伊斯卡:转向节加工技术的新突破
在2008年到2010年期间爆发的全球金融危机将整个汽车行业拖入了一个前所未有的低谷。经过此次危机后,随着行业逐渐回暖,在旺盛需求的推动下汽车厂商们正想方设法缩短交货期。现在,数以百万计的零配件必须要在很短的时间内加工完成,所以如何提高生产效率已成为应对该行业挑战的关键所在。
伊斯卡为此专门推出了一系列解决方案,可有效避免停机时间,缩短零件加工周期,削减单件加工成本(CPP),由此提高生产效率。这些高效加工方案的突出优势还包括:革命性3P(高性能、高生产率、高收益率)理念、束魔涂层技术(SUMO TEC)硬质合金牌号及涂层、工程方面以及创新性研发。伊斯卡决定将汽车配件划分为多个门类(应用)并针对性地制定系统性的优化加工解决方案。转向节便属于其中的一种应用。
转向节是最复杂最精密的汽车零配件之一。要实现快速低成本生产,采用高效的精密切削刀具不可或缺。以往转向节都是由铸铁或钢材制成的,但目前市场趋向于改用铝合金。一方面,这是出于减轻汽车重量,提高燃油经济性的优化需要。另一方面,采用铝合金的加工成本要远远低于采用铸铁的加工成本(分别为15-25美分和约1美元)。不过,并非所有情况下,铝合金转向节都可以替换铸铁或钢质转向节 ,但不论何种时候(铝合金或铸铁),都可以通过以下方法来降低加工成本:
1.采用组合刀具,避免换刀是最省钱的办法之一。
而且,由于许多转向节加工用的数控机床刀库容量往往有限,采用组合刀具有时不仅仅是建议,也是必要的措施。
2.采用FMR(快速金属切削)刀具,以便缩短加工时间并节省额外成本。
2.1 更高的进给量:
伊斯卡束魔变色龙钻(SUMOCHAM)的进给量比常规硬质合金钻提高多达2倍。传统硬质合金钻受碳化钨(WC)的力学性质限制,无法承受相对较高的扭矩并容易损坏,只能采用很小的转进给量。这意味着制造商们无法充分“挤压”机床的性能,只能低效率工作。相比之下,束魔变色龙钻主体由高强度刀具钢制成,可以承受很高扭矩载荷。此外,和这种可换刀头设计理念相比,硬质合金钻还有一个弱点,对总体跳动较敏感,T.I.R.(总体指标偏差)容易造成硬质合金意外折断。相比钢制钻杆,硬质合金钻头钻杆承受弯曲变形的能力极其有限。只要总体跳动值比平均值稍微高出一点,它就很容易折断。
伊斯卡束魔变色龙(SUMOCHAM)可换头式钻削系统拥有以下诸多优点,由此成为全球转向节制造商的首选。
·AlTiN涂层硬质合金刀头结合钢制钻杆,可提升端面钻削加工的每转进给量多达2倍。
·刀头更换,无需对刀时间。
·刀头多次更换也不会影响刀槽寿命。
·易于集成至柔性组合刀具,适合定制刀具设计。
2.2 更高的切削速度:
例如,对于铝合金转向节:经PCD(聚晶金刚石)或DLC(类金刚石)涂层刀具的加工速度远超未经涂层的硬质合金。虽然这些刀具价格更贵,但由于切削快、寿命长,投资回收快且单件加工成本低很多。转向节一般都是大批量生产的,故PCD和DLC涂层刀具性价比极高,应用广泛。最要注意的问题是采用合适的冷却液并确保其以适当的角度喷向切削区域,从而提供有效的润滑并避免产生积屑瘤。
2.3 采用全新刀具设计理念,大幅增加刀齿密度,从而成倍提高加工效率: 转向节的主轴承孔采用镗杆、带导向块的单刃铰刀或可调式双刃镗刀进行精加工。
这些方法十分可靠,因此长期被人们应用。缺点是进给量超低(采用单刃或双刃刀具时进给速度只能保持0.15-0.3 毫米/转),延缓了整个加工过程。
为了加快加工速度,转向节制造商们试图用多齿钎焊铰刀替代这些传统刀具,这解决了加工周期过长的问题,但又产生了一个新的问题。大直径铰刀价格昂贵,如果每次磨损就要更换,用户很不划算。此外,由于主轴承孔公差要求极高,这些铰刀无法进行重磨。
后来,这一老办法有了新的改进。它是一种微调式铰刀环,带有钎焊硬质合金切削刃。这种刀具切削速度很快(例如用10齿铰刀环加工一个?90.0H6孔,其进给量可以达到1毫米/转),并且可以使用一颗锥头螺钉进一步调整直径来补偿磨损。这种直径调整机制可以达到很高的公差,在大多数情况下有利于延长刀具的寿命。铰刀环很快成为了加工主轴承孔的常用刀具,但由于以下致命缺点,这一设计理念没能成为一种最彻底的解决方案。
·如果某个刀刃产生了缺口(由于工件材料质量差等原因,这种情况时有发生),会暴露未涂层的基体而形成积屑瘤(BUE),导致精加工表面受损。
·无法均匀调整刀齿,因此无法精确控制径向偏差。因此,一些刀齿会参与比其它刀齿更深的切削,加速了其过度磨损。
·刀齿磨损后,铰刀环需要送去重新安装刀齿。重新安装费用不菲,通常占到了新铰刀环价格的65-70%。用户还必须控制铰刀环库存,以便安排重新修磨和重涂层等。所有这些都要占用额外的资源,所以许多用户都不喜欢这个办法。
那么转向节主轴承孔精加工的终极刀具在哪里呢?多年前,伊斯卡的研发专家们想出了一种新办法,并立刻赢得了汽车业的热烈追捧。
这种全新刀具是一种可换刀片式微调多齿铰刀。每一个刀片都可以在几秒钟内单独进行精密的调整以获得所需直径。凭借这些功能,这种铰刀既满足高孔径公差要求,又消除了铰刀的径向偏差问题,延长了刀具的寿命。此外,高强度的立装刀片,提高了加工经济性:
·具有4个切削刃
·切削刃不需重新刃磨和重新涂层
·多数情况下,转向节加工机床具有两个主轴,为此伊斯卡还提供第二套方案作为备用(一把为右手刀,备用的为左手刀),左手铰刀可以使用右手铰刀未使用的额外的4个切削刃,刀片性价比更高。
·可视情况轻松地更换刀片牌号(在钎焊铰刀上这是不允许的)。
3.采用不用从机床取出即可更换刀片或刀片更换速度超快的刀具,从而避免或缩短停机时间并节省额外费用。
伊斯卡创新方案融合上述刀具和方法,为广大汽车厂商开辟成功新天地。
声明:本网站所收集的部分公开资料来源于互联网,转载的目的在于传递更多信息及用于网络分享,并不代表本站赞同其观点和对其真实性负责,也不构成任何其他建议。本站部分作品是由网友自主投稿和发布、编辑整理上传,对此类作品本站仅提供交流平台,不为其版权负责。如果您发现网站上所用视频、图片、文字如涉及作品版权问题,请第一时间告知,我们将根据您提供的证明材料确认版权并按国家标准支付稿酬或立即删除内容,以保证您的权益!联系电话:010-58612588 或 Email:editor@mmsonline.com.cn。
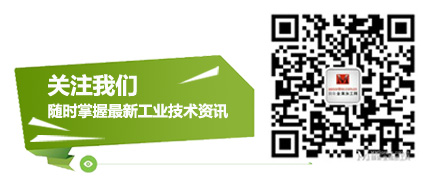
- 暂无反馈