方面着手。提高静刚度的措施已在前面有详细的介绍。因为固有频率 ( 其中, K 为静刚度, m 为结构质量 ) ,所以在提高静刚度时,能相对减小结构件的重量,即提高单位重量的刚度,则能提高固有频率。前面介绍的合理布置筋板,采用钢板焊接结构等提高静刚度的措施,同样能达到提高固有频率的目的。
三、减小机床的热变形
热膨胀是各种金属和非金属材料的固有特性。机床在工作时,有许多部件和部位会产生大量热量,如电机、滚动轴承、切屑及刀具与工件的切削部位、液压系统等。这些产生热量的部件和部位称为热源。热源产生的热量通过传导、对流、辐射传递给机床的各个部件,引起温升,产生热膨胀。由于热源分布不均匀,各热源产生的热量不等,零部件各处质量不均匀,形成机床各部位温升不一致,从而产生不均匀的温度场和不均匀的热膨胀变形,以致破坏刀具与工件的正确相对位置,影响加工精度。
数控机床的主轴转速、进 给速度 远高于传统机床,并且大切削用量产生的炽热切屑也多,故发热远较传统机床严重,而热变形对加工精度的影响往往难以由操作者修正,因此对如何减小机床的热变形应予以特别重视。
1 .改进机床布局和结构设计
(1) 采用热对称结构
这种结构相对热源是对称的。这样在产生热变形时,可保证工件或刀具回转中心对称线的位置不变,从而减小热变形对加工精度的影响。最典型的实例是许多卧式加工中心所采用的框式双立柱结构,主轴箱嵌入框式立柱内 ,且以立柱左、右导轨两内侧定位,在热变形时,主轴中心在水平方向的位置保持不变,从而减小了热变形的影响。
(2) 采用预拉伸的滚珠丝杠结构
数控机床中的滚珠丝杠是在预加载荷大、转速高、散热差的条件下工作的,容易发热,滚珠丝杠的热伸长直接影响进给系统的定位精度。采用预拉伸的方法可以减小丝杠的热变形。这种方法是在加工滚珠丝杠时,使螺距略小于名义值,装配时对丝杠进行预拉伸,即使其螺距值达到名义值,当丝杠工作受热,丝杠中的拉应力补偿了热应力,从而 减小热 伸长。
(3) 在机床布局时,尽量减少内部热源
内部热源的发热是造成热变形的主要原因,因此,在机床布局设计中应尽量考虑将热源从主机中分离出去,如将电动机、变速箱、液压泵站等置于机床主机以外。
加工过程所产生的炽热切屑是一个不可忽视的热源。在机床布局时,应考虑使排屑通畅,应设置自动排屑装置以随时将切屑排到机床外,同时应在工作台或导轨上设置隔热防护罩,使 数控技术切屑的热量隔离在机床外。
2 .控制温升
对机床发热部位采取散热、风冷、液冷等控制温升的办法来吸收热源发出的热量,是在各类数控机床上使用较多的一种减少热变形影响的对策。其中,强制冷却是比较有效的方法。所谓强制冷却,就是利用冷却装置对润滑油或冷却液进行冷却,然后将润滑油送至摩擦副润滑或将冷却液送至切削部位冷却。
3 .热变形补偿
预测热变形规律,建立数学模型并存人计算机中进行实时补偿。热变形附加修正装置已在国外产品上作为商品供货。
四、改善运动导轨副的摩擦特性
机床导轨是机床基本结构的要素之一。机床的加工精度和使用寿命很大程度上取决于机床导轨的质量,而对数控机床的导轨则有更高的要求,如:高速进给时不振动, 低速进 给时不爬行;有高的灵敏度,能在重载下长期连续工作;耐磨性要高,精度保持性要好等。这些都与 导轨副的摩擦特性有关,要求摩擦系数小,静、动摩擦系数之差小。现代数控机床采用的导轨主要有塑料滑动导轨、滚动导轨和静压导轨。
( 一 ) 塑料滑动导轨
数控机床采用的塑料滑动导轨有铸铁 - 塑料滑动导轨 和镶钢 - 塑料滑动导轨。塑料滑动导轨常用在导轨副的运动导轨上,与之相配的金属导轨为铸铁或钢质。铸铁牌号为 HT300 ,表面淬硬至 HRC45~50 ,表面粗糙度磨削至 0.20~0.10 ;镶钢导轨常用 50 号钢或其他合金钢,淬硬至 HRC58~62 。导轨上的塑料常用聚四氟乙烯导轨软带和环氧型耐磨导轨涂层两类。
1 .聚四氟乙烯导轨软带
