机床表面粗糙度
表面粗糙度是指加工表面上具有较小间距和谷峰组成的微观几何形状特征。机床影响工件加工表面粗糙度的工艺因素有:
(l)几何因素从工件表面的微观几何形状分析,切削刃与工件相对运动的轨迹即切削刃几何形状在工件表面上的复映,机床从而形成表面粗糙度c由于已加工表面是由刀具的主、副切削刃切削加工后形成的,两条切削刃相对工件作进给运动时,在已加工表面上遗留下的痕迹,所形成的螺旋面积,即残留面积。机床残留面积与进给量,、背吃刀量、刀具的主偏角、副偏角:和J尖圆弧半径以及切削刃本身的表面粗糙度有关。机床从几何因素考虑,残留面积高度的轮廓算术平均偏差,即为表面粗糙度值。机床残留面积越大,其高度越高,表面粗糙度值就越大。
(2)物理因素物理因素即与被加工材料性质及切削机理有关的因素。
1)在切削过程中,刀具刃口磨损产生的钝角及后刀面对工件表面产生挤压和摩擦,使加工表面的金属层发生塑性变形,引起残留面积扭曲,从而造成表面粗糙度值增大。
2)在车削脆性材料时产生崩碎切屑,使已加工表面出现凸凹不平的断裂穴或崩碎痕迹,留下许多麻点,增大了表面粗糙度值。
3)切削过程中产生的积屑瘤既不规则又不稳定,一方面其不规则的硬点部分地代替切削刃切削,留下深浅不一的痕迹,机床另一方面一部分脱落的积屑瘤嵌入已加工表面,机床形成不规则的毛刺或硬点,使表面粗糙度值增大。
4)用低速切削时,容易产生鳞刺,即在已加工表面上形成与切削速度近似垂直的横向裂纹,并有鳞片状的毛刺出现,使表面粗糙度值增大2—4级。
(3)机械加工振动在切削过程中,受切削力的影响,刀具和工件常发生强烈的振动,产生明显的表面振痕,机床使工件表面粗糙度值增大,严重时还会产生崩刃现象,使表面质量严重恶化。
声明:本网站所收集的部分公开资料来源于互联网,转载的目的在于传递更多信息及用于网络分享,并不代表本站赞同其观点和对其真实性负责,也不构成任何其他建议。本站部分作品是由网友自主投稿和发布、编辑整理上传,对此类作品本站仅提供交流平台,不为其版权负责。如果您发现网站上所用视频、图片、文字如涉及作品版权问题,请第一时间告知,我们将根据您提供的证明材料确认版权并按国家标准支付稿酬或立即删除内容,以保证您的权益!联系电话:010-58612588 或 Email:editor@mmsonline.com.cn。
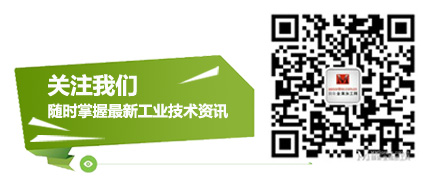
- 暂无反馈