数控加工的工作过程和基本原理
数控加工的工作过程
数控机床加工零件是按照事先编写好的加工程序单来进行的。
首先,对产品零件图进行工艺分析,根据图样中对材料和尺寸、形状、加工精度及热处理等的要求来确定加工方案,进行工艺处理和数值计算,确定合理的程序原点(对刀点)、走刀路线及切削用量。在此基础上,根据数控系统规定的功能指令代码和程序段格式编写数控加工程序单。编程中的数学处理包括:按零件几何尺寸、加工路线,计算刀具中心运动轨迹取得刀位数据;根据机床插补功能及被加工零件轮廓的复杂程度决定计算工作量,计算量小可手工计算完成,若计算量大则要依靠自动编程系统进行计算。目的是获得零件轮廓相邻几何元素交点或切点的坐标值,得出几何要素的起点、终点、圆弧的圆心坐标值等。
然后,编写好的加工程序单,可以制成输入纸带、磁带或磁卡。其中所包含的加工数据可通过光电阅读机、键盘或计算机接口三种方式输入给数控机床的数控装置。数控装置将输入指令进行译码、寄存和运算后,向系统各个坐标的伺服系统发出指令信号,经驱动电路的放大处理,驱劫伺服电动机输出角位移和角速度,并通过执行部件的传动系统转换为工作台的直线位移,实现进给运动。计算机数控的控制功能很强,可以同时控制多根轴。
数控加工的基本原理
数控加工时以程序段为单位,由系统程序逐段进行处理,不仅将刀位数据还将加工速度F代码及其他辅助代码(s代码表示主轴转速,T代码表示刀具号,M代码表示辅助功能指令)均按语法规则解释成计算机所能认可的数据形式,并以一定的格式存放在内存专用区 间。此外,对刀具补偿(长度与半径补偿)作处理,对进给速度(合成速度分解成沿各坐标的分速度以及自动增减速等)做处理,完成加工中的插补运算(由主CPU担任),数据由存储区间调入时,依靠控制总线通过地址总线取址并将数据沿数据总线输入CPU运算,结果仍沿总线返回,分别送至相关输出接口。输出信号也要通过一系列电路处理(分配、中断和缓冲),才能使伺服电机进给,使主轴按转速回转或停止。CRT显示出程序执行过程,并输出位置环与速度环的反馈信号经总线往返后由CPU进一步随机处理的结果。全部过程均在时钟频率的统一控制下,有条不紊地进行工作。
下面对各个加工过程的工作原理进行说明。
(1)输入
加工零件前,要对数控装置输入零件程序、控制参数以及各种补偿数据。输入方式通常分为:a)MDI输入方式,也叫做手动数据输入方式;b)介质输入方式,如纸带通过光电阅读机输入或磁盘、磁卡通过接口输入;e)计算机输入方式,由上级计算机的DNC(直接数控)接口输入。
(2)译码
按语法规则将输入信息以程序段为单位,翻译成计算机所能识别的代码形式,并以一定的数据格式存放在指定的内存专用区间。
(3)刀具补偿
由于加工零件程序编写是以零件的轮廊轨迹来编程,而加工实际中是以刀具中心点所移动的轨迹为依据。因此,必须奄刀具半径和刀具长度上给予补偿,即进行两者之间的转换。
进给速度处理
它包括将刀具速度由编程中的合成速度转换为各坐标上的分速度的处理以及软件自动增、减速的处理。
(5)插补
当零件的被加工面古有斜、锥或曲面时,数控机床需要依靠预先编写好的程序指令,l以数值计算方法密化起始点至终止点间给出的数学特征方程式或离散点之间的小线段,以插值方法完成刀具应走的轨迹从而达到工艺要求,这个过程叫做“插补”。完成“插补”功能的装罩叫做“插补器”。其本质是在保证零件轮廓精度的要求下,把程序始点至程序终点间分成足够微小的线段进行插补,完成定义域内两点之间线段的密化工作。在车削时,通过两个轴联合行动则可形成斜面或曲面,但在箱体零件加工曲面时,至少要有三个坐标配合运动。由此可见,有些曲面可以用两轴联动由第三轴控制加工出来,有些则要三轴联动或三轴以上联动。
(6)位置控制
在伺服回路的位置环上控制位置,这种功能可由软件完成,也可由硬件完成。在闭环(或半闭环)控制系统中,在每个采样周期(可以和插补周期相等或为插补周期的若干分之一)内,将插补计算出的理论位置与实际反馈位置进行比较,用差值去控制进给电机。在位置控制中,通常还要完成位置回路的增益调整、各坐标方向的螺距误差补偿和反向间隙补偿。在开环控制系统中,每进行一次插补运算都产生进给增量,并以脉冲的形式输出。在插补运算过程中,不断向各坐标轴发出互相协调的进给脉冲,控制步进电机运行。
(7)输入/输出(I/O)处理
机床上的强电信号输入/输出和计算机一侧的弱电信号进行交换与处理,以便控制许多应答式动作,如换刀或润滑启闭、冷却供断等。
(8)显示
数控机床的显示大多为CRT显示。通常显示零件程序、参数、机床状态、刀具、报警及自诊断等。
(9)诊断
当故障或不正常情况出现时,系统融合在各部分的自诊断程序会使机床报警,中断运行。同时,各种诊断程序也可以检测各部位的故障所在,以便及时排除故障。
声明:本网站所收集的部分公开资料来源于互联网,转载的目的在于传递更多信息及用于网络分享,并不代表本站赞同其观点和对其真实性负责,也不构成任何其他建议。本站部分作品是由网友自主投稿和发布、编辑整理上传,对此类作品本站仅提供交流平台,不为其版权负责。如果您发现网站上所用视频、图片、文字如涉及作品版权问题,请第一时间告知,我们将根据您提供的证明材料确认版权并按国家标准支付稿酬或立即删除内容,以保证您的权益!联系电话:010-58612588 或 Email:editor@mmsonline.com.cn。
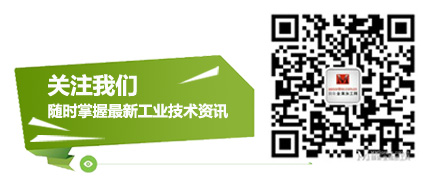
- 暂无反馈