聚四氟乙烯导轨软带是以聚四氟乙烯为基体,加入青铜粉、二硫化钼和石墨等填充剂混合烧结,并做成软带状。这种软带有以下特点:
(1) 摩擦特性好
(2) 耐磨性好
(3) 减振性好
(4) 工艺性好
导轨软带的使用工艺简单。首先,将导轨粘贴面加工至表面粗糙度为 3.2~1.6 的表面,为了对软带起定位作用,导轨粘贴面应加工成 0.5~ 1.0mm 深的凹槽。然后,用汽油或金属清洁剂或丙酮清洗粘接面后,用胶粘剂粘合,加压初固化 1~2 小时后再合拢到配对的固定导轨或专用夹具上,施以一定压力,并在室温下固化 24 小时,取下清除余胶,即可开油槽和进行精加工。由于这类导轨软带采用粘贴方法,故习惯上称为“贴塑导轨”。
2 .环氧型耐磨导轨涂层
环氧型耐磨导轨涂层是以环氧树脂和二硫化钼为基体,加入增塑剂,混合成液状或膏状为一组份,以固化剂为另一组份的双组份塑料涂层。它有良好的可加工性,可经车、铣、刨、钻、磨削和刮削加工;也有良好的摩擦特性和耐磨性,而且抗压强度比聚四氟乙烯导轨软带要高,固化时体积不收缩,尺寸稳定。特别是可在调整好固定导轨和运动导轨间的相关位置精度后注入涂料,这样可节省 许多加工工时,故它特别适用于重型机床和不能用导轨软带的复杂配合型面。
( 二 ) 滚动导轨
滚动导轨具有摩擦系数小 ( 一般在 0.003 左右 ) ,动、静摩擦系数相差小,且几乎不受运动变化的影响,定位精度和灵敏度高,精度保持性好等优点。现代数控机床常采用的滚动导轨有滚动导轨块和直线滚动导轨两种。
1 .滚动导轨块
滚动导轨块是一种滚动体作循环运动的滚动导轨,其结构: 1 为防护板,端盖 2 与导向片 4 引导滚动体 ( 滚柱 3) 返回, 5 为保持器, 6 为本体。使用时,滚动导轨块安装在运动部件的导轨面上,每一导轨至少用两块,导轨块的数目取决于导轨的长度和负载的大小,与之相配的导轨 多用镶钢淬火导轨。当运动部件移动时,滚柱 3 在支承部件的导轨面与本体 6 之间滚动,同时又绕本体 6 循环滚动,滚柱 3 与运动部件的导轨面不接触:因而该导轨面不需淬硬磨光。滚动导轨块的特点是刚度高,承载能力大,便于拆装。
2 .直线滚动导轨
直线滚动导轨是近年来新出现的一种滚动导轨,其结构主要由导轨体 1 、滑块 7 、滚珠 4 、 保持器 3 、端盖 6 等组成。由于它将支承导轨和运动导轨组合在一起,作为独立的标准 导轨副部件 ( 单元 ) 由专门生产厂家制造,故又称单元式直线滚动导轨。使用时,导轨 体固定在不运动部件上,滑块固定在运动部件上。当滑块沿导轨体运动时,滚珠在导轨体和滑块之间的圆弧直槽内滚动,并通过端盖内的滚道从工作负载区到非工作负载区,然后再 滚动回 工 数控机床的结构与传动作负载区,不断循环,从而把导轨体和滑块之间的移动,变成了滚珠的滚动。
单元式直线滚动导轨除有一般滚动导轨的共性优点外,还有以下特点:
(1) 具有自调整能力,安装基面许用误差大。
(2) 制造精度高。
(3) 可高速运行,运行速度可大于 60m /min 。
(4) 能长时间保持高精度。
(5) 可预加负载,提高刚度。
( 三 ) 静压导轨
静压导轨是在两个相对运动的导轨面间通以压力油,将运动件浮起,使导轨面间处于纯液体摩擦状态。由于承载的要求不同,静压导轨分为开式和闭式两种。
声明:本网站所收集的部分公开资料来源于互联网,转载的目的在于传递更多信息及用于网络分享,并不代表本站赞同其观点和对其真实性负责,也不构成任何其他建议。本站部分作品是由网友自主投稿和发布、编辑整理上传,对此类作品本站仅提供交流平台,不为其版权负责。如果您发现网站上所用视频、图片、文字如涉及作品版权问题,请第一时间告知,我们将根据您提供的证明材料确认版权并按国家标准支付稿酬或立即删除内容,以保证您的权益!联系电话:010-58612588 或 Email:editor@mmsonline.com.cn。
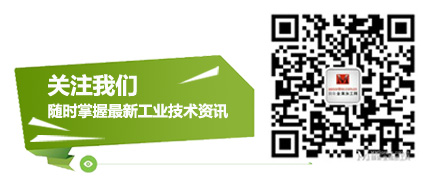
- 暂无反馈