怎样提高线切割加工工件的精度和表面质量
随着模具产业和其它加工制造业的飞速发展,对电火花线切割各项工艺指标如尺寸精度、表面粗拙度等都提出了越来越高的要求。另一途径是采用多次切割,但因为其丝速快,一次切割后再切割时切缝宽度大大增宽,钼丝振动显著增大,若采用常规的切割工艺,第二次切割后的表面粗拙度也得不到有效的进步。
本文从以下几个方面讨论在往复走丝电火花线切机床上采用多次切割技术时工艺的改进,以提高加工工件精度和表面质量。
1.加工参数
在这个阶段,应采取了降低高频电源脉冲宽度,增大脉冲间隙,减小输出电流示值的办法,使电极丝所受的单面火花激扰力减小,同时也减小了火花放电问隙,使跟踪电流调整到运行速度与机床空运行速度接近时进行切割。应在小电流、窄脉宽、小能量脉冲前提下进行。快速走丝时钼丝是一种随机振动,钼丝在空转时,振幅大约在0.03ram左右,为了避开振动对工件表面的影响,在切割凹模时,第一次切割留有极小的余量,然后以大脉宽、大电流快速进给,高速高效一次加工成工件的外形,在第二次切割时将钼丝退离工件一定的间隔,即放电间隙加大,故二次切割时没有电火花,是—次低侵蚀放电过程。
2.易损件
当第一次切割加工结束时,其切割加工的大量工作已经完成,接下来的多次切割加工,实质是针对进步加工工件精度和表面质量进行的。所以在采用二次切割切割前必需调整贮丝筒状态、更换导轮及导轮轴承。因为一、二次切割加工电极丝所处的位置是不相同的,第二次切割时,切缝宽度大大超过第一次切割时的切缝宽度,切缝两侧不能限制钼丝的振动(见图1)。因为往复走丝电火花线切割机床影响切割精度的枢纽题目之一就是电极丝振动题目。电极丝振动的原因主要有贮丝筒的动态不平衡、径向跳动、贮丝筒轴承、导轮、导轮轴承的动态跳动以及电极丝的张力等。另外在加工过程中,电极丝在高速运动(其运动速度为300~700m/min)和切割中产生高温(10000℃左右)作用,加之老化使电极丝损耗、直径减小,造成张力下降、振幅增大,从而导致加工中振动增大,影响加工效果。在紧丝时,一定要留意用力适当,在确保电极丝不断的条件下尽量拉紧电极丝以保证电极丝的张力(一般应在15N左右),使电极丝在切割过程中的振动控制在0,03mm之内。因此可采取了两次紧丝的方法来进步上述指标。此时电极丝的振动与空载时电极丝振动相近,最大限度地减小电极丝振动、增大张力至关重要。其中一次切割是双面临称余量加工,此时电极丝是在一个较封锁的环境中进行切割加工,对电极丝振动的阻尼作用较大,同时有利于电极丝在切缝中的不乱;而第二次切割是单边余量加工,加工时作用在电极丝上的放电力是分歧错误称的,电极丝两侧的阻尼状态也不一样,切缝对电极丝振幅的约束整平作用也不存在了。
3.程序的编制
经由对二次切割加工方法的分析与反复试验,考虑详细二次切割时,机床重新定位精度及二次切割放电间隙等因素,在编写切割凹模的二次切割程序时,取△f≈0.05mm为宜,其中△f=f2-f1,f1-第一次切割间隙补偿量,f2-第二次切割间隙补偿量。实验结果表明,当△f过大时,相称于机床空走,即没有进行火花放电加工;当△f过小时,则相称于机床双边对称余量加工,同样无法达到二次切割加工的目的。
目前,具有多次切割技术的往复走丝线切割机床纷纷走向市场。在均匀加工速度为50mm2/min时,通过多次切割能不乱获得Ra≤1.0微米的表面粗拙度,精度≤10微米。
往复走丝线切割机床实现多次切割是精密传动及控制技术、脉冲电源技术、数控技术的综合应用的结果,也是进步切割加工精度及表面质量的重要手段。如姑苏三光HA系列往复走丝线切割机床,采用SKD2控制系统和EAPT自动编程系统,数控系统带有专家数据库,可为用户提供具体的多次加工工艺参数。
机床本体采用入口交流伺服系统驱动X、y坐标工作台,同时采用螺距补偿功能,定位精度高、可长时间稳定加工、加工件表面光滑无条纹,尤其是大规格机床加工的型孔的精度和跳步精度均比以往电火花线切割机床有显著提高,,整机机能向前迈出了坚实的一步。
声明:本网站所收集的部分公开资料来源于互联网,转载的目的在于传递更多信息及用于网络分享,并不代表本站赞同其观点和对其真实性负责,也不构成任何其他建议。本站部分作品是由网友自主投稿和发布、编辑整理上传,对此类作品本站仅提供交流平台,不为其版权负责。如果您发现网站上所用视频、图片、文字如涉及作品版权问题,请第一时间告知,我们将根据您提供的证明材料确认版权并按国家标准支付稿酬或立即删除内容,以保证您的权益!联系电话:010-58612588 或 Email:editor@mmsonline.com.cn。
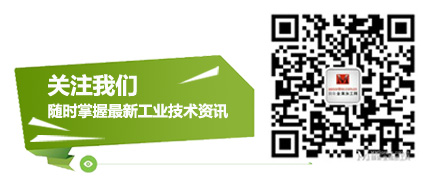
- 暂无反馈