数控车床编程问题的处理
1.编程原点的选择
从理论上讲,编程原点可以选在工件的任意位置,但作为数控车床,大多数加工的是回转体工件。实际上,为了编程的方便以及各尺寸较为直观,应尽量把编程原点选得合理些。X向应取在主轴(2对刀问题工件坐标系确定后,还要确定对刀点在工件坐标系中的位置,即常说的对刀点问题。对刀点是指数控机床上用刀具加工零件时,刀具相对零件运动的起始点。所选择的对刀点必须与零件的定位基准有一定的坐标关系,这样才能确定机床坐标与工件坐标之间的关系,有几点注意的问题:
2.1对刀点的选择与精度,习惯,机床坐标系,编程等有关
当对刀精度要求不高时,可直接选在零件上或夹具上的某些表面作为对刀点。当对刀精度要求较高时,对刀点应尽量选在零件的设计基准上,对于以孔定位的零件,则选用孔的中心作为对刀点。
2.2对刀应选择在对刀方便的地方
在采用绝对坐标系的数控机床中,对刀点可选在机床坐标系的原点上或距原点为确定值的点上,在安装零件时,零件坐标系与机床坐标系要有确定的尺寸关系。对于具有机床坐标原点的数控机床,第一个程序段的指令就是设定对刀点的坐标值指令,用以规定对刀点在机床坐标系中的坐标值。
2.3对刀时应使刀位点与对刀点重合
所谓刀位点:是指刀具的定位基准点。对于车刀:是指刀尖。对于球刀,是指球心。对于立铣刀:是指刀具中心线与刀具底面的交点。快速定位指令G00的使用数控加工时,对于刀具快速定位和空行程时使用G00能够提高效率,但要注意G00不是插补指令。它的运行轨迹是先两轴同步进给作斜线运动,走完较短一轴,再走完较长的一轴。因此,要注意加工时,G00定位容易与工件发生碰撞。
当刀具加工到A点时,准备返回到B点定位。如果编程时如果采用G00X20Z2.G00的行走路线如虚线所示,则刀具与工件会发生碰撞。为了避免刀具与工件发生碰撞。
3.刀尖圆弧半径对加工精度的影响
数控车床编程一般以刀尖作为对刀点和编程点,但实际上刀尖不是理想的刀尖,会有一定的圆弧。这就导致刀具行走轨迹与编程轨迹不相吻合,而有一差值。尤其刀具在加工锥度,圆弧时,对加工精度影响更为突出。
特别是在没有刀尖圆弧半径补偿的系统中。因此,在编程时必须根据具体情况考虑这个因素。下面举例说明工件形状发生变化时,刀尖圆弧半径对加工精度的影响及采取相应的措施。
3.1工件加工表面由外圆柱面向锥度面过渡时
加工从圆柱体向圆锥体转换时,编程控制的刀具理论上应处在O1的位置上,但由于刀尖圆弧半径r的影响,实际上刀具对锥体的切削点由原来的E点转换为A点。可以看出按此加工的锥体与设计图样的锥体不相符,比设计的锥体尺寸大一些,也就是在轴向和径向产生了误差,即A点与C点的坐标值。轴向误差Δx=r-rcosα径向误差Δz=r-rsinα式中:r―――刀尖圆弧半径α―――工件锥体母线与中心线的夹角要想加工出与设计相符合的锥体,由图可知,刀具必须处在O2的位置,相当于刀尖在Z轴向前移动一个ZΔ值,由图可得:根据几何关系∠BO2D=α∠CO2D=α/2那么:CD=rtanα/2ZΔ=r-rαtanα/2在编程时,往往忽略了这个误差,若果考虑了这个误差,就能保证锥体的加工精度。一般尽量采用圆心编程和刀尖圆弧半径补偿功能来解决。
3.2工件加工表面由圆柱面向圆球面过渡时
当刀尖半径增加时,AB值增加;反之,AB值减少。当球体半径增大时,AB值减少。
在加工中要消除这个误差就要改变刀具的切削点,即将O1位置移动到O2位置,即向左移动一个ZΔ值。
根据几何关系得:OC=(R+r)cosαZΔ=CD=OD-OC=(R+r)-(R+r)cosα=(R+r)(1-cosα)
式中:R―――工件半径
r―――刀尖圆弧半径
α―――工件中心与刀尖中心连线与Z轴坐标的夹角在编程时,将加工圆柱面向球面转换时的Z轴坐标值加上ZΔ值作为切削球体的起始点,就可保证球体的加工质量。
结束语
综上所述,充分认识到:数控加工是理论和实践都要掌握好的一项工作。尤其是手工编程,必须对数控系统非常熟悉和了解。认真研究和分析每个指令的性质,作用,要求和参数的含义,指令对加工路线的影响等,正确选择和使用各个指令,再加工掌握一定的车工工艺知识和实践经验,就能很好地使用数控机床加工,尽量避免出错和发生重大事故,加工出合格的产品。
声明:本网站所收集的部分公开资料来源于互联网,转载的目的在于传递更多信息及用于网络分享,并不代表本站赞同其观点和对其真实性负责,也不构成任何其他建议。本站部分作品是由网友自主投稿和发布、编辑整理上传,对此类作品本站仅提供交流平台,不为其版权负责。如果您发现网站上所用视频、图片、文字如涉及作品版权问题,请第一时间告知,我们将根据您提供的证明材料确认版权并按国家标准支付稿酬或立即删除内容,以保证您的权益!联系电话:010-58612588 或 Email:editor@mmsonline.com.cn。
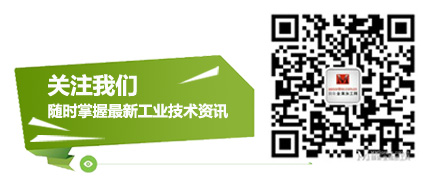
- 暂无反馈